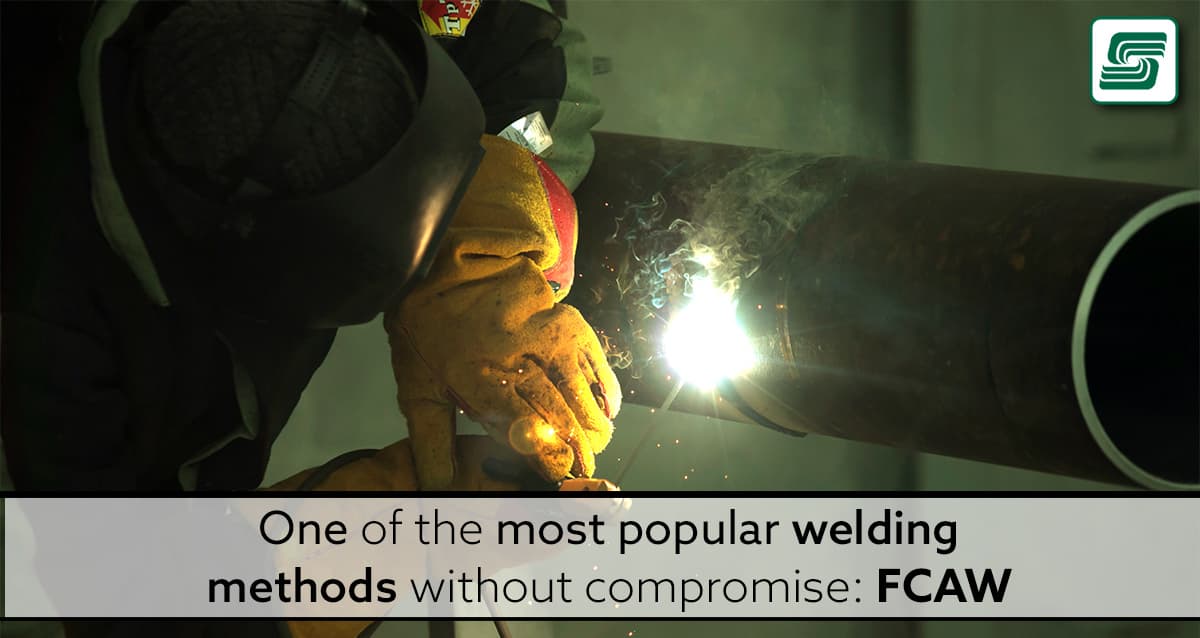
Flux-cored arc welding (FCAW) is a semi-automatic or fully automatic arc welding technique in which a continuously fed consumable electrode contains a flux using a continual-voltage or constant-current welding power supply.
FCAW welding uses externally existing shielding gas and safeguards the gas from atmospheric gases, which protects it.
Development
FCAW, developed from shielded metal arc welding (SMAW), is among the most flexible and widely used arc welding methods. SMAW uses an electrical arc burning between a sheathed rod electrode and the base metal. The sheathed melting electrode forms a shielding gas protecting the smelt, meaning SMAW doesn't need an external source of shielding gases.
SMAW became popular because the equipment requirements are simple; it's portable, easy to use outdoors, and works well with various metals and thicknesses. However, there are significant disadvantages to using SMAW on an industrial scale, limiting its growth, including
- Not as productive as continuous wire processes
- Likely to be more costly to deposit a quantity of metal
- Frequent stops for changing the electrode
- Relatively high metal wastage (electrode stubs)
- Current limits are lower than for continuous or automatic processes (reduces deposition rate)
The stick electrodes used in SMAW aren't necessary for the FCAW method. This reason, combined with the disadvantages listed above, is why FCAW developed into SMAW's preferred alternative.
FCAW Types
There are two main types of FCAW:
No Shielding Gas
The flux-cored electrode used in FCAW generates its own protective gas to shield the weld. Thus FCAW can often be performed with no additional shielding gas without a compromise in weld quality. This eliminates the cost and setup associated with a separate shielding gas system. FCAW without shielding gas is effective for thinner, flat-position metals. The lack of a shielding gas also allows this process to be effective in outdoor or windy environments that dissipate a shielding gas.
For welding on thicker, out-of-position metals, especially structural steel welding, FCAW may be used with shielding gas for greater quality and consistency. This is often known as "duel shield" welding since both the shielding gas and the flux is used to shield the weld. This process is better used in a controlled environment such as a fabrication shop where the wind doesn't interfere with the shielding gas. The shielding gas is commonly carbon dioxide (CO2) or an argon-carbon dioxide mixture such as C-25, which contains 75% argon and 25% carbon dioxide.
The Flux in Flux-Core
An essential piece of the FCAW process is weld flux. Weld flux is a chemical purifying agent preventing the weld from combining with the surrounding materials present during welding.
The primary function of weld flux is to oxidize the base and filler materials during the welding process. Weld flux is a substance that is almost inert at average room temperature but can be intensely reduced when exposed to higher temperatures to prevent metal oxide formation. Flux dissolves the metal surface oxides that facilitate the molten metal wetting, acts as a barrier to oxygen, and minimizes oxidation. Fluxes are used to generate a surface for wetting the solder. However, flux can contain bromine and chlorine and remain corrosive after the soldering process, subsequently causing corrosion to the surface throughout production or operation. Therefore, testing and cleaning techniques have been developed to ensure that the surface remains noncorrosive after the process. The most common tests are designed to identify the flux residues' corrosive properties under extreme conditions. A solder pellet is melted during testing when it comes in contact with the flux over a metal sheet. Afterward, the solder is exposed to various humidity levels. The corrosion generated is then evaluated visually.
Flux also directly affects the strength of the weld. The less oxygen present in the weld, the stronger the weld.
A quick summary of flux:
The selection of flux material depends on the metals used. In addition to preventing the formation of oxides, weld flux also:
- Creates a protective slag over the molten metal
- Removes impurities from the motel metal
- Reduces splatter
- It prevents hardening by slowing down cooling time, etc.
Fluxes find applications in Shielded Metal Arc Welding (SMAW), Flux-Cored Arc Welding (FCAW), and Submerged Arc Welding (SAW).
FCAW Process
The FCAW doesn't use external shielding gases but relies on the flux core electrode's protection itself. This electrode gives gaseous protection and even creates a slag surrounding the weld's molten metal, supporting it.
The filler wire core comprises fluxing agents creating slag and materials containing shielding gases as burnt by the welding arc heat. The shielding flux allows for welding outside, even in high winds environments, without additional shielding gas.
Weldnotes.com shares a five-minute video describing FCAW.
FCAW Industrial Uses
Flux-co
re welding works well with thicker joints because of its deeper penetration. The welder can weld in all directions while holding the torch at different angles. These two facts and not needing high skill levels make FCAW well-suited for shipbuilding, general repairs, underwater welding, pipeline welding, and other manufacturing processes.
The Tulsa Welding School explains another benefit of using FCAW for industrial purposes:
The deposit rate of filler material for flux-core welding is the highest of any other method. While a MIG welder can deposit up to 8 pounds of wire per hour, a flux-core welder can deliver up to 25 pounds per hour. For big projects with tight deadlines, flux-core welding can be a saving grace, particularly in industrial manufacture and repair settings that process large orders.
FCAW Advantages
There are properties unique to FCAW, giving it some advantages over other welding methods. The extra tank containing shielding gas does not need to increase mobility. However, it would be best to weigh mobility over smoke: FCAW creates more smoke than MIG welding, requiring a highly vented working area or simply welding outside. Since the wire shields the flux from environmental conditions, the wind doesn't negatively affect the weld quality.
Other advantages include:
- A high deposition rate, which is the speed that the filler metal is applied
- It can be used in all positions with the right filler metal
- Suitable for outdoor welding or shop welding
- Relatively easy to learn compared to other welding processes
- More forgiving of rust, scale, and other base metal contaminants
- The welding arc has good visibility
- Provides excellent weld penetration
- Allows for high welding productivity
FCAW Disadvantages
Like everything with advantages, there are disadvantages, too:
- A high level of noxious fumes must be ventilated
- Higher electrode wire cost compared to solid electrode wires
- More costly equipment than many other welding processes
- Less portable equipment than SMAW or GTAW
- The slag covering the weld must be removed
- Mechanical problems can lead to melted contact tips, irregular wire feed, or porosity of the weld
- Not well-suited to all metal types
In Sum
Welding experts consider FCAW the most flexible of all arc welding processes, offering various materials and welding configurations. The lowest quantities of slag, the most consistent weld bead, and the least amount of spatter are common with FCAW.
- FCAW is flexible in fabrication shop settings and industrial manufacturing, making it well-suited to several applications. The ability to work outdoors while welding makes it especially well-suited for projects in windy areas.
- Flux-core arc welding is easier to use than SMAW because it doesn't require an external gas.
- Flux-cored welding (FCAW) combines the benefits of shielded metal arc welding (SMAW) and submerged arc welding (SAW).
- FCAW has a continuous fluxing longitudinal electrode and a core rod of filler material. The welding process continues until it completely consumes the electrode. The welder may perform this task as often as necessary to maintain a quality weld.