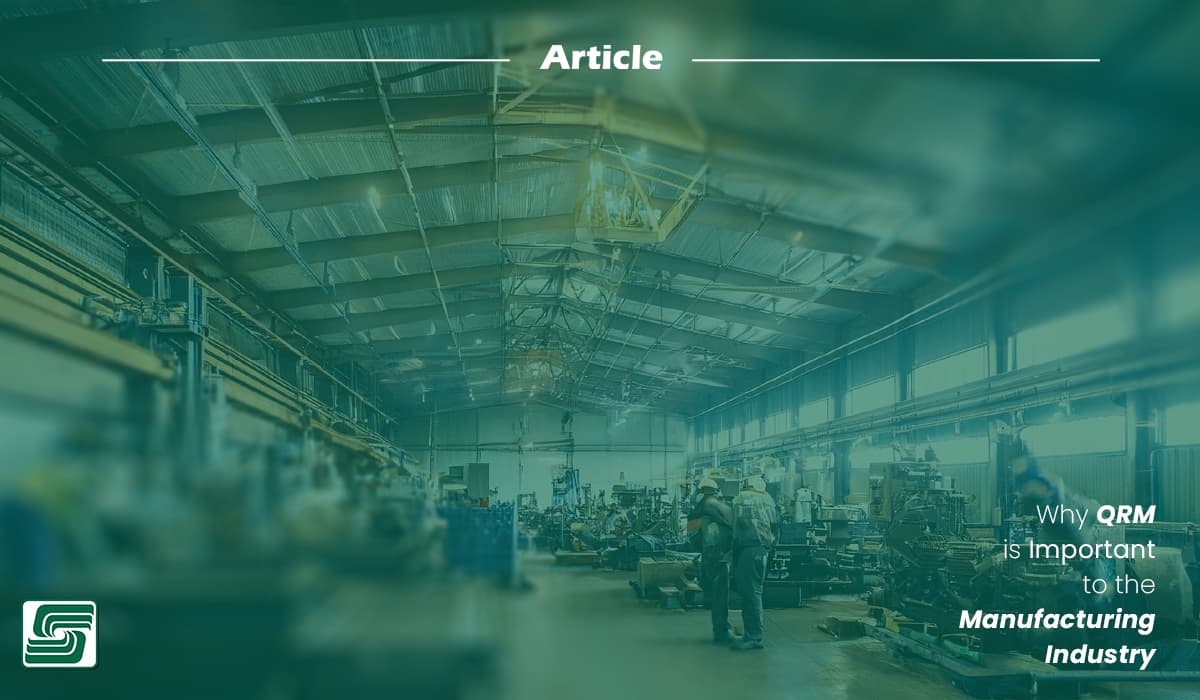
Time is a critical factor in metal fabrication that significantly impacts the efficiency and effectiveness of the manufacturing process. Quick response manufacturing (QRM) is a powerful strategy to address this challenge by reducing lead times, optimizing costs, and enhancing delivery efficiency.
Quick response manufacturing emphasizes the importance of time at every stage of the manufacturing process. By streamlining operations and minimizing delays, it enables companies to achieve remarkable results.
So, What is QRM?
Quick response manufacturing (QRM) is a strategy that significantly reduces lead times across all organizational functions to enhance responsiveness and competitiveness. It aims to improve quality, reduce costs, and eliminate non-value-added waste by streamlining processes and quickly adapting to customer needs.
QRM benefits companies with low-volume, high-variability production environments, emphasizing a holistic approach that integrates shop floors and office operations.
According to statistics, companies implementing QRM have experienced an impressive 95% reduction in lead times. This substantial improvement accelerates production and enhances overall operational agility.
QRM's Role
QRM plays a pivotal role in cost optimization within metal fabrication. Organizations can achieve up to a 30% decrease in finished product costs by eliminating process inefficiencies and bottlenecks.
This cost-saving aspect makes QRM an attractive strategy for businesses looking to enhance their bottom line while maintaining high-quality standards.
The impact of QRM extends beyond lead times and costs; it also revolutionizes delivery efficiency. Companies leveraging QRM principles have reported significant enhancements in on-time delivery rates by up to 60% and an impressive 80% reduction in rework and scrap.
These improvements boost customer satisfaction and contribute to sustainable business growth.
How Effective is QRM?
The concept of QRM is a strategy for cutting lead times in all aspects of manufacturing operations.
When implemented, a QRM program:
- 95% reduction in lead times
- 30% reduction of the finished product cost
- 60% improvement in on-time delivery
- 80% reduction of rework and scrap
Two types of businesses use a QRM:
- A company producing small-batch engineered materials
- A company that doesn't need to engineer products but offers many pieces with varying demand
Necessity is the mother of invention, and QRM is no exception to that saying.
QRM Evolution
The roots of QRM go back to Japan after World War II. Following the war, the Japanese industrial complex was in shatters. Rebuilding its manufacturing base required a new tactic: Just-In-Time (JIT) Manufacturing.
Gerhard Plenert, a supply chain expert, provides four theories why JIT implementation became necessary in Japan:
- Money: Japan's war effort depleted cash reserves, eliminating opportunities to finance large inventory production.
- Space: Japan didn't have enough real estate to build large factories
- Resources: an island nation, Japan doesn't have any natural resources
- Labor: despite a high unemployment rate, labor efficiency methods haven't been developed yet
JIT was an accidental invention. Plenert wrote that Japan developed small factories using small inventories of material only used for products being worked on.
Because of this setup, inventory levels and investments were kept low while providing a fast turnaround on natural resources.
Understanding Quick Response Manufacturing
Quick response manufacturing has evolved from the principles of Just-In-Time (JIT) manufacturing, tracing its origins back to post-World War II Japan.
While JIT focuses on minimizing waste and optimizing production processes, QRM takes a more comprehensive approach by emphasizing the critical role of time in manufacturing. A key distinction between QRM and JIT lies in their core principles.
While JIT aims to reduce inventory levels and enhance efficiency, QRM places a stronger emphasis on lead time reduction and responsiveness to customer demands.
Evolution from Just-In-Time Manufacturing
The transition from JIT to QRM signifies a paradigm shift towards a more agile and customer-centric manufacturing approach.
By recognizing the importance of time as a competitive advantage, QRM enables companies to adapt quickly to changing market dynamics and customer preferences.
This evolution highlights the need for businesses to focus on operational efficiency and prioritize speed and flexibility in their production processes.
Relationship with Lean Manufacturing
Taiichi Ohno, the father of Lean Manufacturing, has significantly shaped the principles of both Lean and QRM methodologies. Ohno's emphasis on waste reduction and efficiency enhancement resonates deeply with QRM's core values.
By integrating Lean principles into QRM strategies, organizations achieve a harmonious balance between quality, efficiency, and customer satisfaction.
This synergy between Lean Manufacturing and QRM underscores the importance of continuous improvement and optimization in modern manufacturing practices.
Significance of QRM in Manufacturing
Implementing quick-response manufacturing brings about multifaceted benefits that extend beyond operational enhancements.
By embracing QRM principles, companies elevate customer service standards, enhance product quality, boost employee morale, increase engagement, and improve operational efficiency.
The holistic approach to QRM drives performance improvements and fosters a culture of continuous organizational learning and innovation.
Implementing QRM Strategies in Metal Fabrication
Successfully implementing QRM strategies in metal fabrication is crucial for enhancing operational efficiency and responsiveness to customer demands.
Adopting QRM principles involves integrating agile methodologies into existing metal fabrication processes and investing in training and development initiatives to ensure a seamless transition.
Adopting QRM Principles
Integrating QRM strategies into metal fabrication processes requires a fundamental shift towards prioritizing lead time reduction and flexibility. Companies streamline operations and enhance productivity by aligning production schedules with customer demand patterns and optimizing workflow layouts.
Training programs focused on QRM principles empower employees to embrace change, adapt to new methodologies, and drive continuous organizational improvement.
Overcoming Challenges
Despite the many benefits associated with QRM implementation, businesses often face challenges when adopting these strategies. Identifying and addressing barriers to QRM adoption is essential for ensuring successful integration into metal fabrication operations.
Common obstacles include resistance to change, lack of buy-in from key stakeholders, inadequate resources, and organizational inertia. Companies implement effective communication, stakeholder engagement, pilot projects, and performance monitoring mechanisms to overcome these challenges.
By proactively managing resistance to change and fostering a culture of innovation, organizations navigate the complexities of implementing QRM strategies effectively.
Gerhard Plenert's expert opinions emphasize the significance of Japan's approach to small factories with minimal inventories during product manufacturing.
This lean method reduces inventory levels and enhances resource utilization efficiency, enabling rapid turnaround times on natural resources.
Drawing inspiration from such practices guides metal fabrication companies in adopting lean principles.
Benefits of QRM in Metal Fabrication
QRM has proven to be a game-changer in the metal fabrication industry. It offers many benefits that significantly enhance operational efficiency and customer satisfaction.
Reduction in Lead Times and Costs
One of the most notable advantages of implementing QRM strategies in metal fabrication is the substantial reduction in lead times.
Companies leveraging QRM principles have achieved remarkable results, with reports showing an impressive 95% reduction in lead times. This significant improvement accelerates production cycles and enables businesses to respond swiftly to changing market demands.
QRM contributes to cost optimization by streamlining processes and eliminating inefficiencies. Organizations have witnessed a noteworthy 30% decrease in finished product costs, underscoring the financial benefits of adopting QRM methodologies.
Improvement in Delivery Efficiency
Enhancing delivery efficiency is another key benefit of implementing QRM practices. Companies significantly improve on-time delivery rates by aligning production schedules with customer demand patterns and optimizing workflow layouts.
Statistics reveal that organizations embracing QRM have experienced a remarkable 60% enhancement in on-time delivery performance. Implementing QRM leads to a substantial reduction in rework and scrap rates, further enhancing operational efficiency.
Businesses have reported an impressive 80% decrease in rework and scrap levels, highlighting the positive impact of QRM on overall production quality and resource utilization.
Quick response manufacturing has become a transformative strategy for achieving excellence in metal fabrication operations based on the combined effects of:
- Reduced Lead Times
- Cost Savings
- Enhanced Product Quality
Embracing a New Era of Metal Fabrication Excellence
As metal fabrication evolves, combining quick-response manufacturing strategies heralds a new era of excellence in manufacturing processes.
The future outlook for metal fabrication with QRM strategies is promising. Companies are experiencing significant improvements in operational efficiency and customer satisfaction.
By embracing QRM principles, businesses embark on a journey of continuous improvement, driving innovation and agility within their operations.
Real-World Example of QRM Benefits
<Author's Note: an ironclad rule we follow here at Fab Times is not to mention Schuette Metals, our services, and our capabilities. Fab Times's role is to share knowledge, not brag. I couldn't locate an accurate example of QRM's effectiveness when working on this article. After this fruitless search, I opted to look inside our walls.>
Schuette Metals is a prime example of the transformative power of QRM implementation.
Through adopting a QRM program, Schuette Metals achieved remarkable results, including a substantial reduction in lead time by nearly 11-1/2 days and an impressive increase in touch time by 34%.
These outcomes underscore the tangible benefits companies realize by leveraging QRM methodologies to enhance productivity and streamline production processes.
In Sum
By prioritizing continuous improvement through QRM implementation, organizations position themselves at the forefront of manufacturing excellence.
Achieving operational excellence with QRM involves optimizing internal processes and fostering a culture of innovation, collaboration, and adaptability.
As businesses navigate the complexities of modern manufacturing landscapes, embracing QRM emerges as a strategic imperative for driving sustainable growth and competitiveness in the metal fabrication industry.