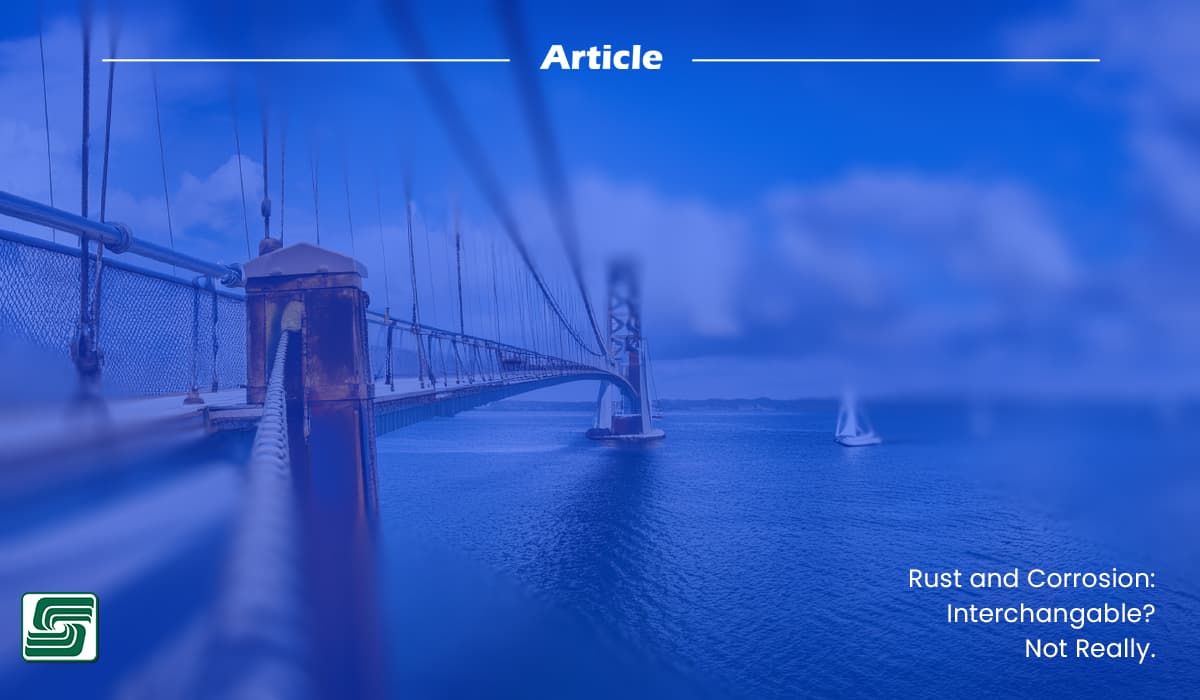
Understanding rust and corrosion is important for many people in as many fields. Rust and corrosion are terms people confuse because of their similarities. Despite the number of similarities, there are distinct differences between the two terms.
Let's look at rust and corrosion.
What is the Definition of Rust?
Rust refers to the reddish-brown flaky coating that forms on iron or iron alloys. This process occurs when iron reacts with oxygen and water, only affecting iron and its alloys.
What is the Chemical Composition of Rust?
Rust primarily comprises iron(III) oxide (Fe2O3) and sometimes includes hydrated iron(III) oxide-hydroxide (FeO(OH), Fe(OH)3). The chemical reaction involves iron, oxygen, and water, producing a weak and brittle substance.
What are Common Occurrences of Rust?
Rust commonly appears on items like iron gates, railings, and tools. Vehicles and machinery also experience rusting, especially in humid environments. Rust significantly weakens structures and objects.
What is the Definition of Corrosion?
Corrosion involves the gradual destruction of materials, usually metals, through chemical or electrochemical reactions to their environment.
Compared to rust, corrosion encompasses a broader range of materials. It affects metals like aluminum, copper, and steel.
What are the Chemical Processes Involved in Corrosion?
Corrosion occurs through oxidation-reduction reactions, which involve the transfer of electrons from the metal to another substance.
For example, iron corrosion involves iron losing electrons and reacting with oxygen and water, forming iron oxides.
What are Common Types of Corrosion?
Corrosion manifests in various forms:
- Uniform Corrosion: Affects the entire surface of the material evenly.
- Pitting Corrosion: Creates small, localized holes or pits in the material.
- Galvanic Corrosion: Occurs when two different metals come into electrical contact in the presence of an electrolyte.
- Crevice Corrosion: Develops in confined spaces where the electrolyte becomes trapped.
Understanding these types helps in identifying and preventing corrosion in different environments.
What Causes Rust and Corrosion?
Environmental Factors
- Moisture: Moisture plays a crucial role in both rust and corrosion. Water acts as an electrolyte, facilitating the chemical reactions that lead to material degradation. Iron corroded or rusted because of moisture exposure forms iron oxide. Corrosion impacts various metals by creating an environment where oxidation-reduction processes occur.
- Temperature: Temperature significantly affects corrosion rates. Higher temperatures accelerate chemical reactions, leading to faster corrosion. Cold environments slow down these processes but do not prevent them. Corrosion requires surface contact with environmental factors like moisture and temperature variations.
Material Susceptibility
- Metals Prone to Rust: Iron and its alloys, such as steel, are highly susceptible to rust. When exposed to oxygen and moisture, iron corroded or rusted forms a brittle, reddish-brown substance. Rust weakens the structural integrity of iron-based materials.
- Materials Prone to Corrosion: Corrosion includes rust but affects a broader range of materials. Metals like aluminum, copper, and zinc also experience corrosion. Each metal undergoes specific chemical reactions based on its properties. Corrosion results in material degradation that impacts its appearance and functionality. It occurs in various environments, from industrial settings to everyday household items.
Effects and Consequences
- Impact on Buildings and Infrastructure: Rust and corrosion significantly impact buildings and infrastructure. Rusting specifically refers to the oxidation of iron, which weakens structural components. Rust is an iron oxide that forms on steel beams and iron reinforcements. Over time, rust compromises the stability of bridges, buildings, and other structures. Corten Steel, known for its weather-resistant properties, offers some protection against rust. However, even Corten weathering steel requires regular maintenance. Rust protection in Las Vegas, for example, involves applying protective coatings to prevent rust formation. Corrosion affects a wider range of materials, including aluminum and copper. Corroded metal parts lose their strength and durability. This degradation poses safety risks and causes frequent inspections. Engineers must address both rust and corrosion to ensure the longevity of the infrastructure.
- Effects on Vehicles and Machinery: vehicles and machinery also suffer from rust and corrosion. Rusting specifically refers to the damage seen on iron and steel components. Rust weakens the frames and bodies of cars, trucks, and industrial machines. Rust is an iron oxide that forms when iron reacts with moisture and oxygen. This reaction leads to the deterioration of essential parts.
Corrosion impacts various metals used in machinery. Aluminum parts corrode when exposed to harsh environments.
Copper wiring and connectors degrade over time, affecting electrical systems. Regular maintenance and rust protection in Las Vegas help mitigate these issues.
Corten steel and Corten weathering steel offer some resistance but still require care.
Economic Impact
Cost of Repairs and Maintenance
The economic impact of rust and corrosion is substantial. Repairing rust-damaged structures and vehicles incurs high costs.
Rust protection in Las Vegas involves applying coatings and sealants, adding to maintenance expenses.
Rusting specifically refers to the damage to iron-based materials requiring specialized treatments.
Corrosion affects a broader range of materials, increasing repair costs. Industries spend billions annually on corrosion-related repairs.
Preventive measures, such as using corrosion-resistant materials, also contribute to expenses.
Because of their durability, Corten Steel and weathering steel offer some cost savings.
Preventive Measures and Their Costs
Preventive measures against rust and corrosion involve significant investments. Applying protective coatings and sealants helps prevent rust formation.
Rust protection in Las Vegas includes using advanced materials like Corten steel. These measures reduce long-term maintenance costs but require initial investments.
Corrosion prevention involves using alloys and special treatments. Industries employ cathodic protection and inhibitors to minimize corrosion.
These methods increase the lifespan of materials but come at a price. The cost of preventive measures must be weighed against the potential savings in repair and replacement expenses.
Prevention and Protection
Coatings and Sealants
- Types of Protective Coatings: Protective coatings are crucial in preventing rust. Various types of coatings exist to shield materials from environmental factors. Paints and primers create a barrier that prevents moisture contact with iron surfaces. Epoxy coatings offer excellent resistance to chemicals and physical wear. Galvanization involves applying a zinc coating to iron or steel, providing long-lasting protection against rust.
- Application Methods: Applying protective coatings requires careful preparation and technique. Surface preparation involves cleaning the material to remove dirt, grease, and existing rust. Sandblasting or wire brushing ensures a clean surface for optimal adhesion. Spraying, brushing, or dipping methods apply the coating evenly. Each method has specific advantages depending on the material and the environment. Regular maintenance and reapplication ensure continued protection against rust.
Environmental Control
- Reducing Moisture Exposure: Controlling moisture exposure significantly reduces the risk of rust. Dehumidifiers that maintain low humidity levels benefit indoor environments. Proper ventilation helps circulate air and prevent condensation. Outdoor structures require design considerations to minimize water accumulation. Sloping surfaces and drainage systems direct water away from vulnerable areas. Covering exposed metal parts with tarps or shelters provides additional protection.
- Temperature Regulation: Temperature regulation also plays a vital role in preventing rust. High temperatures accelerate chemical reactions, increasing the rate of rust formation. Insulating materials help maintain stable temperatures around metal structures. Heat-resistant coatings provide an extra layer of defense against temperature fluctuations. Monitoring and controlling temperature variations reduce the likelihood of rust development.
Detection and Monitoring
- Signs of Rust: Rust appears as a reddish-brown flaky coating on iron or steel surfaces. Small spots may develop into larger patches. Rust often forms in areas exposed to moisture and air. Common signs include discoloration, rough texture, and weakened material. Regular inspections help identify the early stages of rust.
- Signs of Corrosion: Corrosion affects various metals and manifests differently. Aluminum shows white or gray powdery deposits. Copper develops a green or blue patina. Steel exhibits pitting or surface irregularities. Corrosion weakens the material and changes its appearance. Frequent visual checks detect early signs of corrosion.
Technological Tools
- Sensors: Sensors are crucial in detecting rust and corrosion. Corrosion sensors measure environmental factors like humidity and temperature, providing real-time data to predict corrosion risk. Rust detection sensors identify changes in electrical resistance on metal surfaces. Using sensors helps in early identification and preventive measures.
- Advanced Imaging Techniques: Advanced imaging techniques offer a detailed analysis of rust and corrosion. Ultrasonic testing detects internal flaws and thickness reduction. X-ray imaging reveals hidden corrosion beneath coatings. Infrared thermography identifies temperature variations, showing corrosion activity. These techniques provide comprehensive insights into material health. Regular use of imaging tools ensures timely intervention and maintenance.
Historical Examples of Rust Damage
Famous Bridges and Structures
The Brooklyn Bridge in New York City has experienced significant rust damage. The iron cables and steel beams have eroded over time because of exposure to moisture and air.
Engineers have conducted many repairs to maintain the bridge's structural integrity.
The Sydney Harbour Bridge in Australia also suffers from rust. The steel arch and pylons are constantly exposed to the marine environment.
Regular maintenance and protective coatings help mitigate rust formation.
Lessons Learned
Historical examples of rust damage highlight the importance of regular inspections. Engineers must identify early signs of rust to prevent structural failures.
Protective coatings and sealants are crucial in extending the lifespan of metal structures.
Modern Examples of Corrosion Issues
Industrial Applications
Oil rigs in the Gulf of Mexico face severe corrosion issues. Saltwater exposure accelerates the corrosion of metal components, so companies invest heavily in corrosion-resistant materials and protective coatings.
Aircraft manufacturing industries also deal with corrosion. Aluminum parts corrode when exposed to harsh environments.
Regular maintenance and the use of advanced materials help reduce corrosion risks.
Key Differences Between Rust and Corrosion
- Chemical Differences: Corrosion vs. Rust involves different chemical processes. Rust forms when iron reacts with oxygen and water, creating iron oxide. Corrosion includes various chemical reactions that degrade metals. Each metal undergoes specific oxidation-reduction reactions. The difference between rust and corrosion lies in the materials affected. Rust impacts only iron and its alloys. Corrosion affects a broader range of metals like aluminum and copper.
- Visual Differences: Rust vs corrosion also shows visual differences. Rust appears as a reddish-brown flaky coating on iron surfaces. Corrosion manifests in different ways depending on the metal. Aluminum shows white or gray powdery deposits. Copper develops a green or blue patina. Steel exhibits pitting or surface irregularities. These visual cues help identify the type of degradation occurring.
Similarities and Overlapping Areas
- Common Prevention Methods: There are common prevention methods for rust and corrosion. Protective coatings and sealants prevent both rust and corrosion. Paints, primers, and epoxy coatings create barriers against moisture. Galvanization applies a zinc coating to iron or steel. Environmental control measures reduce moisture exposure. Dehumidifiers, proper ventilation, and drainage systems help. Regular maintenance ensures continued protection.
- Shared Environmental Factors: Corrosion vs. Rust also shares environmental factors. Moisture and temperature influence both processes. Water acts as an electrolyte, facilitating chemical reactions. Higher temperatures accelerate these reactions. Cold environments slow down the processes but do not stop them. Both rust and corrosion require surface contact with environmental factors. Understanding these factors aids in prevention and protection.
Everyday Applications
- Household Items: Household items often suffer from rust and corrosion. Iron-based tools like hammers and wrenches rust when exposed to moisture, and kitchen appliances with metal parts also suffer from corrosion. Stainless steel utensils resist rust but corrode under certain conditions. Regular cleaning and drying of metal items help prevent rust formation, and applying protective coatings extends the lifespan of these items.
- Consumer Electronics: Consumer electronics contain various metals prone to corrosion. Copper wires and connectors corrode, affecting device performance. Aluminum casings on laptops and smartphones show signs of corrosion. Manufacturers use protective coatings to shield metal parts. Regular maintenance and proper storage reduce corrosion risks. Keeping electronics in dry environments helps prevent damage.
Industrial Applications
Manufacturing Processes
Manufacturing processes involve metals that rust or corrode. Factories use ductile iron products for their strength and durability.
Ductile iron pipes transport fluids in industrial settings. Corrosion affects the efficiency of these systems.
Regular inspections and maintenance ensure optimal performance. Protective coatings and environmental controls reduce corrosion risks.
Ductile iron pipelines require specific measures to prevent rust. Epoxy coatings protect the internal surfaces, and galvanization adds a zinc layer to the external surface.
Proper installation and regular monitoring maintain pipeline integrity. Using advanced materials like ductile iron enhances durability.
Construction Practices
Construction practices must address rust and corrosion. Buildings and infrastructure use ductile iron for structural components.
Rust weakens steel beams and iron reinforcements. Corrosion affects aluminum and copper parts in construction.
Engineers apply protective coatings to metal surfaces. Regular inspections identify early signs of rust and corrosion.
- Ductile iron pipe systems in construction require special attention.
- Cutting ductile iron pipe involves precise techniques to avoid damage.
- Measuring ductile iron pipe ensures accurate installation.
- Proper handling and storage prevent rust formation.
Using ductile iron products enhances the longevity of construction projects.
In Sum
Understanding these differences helps identify and prevent material degradation.
Preventive measures protect everyday items and industrial equipment, and regular inspections and maintenance ensure long-term durability.