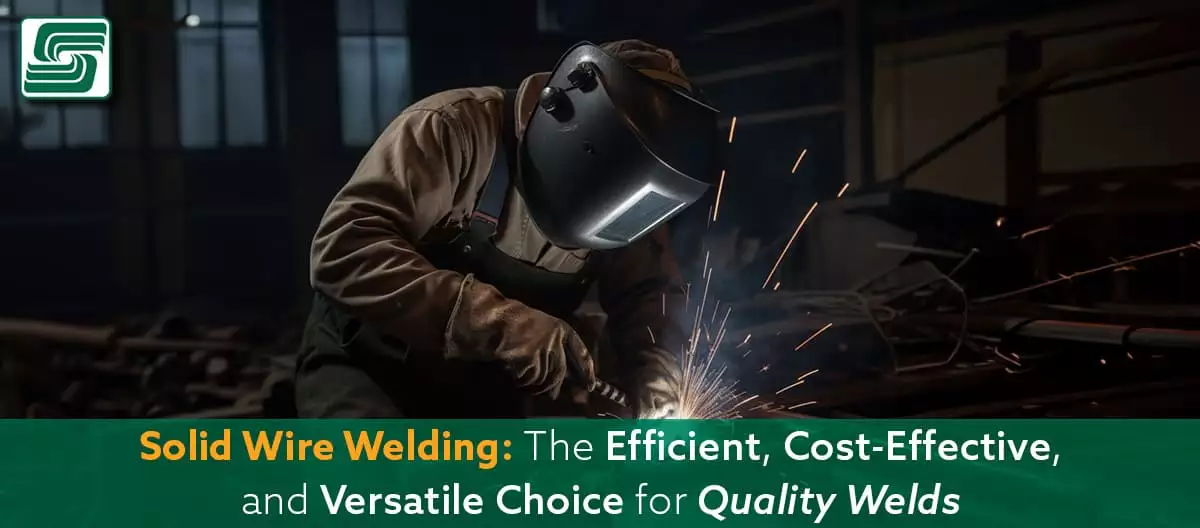
Welding is essential in various industries, such as automobile, construction, and manufacturing. It involves joining two materials together using heat and pressure.
Solid wire welding is a popular method that uses a consumable electrode made of solid steel wire. This type of welding is widely used because of its many benefits.
A brief explanation of solid wire welding
Solid wire welding is a type of Gas Metal Arc Welding (GMAW) that uses a solid metal wire as the consumable electrode. The process involves melting the base metal and the filler metal (the solid wire) together to form a strong joint.
The filler metal provides additional material for the joint, making it stronger than the base metal alone. Solid wire welding uses shielding gas to protect the weld pool from contamination.
Importance of welding in various industries
Welding plays a crucial role in many industries, including construction, automotive, aerospace, and manufacturing. It creates complex structures by joining two or more pieces of metal together.
Without welding, many products we use daily would not exist. For example, welding creates car frames and bodies in the automotive industry.
In construction, it’s used to combine structural steel beams to create large buildings or bridges. Aerospace engineers use welding to join complex parts together for airplanes and spacecraft.
In addition to creating structures and products, welding ensures safety by ensuring joints are strong enough to support loads without breaking or failing over time. Welding also helps reduce waste by allowing companies to salvage materials that would otherwise be discarded because of damage or wear.
Overall, solid wire welding remains an important process in modern-day manufacturing processes because of its high-efficiency levels and quality welds produced with it compared with other forms of arc-welding processes like TIG/MIG while still being cost-effective and easy to use. In the upcoming sections, we will discuss the advantages of solid wire welding over other methods in detail.
Higher Efficiency
Welding is essential in many industrial processes, including construction and manufacturing. Solid wire welding is an efficient method because of its faster welding speed.
This advantage means the welder spends less time on the welding process, increasing productivity for both small and large-scale projects. In addition to speed, solid wire welding requires minimal time spent on cleaning and preparation.
Compared to other methods like TIG or MIG welding, there's no need for gas shielding or flux; hence, less equipment is needed, making solid wire welding a more efficient process since it saves time and money without compromising on quality.
Better Quality Welds
Solid wire welding guarantees stronger welds because of higher deposition rates. The consistent deposition rate provided by this method ensures that the weld is structurally sound with fewer weak points, thus giving the product a longer lifespan.
Furthermore, solid wire welding reduces spatter and porosity during the process compared to other methods like stick welding, which leaves behind slag that needs cleaning up when done. Solid wire welds also have an improved appearance since they produce smooth finishes without blemishes or surface imperfections.
Versatility
Solid wire welding can be used with various materials, such as stainless steel, aluminum, and carbon steel. It is also suitable for both thin and thick materials, making it a versatile option for various industrial applications where different metals are used concurrently. Moreover, this method handles high-heat input without causing any warping of thin metals since it provides complete fusion during the process while still maintaining its strength properties.
Cost-effective
Another advantage of solid wire welding is its cost-effectiveness compared to other methods, such as TIG or MIG welding. The reduced preparation times and lower equipment costs because of the simplified setup result in low overheads and higher business profits.
In addition, since solid wire welding requires less shielding gas and other consumables, product manufacturing costs are significantly lower, making it an affordable option for small businesses and large-scale industrial manufacturers.
Ease of Use
Solid wire welding is an ideal option for beginners or those with limited experience in welding. The process is easy to learn and requires less skill than other methods like TIG or MIG welding, requiring higher levels of expertise.
Additionally, the equipment used in solid wire welding is much simpler than other methods hence providing a straightforward learning curve. The ease of use also means that the welder completes jobs faster without sacrificing quality while always producing consistent results.
Higher Efficiency: Faster Welding Speeds, Less Prep Time, and Increased Productivity
Solid wire welding is known for its higher efficiency than other welding methods like TIG or MIG welding. One of the reasons for this is the faster welding speed that solid wire welding offers. Since a continuous wire feeds into the weld pool, it reduces the need to frequently stop and reload electrodes, making it faster and more efficient.
Another factor contributing to higher efficiency is less time spent on cleaning and preparation. Solid wire welding uses a shielding gas to protect the weld from contaminants such as oxygen and moisture, meaning less time is spent cleaning surfaces before welding. Increased productivity comes naturally with higher efficiency.
Solid wire welding allows for more welds to be completed in a shorter amount of time, ultimately leading to better productivity. Solid wire welding makes all the difference in completing projects efficiently without compromising on the quality in industries where time is precious- like construction or manufacturing.
Better Quality Welds: Stronger Welds with Reduced Spatter and Porosity
Solid wire welding produces better quality welds because of several reasons.
- Solid wires have a higher deposition rate than flux-cored wires, which leads to stronger welds.
- Since no slag or flux components are involved in this welding method, there is reduced spatter and porosity during the process, making for cleaner-looking welds.
- When using solid wire instead of other types of filler materials like stick electrodes or flux-cored wires that produce slag - it's possible to control heat input more precisely, which helps maintain uniformity throughout each part of the welded joint.
Overall, better quality welds mean less rework required down the line, which saves both time and money in terms of repairs needed further down the road.
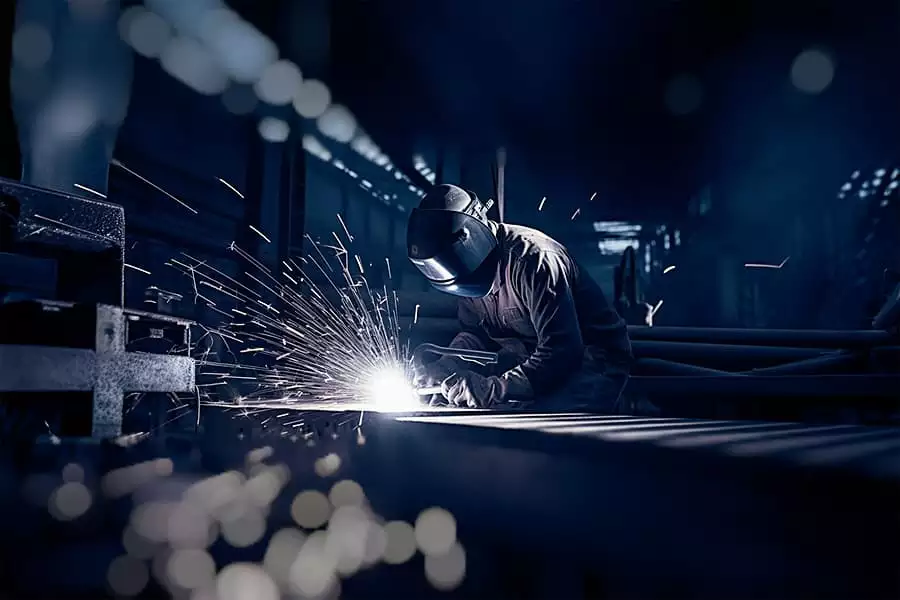
Versatility: Suitable For Different Materials and Thicknesses
Solid wire welding is versatile because it can be used with several materials, such as stainless steel, aluminum, and carbon steel, so it can be adapted to different welding jobs without requiring extensive changes to the equipment setup. Solid wire welding suits both thin and thick materials, making it an ideal choice for various projects.
Thin materials require a welding method that produces minimal deformation and heat input, while thicker materials require a method that provides enough heat input to penetrate all the way through. Solid wire welding handles both situations efficiently, making it an excellent choice for many applications.
In Sum
Solid wire welding has many advantages over other methods like TIG or MIG. Solid wire welding leads to increased productivity with its higher efficiency in terms of faster speeds and less preparation time.
Additionally, better quality welds produced by solid wire ensure less rework, saving time and money. The versatility of solid wire welding makes it an ideal choice for different kinds of projects with varying material thicknesses.
Overall, this type of welding offers a cost-effective option that requires less skill than other methods making it highly accessible even to beginners.