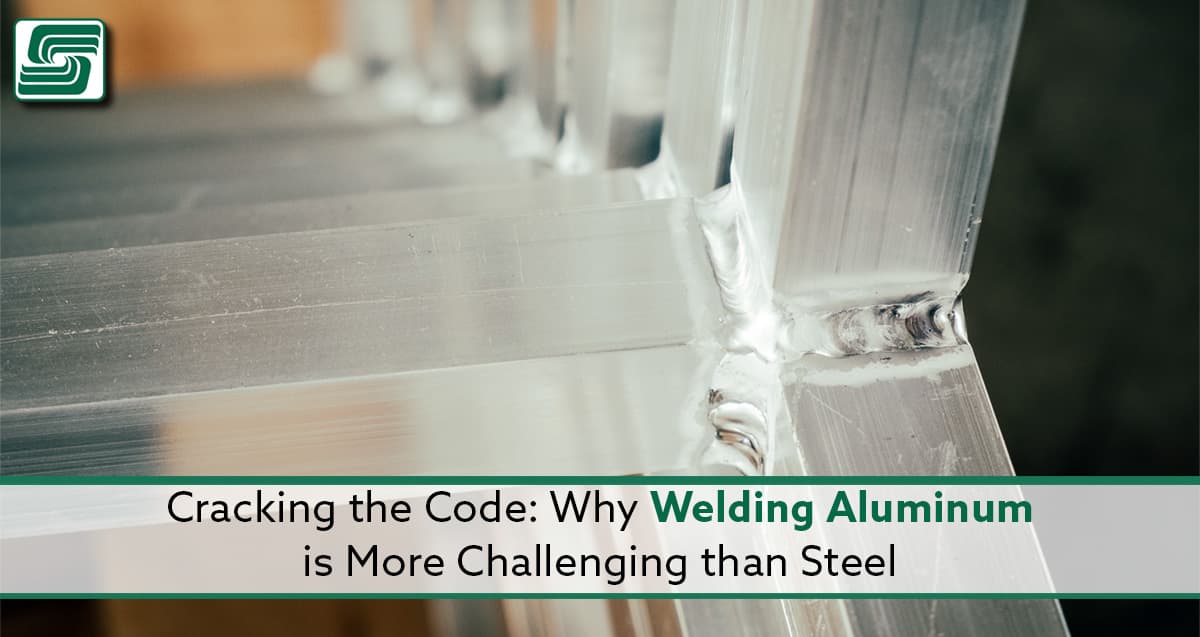
Welding aluminum involves joining two or more aluminum pieces using a welding process.
Aluminum is a popular metal used in various industries because of its lightweight, durability, and corrosion resistance, and is commonly used in the aerospace, automotive, and marine industries.
Welding aluminum requires specific techniques and considerations that differ from welding steel.
Differences Between Welding Aluminum and Steel
The primary difference between welding aluminum and steel is their physical properties. Aluminum has a high thermal conductivity and a low melting point compared to steel. The high thermal conductivity means aluminum can dissipate heat quickly, making welding more challenging.
The low melting point also makes it easier to overheat and burn through the material.
Another notable difference is that aluminum has a thin, transparent oxide layer that forms on the surface when exposed to air.
Remove this layer before welding because it prevents proper fusion. On the other hand, steel has a thicker, more substantial oxide layer that can be removed during welding.
Understanding the Properties of Aluminum
To effectively weld aluminum, it is essential to understand its properties. Aluminum is a soft, malleable metal that is highly reactive to oxygen, and its low density makes it lightweight but also prone to warping and distortion during welding. Aluminum is also non-magnetic, making using magnetic clamps and fixtures challenging during welding.
Challenges in Welding Aluminum
Welding aluminum presents several challenges, including:
- Heat Dissipation: Aluminum has high thermal conductivity, making it challenging to concentrate heat in a specific area during welding, which leads to warping, distortion, and burn-through.
- Oxide Layer: As mentioned earlier, aluminum has a thin oxide layer that must be removed before welding. Failure to remove this layer causes poor fusion and weakened welds.
- Porosity: Aluminum is prone to porosity, which refers to gas pockets that form in the weld. Porosity weakens the weld and can lead to cracking and failure.
- Softness: Aluminum is a relatively soft metal, making it prone to deformation during welding. It is crucial to use proper clamping and fixturing to prevent distortion.
Types of Aluminum Welding - MIG, TIG, and Stick Welding
Three primary methods for welding aluminum are MIG, TIG, and stick welding.
- MIG Welding: MIG welding is the most common method used for welding aluminum. It uses a wire electrode fed through a spool gun and a shielding gas to protect the weld from contamination. MIG welding is fast, efficient, and produces high-quality welds.
- TIG Welding: TIG welding is a slower and more precise method of welding aluminum. It uses a tungsten electrode and a filler rod to create the weld. TIG welding produces high-quality welds but requires more skill and experience than MIG welding.
- Stick Welding: Stick welding is the least common method used for welding aluminum. It uses a coated electrode that melts and forms the weld. Stick welding is slower and less efficient than MIG and TIG welding and produces lower-quality welds.
Choosing the Right Welding Method for Aluminum
When choosing a welding method for aluminum, several factors need to be considered, including:
- The material's thickness
- The type of joint
- The required welding speed
- The desired weld quality
- The availability of equipment and materials
MIG welding is the most common method for welding aluminum because of its speed, efficiency, and high-quality results. TIG welding is better suited for thin or intricate welds that require precise control. Stick welding is rarely used for welding aluminum because of its lower quality results and slower speed.
Welding Aluminum to Steel - Techniques and Considerations
Welding aluminum to steel requires specific techniques and considerations. The two metals have different physical properties, making creating a strong, durable weld challenging.
The following techniques can weld aluminum to steel:
- Mechanical Fastening: Mechanical fastening involves using bolts or rivets to join the aluminum and steel. This method is simple, easy, and does not require welding. However, it produces a less durable joint than welding.
- Adhesive Bonding: Adhesive bonding involves using an adhesive to join the aluminum and steel. This method is simple and easy but produces a less durable joint than welding.
- Friction Stir Welding: Friction stir welding involves using a rotating tool to create heat and friction between the aluminum and steel, causing them to fuse. This method produces a durable joint but requires specialized equipment and expertise.
- MIG Welding: MIG welding can also weld aluminum to steel. However, it requires specific techniques and considerations, such as using a welding wire compatible with both metals and adjusting the welding parameters to accommodate the different melting points and thermal conductivities.
Safety Precautions for Welding Aluminum
Welding aluminum is hazardous if ignoring proper safety precautions. Follow these safety precautions when welding aluminum:
- Wear protective clothing, including a welding helmet, gloves, and a welding jacket.
- Use proper ventilation to prevent exposure to harmful fumes and gases.
- Use a welding curtain or screen to protect nearby individuals and objects from sparks and debris.
- Use a fire extinguisher and have a first aid kit on hand.
- Follow all manufacturers' instructions and safety guidelines.
Tips for Successful Aluminum Welding
To achieve successful aluminum welding, the following tips should be followed:
- Clean the aluminum surface thoroughly to remove any oxide layer or other contaminants.
- Use proper clamping and fixturing to prevent warping and distortion.
- Use the correct welding technique and parameters for the thickness and type of aluminum welded.
- Use a shielding gas compatible with aluminum, such as argon or helium.
- Practice, practice, practice! Aluminum welding requires skill and experience, so practicing and honing your skills regularly is essential.
How to Weld Aluminum with MIG - Step-by-Step Guide
MIG welding is the most common method used for welding aluminum. The following is a step-by-step guide on how to weld aluminum with MIG:
- Clean the aluminum surface thoroughly to remove any oxide layer or other contaminants.
- Choose a welding wire compatible with aluminum and the MIG welding machine.
- Set the MIG welding machine to the correct parameters for the thickness and type of aluminum welded.
- Use proper clamping and fixturing to prevent warping and distortion.
- Begin welding, moving the gun back and forth while maintaining a consistent distance from the workpiece.
- Use a shielding gas compatible with aluminum, such as argon or helium.
- Continue welding until the joint is complete.
Common Mistakes to Avoid While Welding Aluminum
The following are common mistakes to avoid while welding aluminum:
- Overheating: Overheating can cause burn-through, warping, and distortion, and keeping the heat input low and maintaining a consistent speed while welding is essential.
- Poor Fit-Up: Poor fit-up can cause gaps, porosity, and weakened welds. Make sure the pieces fit snugly before welding.
- Contamination: Contamination can weaken the weld and cause porosity, so clean the aluminum surface before welding to prevent exposure to contaminants during welding.
- Inadequate Shielding Gas: Inadequate shielding gas can cause porosity, weakened welds, and contamination. It is crucial to use the correct shielding gas and ensure it flows properly during welding.
FAQs About Welding Aluminum
- Can you weld aluminum to steel? Yes, it is possible to weld aluminum to steel using specific techniques, such as mechanical fastening, adhesive bonding, friction stir welding, or MIG welding.
- Can you stick weld aluminum? Yes, it is possible to stick-weld aluminum using specialized equipment and techniques. However, stick welding is rarely used for welding aluminum due to its lower quality results and slower speed.
- How do you weld aluminum to steel? Welding aluminum to steel requires specific techniques and considerations, such as mechanical fastening, adhesive bonding, friction stir welding, or MIG welding.
In Sum
Welding aluminum is more challenging than welding steel because of its unique properties, such as high thermal conductivity, low melting point, and thin oxide layer. However, successful aluminum welding is possible with the right techniques, equipment, and experience.
Following the tips and guidelines outlined in this article can improve your aluminum welding skills and achieve high-quality results.