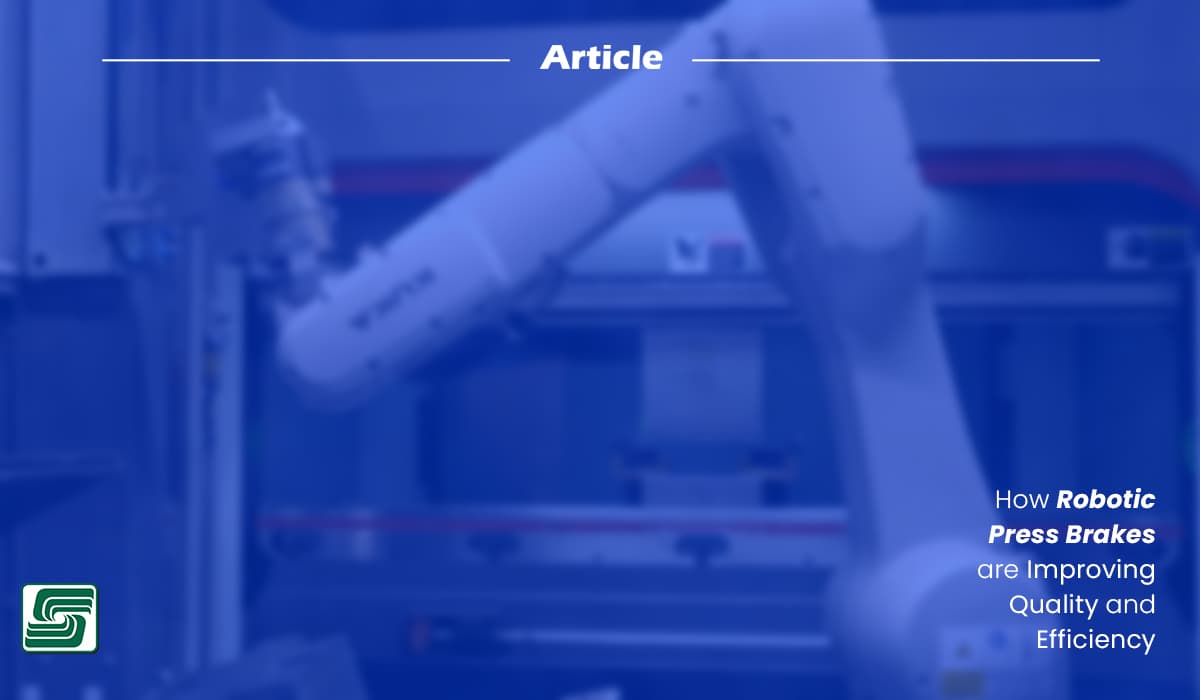
Ensuring Robotic press brake quality control in modern manufacturing is paramount for producing flawless metal components. The precision and accuracy of robotic press brakes have revolutionized the industry, guaranteeing consistent quality standards.
Robotic Press Brake Quality Control Innovations
Automated inspection systems are crucial in enhancing the quality control process within manufacturing facilities. By implementing automated inspection systems, manufacturers ensure precise and accurate evaluations of metal components. This innovative approach offers many benefits to the production line:
- Improved Accuracy: Automated inspection systems use advanced technology to detect even the slightest imperfections in metal parts, ensuring that only flawless components proceed further in the manufacturing process.
- Enhanced Efficiency: Integrating automated inspection systems streamlines the quality control process, reducing manual labor and minimizing the risk of human error.
- Cost-Effective Solutions: By automating the inspection phase, manufacturers significantly reduce operational costs associated with manual quality control procedures.
Implementation of automated inspection in manufacturing environments involves a systematic approach to guarantee optimal results:
- Integration Planning: Manufacturers must carefully plan and integrate automated inspection systems into their existing production lines to maximize efficiency and accuracy.
- Training Programs: Conducting comprehensive training programs for staff members is essential to ensure seamless operation and maintenance of automated inspection equipment.
Real-time monitoring is another critical aspect of quality control that significantly impacts manufacturing processes. Leveraging real-time data provides manufacturers with immediate insights into production operations, enabling them to make informed decisions promptly:
- Instant Feedback Loop: Real-time monitoring systems offer an instant feedback loop, allowing operators to address issues as they arise and prevent potential defects in metal components.
- Continuous Improvement: By continuously monitoring production metrics in real time, manufacturers identify improvement areas and promptly implement corrective measures.
Examples of Real-Time Monitoring Systems include:
- IoT Sensors: These sensors collect real-time data on various aspects of press brake operations, such as machine performance and energy consumption.
- Machine Vision Technology: By using cameras and image processing algorithms, machine vision technology enables real-time bending process monitoring for enhanced precision.
Smart Scheduling Software
Smart scheduling software is a pivotal tool in modern manufacturing. It enhances operational efficiency and ensures optimal resource utilization. By implementing Smart Scheduling Software, manufacturers streamline production processes, reduce idle time, and improve overall output consistency.
Enhancing Efficiency
Reducing Idle Time
Smart scheduling software allocates tasks efficiently, ensuring that press brake machines are operational throughout the production cycle to minimize downtime and maximize productivity. By optimizing the sequencing of operations, manufacturers eliminate unnecessary delays and maintain a continuous workflow:
- Prioritizing Tasks: Smart scheduling software categorizes tasks based on urgency and complexity, allowing operators to focus on critical activities first.
- Minimizing Changeovers: The software reduces changeover times between production runs by grouping similar tasks.
- Maximizing Machine Utilization: Through intelligent scheduling algorithms, manufacturers use press brake machines to their full capacity, minimizing idle time.
Improving Setup Times
Efficient setup procedures are essential for reducing lead times and increasing production efficiency. Smart scheduling software facilitates quick machine setups by providing operators with detailed instructions and automating certain preparatory tasks:
- Automated Tooling Changes: The software coordinates tooling changes with minimal manual intervention, speeding up the setup process.
- Preemptive Maintenance Alerts: Smart scheduling software monitors equipment status in real-time and alerts operators to potential issues before they impact setup times.
- Standardized Setup Protocols: Establishing standardized setup protocols ensures consistency across different production runs, reducing variability in setup times.
Maintaining Quality Standards
Maintaining consistent quality standards is paramount in manufacturing to ensure customer satisfaction and uphold brand reputation. Smart scheduling software plays a crucial role in maintaining quality standards by:
- Monitoring Production Metrics: The software tracks key performance indicators (KPIs) related to product quality, alerting operators to deviations from set benchmarks.
- Implementing Quality Checks: Automated quality checks at various stages of production help identify defects early on, preventing substandard products from reaching customers.
- Continuous Improvement Initiatives: Manufacturers implement corrective actions to continuously enhance product quality by analyzing historical data and identifying trends.
High Positioning Accuracies
Integrating modern CNC press brakes revolutionizes the landscape of metal component fabrication, offering manufacturers a pathway to unparalleled precision and efficiency. These advanced machines use state-of-the-art technology to ensure that each bend is executed meticulously, meeting the industry's most stringent quality requirements.
Achieving Precision in Bending
Manufacturers rely on the sophisticated capabilities of modern CNC press brakes to achieve precision in bending operations. These machines execute complex bending sequences with the utmost accuracy through precise control systems and advanced programming interfaces, resulting in flawless metal components that adhere to strict dimensional tolerances.
Consistent Inspection
Consistency in inspection processes is vital for ensuring the accuracy and reliability of metal components produced through press brake operations. By implementing rigorous quality control measures, manufacturers uphold their commitment to delivering flawless products that meet or exceed customer expectations.
Ensuring Accuracy
Ensuring accuracy in press brake operations requires a systematic approach that encompasses meticulous inspection protocols and adherence to predefined quality standards. By leveraging automated inspection systems and real-time monitoring technologies, manufacturers detect deviations from specifications promptly, enabling swift corrective actions.
Techniques and Tools
The arsenal of techniques and tools for maintaining consistent inspection standards includes next-gen technologies designed to enhance the accuracy and efficiency of quality control processes. From non-destructive testing methods to advanced metrology equipment, manufacturers have access to a diverse range of tools that empower them to validate the precision and integrity of their metal components.
Emerging Technologies
Artificial Intelligence (AI) and Machine Learning are shaping the future of quality control in manufacturing. These technologies empower machines to learn from data, adapt to new information, and decide with minimal human intervention. Integrating AI algorithms into quality control processes revolutionizes how manufacturers detect defects, predict maintenance needs, and optimize production efficiency.
Predictive Maintenance
Predictive Maintenance is a game-changer in ensuring uninterrupted manufacturing operations by forecasting equipment failures before they occur. By leveraging data analytics and machine learning models, manufacturers expect maintenance requirements based on equipment performance trends. This proactive approach minimizes downtime, reduces repair costs, and enhances operational reliability.
Long-Term Benefits
Industry experts foresee a myriad of long-term benefits resulting from the adoption of advanced quality control technologies. Manufacturers embracing AI-driven quality control systems expect:
- Enhanced Productivity: AI-powered systems streamline production processes, increasing output rates and operational efficiency.
- Cost Savings: Predictive maintenance strategies reduce unplanned downtime and extend equipment lifespan, resulting in significant cost savings for manufacturers.
- Quality Improvements: By detecting defects early on, AI-enhanced quality control systems ensure that only high-quality products reach customers, enhancing brand reputation.
Potential Challenges
While the future of quality control holds immense promise, certain challenges must be addressed to maximize the benefits of emerging technologies:
- Data Security Concerns: The reliance on interconnected systems raises cybersecurity risks that could compromise sensitive manufacturing data.
- Skill Gaps: Implementing AI and predictive maintenance solutions requires specialized skills that may not exist within prevailing workforce structures.
- Integration Complexity: Integrating new technologies into established manufacturing processes poses challenges related to system compatibility and operational disruptions.
In Sum
Highlighting the transformative innovations in robotic press brake quality control, manufacturers witness a new era of precision and efficiency.
Emphasizing the vital role of continuous improvement in quality control processes ensures sustained excellence in metal component fabrication.
Embracing emerging technologies like AI and machine learning promises a future where predictive maintenance drives operational reliability and cost savings for manufacturers.