Articles like these typically begin, "using laser technology used to sound like science fiction," but I will not start things this way.
I'm old enough to remember the transition from music cassettes to CDs. The first commercial CD players were expensive! Like all new technology, only a few companies could mass-produce CD players. Those were the days before startup companies appeared overnight, having the capability to make cheaper, disposable electronics countering the top brands.
When I bought my first stereo, a Pioneer rack system with seven (!) CDs queued up; I was in heaven. I didn't have to do much except let the stereo do its thing. If I recall correctly, I think I paid more for that Pioneer stereo than I did my first car. The car lasted longer, though. A lightning strike took care of the stereo.
Until CD players became common, I was stumped; trying to think of another laser uses became quite challenging. Nowadays? We take them for granted. Think of:
- How quickly cashiers work through a conveyor of groceries
- The precision surgeons have during eye surgery
- Knowing exactly how far you are away from the flag on a par five-hole on a golf course.
Using lasers in manufacturing has also become ubiquitous in a myriad of ways. One example is using lasers to cut metal rapidly and with greater accuracy. Despite this increase in productivity and quality, a seemingly innocent result of laser cutting developed. This result created a breakdown in protective metal coatings: the buildup of Laser Oxide Scale.
How? Well, we'll get to that, but let's peek at how the laser has developed over 100 years.
Formidable One-Two Punch: Max Planck and Albert Einstein
Max Planck is the German theoretical physicist famous for being the originator of quantum mechanics, a revolutionary theory of atomic and subatomic processes. However, in 1900, while working on the problem of how an object emits radiation relative to its temperature, he derived a formula that
... agreed very closely with experimental data, but the formula only made sense if he assumed that the energy of a vibrating molecule was quantized--that is, it could only take on certain values. The energy would have to be proportional to the vibration frequency.
Plus, the energy seemed to come in little chunks of the frequency multiplied by a certain constant. This constant came to be known as Planck's constant.
Limited Theories
The leading theories about light at the time couldn't explain Planck's work. It was a radical idea to suggest transmitting energy in discrete lumps, no matter how small. Planck didn't realize the significance of his work, and he thought he was fudging his numbers to get the correct answer.
Mr. Einstein
Planck was convinced that a better explanation for his formula would come elsewhere. Enter Albert Einstein. Based on Planck's work, Einstein proposed light also transmitted energy in lumps—tiny particles called photons. The energy of each photon uses the energy of Planck's constant times its frequency, leading to Einstein predicting Stimulated Light Emission.
His theory proposed that stimulating electrons create light in particular wavelengths. Einstein's stimulated light emission became the foundation for laser technology's principle. However, it took years before they proved his theory correct.
Proving Einstein Right
German physicist Rudolf Ladenburg studied the optical properties of neon gas at a wavelength close to where the gas absorbed, then emitted light. His indirect observation in 1928 of stimulated light emissions led to the first evidence that stimulated emission existed, proving Einstein's theory. Then, in 1939, Valentin Fabrikant theorized the amplification of radiation by stimulating emissions.
Theory to Practical
There were two primary reasons that laser technology stalled after Fabrikant and Ladenburg's work. First, they worked independently of each other and, of course, World War II.
During the war, light-related research stopped. After WWII ended, the sophisticated equipment they worked on during the war was available as military surplus! Using that equipment and working with small budgets, many resumed their work.
Charles Townes worked on American military radar during WWII. He researched ways of increasing the strength of the radar while reducing the size of the equipment. His goal was making it small enough to fit inside an airplane.
As the war progressed, Townes switched to microwave frequencies and increased the power output. None of his work resulted in battle-ready equipment. Townes' work using a 24-GHz system, the availability of military surplus equipment, and his interest in microwave spectroscopy helped move the idea of laser technology forward.
From Maser to Laser
Townes' work with microwaves, stimulating microwave emissions, led to the Microwave Amplification by Stimulated Emission of Radiation, or simply maser. Townes and his team won the Nobel Prize in Physics for their maser work. For the next decade, research and development of masers continued with enthusiasm.
The groundwork laid by maser research created the foundation for lasers. In 1959, Gordon Gould, a graduate student from Columbia University, thought a stimulated emission could amplify light. Gould coined Light Amplification by Stimulated Emission of Radiation, or LASER.
Masers and Lasers: Cut from the Same Cloth
The combination of maser research with Gould's insight led to further laser development. Theodore Maiman built his first working laser prototype in 1960, using a synthetic ruby crystal as the operating medium.
We still use those ruby lasers commercially for drilling tough surfaces because of their high peak power. Ruby lasers were first used as military range finders. Their red light became ubiquitous, especially as a special effect in those science fiction movies.
Afterward, other researchers developed other kinds of lasers.
- Ali Javan's gas laser in 1960
- Robert Hall's semiconductor injection laser in 1962
- And one of the most important ones, the carbon dioxide (CO2) laser
Kumar Patel developed at AT&T Bell Labs 1964 the first CO2 laser. CO2 lasers offer higher efficiency at a lower cost than ruby lasers, making them the most popular industrial laser.
In 1967, Peter Houldcroft of The Welding Institute in England performed the first commercial application of laser materials processing. He used an oxygen-assisted CO2 laser to cut through a 1 mm thick steel sheet.
Creating a laser beam is one thing: maintaining it another. Masers and lasers need to stimulate and amplify light sources. Nikolay Basov was a Soviet physicist who contributed to the laser journey by developing oscillators and amplifiers. Like champagne, he stumbled on the solution by accident:
While trying to find ways of moving electrons around atoms into higher-energy states and researching oscillators, Basov stumbled upon the concept of negative absorption. Negative absorption is commonly called the pumping method.
Basov's work created a way for a sustainable laser beam by maintaining the needed population inversion of the laser from pumping electrons into a metastable state. That pumping is needed to release photons.
The rest, they say, is history.
Cutting Edge Tech: Lasers Cutting Metal
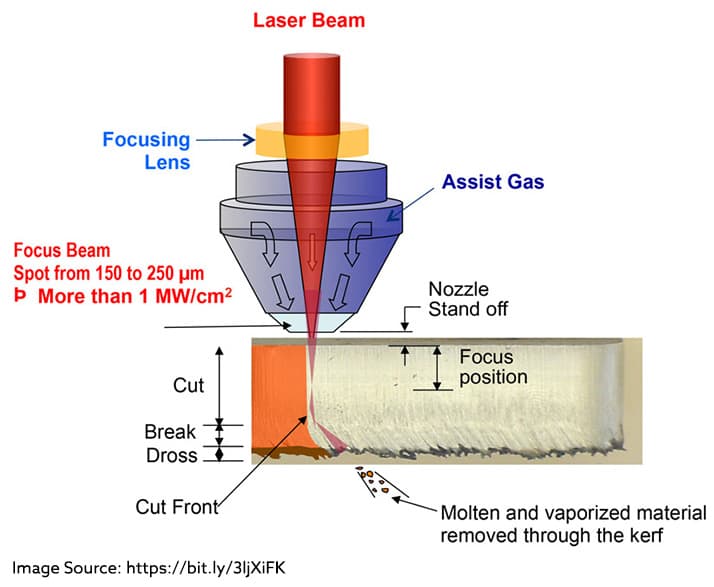
As laser technology grows, so have its uses. Eventually, lasers found their way to manufacturing. One of the primary ways lasers have affected manufacturing is their ability to cut metal—a staple in steel fabrication.
Three principal components work together for cutting sheet metal:
- Laser beam source
- Laser beam guide
- Processing head with a cutting nozzle.
Metal melts, vaporizes, and burns after focusing the laser beam. Laser amplification materials then take place after reflecting internally through a partial mirror. The phenomenon continues until it builds enough energy in a stream of coherent monochromatic light to allow for its escape. The intensity of the light increases after using fiber optics or mirrors to focus on the work area.
A easier way of saying this is using a concentrated, tightly focused beam of light on a tiny area that brings the heat, so to speak. Think of the tip of a pencil easily pokes through a sheet of paper, while a rigid piece of cardboard simply slaps against it without leaving a mark.
Advantages of Laser Cutting
There are several advantages of cutting metal with lasers:
Accuracy and Precision
The phrase "laser accuracy" isn't a misnomer. Manufacturers enjoy cutting gaps barely wider than the beam with tolerances of +/- 0.1 millimeters. There's no speed drop-off either. Depending on the metal type, speeds of up to 130 feet per minute are typical.
Low-Cost
Lasers don't cost a lot of money for setup, operation, or maintenance.
Flexibility
There is a wide tolerance for cutting with lasers, and you don't need to retool for the myriad of metal thicknesses or metal types.
Little Waste
Using CNC programming, nearly the entire metal sheet is used. Changing the location of the cut also reduces the chances of the metal warping from exposure to such high heat in the localized area.
This embedded video illustrates both the speed and accuracy of the laser cut.
Energy Savings
It sounds like an oxymoron because of the speed the laser moves; laser cutting saves energy. But it's true! Usually, the laser is the only component moving, plus the speed involved means less cutting time. Less time equals less energy used, equaling lower operating costs.
Disadvantages of Laser Cutting
There are many disadvantages to cutting metal with a laser, like any process. However, we'll stick to these four.
Material Evaporation
Heat creates an exchange of a material's state. For example, fire boils water, changing water into steam. Although it's a simplistic example, the same results occur if you try cutting plastic with a laser. The heat from the laser melts the plastic. Avoiding this issue is possible, but it entails a change in tooling and programming, which isn't free.
Experts Sometimes Needed
Further expertise isn't necessarily needed if the laser cutting process is correctly set up. However, if unforeseen failures occur, they need a knowledgeable technician to fix those failures. Unless a manufacturer staffs such an expert, hiring someone to visit a facility onsite adds up.
Metal Thickness Limitations
Most manufacturers install laser cutting systems to fabricate metal of specific thicknesses. Customer specifications falling within those thicknesses create the sweet spot for fabricators. However, those same manufacturers don't have the flexibility to change their lasers to cut thicker material. This limits the range of customer specifications and earning them revenue.
Expensive to Startup
Most laser cutting stations require a capital expenditure to install, operate, and maintain the system. After paying those startup costs, laser cutting stations are relatively inexpensive to run.
Dangerous Gases and Fumes
Toxic gases and fumes directly result from the metal laser cutting process. Removing those gases is tantamount to human safety. Creating that safe environment also costs money.
Scratching and Flaking the Surface: Laser Oxide Scale
Laser oxide scale is a film formed on metal surfaces after laser cutting metal from the combination of extreme temperatures and oxygen. The scale is found near the area laser cut and has a shiny bluish finish. Most importantly, the oxide scale prevents any powder coating or paint from sticking to the metal substrate.
Sounds innocuous enough, right?
Unfortunately, it's not. Companies pay fabricators sizeable sums of money to create functionally attractive components. That layer of oxide becomes the Achilles Heel for steel parts; any finish easily chips or flakes off, exposing the substrate to the elements, defeating the purpose of those protective metal coatings.
Taking a Bath
Removing the oxide scale becomes essential during the metal fabrication process. Fortunately, it's a simple solution: pre-wash systems.
In a pre-wash system, typically multi-stage, one of the first stations is an acid or chemical shower removing the oxide scale. This simple step removes the potentially destructive element of air and moisture exposure to a steel substrate.
In Sum
If someone creates a house of cards, something minimal causes it to tumble. This analogy is apt; consider it when thinking of a metal laser cutting system.
Decades of research, development, and implementation of lasers in manufacturing have led to their ubiquitous use. The advantages laser presents are impressive, but the weakest link doesn't seem dangerous—it's literally the width of a fingernail!
That small layer of oxide prevents protective coatings from performing the intended job. At the least, a quality fabricated and painted component has an ugly spot. At the worst, the resulting oxidized layer creates potential structure failure from instability caused by rust.
Laser oxide scale: a slight problem with a simple solution.