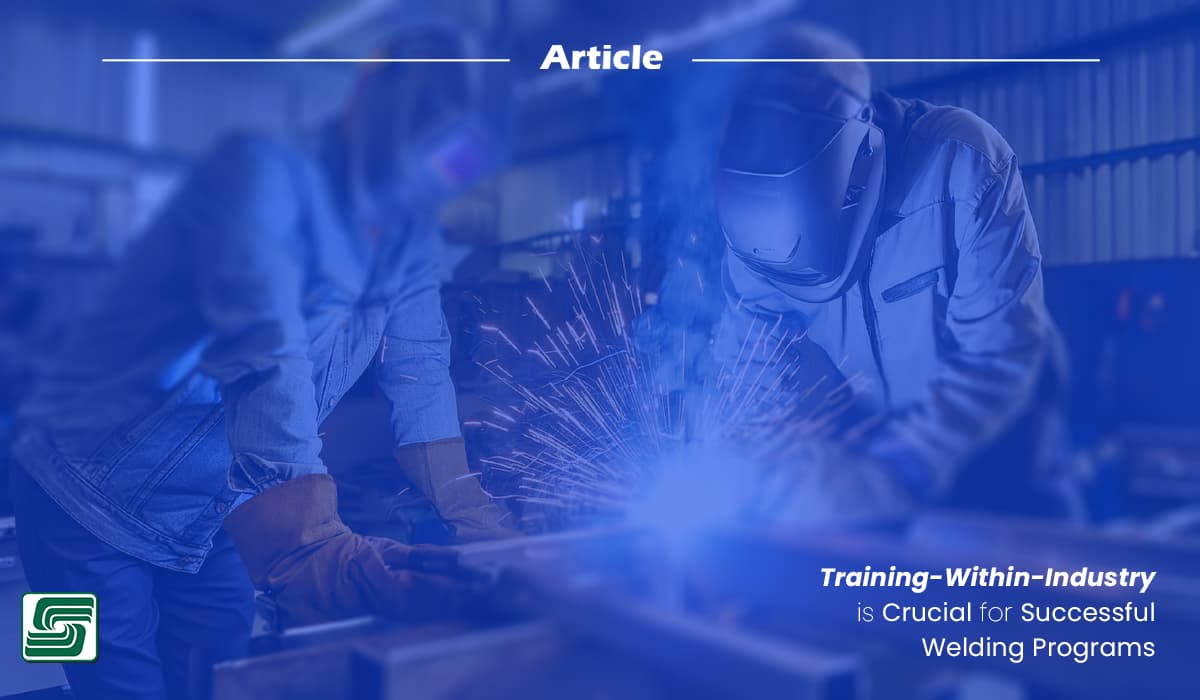
The significance of training-within-industry (TWI) cannot be overstated in welding. Originating from a rich historical background, TWI has shaped the welding landscape.
Understanding Training-Within-Industry
Understanding the fundamental aspects of training-within-industry (TWI) is crucial when considering its implementation. Various elements within TWI shape the training process.
Definition and Components of TWI
- Job Instruction (JI): In TWI, Job Instruction (JI) stands out as a cornerstone. It involves breaking down tasks into smaller steps, ensuring clarity and precision in training delivery.
- Job Methods (JM): Job Methods (JM) within TWI focuses on optimizing processes by encouraging innovation and efficiency in task execution. This component emphasizes continuous improvement and streamlining workflows.
- Job Relations (JR): Within TWI, Job Relations (JR) are significant in fostering positive workplace relationships. They emphasize effective communication, conflict resolution, and team dynamics to enhance productivity.
Historical Context and Development
Exploring the historical context of TWI unveils its evolution from traditional industrial practices to a structured training method. Over time, TWI has adapted to meet the changing needs of industries worldwide, reflecting its enduring relevance.
Importance in Modern Industry
Training-within-industry cannot be underestimated in today's industrial landscape. Its principles align with contemporary demands for efficiency, quality, and skilled workforce development. Implementing TWI practices ensures organizations remain competitive and adaptable in an ever-evolving market environment.
TWI was a workforce training program developed in the United States during World War II to rapidly train workers in manufacturing and industrial jobs to support the war effort. It was created in 1940 by the United States Department of War in collaboration with private industry leaders and experts.
The program aimed to increase productivity and quality in manufacturing by providing structured training methods for supervisors and workers. It focused on developing essential skills like job instruction, job methods, job relations, and program development.
Some key historical points about TWI:
- It emerged from the need to quickly ramp up industrial production for the war, rapidly integrating many new workers into manufacturing roles.
- TWI drew on scientific management principles and industrial psychology to create standardized training techniques.
- Major companies, such as General Electric, General Motors, Westinghouse, and others, worked with the government to develop and implement TWI methods.
- By 1945, over 1.7 million industrial supervisors and workers had received TWI training across the United States.
- After WWII, TWI methods spread to other countries like Japan, which influenced lean manufacturing and Kaizen practices.
TWI was an innovative workforce training solution created under the pressures of wartime production needs that had a lasting impact on global industrial training and management philosophies.
The Intersection of TWI and Welding
In welding, training-within-industry catalyzes the enhancement of essential skills crucial for mastering the craft. Individuals improve their proficiency and precision in effectively executing welding tasks by integrating TWI principles into welding practices.
How TWI Enhances Welding Skills
Enhancing welding skills through TWI involves a structured approach emphasizing meticulous attention to detail and adherence to best practices. By instilling a continuous learning and improvement culture, TWI enables welders to refine their techniques, resulting in superior weld quality and durability.
Industry Standards and TWI
Integrating training-within-industry aligns with established industry standards governing welding practices. By adhering to these benchmarks and incorporating TWI protocols, organizations ensure compliance with regulatory requirements while fostering a culture of excellence and precision in welding operations.
Benefits of Implementing TWI in Welding
Implementing TWI in welding yields many advantages that significantly impact the overall quality, safety, and productivity of welding operations.
Improved Quality and Consistency
- Enhances the precision and accuracy of welds through standardized training methodologies
- Ensures uniformity in welding techniques, leading to consistent output quality
- Facilitates adherence to established quality control measures for impeccable weld integrity
- Promotes a culture of excellence by emphasizing meticulous attention to detail in every welding task
Enhanced Safety Measures
- Prioritizes safety protocols by instilling best practices for injury prevention during welding activities
- Fosters a safety-conscious environment through comprehensive training on hazard identification and mitigation
- Empowers welders with the knowledge and skills to handle equipment safely, reducing workplace accidents
- Cultivates a safety-oriented mindset among personnel, promoting a secure working environment for all team members
Increased Productivity
- Optimizes workflow efficiency by streamlining processes and eliminating unnecessary steps in welding tasks
- Boosts operational productivity by enhancing skill levels and minimizing errors in weld fabrication
- Reduces downtime associated with rework or corrections, maximizing output within set timelines
- Encourages continuous improvement initiatives that drive productivity enhancements across all facets of welding operations
Cost Efficiency
- Enhances financial viability by optimizing resource allocation and minimizing wastage in welding processes
- Ensures cost-effective practices through efficient utilization of materials and streamlined production workflows
- Maximizes return on investment by reducing expenses associated with rework and errors in welding operations
- Promotes sustainable cost management strategies that enhance profitability and competitiveness in the welding industry
Practical Applications of TWI in Welding
Implementing TWI in welding manifests through various practical applications that enhance skill development and operational efficiency. These applications encompass structured training programs, on-the-job techniques, and the pivotal roles of supervisors and managers in fostering a culture of excellence.
Training Programs and Workshops
- Start specialized training programs tailored to address specific welding techniques and industry requirements.
- Conduct workshops focusing on hands-on experience to reinforce theoretical knowledge with practical application.
- Collaborate with industry experts to design comprehensive training modules that align with evolving welding standards.
- Implement interactive sessions that engage participants in simulated welding scenarios to enhance skill proficiency.
On-the-Job Training Techniques
- Integrate on-the-job training techniques into daily welding operations to provide real-time learning opportunities.
- Assign experienced welders as mentors to guide novices through practical tasks and troubleshoot challenges effectively.
- Rotate job responsibilities among team members to broaden skill sets and promote cross-functional expertise.
- Use feedback mechanisms to evaluate performance and identify areas for improvement, ensuring continuous learning and skill enhancement.
Role of Supervisors and Managers
- Empower supervisors to oversee training initiatives, monitor progress, and provide constructive feedback to enhance skill development.
- Equip managers with the tools to create a conducive learning environment that fosters collaboration and knowledge sharing among team members.
- Delegate responsibilities based on individual competencies, optimizing workflow efficiency while nurturing organizational talent.
- Establish clear communication channels between supervisors, managers, and welders to ensure alignment with organizational goals and quality standards.
Use of Simulation and Virtual Reality
- Implementing simulation technology in welding training allows for immersive learning experiences that replicate real-world scenarios.
- Virtual reality applications provide a dynamic platform for welders to practice techniques in a controlled, risk-free environment.
- Simulated welding environments enable trainees to hone their skills through interactive exercises and scenario-based challenges.
- Virtual reality simulations offer a hands-on approach to learning, enhancing muscle memory and spatial awareness in welding tasks.
- Virtual reality tools facilitate the visualization of complex welding processes, aiding comprehension and skill development.
- Simulation training enhances proficiency by offering immediate feedback on technique execution and identifying areas for improvement.
- Virtual reality platforms simulate diverse welding conditions, preparing welders for various challenges in actual work settings.
- Incorporating virtual reality into TWI programs revolutionizes traditional training methods, fostering innovation and adaptability in skill acquisition.
Challenges and Solutions in TWI Implementation
Common Obstacles
- Inadequate Training Resources: Limited access to comprehensive training materials and skilled instructors hinders the effective implementation of TWI in welding.
- Resistance to Change: Some individuals may resist adopting new training methodologies, posing a challenge to integrating TWI practices into existing welding processes.
- Lack of Management Support: Without strong leadership backing and organizational commitment, the successful execution of TWI initiatives may face obstacles in garnering widespread acceptance.
- Skill Knowledge Gaps: Identifying and addressing gaps in welders' skill levels presents challenges in tailoring TWI programs to meet individual learning needs effectively.
Strategies for Overcoming Challenges
- Resource Expansion: Investing in diverse training resources, including online modules, practical workshops, and expert-led sessions, enhances the accessibility and quality of TWI programs.
- Change Management Initiatives: Implementing structured change management strategies that emphasize the benefits of TWI, provide clear communication channels, and offer continuous support mitigates resistance and fosters a culture of openness towards innovation.
- Leadership Engagement: Engaging with management at all levels to communicate the value of TWI, align training objectives with organizational goals, and secure ongoing support is essential for overcoming resistance and ensuring successful implementation.
- Personalized Learning Paths: Tailoring TWI programs to address individual skill gaps through competency assessments, personalized coaching, and targeted skill development plans bridges knowledge deficiencies effectively.
Role of Continuous Improvement
- Embracing a culture of continuous improvement in welding practices is paramount for enhancing operational efficiency and elevating quality standards.
- Implementing systematic evaluation processes allows organizations to identify areas for enhancement and streamline workflows effectively.
- By fostering a mindset of ongoing development, welders refine their skills, optimize performance, and adapt to evolving industry requirements seamlessly.
- Regular feedback mechanisms enable teams to proactively address challenges, drive innovation, and maintain a competitive edge in the welding sector.
- Prioritizing continuous improvement initiatives enhances individual proficiency and contributes to welding operations' overall success and sustainability.
Future Trends in TWI and Welding
Technological Advancements
The welding industry is witnessing a transformative shift driven by technological advancements. Innovations in welding equipment, materials, and processes are revolutionizing how welders operate.
Automation and robotics are increasingly integrated into welding practices, enhancing precision and efficiency on the shop floor.
The emergence of advanced welding techniques, such as laser welding and friction stir welding, is reshaping the landscape of modern welding applications.
These technological strides not only streamline production processes but also elevate the quality and durability of welds to meet evolving industry standards.
Evolving Industry Needs
As industries evolve, so do the demands placed on welding professionals. The evolving industry needs a dynamic approach to TWI to align with changing requirements.
Welders are expected to adapt to new materials, technologies, and safety protocols as they navigate complex projects in diverse sectors. The emphasis on sustainable practices, cost efficiency, and regulatory compliance underscores the importance of continuous skill development through TWI programs.
Staying attuned to shifting industry dynamics and upskilling, welders remain competitive in a rapidly changing market environment.
Predictions and Forecasts
Predictions show a continued trajectory of growth and innovation in TWI and welding. Forecasts suggest an increased integration of digital tools and augmented reality solutions into training programs to enhance welders' learning outcomes.
The rise of remote training modules and virtual simulations is projected to offer unprecedented flexibility in skill acquisition, catering to a global workforce seeking accessible training avenues.
Advancements in material science and metallurgy are expected to drive breakthroughs in weld quality assessment and defect detection methods, ensuring welders uphold stringent quality standards across diverse applications.
Digital Tools Integration
Implementing advanced digital tools in welding practices enhances precision and efficiency in training programs.
- Virtual reality simulations provide immersive learning experiences, replicating real-world welding scenarios for enhanced skill development.
- Augmented reality solutions offer interactive platforms that engage welders in dynamic training exercises, fostering adaptability and innovation.
- Remote training modules enable global access to specialized welding techniques, catering to a diverse workforce seeking continuous skill enhancement.
Integrating digital tools revolutionizes traditional training methods, emphasizing practical application and hands-on learning experiences for welders. Advanced software applications streamline the training process, providing immediate feedback on technique execution and facilitating skill improvement.
- Digital tools facilitate visualizations of complex welding processes, aiding in comprehension and proficiency development among trainees.
- Using simulation technology in training-within-industry programs offers a forward-thinking approach to skill acquisition, aligning with industry demands for technological proficiency.
Valuable Insights from Failures
- Instances, where TWI implementation lacked comprehensive training resources, highlighted the importance of investing in diverse learning materials to ensure the effectiveness of training programs.
- Challenges arising from resistance to change emphasized the need for structured change management strategies that promote the benefits of TWI and foster a culture receptive to innovation.
- Failures because of skill knowledge gaps underscored the significance of personalized learning paths tailored to address individual competency levels effectively within TWI frameworks.
Comparative Analysis of Training Methodologies
- Comparing traditional welding training approaches to training-within-industry reveals a distinct shift towards structured methodologies prioritizing skill development and operational efficiency.
- The comparative analysis showcases how TWI enhances safety measures, promotes continuous improvement initiatives, and aligns with evolving industry needs more effectively than conventional training methods.
- By evaluating the outcomes of different training methodologies, organizations discern the tangible benefits of adopting training-within-industry practices for sustainable growth and excellence in welding operations.
Global Perspectives
- Welding practices vary across different regions, reflecting cultural influences and industry standards.
- International collaborations in welding research promote knowledge exchange and technological advancements.
- Global welding certifications enhance professional mobility and recognition on a worldwide scale.
- Cross-border initiatives in welding education foster a diverse talent pool and skill-sharing opportunities.
- Harmonizing welding regulations globally ensures consistent quality and safety standards in the industry.
In Sum
Remember, embracing training-within-industry is not just a choice but a strategic imperative for welding professionals aiming for unparalleled expertise and operational efficiency in a dynamic industrial landscape.