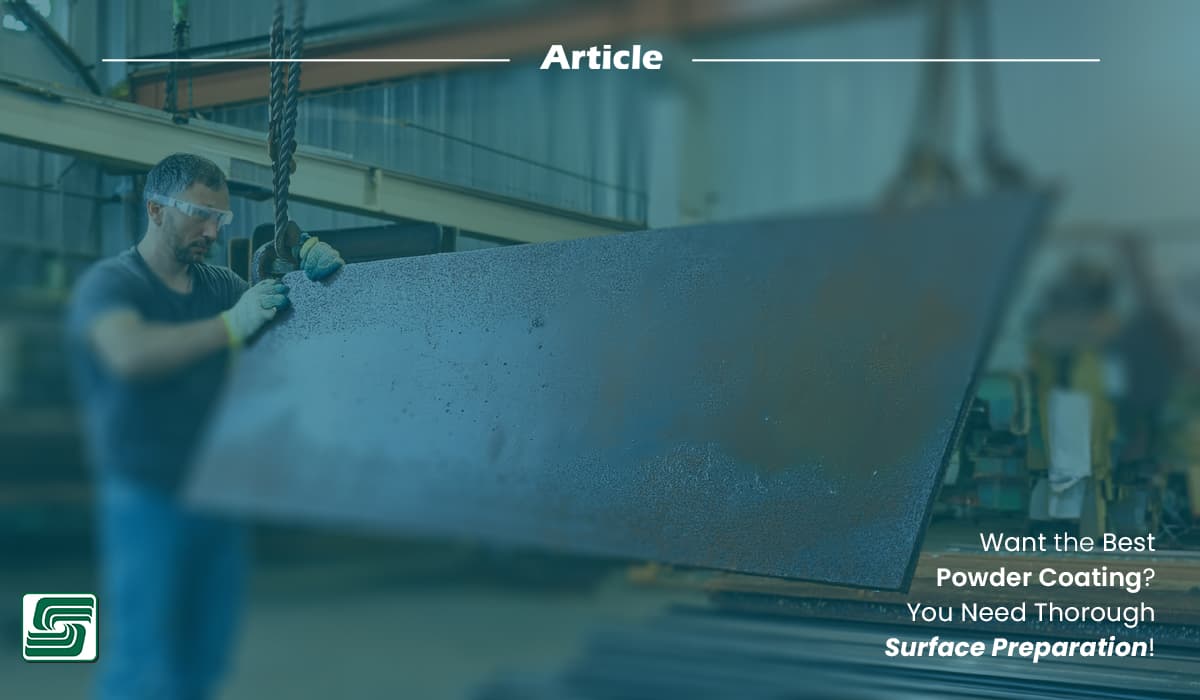
Powder coating offers a durable and aesthetically pleasing finish for various industries. Industries such as automotive, aerospace, and construction rely on powder coating for its resilience and versatility. Surface preparation plays a crucial role in powder coating. Proper surface preparation ensures optimal adhesion and longevity of the coating.
Thorough surface preparation removes contaminants and enhances the bonding process. The importance of meticulous surface preparation cannot be overstated. Achieving the best powder coating results requires attention to detail in preparing surfaces.
Understanding Powder Coating
Powder coating is an excellent method for surface finishing. This process involves applying a dry powder to a metal surface, which then undergoes curing under heat to form a hard, protective layer.
The result is a finish that surpasses conventional paint in terms of toughness and durability.
Manufacturers favor powder coating because of its efficiency and reliability. The coating provides a long-lasting and easy-to-maintain finish, making it an ideal choice for various applications. Quality control tests ensure that each coating meets the highest standards, guaranteeing a consistent and superior finish.
Benefit |
Description |
Durability |
Provides a hard, protective layer surpassing conventional paint in terms of toughness and durability |
Aesthetic Appeal |
Offers an attractive finish enhancing the appearance of surfaces |
Environmental Advantages |
Eliminates the need for solvents, reducing VOC emissions, and making the process more environmentally friendly |
Cost-Effectiveness |
Minimizes waste, reduces application time, and requires less frequent maintenance and replacement |
Efficiency |
Provides a long-lasting and easy-to-maintain finish, making it an ideal choice for various applications |
Versatility |
Widely used across many industries, including automotive, aerospace, and construction |
The benefits of powder coating extend beyond mere aesthetics. The coating offers significant environmental advantages by eliminating the need for solvents, reducing volatile organic compound (VOC) emissions, and making the process more environmentally friendly than traditional liquid paints.
The coating's efficiency translates into cost savings, as it minimizes waste and reduces the time required for application. The robust nature of the coating also means less frequent maintenance and replacement, further enhancing its cost-effectiveness.
Common Applications
Thanks to its versatility and resilience, powder coating is widely used across many industries.
Among the many industries that rely on powder coating include:
- Automotive
- Aerospace
- Construction
- Furniture
The automotive industry heavily relies on this coating to provide a durable and attractive finish. Components such as wheels, bumpers, and chassis benefit from the coating's protective qualities, ensuring longevity and resistance to wear and tear.
Powder coating is crucial in protecting aircraft components from harsh environmental conditions in the aerospace sector.
The coating's ability to withstand extreme temperatures and resist corrosion makes it an invaluable asset to maintain the integrity of aerospace parts.
The construction industry also benefits significantly from powder coating.
Architectural elements like window frames, railings, and structural steel receive enhanced protection against the elements, ensuring they maintain their appearance and functionality.
The coating's durability and aesthetic appeal make it a preferred choice for interior and exterior applications.
Overall, powder coating stands as a testament to innovation in surface finishing. Its durability, environmental benefits, and cost-effectiveness make it an indispensable tool in various sectors.
The Importance of Surface Preparation
Surface preparation stands as a pivotal step in the powder coating process. The surface's quality directly influences the coating's adhesion and longevity. A well-prepared surface ensures that the coating bonds effectively, providing a durable finish.
Importance of Surface Preparation
- Removes contaminants and enhances the bonding process
- Ensures optimal adhesion and longevity of the coating
- Meticulous surface preparation is crucial for receiving the best results
Enhancing Adhesion
Adhesion plays a critical role in the success of powder coating. Surface preparation enhances adhesion by removing contaminants such as dust, oils, and oxidation products, which interfere with bonding.
Scientific research findings highlight that chemical composition and surface roughness significantly impact bonding strength. Techniques like chemical cleaning and degreasing prepare the surface for optimal adhesion. Surface roughening methods create a desirable texture, improving mechanical bonding.
A properly prepared surface ensures the coating adheres strongly, resulting in a long-lasting finish.
Preventing Coating Failures
Surface preparation prevents coating failures by addressing potential issues before they arise. Contaminants like dirt and grease compromise the adhesion of new coatings.
Thorough preparation removes these obstacles, reducing the risk of premature failure.
The Elcometer Guide to Surface Preparation emphasizes the importance of creating a surface profile. A well-prepared surface profile ensures proper adhesion, enhancing the coating's performance. Surface preparation also involves assessing environmental factors that may affect the coating.
By considering these factors, the process minimizes the chances of coating failures, ensuring a successful application.
Factors Affecting Surface Preparation
Surface preparation stands as a critical step in achieving optimal powder coating results.
Various factors influence the effectiveness of this process. Understanding these factors ensures that the surface reaches an acceptable level of preparation for coating application.
Material Type
Material type significantly impacts the surface preparation process. Different materials require specific preparation methods to achieve the desired adhesion—metals such as aluminum and steel demand distinct approaches because of their unique properties.
Aluminum surfaces often undergo chemical treatments to remove oxidation and enhance bonding. Steel surfaces benefit from abrasive blasting to create a suitable texture for coating adhesion. Each material presents unique challenges that cause tailored preparation techniques.
Surface Condition
Surface condition plays a pivotal role in determining the success of the coating process.
A clean and smooth surface ensures effective bonding of the coating. Contaminants like oils, dirt, and rust impede adhesion. Degreasing and chemical cleaning effectively remove these contaminants.
Mechanical abrading creates a desirable texture that enhances mechanical bonding. The surface's condition directly influences the coating's longevity and durability. Ensuring an acceptable level of surface preparation minimizes the risk of coating failures.
Proper assessment and treatment of the surface condition lead to superior coating performance.
Assessing the Surface Condition
Effective powder coating begins by assessing the surface condition. The surface's quality directly impacts the coating's durability and integrity.
A thorough assessment identifies any potential issues that may affect the coating process.
Visual Inspection
Visual inspection is the first step in evaluating the surface. Inspectors look for visible surface contamination, such as rust, dirt, or old coatings.
These contaminants hamper adhesion and lead to coating failures. A clean and smooth surface ensures better bonding of the powder coating. Inspectors use various tools, like magnifying glasses, to detect imperfections.
Identifying visible surface defects early in the process prevents future problems with oxidation and corrosion.
Testing for Contaminants
Testing for contaminants involves more than just visual checks. Surface contamination includes both visible and non-visible surface contaminants. Non-visible contaminants like oils or surface salt can compromise the coating's performance.
Specialized tests measure the contamination level to ensure the surface meets cleanliness standards. Techniques like solvent rub tests help identify oils and greases. Salt spray tests detect corrosive salts on the surface. Removing these contaminants is crucial for achieving a high-quality finish.
Proper testing ensures the surface is ready for coating, enhancing durability and reliability.
Preparing the Surface for Powder Coating
Effective surface preparation is essential for achieving optimal results in powder coating.
Surface preparation ensures the surface is clean, smooth, and ready for coating or surface treatment. Two primary methods used in this process are cleaning techniques and abrasive blasting.
Cleaning Techniques
Cleaning techniques form the foundation of surface preparation.
These techniques remove contaminants such as oils, grease, and dirt from the surface. Various methods exist to achieve this cleanliness. Solvent cleaning involves using chemical solvents to dissolve and remove oils and greases.
This method ensures that no residue remains on the surface. Alkaline cleaning uses alkaline solutions to break down organic materials. This technique effectively removes stubborn contaminants.
Each cleaning method targets specific contaminants, ensuring a thorough and tailored approach to surface preparation.
Abrasive Blasting
Abrasive blasting plays a crucial role in preparing surfaces for powder coating. This process propels abrasive media against the surface to remove rust, paint, and other residues.
The blasting creates a desirable texture that enhances the adhesion of the coating. Steel grit and aluminum oxide abrasives are commonly used in blasting. These materials efficiently clean surfaces and create a surface profile.
However, mechanical abrasives can leave dust behind, which may contaminate the surface. Proper cleaning after blasting ensures that the surface remains free of contaminants.
Abrasive blasting is a cost-effective solution for achieving a clean and well-prepared surface.
Technique |
Description |
Solvent Cleaning |
Uses chemical solvents to dissolve and remove oils and greases |
Alkaline Cleaning |
Uses alkaline solutions to break down organic materials and remove stubborn contaminants |
Abrasive Blasting |
Propels abrasive media against the surface to remove dust, paint, and other residues |
Chemical Treatments |
Applies chemical solutions to clean and etch the substrate—creating a micro-roughened surface |
Mechanical Methods |
Uses physical force to clean and roughen the substrate, including abrasive blasting and mechanical abrading |
Surface Preparation
Thorough cleaning techniques and abrasive blasting ensure the surface is ready for powder coating. A well-prepared surface enhances the coating's adhesion and longevity, leading to superior performance and durability.
Processes Involved in Surface Preparation
Surface preparation involves a series of processes that ensure the substrate is ready for powder coating. These processes are crucial in enhancing the coating's adhesion and longevity.
Proper surface preparation is essential for achieving a successful powder coating project.
Chemical Treatments
Chemical treatments stand as a vital component in surface preparation. These treatments involve the application of chemical solutions to clean and etch the substrate. Chemical cleaning removes contaminants such as oils, grease, and oxidation.
This process ensures a clean surface, which is essential for optimal adhesion. Chemical treatments often include etching, which creates a micro-roughened surface. This texture enhances the mechanical bonding of the coating.
Using chemical treatments provides a highly adhering oxide layer, which improves the durability of the final coating.
Chemical surface preparation is an important anti-corrosion protection step. It affects the quality of the technological operations to be undertaken and the value of the final coating.
Mechanical Methods
Mechanical methods offer another approach to surface preparation. These methods involve using physical force to clean and roughen the substrate. Abrasive blasting is a common mechanical method. This process propels abrasive media against the surface to remove rust, paint, and other residues.
Abrasive blasting creates a desirable texture that enhances coating adhesion.
Steel grit and aluminum oxide are popular abrasives used in this process. Mechanical abrading also falls under mechanical methods.
This technique involves the use of tools to physically roughen the surface. Mechanical methods significantly affect the lifetime of the coating.
Proper and thorough surface preparation is crucial for successfully applying a coating or surface treatment.
The combination of chemical and mechanical methods ensures a well-prepared surface. Each method targets specific contaminants and surface conditions.
A comprehensive approach to surface preparation enhances the adhesion and durability of the powder coating. Proper surface preparation is critical to achieving a successful powder coating project. It ensures the finished product is aesthetically pleasing, durable, and long-lasting.
Inspection After Surface Preparation
Inspection after surface preparation ensures the substrate meets all necessary criteria for powder coating.
The inspection process involves evaluating the surface profile and cleanliness. Proper inspection guarantees that the coating adheres effectively and lasts longer.
Surface Profile Measurement
Surface Profile Measurement plays a crucial role in determining the success of powder coating.
The profile refers to the texture and roughness of the substrate after preparation. Creating a surface profile enhances the coating's mechanical bonding.
Technicians use specialized equipment to calculate the profile. Instruments like profilometers provide precise readings of the surface's peaks and valleys.
The profile must meet specific standards to ensure optimal adhesion. A well-defined profile contributes to the coating's durability and performance.
Benefit |
Description |
Durability |
Provides a hard, protective layer surpassing conventional paint in terms of toughness and durability |
Surface Profile Measurement |
Offers an attractive finish enhancing the appearance of surfaces |
Surface Profile Standards |
Eliminates the need for solvents, reducing VOC emissions, and making the process more environmentally friendly |
Cleanliness Standards |
Minimizes waste, reduces application time, and requires less frequent maintenance and replacement |
Visual Assessment |
Provides a long-lasting and easy-to-maintain finish, making it an ideal choice for various applications |
Testing Methods |
Uses specialized tests to detect non-visible contaminants and impurities |
Cleanliness Standards
Surface cleanliness directly affects the quality of the powder coating. Contaminants on the surface compromise the coating's adhesion and longevity.
Cleanliness standards define the acceptable level of contaminants on the substrate. Technicians perform thorough inspections to ensure the surface meets these standards. Visual assessments and testing methods help identify any remaining impurities.
Adhering to cleanliness standards ensures a successful coating application. The inspection confirms the surface is free from oils, grease, and other residues.
Meeting cleanliness criteria enhances the overall quality of the powder coating.
Ensuring Quality in Powder Coating
Quality in powder coating relies on several important parameters. These parameters ensure the coating's performance and longevity.
Proper quality control procedures and troubleshooting techniques are important in maintaining high standards.
Quality Control Procedures
Quality control procedures are the backbone of successful powder coating applications.
Technicians perform regular inspections to verify the coating's thickness and uniformity, helping identify deviations from the desired specifications. Instruments like thickness gauges provide accurate measurements of the coating layer.
Consistent thickness ensures even coverage and optimal protection.
Adhesion tests are another critical component of quality control. They assess the bonding strength between the coating and the substrate.
Technicians use methods, such as cross-hatch testing, to evaluate adhesion. Strong adhesion prevents peeling and extends the coating's lifespan.
Environmental conditions also impact the quality of powder coating. Monitoring temperature and humidity levels during the application is crucial.
Proper environmental control minimizes defects and enhances the coating's appearance. Quality control procedures ensure that all important parameters meet industry standards.
Troubleshooting Common Issues
Troubleshooting common issues in powder coating requires a systematic approach. Surface defects often arise from improper surface preparation. Identifying and addressing these defects early prevents coating failures.
Technicians examine the surface for contaminants or irregularities that may affect adhesion.
Coating defects, such as orange peel or pinholes, occur during application. Adjusting spray gun settings helps achieve a smooth finish.
Proper equipment calibration ensures consistent results. Technicians also check for clogs or blockages in the spray system.
Curing problems may lead to incomplete or uneven coatings. Verifying oven temperatures and curing times resolves these issues.
Proper curing ensures the coating reaches its full hardness and durability. Troubleshooting involves analyzing each step of the process to identify potential problems.
Ensuring quality in powder coating involves attention to detail and adherence to important parameters. Quality control procedures and effective troubleshooting contribute to a successful coating application.
These practices enhance the coating's performance and longevity, providing a reliable and durable finish.
In Sum
Thorough surface preparation is essential in achieving the best results in powder coating. Proper preparation ensures optimal adhesion and prevents defects, leading to a durable and aesthetically pleasing finish.
Clean and rust-free surfaces form the foundation of successful powder coating projects. Adhering to surface preparation standards enhances the longevity and effectiveness of the coating. Removing contaminants and debris optimizes substrate surfaces for stronger adhesive bonding.
The meticulous attention to surface preparation directly influences the quality and performance of powder coating applications.