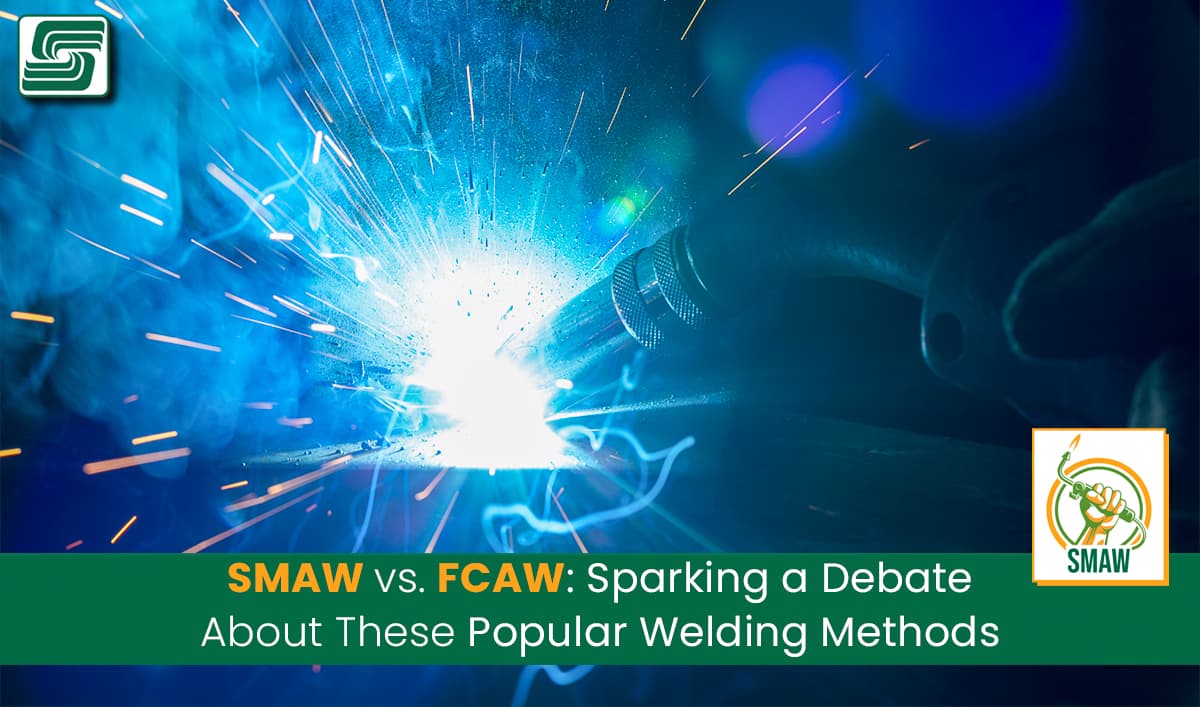
Welding is an essential process in various industries, allowing the joining of metals by applying heat and pressure.Shielded Metal Arc Welding (SMAW) and Flux-Cored Arc Welding (FCAW) have emerged as popular techniques among the many welding methods available.
These processes offer distinct advantages and disadvantages, making it crucial for welders to understand their differences to choose the most appropriate method for a particular application.
FAB Times SMAW Series
In our recent series on FAB Times, we delved deep into the world of Shielded Metal Arc Welding (SMAW). We focused on SMAW's nuances, starting with an overview of popular welding methods. The series also pits SMAW against other welding techniques, such as FCAW, GMAW, GTAW, and SAW, to help you understand which method best suits your needs.
Articles in the Series:
- How Well do You Know the 5 Most Popular Welding Methods?
Get a broad view of the top welding methods, including SMAW. Read More
- What Does it Take to Master the Art of Shielded Metal Arc Welding?
Learn what makes SMAW unique and how to master it. Read More
- SMAW vs. FCAW: Sparking a Debate About These Popular Welding Methods
Compare SMAW and FCAW to find out their pros and cons. Read More
- SMAW vs. GMAW: Unveiling the Key Differences to Decide Which is Better
Explore the differences between SMAW and GMAW. Read More
- Anyone Ever Teach you the Differences Between Stick and TIG Welding?
Understand how SMAW differs from GTAW, also known as TIG welding. Read More
- Speed Matters: How SAW Outpaces SMAW in Welding Efficiency
Learn why SAW is faster than SMAW and when to use each method. Read More
SMAW & FCAW
Before continuing, learn about SMAW in the first article of our comparison series: What Does it Take to Master the Art of Shielded Metal Arc Welding?
SMAW, also known as stick or arc welding, has stood the test of time as one of the oldest welding processes. Developed by Swedish engineer Oscar Kjellberg in 1907, SMAW uses a consumable electrode coated with flux. When the electrode comes into contact with the workpiece, the electric current creates an arc that generates intense heat.
The flux coating acts as a shield against atmospheric contamination during the welding process. FCAW is a relatively newer technique that evolved from SMAW in the mid-20th century.
FCAW employs a tubular wire electrode filled with flux, eliminating the need for separate shielding gas like in Gas Metal Arc Welding (GMAW), making FCAW more versatile and suitable for outdoor applications where wind or drafts may disperse shielding gases.
Differences Between SMAW and FCAW
Understanding the differences between SMAW and FCAW is vital for welders to make informed decisions when selecting a welding method based on specific project requirements. Each process has unique characteristics influencing factors such as weld quality, efficiency, ease of use, cost-effectiveness, and environmental considerations.
By comprehending these dissimilarities thoroughly, welders gain the ability to optimize their welding processes, resulting in improved productivity and weld integrity.
Knowing these differences allows for the appropriate selection of welding equipment and consumables, ensuring optimal performance and reducing potential risks.
Which Process Is Better?
The debate surrounding which process is superior, SMAW or FCAW, has generated much discussion within the welding community. SMAW's simplicity and versatility make it a reliable choice for various applications.
Others contend that FCAW's higher deposition rates and increased efficiency provide a competitive edge in productivity. Factors such as material type, joint configuration, environmental conditions, operator skill level, and project specifications can influence the better process.
It is important to note that there is no definitive answer to this debate because both SMAW and FCAW have their strengths and weaknesses.
Determining which process suits a particular welding job requires careful consideration of various factors.
This article comprehensively explores these differences so welders can make informed decisions based on their needs and project requirements.
In the following sections, we will discuss the specifics of each process's equipment and consumables and their advantages and limitations in detail.
SMAW - Shielded Metal Arc Welding
Shielded Metal Arc Welding (SMAW), also commonly referred to as stick welding or arc welding, is a welding process that has been in use since its invention by Oscar Kjellberg in 1907.
This method creates an electric arc between a flux-covered electrode and the workpiece, generating enough heat to melt the base metal and form a weld joint. SMAW revolutionized the welding industry, improving versatility and accessibility in various applications.
SMAW Advantages and Limitations
SMAW excels in its versatility across various environments because of its self-contained nature, allowing it to be used indoors and outdoors without needing external shielding gases. This versatility makes it particularly useful in remote or confined spaces where other welding processes might be impractical. However, SMAW has some limitations.
SMAW generally has a slower deposition rate than other processes like Gas Metal Arc Welding (GMAW) or Flux-Cored Arc Welding (FCAW), meaning it may not be the most efficient method for large-scale projects where productivity is a primary concern.
SMAW requires frequent electrode changes and manual slag removal, which increases downtime and labor costs compared to semi-automatic or automatic welding processes. SMAW remains a fundamental welding process that has stood the test of time.
Its simplicity, versatility, and suitability for various environments make it an indispensable tool in many industries. However, its deposition rate and manual operation limitations should be considered when selecting the most appropriate welding technique for specific applications.
FCAW - Flux-Cored Arc Welding
Flux-Cored Arc Welding (FCAW) is a welding process that emerged as an improvement over Shielded Metal Arc Welding (SMAW) in the mid-20th century. It was developed to address some of the limitations of SMAW and provide welders with a more efficient and versatile method.
FCAW uses a continuously fed consumable electrode wire that contains flux within its core.
This flux serves multiple purposes, including shielding the molten weld pool from atmospheric contamination, stabilizing the arc, and providing additional alloying elements to enhance the weld quality.
The development of FCAW was driven by the need for higher productivity, faster welding speeds, and improved quality in various industries, such as shipbuilding, construction, and manufacturing.
The mid-1940s saw significant advancements in welding technology when tubular electrodes with flux were introduced.
This innovation marked a breakthrough in welding efficiency as it allowed for continuous wire feeding rather than manually replacing electrodes frequently during SMAW.
FCAW Variations
One notable distinction within FCAW is the differentiation between self-shielded (FCAW-S) and gas-shielded (FCAW-G) variations.
- Self-Shielded FCAW (FCAW-S): Self-shielded FCAW employs a tubular electrode wire filled with flux that generates its own shielding gas during welding—eliminating an external shielding gas cylinder or complex gas delivery system. This variation excels in outdoor applications where wind or drafts compromise shield gas effectiveness.
- Gas-Shielded FCAW (FCAW-G): Gas-shielded FCAW relies on an external shielding gas to protect the weld from atmospheric contamination.
Argon and carbon dioxide are typically used as shielding gas. This variation provides greater control over the welding process and allows for better penetration and higher deposition rates than self-shielded FCAW.
FCAW Equipment and Consumables Used
The equipment required for FCAW includes:
- A power source (welding machine)
- Welding gun or torch
- Wire feeder unit
- Electrode wire spool
- Contact tips
- Gas cylinder (for gas-shielded variation)
The consumables used in FCAW primarily focus on the electrode wire. It is important to select the appropriate wire type based on factors such as base metal composition, desired mechanical properties of the weld, application requirements, and environmental conditions.
The flux-cored electrode wires come in various classifications that show their suitability for specific applications. These classifications include factors such as tensile strength, impact toughness at low temperatures, all-position capability (e.g., vertical-up or overhead welding), and specific shielding gases, if applicable.
Denique
Flux-Cored Arc Welding (FCAW) emerged as an innovation that aimed to optimize productivity while addressing some limitations of Shielded Metal Arc Welding (SMAW). The development of this process revolutionized industries by allowing for continuous wire feeding with flux-filled electrodes.
FCAW offers two variations: self-shielded (FCAW-S) and gas-shielded (FCAW-G), each serving different purposes depending on environmental conditions and desired outcomes.
FCAW has proven to be a versatile welding process suitable for various applications in industries ranging from construction to manufacturing and beyond. Its efficient ability to provide high-quality welds has made it a popular choice among welders worldwide.
While the debate on which process is better continues, SMAW and FCAW have their strengths and weaknesses. Ultimately, the choice between the two depends on specific project requirements, environmental conditions, and personal preference.