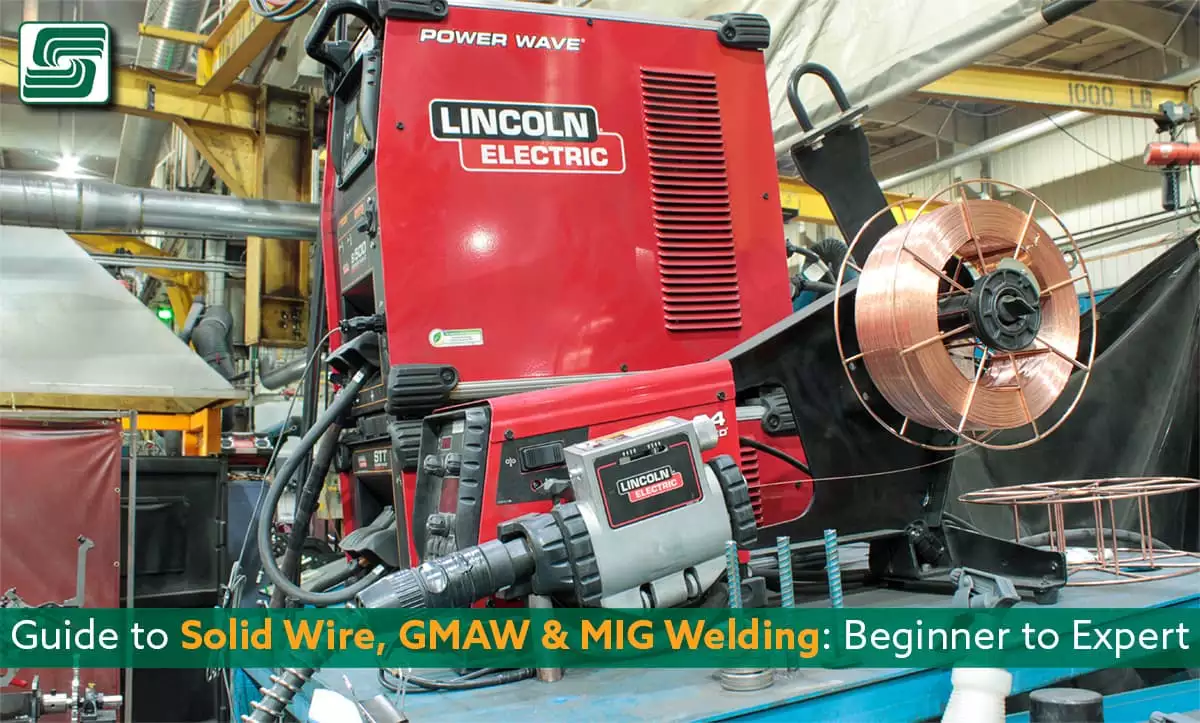
Welding is a process of joining two or more pieces of metal together by melting and fusing them. It is an essential process in various industries, such as construction, manufacturing, aerospace, and automotive.
Welding has been around for centuries and has evolved over time. As technology advances, welding techniques have also become more sophisticated, efficient, and safer.
Solid wire welding, gas metal arc welding (GMAW), and metal inert gas (MIG) welding are the most commonly used techniques.
A Quick Welding Overview
Welding is a critical function in the manufacturing industry as it allows the production of large structures that are impossible to create by any other means. From simple everyday items like DIY shelving to complex components like drilling platforms or aircraft parts, welders play a vital role in constructing these structures.
The importance of welding cannot be overstated when considering the safety implications of welded joints. Welds must be created correctly to ensure they can bear the necessary load without experiencing failure, which could result in damaging or catastrophic consequences.
Many industries require strict adherence to standards such as ISO 3834, which sets out requirements for quality control in all aspects of welding work, including design specification, materials selection, testing, and training requirements for welders.
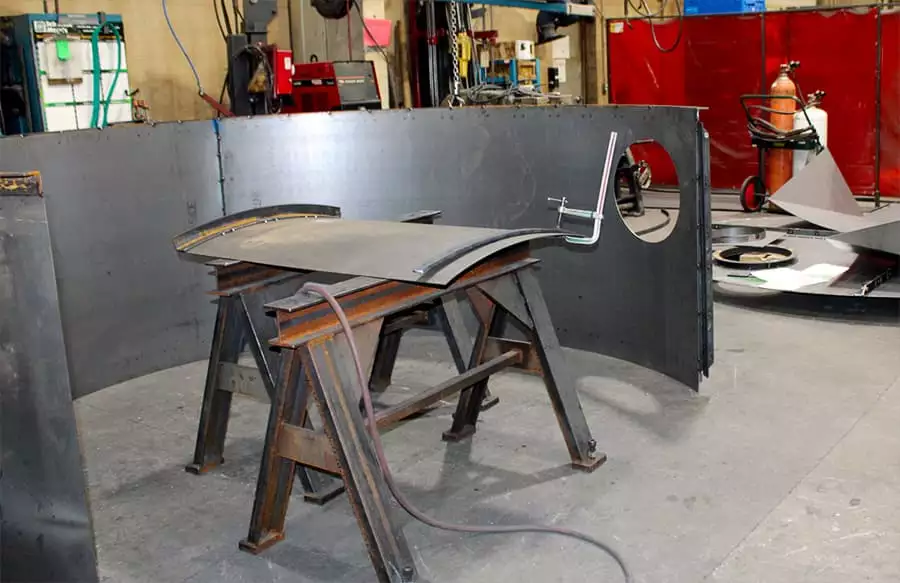
GMAW and MIG Welding
Solid wire welding is a type of GMAW or MIG using a solid electrode wire instead of a flux-cored wire. The electrode wire is fed through a gun connected to a power source while shielding gas flows through the nozzle onto the base material surrounding the electrode arc.
In GMAW, also known as MIG (Metal Inert Gas), Argon or helium gas serves as shielding gases for protecting the weld zone from contaminants in the air.The continuous welding process allows for faster work with higher productivity than other welding techniques.
In MIG welding, Argon or a combination of Argon and carbon dioxide shields gases. MIG welding is known for its versatility in welding different metals with varying thicknesses and can produce high-quality welds with a clean finish.
Solid wire welding uses similar equipment as GMAW or MIG, but without flux, as the shielding gas protects from atmospheric oxygen and nitrogen which could cause porosity and weaken the welded joint. Solid wire's consistent size and shape deliver a more stable arc, allowing better control of the weld puddle, resulting in higher quality welds, especially on thin gauge materials.
These processes have become popular due to their efficiency, versatility, speed, and ability to create high-quality welds even when working on delicate materials.
In the following sections, we'll look at each type of welding technique to provide detailed information on their advantages and disadvantages, along with preparation techniques involved to help you decide which technique suits your requirements best.
Solid Wire Welding
Solid wire welding, gas metal arc welding (GMAW), or metal inert gas (MIG) welding is a fusion welding process where a continuous solid wire electrode is fed through a wire feeder to the weld. The electrode wire is melted and fuses the base material.
The process involves using an electric arc between the electrode wire and the base material. The arc melts the wire, creating a pool of molten metal that fuses the base material together.
A shielding gas fed through a nozzle attached to the torch protects the weld pool from atmospheric contamination. Solid wire welding is commonly used in manufacturing and construction industries because it allows for high production rates and produces high-quality welds requiring minimal post-weld clean-up.
Solid Wire Welding Advantages
One of the main advantages of solid wire welding is its ability to produce consistent, high-quality welds at high speeds. The process allows for continuous electrode wire feeding, eliminating downtime associated with changing out rods in other welding processes.
Another advantage is that it can be used on various materials such as carbon steel, stainless steel, and aluminum alloys, making it useful in many industries, such as automotive manufacturing, aerospace engineering, pipeline construction, and shipbuilding.
Solid wire welding produces less spatter than other welding processes, such as stick or flux-cored arc welding, which means less post-weld clean-up after completing each weld.
Solid Wire Welding Disadvantages
One disadvantage of solid wire welding is that it requires an external shielding gas supply to protect the molten weld pool from oxidation during cooling, meaning additional equipment, such as tanks or bottles, may be necessary to store and transport these gases.
Another disadvantage is that higher skill levels are required to operate the equipment properly. Operators must be able to adjust the settings on the machine correctly and maintain proper technique and weld placement to produce high-quality welds.
Solid Wire Electrodes Used
Solid wire welding electrodes are typically made from carbon steel, stainless steel, or aluminum alloys. The type of electrode used depends on the base material being welded and the specific application.
Carbon steel electrodes are commonly used for welding low-carbon steels because of their higher deposition rate than other types of electrodes.
Stainless steel electrodes are used for welding stainless steel materials because they increase corrosion resistance.
However, aluminum alloy electrodes are used for welding aluminum materials because they create strong, high-quality welds.
In addition to these three main types of solid wire electrodes, other specialized types, such as nickel-based or copper-nickel alloys, can be used for specific applications where high heat or corrosion resistance is required.
Solid wire welding is a versatile and efficient process that produces high-quality welds with minimal post-weld clean-up requirements, making it a popular choice in manufacturing and construction industries where speed and quality are both important factors.
Gas Metal Arc Welding
Gas Metal Arc Welding (GMAW), or Metal Inert Gas (MIG) welding, is an arc welding process that uses a consumable electrode wire and an externally supplied shielding gas to create a high-quality weld.
The electric arc is established between the workpiece and the wire, which melts the wire and fuses it with the workpiece.
GMAW is commonly used in various industries for its versatility, speed, and ease of use. The welding process begins when a wire electrode is fed through the torch into the weld pool.
The torch also releases a stream of shielding gas from a nozzle around the electrode tip protecting the molten weld pool from contamination by atmospheric gases such as oxygen or nitrogen. As such, GMAW joins many different materials, including steel, aluminum, nickel, copper, and stainless steel.
GMAW Advantages & Disadvantages
One main advantage of GMAW is its versatility in terms of material thicknesses that can be welded from thin sheet metals up to thick plates. It also has high deposition rates allowing for faster production times and reducing labor costs.
This process yields excellent control over filler metal placement during welding due to steady feeding rates from wire feeders allowing accurate placement into tight spaces.
However, some disadvantages come with this method, such as limited accessibility because it requires two hands - one hand steadies the torch while the other feeds wire leading to limited angles or positions achievable by this technique.
Additionally, gases are required for shielding during this process which can add to operational costs and increase complexity overall.
Gases Used
The gases used in this process vary depending on the welded material and desired finish. Different combinations of gases provide various atmospheres around the weld pool to produce different welding characteristics.
Argon and carbon dioxide are the most commonly used gases in GMAW. Argon is used for welding non-ferrous metals such as aluminum alloys.
In contrast, carbon dioxide is used for welding mild steel. Other gases, such as helium and oxygen, can be mixed with these core gases in different ratios depending on the desired properties in the final weld.
GMAW is a popular welding process because it offers a good balance between speed and quality while being relatively simple to operate.
However, careful consideration must be given to material selection, gas choice, shielding gas flow rates, and wire feeder settings for optimal results to be achieved during this process.
Metal Inert Gas Welding
MIG welding is a type of arc welding using a continuously fed wire electrode and a shielding gas to protect the weld from contaminants in the atmosphere.
The process involves creating an electric arc between the wire electrode and the metal being welded, producing heat that melts and fuses the metal.
Because of its speed and versatility, MIG welding is commonly used in automotive, construction, and manufacturing industries. The wire electrode used in MIG welding comes in various sizes and materials, such as steel, aluminum, or stainless steel.
The shielding gas used depends on the type of material being welded. For example, Argon is commonly used for aluminum, while a mix of Carbon Dioxide (CO2) and Argon is used for steel.
MIG welding Advantages & Disadvantages
One of the main advantages of MIG welding is its speed. The process can be automated, which increases efficiency compared to other manual welding processes—ideal for high-volume production work.
Another benefit is that MIG welding produces clean welds with minimal splatter or waste material, making it easy to produce high-quality welds with minimal clean-up time required. Also, there’s no need to manually change electrodes during operation, which further boosts productivity.
However, one disadvantage of MIG welding is that it requires much more equipment than other metal joining methods, including gas cylinders for supplying shielding gases which can add extra costs to your overall operation.
MIG and Tungsten Inert Gas (TIG) Welding Comparison
There are several differences worth noting When comparing MIG to Tungsten Inert Gas (TIG) welding—another popular type of arc welding.
TIG welding uses a tungsten electrode, which does not melt during the process and only acts as an arc initiator. The filler material is supplied separately, making TIG welding ideal for precise, high-quality welds on thin materials.
On the other hand, MIG welding can be more versatile for thicker materials or when working with long or continuous welds.
MIG welding produces faster results and requires less operator skill than TIG welding. MIG welding is generally better suited for high-volume production work where speed and efficiency are critical factors. At the same time, TIG is often preferred when high quality and precision are needed in low-volume projects.
Equipment List
The Power Source
The power source is the heart of any welding machine, supplying the electrical energy that melts the filler wire and generates the weld pool. Different types of power sources are available for solid wire, GMAW, or MIG welding machines.
The most common type of power source used in these welding processes is a constant voltage (CV), which provides a stable voltage output and allows for consistent welds.
The Electrode Wire Feeder
The electrode wire feeder is another important piece of equipment for solid wire, GMAW, or MIG welding machines. It feeds the electrode wire to the welding gun at a consistent rate. The speed at which the feeder delivers the wire determines how much filler material is deposited into the weld pool.
Examples of wire feeders includes:
- Bench-top Feeders: used for low-volume applications
- Portable Feeders: useful when working on large structures
- Push-pull Feeders: maintain a constant pressure on soft wires to ensure they do not tangle.
Choosing an electrode feeder that matches your specific application requirements is essential.
The Shielding Gas Supply
Shielding gas protects the molten metal from atmospheric gases such as oxygen and nitrogen during solid wire, GMAW, or MIG welding. It allows for clean and strong welds while minimizing porosity and oxidation.
Some examples of shielding gases include:
- Argon: commonly used with aluminum
- Carbon Dioxide: widely used with steel alloys
- Helium: commonly used with stainless steel.
Selecting an appropriate shielding gas that matches your specific application requirements is crucial.
The Welding Torch/Gun
The welding gun is the handheld tool used to manipulate the electrode wire and shielding gas while generating the weld. It's made up of a handle, trigger, contact tip, nozzle, and diffuser.
- Air-cooled Guns: useful for low-temperature applications
- Water-cooled Guns: allow for higher amperages and longer duty cycles.
Choosing a welding gun that matches your specific application requirements is essential.
The Ground Clamp
The ground clamp completes the circuit between the workpiece and the power source, ensuring a stable electrical connection between these two components. Choosing suitable equipment for solid wire, GMAW, or MIG welding is critical for achieving high-quality welds.
Each equipment type serves a unique welding purpose.
Understanding how each piece of equipment works and selecting appropriate equipment according to your specific needs helps you achieve consistent results whenever you weld.
Techniques Used in Solid Wire, GMAW, or MIG Welding
Preparing the Base Material
Before starting the welding process, it is crucial to prepare the base material, which involves cleaning and removing contaminants such as rust, oil, or paint which can affect the weld quality.
A wire brush or grinding wheel can be used to clean the surface of the base material. The edges of the metal should also be chamfered so that there is enough space for sufficient penetration during welding.
In addition to cleaning and chamfering, it is important to ensure that the base materials are correctly positioned before welding begins. Properly aligning and clamping the materials together will result in a stronger weld.
Welding Techniques
The first step in solid wire, GMAW, or MIG welding is setting up equipment correctly, including a power source, electrode wire feeder, shielding gas supply, and other necessary equipment.
The next step is selecting appropriate settings for current and voltage based on factors such as material thickness and type of electrode used. It is recommended to start with lower settings and gradually increase the voltage while observing how well they perform.
Maintaining proper arc length throughout the welding process is essential because this affects heat input into the metal, resulting in porosity (holes in the weld). The distance between the electrode tip and the work piece should be around 1/4 inch for optimum results.
Consistent travel speed should be maintained while welding to not produce uneven beads, which weakens the welded joints.
Post-weld clean-up includes the removal of any slag (metallic residue) from the weld area, which requires chipping with a hammer or wire brush and grinding off any spatter (small droplets) left behind by molten metal during the welding process.
In Sum
The key to achieving strong welds is properly preparing the base material and equipment setup, selecting appropriate settings, and maintaining consistent arc length and travel speed throughout the welding process.
With these techniques in mind, welders can produce quality welds that meet the standards required for their respective applications.