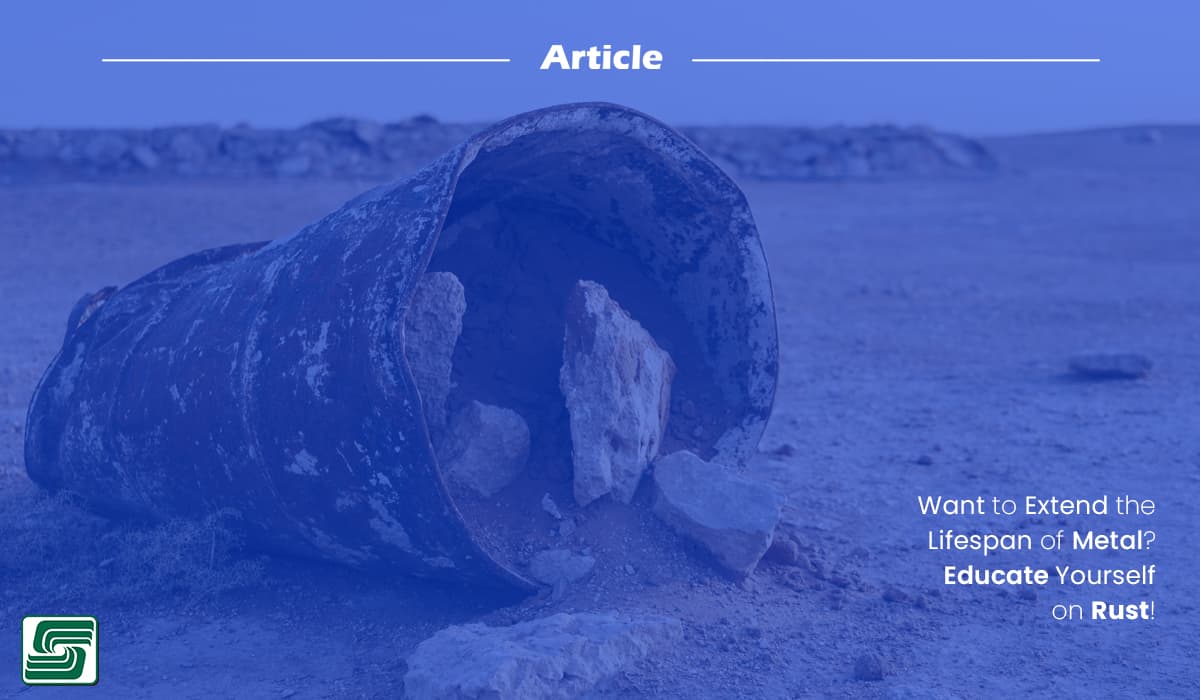
Metal fabrication is pivotal in various industries, from construction and automotive to aerospace and manufacturing.
Corrosion resistance is crucial in metal projects as it directly impacts the durability and performance of fabricated metal products.
According to a study by NACE International, corrosion costs the US economy (pdf) about $276 billion annually, encompassing direct costs like repairs, maintenance, and replacements, as well as indirect costs such as lost productivity and environmental impact.
The insidious effects of rust and corrosion devastate metallic components as they not only impair the functionality of the parts but also mar their appearance, significantly reducing their aesthetic appeal and overall lifespan.
The gradual degradation of the metal from rust and corrosion weakens the structure and causes unsightly blemishes, making it crucial to take proactive measures to prevent these issues.
Understanding Corrosion Resistance in Metal Fabrication
Corrosion resistance in metal fabrication is influenced by several key factors that play a critical role in determining the longevity and reliability of metal products.
Factors Affecting Corrosion Resistance
Several factors affect corrosion resistance, including:
- The type of metal used: stainless steel exhibits exceptional corrosion resistance because of its chromium content, while aluminum's natural oxide layer provides inherent protection against corrosion.
- Surface preparation techniques: cleaning, degreasing, and etching cannot be overstated in enhancing corrosion resistance. Properly prepared surfaces ensure better adhesion for protective coatings and minimize the risk of corrosion initiation.
- Welding methods and environmental factors: exposure to moisture and harsh chemicals either bolsters or compromises the corrosion resistance of fabricated metal components.
Improving Corrosion Resistance
Besides the three factors listed above, several methods are available for improving corrosion resistance.
- Applying protective coatings to metal substrates is critical when improving resistance. But, the key to great protective coatings is surface preparation.
- Effective surface preparation methods, such as abrasive blasting or chemical treatments, create an ideal foundation for promoting superior adhesion of protective coatings.
- Protective coatings, like paint or powder, are a robust defense against corrosion by forming a barrier between the metal substrate and corrosive elements.
These coatings add both protection and aesthetic appeal to metal products.
Metal Fabrication Threats
Rust and corrosion pose significant threats to the integrity and longevity of metal fabrication projects, causing a comprehensive understanding of their nature and effective prevention methods.
Understanding Rust and Corrosion
Distinguishing between rust and corrosion is crucial to understanding their distinct characteristics and impact on metal components.
What's the Difference Between Rust and Corrosion?
Corrosion and rust are often used interchangeably, but there are differences between the two.
Traditional vs. Innovative Rust Prevention Methods
Traditional rust prevention methods have advantages and disadvantages, from simple techniques like oiling or greasing to more complex approaches like galvanization or sacrificial coatings.
One innovative way to protect metal is the use of nanocoatings.
Nanocoatings have proven to be a revolutionary solution for preventing rust in various industries, such as aerospace, automotive, and the military, where corrosion can have significant consequences.
Nanocoatings are a type of thin film coating that offers exceptional benefits. They are engineered to provide superior adhesion, durability, and resistance to environmental stressors, such as corrosion, abrasion, and oxidation. Nanocoatings are also known for their ease of application, making them a popular choice for various industrial and commercial applications.
In addition, they are environmentally friendly and do not contain harmful chemicals, making them a safer option than traditional coating methods.
By providing a highly durable and long-lasting barrier against rust and other forms of corrosion, nanocoatings are helping to ensure the longevity and reliability of critical equipment and infrastructure.
Proactive Rust Prevention Techniques
Sitting back and waiting for rust to appear on costly metal fabrication projects isn't a great plan. There are situations where a proactive approach becomes a game-changer. One such approach for consideration is preventive maintenance programs.
Implementing preventive maintenance practices is crucial in reducing the risk of rust formation. Regular inspections, cleaning, and prompt repair of any surface damage significantly impede the progression of rust.
To further reduce the risk of rust formation, storing items properly and controlling the environment by lessening exposure to moisture and oxygen is important. By doing so, we avoid rust formation and protect our metal.
For instance, car bodies are susceptible to surface rust that escalates if left untreated. A seemingly small patch of surface rust on a vehicle spreads rapidly throughout the entire body, leading to extensive damage that causes costly repairs.
In Sum
Rust protection is pivotal in enhancing the durability and longevity of metal projects across various industries. Understanding and addressing the root causes of rust formation is fundamental in implementing proactive measures to mitigate its impact.
Combining preventive maintenance practices and advanced protection techniques, such as protective coatings and galvanization, helps ensure the sustained resilience of metal fabrication projects.