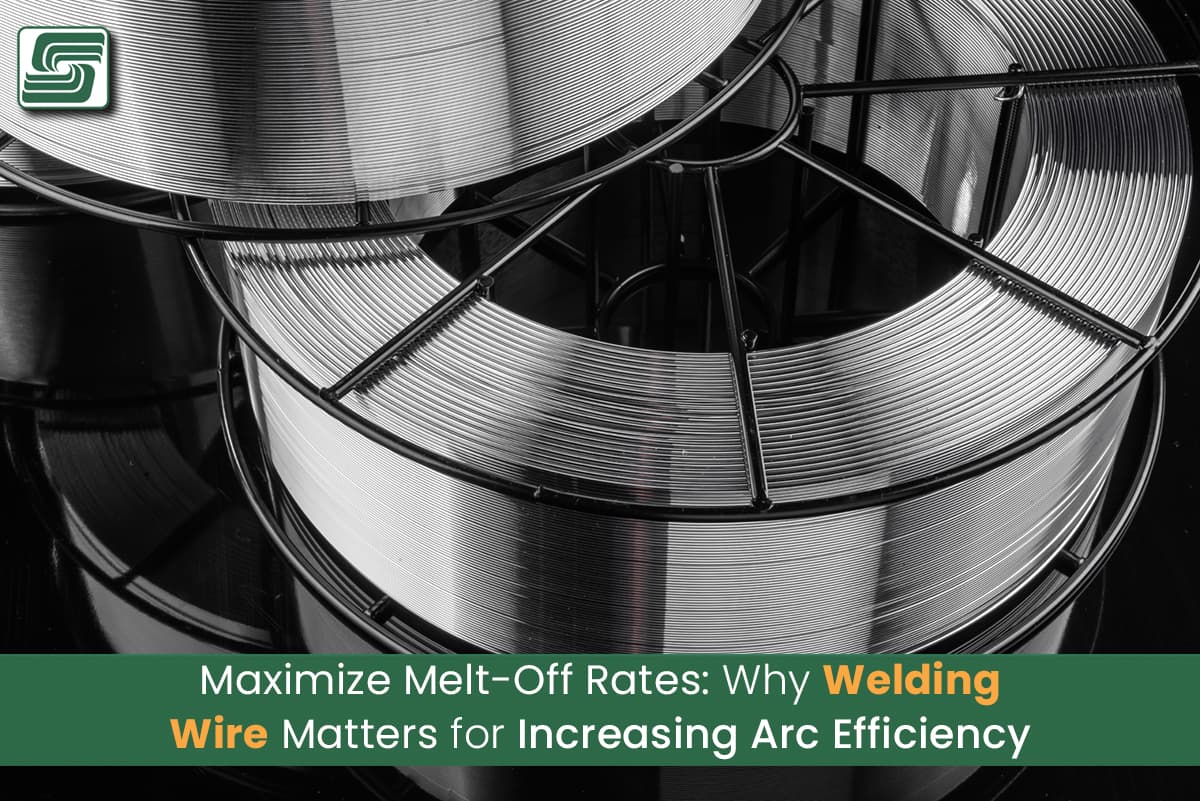
Welding is crucial across many industries, from auto manufacturing to construction. But not all welding wire is created equal. The type of filler metal used significantly impacts your welding efficiency and productivity. This article explores the filler metal effect and how wire selection impacts your shop’s bottom line.
What is Filler Metal?
In welding, the filler metal refers to the consumable wire fed into the weld pool during the process. This additional metal is melted and fused with the base metals being joined. Filler metal alloys provide specific properties in the finished weld.
There are several main types of filler metal used in modern welding:
- Solid wire
- Metal-cored wire
- Gas-shielded flux-cored wire
These wires look similar, but their designs and alloy chemistries produce markedly different results. Your choice of filler metal affects weld quality, deposition rates, spatter levels, and more.
Understanding these distinctions is key to selecting the most efficient wire for your welding processes.
Solid Wire: The All-Purpose Option
Solid wire electrodes are one of the most common types of filler metal used in GMAW (gas metal arc welding). As the name suggests, these comprise a solid single alloy core, rather than any flux coating.
Solid MIG wire offers an excellent balance of versatility, metal deposition rate, and cost-effectiveness. It performs well in positions, on materials, and for welds where high basic mechanical properties are needed.
Solid wires are often the go-to choice for shops performing high-volume welding on materials like mild steel. Their smooth, stable arc makes for easy welding, albeit with higher spatter levels.
Solid wires have drawbacks when used on certain metals. The solid wire may produce a refractive weld profile or porosity on some aluminum. Alternatives like metal-cored wire are a better choice where more advanced metallurgical properties are needed.
Metal-Cored Wire: Enhanced Metallurgy and Speed
Where solid wire falls short in some areas, metal-cored filler metal provides major benefits. As the name suggests, these wires have a hollow core filled with metal alloys and dust-like metal compounds.
The powdered metal core allows the addition of alloying elements like chromium, nickel, silicon, and more. This leads to improved metallurgical properties you can’t achieve with solid wire.
Metal-cored wires also offer much higher deposition rates than solid wires of equal diameter. The hollow core is associated with a higher electrode current density. You weld faster and with less heat input using smaller diameter metal-cored filler.
These advantages do come at a cost. A metal-cored wire is more expensive, less versatile, and prone to more slag cleaning than solid equivalents. These tradeoffs are often worthwhile for applications requiring specialized metallurgy or maximal speed.
Flux-Cored Wire: Built-In Slag Protection
Self-shielded flux-cored wires provide a useful solution for welding situations where shielding gas is impractical. These electrodes contain fluxing compounds in their core, eliminating the need for external gas shielding.
The flux core forms protective slag and gasses as the wire melts, shielding the weld puddle from atmospheric contamination. This makes flux-cored wires ideal for outdoor welding or working in drafty conditions.
While unsuitable for all materials, flux-cored filler provides strong mechanical properties when welding carbon and low-alloy steel. Their all-position welding capabilities are also popular in the structural steel fabrication industry.
Using flux-core leads to higher spatter levels and slag clean-up time than gas-shielded solid and metal-cored wires. Proper parameter selection and techniques like drag angles help mitigate these limitations.
How Filler Metal Selection Impacts Efficiency
It’s clear that filler metal choice significantly impacts the welding process. But how do these differences ultimately affect productivity and the bottom line? Let’s dig into the key factors:
- Deposition Rates: Given the same wire diameter, metal-cored electrodes melt faster and deposit more filler metal than solid equivalents. Higher deposition equals faster travel speeds and welding times.
- Current Density: Metal-cored wires carry more current for their diameter. This increased current density leads to faster melting with a smaller weld pool. You weld faster with less heat input.
- Arc Performance: Arc stability affects how easily an operator controls the weld pool. Metal-cored wires promote a smooth arc, while flux-cored inherently has more spatter. Easier welding equals greater efficiency.
- Mechanical Properties: Better metallurgy in finished welds means less rework and repairs later.
- Specialty alloy wires enhance properties so welds pass inspections the first time.
- Slag Removal: More time spent cleaning slag is less time welding. Flux-cored wires produce an abundant slag that must be removed between passes.
- Versatility: Solid wires weld well on a broader range of materials versus more specialized options. The ability to use one wire for more applications reduces changeover downtime.
Analyze your welding workflows and costs to determine which factors will provide the biggest efficiency gains and savings. Spending more on consumables often results in large net savings from enhanced productivity and quality.
Choosing the Optimal Filler Metal for Your Needs
With the wide range of filler metals available, how do you determine what’s best for your welding operations? Here are some key questions to consider:
- What materials do you weld most often? Match your wire to the alloys being joined.
- What physical and mechanical properties are needed? Specialty wires provide enhanced characteristics.
- Is all-position welding needed? If so, flux-cored is likely the best process.
- Can shielding gas be used, or is a self-shielded process mandatory? Gasless flux-cored wires are made for the latter.
- What welding positions are required? Vertical-up welds prefer a fast-freezing metal-cored wire for good control.
- How much spatter and slag are acceptable? Solid wires spatter more, while flux-cored produces excessive slag.
- What level of arc control and welding expertise is available? Solid/metal-cored wires are easier to weld with.
- How critical is the deposition rate? Metal-cored wires substantially boost melting speed.
Doing small-scale test welds with different wires on your specific material provides valuable insights. Qualified welding distributors are also excellent resources for choosing wire.
Adopting New Welding Filler Metal Technology
It pays to keep up with emerging improvements in filler metal technology to achieve the highest efficiency and performance possible. Wire manufacturers are continuously enhancing their products and introducing new alloys.
Metal-cored wires are one area where technology keeps progressing. Wires with advanced flux compositions now rival solid GMAW for usability while retaining speed benefits. New metal powders enable wires tailored for specialized applications like high-strength steels or nickel alloys.
Adopting new filler metals requires upfront costs for testing, welder training, and potentially new equipment. But the boost in productivity and weld quality quickly offset these investments. Talking to your consumable suppliers about new product releases saves you time and money.
In Sum
Choosing the optimal welding wire for your applications is critical for efficiency.
- Solid wires offer versatility for broad use but have limitations on certain materials.
- Metal-cored wires provide exceptional deposition rate and metallurgy but cost more.
- Flux-cored wires work well where shielding gas is unavailable but produce substantial slag.
Analyze your workflow and requirements to select the best option. Higher consumable costs often result in far greater productivity gains. Keeping up with the latest filler metal technology ensures you maximize efficiency.
With expertise and testing, you can leverage the filler metal effect to reduce welding costs, speed production, and boost your bottom line. Consult knowledgeable suppliers to find the best wires for your specific welding needs.