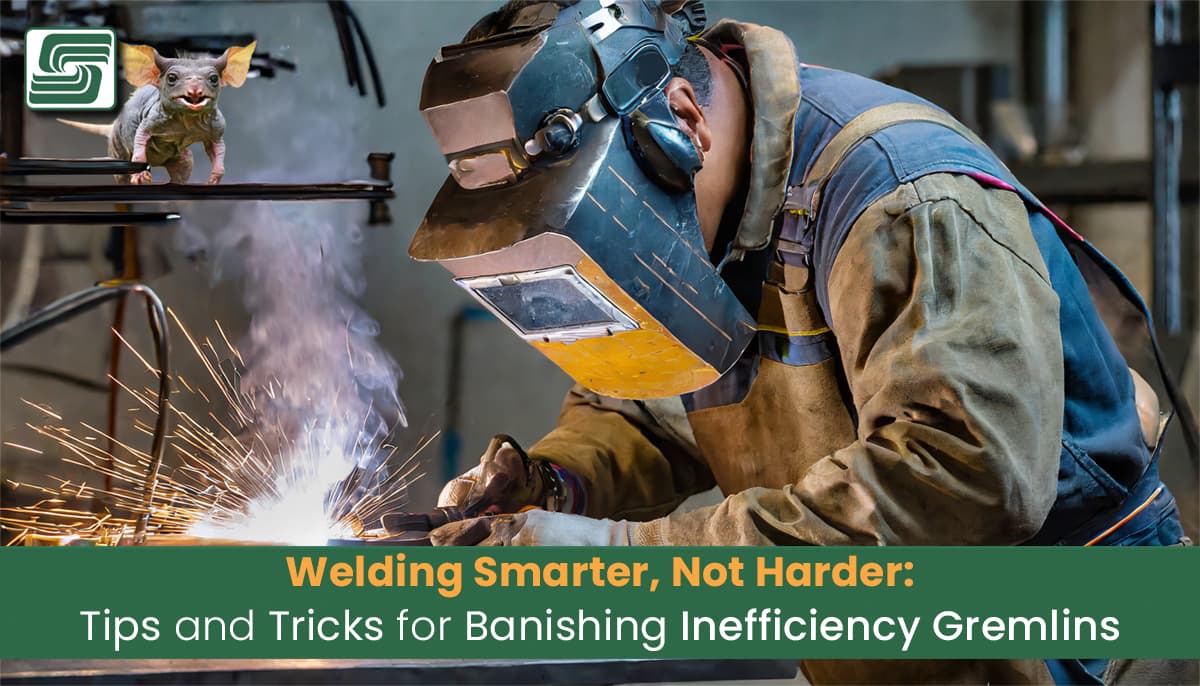
Inefficiencies in welding lurk like gremlins, slyly sabotaging productivity. But armed with keen eyes and wisdom, we can banish these gremlins and transform welding operations into well-oiled machines purring with potential.
Sources of Inefficiency
In welding, inefficiencies originate from equipment, materials, and human error. Using outdated tools slows speed and reduces quality, wasting time and materials. Inadequate training leads to errors requiring rework and squandering resources. Improper maintenance causes unexpected downtime.
Traditional wires may not suit all applications, producing excessive spatter or lower deposition efficiency versus advanced options like metal-cored wires.
Time spent on pre- and post-welding tasks like cleaning and grinding takes up valuable production time if not managed well. Shield gas selection significantly affects spatter and post-weld cleanup time.
Cost Drivers
In welding, cost inefficiencies penetrate each process stage. Energy consumption for high-powered welding contributes significantly to overhead costs and impacts budgets. Material wastage represents immediate financial loss and compromises weld quality, causing rework and inflating costs.
Waste management for residual slag and spatter is also expensive. Skilled labor carries costs, including time spent on pre- and post-welding tasks instead of core welding work. Equipment downtime exacerbates costs through production delays, showing systemic issues. Regular maintenance checks are critical to ensure smooth operations and avoid costly breakdowns.
Comparing Fillers
Filler metal choice affects welding efficiency and outcomes significantly. Solid wire offers practicality with versatility but may lack the characteristics of other fillers. It is prone to splatter, requiring more post-weld cleanup.
Metal-cored wires enable faster welding, reducing costs for high-volume projects. Their alloy composition mitigates splatter. Gas-shielded flux-cored wires offer superior penetration and deposition with minimal splatter. Their inner core enhances performance, suiting diverse applications. Each filler has strengths and weaknesses depending on the operation.
Solid Wire
Commonly used solid wire filler offers efficiency and ease of use for automated processes like GMAW and SAW. The continuous form enables smooth feeding, reducing downtime. Robustness suits large-scale manufacturing and construction. However, it produces more splatter than other fillers, requiring cleanup. It lacks forgiveness for dirty metals. Despite limitations, solid wire provides an economical option for many applications.
Metal-Cored Wire
Metal-cored wire enhances efficiency significantly. Its tubular structure filled with alloying elements enables faster deposition and travel speeds by focusing heat on the work piece. This exponential productivity increase provides substantial savings. Its composition reduces splatter remarkably. Superior gap bridging and manipulation control bolster quality. Its consistency across varied stick-out lengths adds reliability.
Gas-Shielded Flux-Core Wire
Versatile gas-shielded flux-core wire excels for thick materials and out-of-position welding. Its high deposition rates are essential for large-scale applications. The tubular flux-filled structure enables deep penetration, suiting contaminant-laden metals. It generates less spatter. Both self-shielded and gas-shielded types exist. Self-shielded portability trades off higher smoke and slag.
Beyond faster cooling and excellent mechanical properties, gas-shielded flux-core wire provides superb toughness and crack resistance for high-stress, critical applications. Careful wire speed control ensures consistency between filler and base material for quality welds with the required strength. This robust tool has broad potential across sectors.
Pre- and Post-Welding Time
A substantial proportion of welders’ time involves pre- and post-welding tasks. Preparing metals is fundamental for quality and longevity. Surfaces must be cleaned meticulously to remove contaminants that may degrade welds. Manual cleaning consumes labor hours. Advanced cleaning technologies could save time and resources.
Post-welding splatter grinding requires extensive attention. Removing molten metal adhered during cooling takes manual effort and tools, inflating costs. Optimizing voltage and electrode angle reduces splatter. Shield gas selection also influences performance and splatter production, significantly impacting cleanup time.
Focusing only on welding while ignoring auxiliary tasks misses opportunities to boost efficiency.
Cleaning Metals
Cleaning base metals before welding is crucial, yet often overlooked. Removing elements like rust, oil, and oxides ensures weld integrity. Contaminants affect penetration and cause porosity, compromising durability. Proper preparation enhances arc performance and reduces defects and rework, saving time and materials. No universal method exists. Experienced judgment is vital for surface preparations.
Grinding Splatter
The recurring splatter issue has plagued welding for decades. Splatter leads to time-consuming, costly cleanup. Optimizing power, technique, gas, and filler quality reduces splatter without sacrificing weld integrity. Anti-spatter spray or consumables help. Splatter cannot be eliminated but minimized to boost productivity and quality.
Shield Gas Selection
Shield gas choice profoundly impacts welding quality and efficiency, influencing the arc, bead profile, and metal transfer method. Typically, welders use argon and carbon dioxide mixtures. Composition affects splatter quantity since CO2 causes more. Argon enables a smoother arc and less turbulence.
Though initial argon costs may be higher, reducing cleanup time afterward provides long-term savings. Enhanced bead appearance from argon mixtures requires less finishing, too. Strategic shield gas selection elevates efficiency while curbing cleanup costs.
Gas Mixture Affects Splatter
Though overlooked, shield gas composition significantly impacts splatter production during welding. Different mixtures exacerbate or minimize splatter occurrence. Pure CO2 induces substantial splattering with its intense reactivity. Inert argon enables smoother arcs with less spatter comparatively.
So for CO2 versus an argon-CO2 blend, increasing argon content mitigates splatter, improving aesthetics and reducing post-weld cleaning needs.
Higher Argon Content Reduces Cleanup Time
Argon creates an inert shield during welding, protecting molten metal from atmospheric gases compromising quality. Its low reactivity makes it ideal for the weld pool shield, preventing oxidation and nitriding. This noble gas features in mixtures used in technologies like TIG and MIG welding, amplifying benefits when combined.
The quest for efficiency seeks to improve speed without sacrificing weld quality. Increasing argon concentration in shielding gases may help by enhancing the protective weld pool shield for faster speeds and better quality. However, implications require thorough understanding before implementation.
Argon’s non-reactive nature prevents undesirable chemical reactions at welding high temperatures that could degrade weld quality. As an effective insulator, it maintains heat for improved penetration and stability. Its cleaning action removes oxides and contaminants for stronger joints. It minimizes spattering issues faced with other gases.
Argon finds broad usage across techniques like GTAW, GMAW, FCAW, and SMAW for its versatility. It provides stable arcs, enables smooth welds with minimal spatter, and aids quality welds.
Higher argon content correlates directly with improved fusion from its enhanced shielding. Higher content means less post-weld cleanup from minimal spatter, preserving aesthetics and integrity. Smoother arcs translate into uniform deposition. Increased argon enables swifter welding and better heat control for superior penetration and joints without compromising mechanical properties.
In Sum
By optimizing our welding practices, we can banish the gremlins of inefficiency, paving the way for maximized productivity and quality. The path forward relies on keen eyes to spot areas of improvement and wisdom to find solutions. With diligence and care, our welding operations will shine brighter than ever.