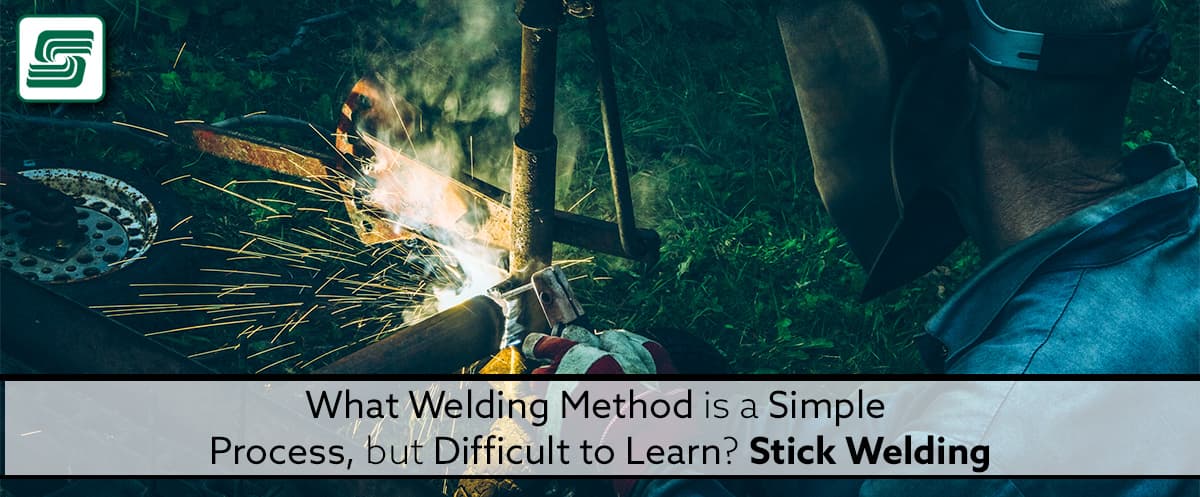
Shielded Metal Arc Welding (SMAW), or Stick Welding, is an arc welding process completed by hand using an electrode covered with a flux laying the weld. The method uses a welding power supply that arcs the melting electrode to the metal. As it does so, it forms a small weld pool. When the weld pool cools, it creates a weld bead. The flux coating role gives off a shielding gas when the electrode melts, helping protect the weld area.
SMAW welders need to strike an arc between the electrode and the metal. Lightly touching the electrode to the metal creates the arc. The arc started, and the electrode and the metal melted, creating the weld bead. WeldNotes.com provides an excellent overview of the SMAW process.
SMAW is the most widely used form of welding, mostly used for ferrous metals of all thicknesses, like carbon steels, stainless steels, alloy steels, and iron.
We find welding using the SMAW method in many industries, such as:
- Construction
- Shipbuilding
- Petroleum
- Field Repair
- Structural Welding
Invention
Two people in history are responsible for SMAW. In 1888, Russian inventor Nikolay Slavyanov introduced the concept of arc welding with consumable metal electrodes. Although Nikolay Bernardos invented arc welding, Slavyanov was the first to use this welding method practically.
Slavyanov worked at the Perm cannon factories and used the electric arc to liquefy metal to improve the quality of metal for forging gun barrels. Using consumable metal electrodes, he developed a better method of degassing the metal fluid to avoid blowholes weakening the strength of the metal.
In 1890, Charles L. Coffin patented an arc welding process that used metal electrodes. While Slavyanov used the electric arc for casting metal in a mold, Coffin’s idea was to use melted metal as a filler material in the joint, creating a weld.
Today SMAW welding is still a manual trade, but electrodes have become more advanced, and the equipment used is much more efficient.
Process
SMAW is a relatively simple process because the needed equipment is simple.
- Power supply
- Electrodes
- Electrode holder
- Clamp
- Welding leads
- Correct PPE
- Electrodes
Power Supply
AC or DC forms the arc between the working metal piece and the electrode. Arc length, determined by the electrode’s type and diameter, determines the amount of required voltage. Higher amps provide the power needed for welding thicker metals.
Electrodes
Knowing what electrodes to use and how they work is essential. There are three groups of electrodes:
- Fast-fill: electrodes that melt fast-for fast, flat, and horizontal welding
- Fast-freeze: electrodes that solidify quickly used for welding in all positions
- Fill-freeze: electrodes that are intermediate and ideal for general use.
Electrodes have a flux coating, which converts to gas, giving weld protection by reducing contamination and increasing the joint’s purity and weld quality.
Skill Level
Although SMAW welding is relatively simple, the learning curve may be higher than other welding methods. Despite its simplicity, the process needs skilled and experienced welders for quality results.
Advantages and Disadvantages
Advantages
Some advantages are comparatively significant:
- No separate shielding gas is required.
- SMAW welding uses basic equipment.
- A wide range of types and sizes of electrodes are available.
- Operators can use it with a variety of metals.
- It works well outdoors and indoors, rain or shine.
- Operators can learn it fairly quickly.
- It’s suitable for a range of projects.
Disadvantages
Disadvantages of stick welding include:
- Need to remove slag after welding. Slag entrapment is also an issue in SMAW forming inclusions, which need to be removed.
- Unused electrode stubs—need to stop welding when reaching the last 2 inches of the electrode.
- Spatter
- The slow relative speed of SMAW.
- Spatter cleanup and slag removal are labor-intensive
- It creates more sparks and heat than other welding methods
- Chipping and grinding on completed welds creates harmful dust.
- Need to stop during the welding process to replace used electrode and to chip away slag
Common Stick Welding Problems
Besides the list of disadvantages, there are several problems that, if occurred, compromise the quality of the weld.
- Cracking
- Shallow penetration
- Poor fusion
- Porosity
- Wandering arc
- Unstable arc
- Undercutting
- Spatter
Cracking
Several kinds of cracks are possible along the weld leading to the chance of fractures. The three principal reasons for cracking include high sulfur, alloy, or high carbon content in the base metals. Also, there is a greater chance of cracks if the parts are rigid.
Shallow Penetration
Penetration is how deep inside the base metal the weld reaches. Because of the process used in stick welding, it is difficult to see if it has reached the correct penetration.
Poor Fusion
When a solid bead forms through the entire joint and the weld pool strongly bond both sides of a joint, proper fusion has occurred. When poor fusion occurs, it is easy to see.
Porosity
Porosity is the measure of voids in material and is not ordinarily visible. This is one of the more common issues when stick welding. If the base metal’s surface is dirty or the weld poor does not remain molten very long, gas bubbles created during the welding process don’t have time to escape.
Wandering Arc
Stray magnetic fields may cause the arc to wander off its intended direction, typically an issue when using DC.
Unstable Arc
If the arc is unstable despite proper polarity and current, there may be a simple cause: wet electrodes.
Undercutting
Although it may seem to be an aesthetic issue, when a groove develops at the base of the metal, it leads to undercutting. Fixing undercutting problems cuts production speed and is expensive.
Spatter
There is no effect of weld strength after a weld spatters, but the poor surface finish takes time resulting in increased cleanup costs.
What’s New in SMAW
The SMAW process has changed little since its invention. It still needs an arc to get the process underway, and the welder lays down a bead with the melting electrode.
The improvements in stick welding have been in advances in electrodes and welding power source innovations.
Electrode Innovations
In the old days, hydrogen cracking was a big issue. Cracking happens when the welding cracks at the joint, caused by electrodes releasing.
Introducing low hydrogen electrodes helped overcome the cracking problem. When using low hydrogen electrodes, there are some storage issues associated with them. Opening the packaging exposes the electrodes to moisture. Correctly storing the packages reduces moisture-related problems.
Using them within the 9-hour working day is advisable; otherwise, they could revert to their hydrogen-cracking behavior.
Advanced electrodes increase the strength of the welds required for military applications.
The same goes for welding high-pressure vessels such as boilers or equipment required to operate at low temperatures.
Power Innovations
Sticking an electrode is a problem caused by a natural drop in voltage, stopping the arc. Today, there are SMAW power devices designed to expect the problem. When sticking is about to happen, the power source increases the current, preventing sticking from occurring.
Inverters eliminate the need for three-phase power sources. Inverters prevent interruptions from occurring during welding, stopping dips in the power supply.
These inverter units are much easier to transport and offer much more welding versatility.
In Sum
The portability of stick welding means it is used in various industries, indoors or out. The simplicity of the equipment means the process is less expensive to set up. However, that simplicity is misleading because it is a challenging welding process to master.
Production speed is slower, and the results may not be as pretty as TIG welding, but SMAW remains one of the most popular arc welding methods.