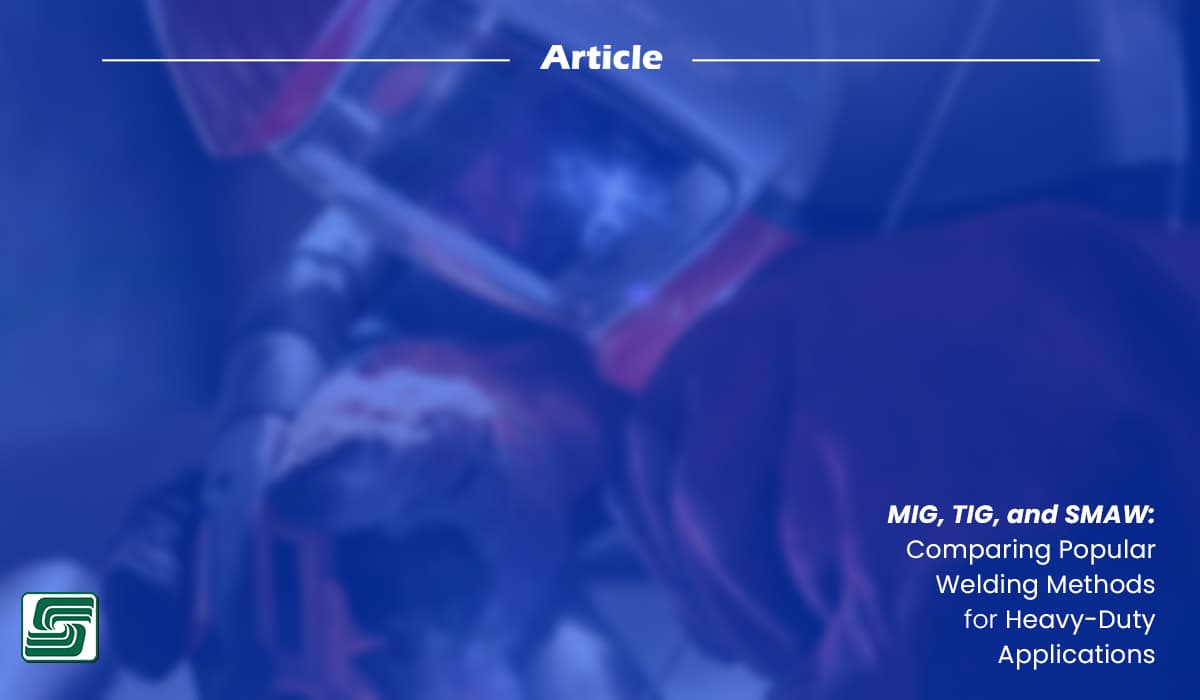
Welding is crucial in heavy-duty applications, serving as the cornerstone of many industrial processes and infrastructure development.
The Importance of Welding in Heavy-Duty Applications
Welding is essential for heavy-duty applications, such as:
- Construction
- Shipbuilding
- Aerospace Engineering
- Automotive Manufacturing
Welding is a process that makes it possible to fabricate important structures, machinery, and vehicles for these industries on a large scale. It guarantees the reliability and security of important heavy-duty machinery and infrastructure elements.
TL:DR
Throughout this exploration of welding methods for heavy-duty applications, several key points have emerged:
- Different welding processes, such as MIG, TIG, and SMAW, offer unique advantages and considerations for producing various welds. For instance, MIG welding produces smooth joints with minimal slag or spatter interference, while GMAW's large arc enables the welding of thick and thin materials using the same process.
- Innovative techniques like friction spot welding have expanded the employability of welding advanced higher-strength aluminum alloys that were previously challenging to weld with conventional methods.
- Each arc welding process, including Submerged Arc Welding (Sub-Arc) and Gas Tungsten Arc Welding (TIG), presents specific benefits and considerations for achieving good penetration, high deposition rates, weld metal fusion, and cost savings in different scenarios.
- Weld process data is crucial in educating new welders, developing new welding processes, and increasing the efficiency of high-specification projects using rare or expensive materials.
Overview of Welding Techniques
Various welding techniques are employed to meet the diverse needs of heavy-duty applications. These techniques include:
Each method offers unique efficiency, quality, and suitability advantages for specific materials.
Innovative joining techniques have become essential because the welding industry demands improved productivity, efficiency, and quality. These techniques address the challenges posed by sophisticated materials used in heavy-duty applications.
By gaining insights into the diverse uses and benefits of welding methods in heavy-duty applications, people make informed decisions when selecting the most suitable technique for their industrial needs.
Understanding MIG, TIG, and SMAW Welding
MIG, TIG, and SMAW are prominent welding methods with unique characteristics and applications in heavy-duty applications.
MIG Welding: The Role of Solid Wire and Gas
MIG welding, or Gas Metal Arc Welding (GMAW), uses a solid wire electrode and a shielding gas to join metals.
GMAW and Its Industrial Applications
GMAW is widely employed in various heavy-duty industries, such as automotive manufacturing, shipbuilding, and structural steel fabrication. This method is favored for producing clean welds on various materials, including aluminum, stainless steel, and mild steel.
MIG Welding Efficiency
MIG welding offers exceptional efficiency because of its semi-automatic or automatic nature. The wire electrode's continuous feeding and shielding gas results in faster weld completion times than other manual welding processes.
This efficiency makes MIG welding suitable for large-scale industrial projects where productivity is paramount.
TIG Welding: Precision and Quality
Tungsten Inert Gas (TIG) welding is renowned for its precision and high-quality welds achieved without filler metal.
Longevity's diverse range of welding equipment includes advanced TIG welders that cater to the demands of precision welding in heavy-duty applications.
The Art of Shielded Metal Welding
TIG welding involves using a non-consumable tungsten electrode and an inert shielding gas, such as argon or helium.
This process ensures that the weld area remains free from atmospheric contamination, resulting in exceptionally clean and high-integrity welds suitable for critical components in heavy-duty machinery and structures.
Helium Shortage and Its Impact
The global helium shortage has significantly affected Tungsten Inert Gas (TIG) welding.
Helium is a commonly used shielding gas in TIG welding because of its superior arc characteristics. The shortage has increased costs and made maintaining optimal welding conditions challenging.
The effort to maintain welding conditions has prompted industry professionals to explore alternative shielding gases while adapting their techniques to mitigate the impact of the helium shortage.
SMAW Welding: Versatility and Accessibility
Shielded Metal Arc Welding (SMAW), called stick welding, offers versatility and accessibility in heavy-duty applications.
Longevity's comprehensive range of welding equipment includes the FAB Times SMAW Series designed to meet the diverse needs of SMAW applications.
SMAW Required Equipment and Its Applications
SMAW requires minimal equipment compared to other welding methods, making it highly accessible in various industrial settings.
It is effective for outdoor construction projects, where portability is essential. SMAW's capability to produce robust welds on thick materials makes it indispensable in heavy-duty fabrication scenarios.
When looking into the distinctive attributes of MIG, TIG, and SMAW welding methods and their specific industrial applications, people gain valuable insights into selecting the most suitable technique based on their unique project requirements.
Key Differences between SMAW, MIG, and TIG
When comparing Shielded Metal Arc Welding (SMAW), Metal Inert Gas (MIG), and Tungsten Inert Gas (TIG) welding methods, several key differences become apparent.
One of the primary distinctions lies in the arc efficiency of each method.
Increasing Arc Efficiency: SMAW vs. GMAW
Mechanized welding processes might optimize weld quality and production speed.
- Quality and speed are relevant when comparing SMAW with Gas Metal Arc Welding (GMAW).
- While SMAW is versatile and popular for repairing and changing metal parts because of its accessibility,
- GMAW offers increased arc efficiency, resulting in faster completion times for welding projects.
The wire electrode's continuous feeding and shielding gas in GMAW contribute to its higher arc efficiency than SMAW.
Quality Welds: The Top Priority
In heavy-duty applications, achieving high-quality welds is paramount. TIG welding has been found suitable for joining metals like aluminum, stainless steel, and copper, producing strong and consistent-quality welds.
MIG welding produces smoother weld beads with better quality and is suitable for thin materials. Innovative joining techniques like electromagnetic pulse welding join difficult-to-weld dissimilar materials while maintaining high-quality welds.
Heavy-Duty Welding: Choosing the Right Process
In heavy-duty applications such as metal fabrication, choosing the right welding process is crucial to ensure structural integrity and durability.
Metal Fabrication and Its Challenges
Metal fabrication involves intricate processes that demand precision and reliability.
Each welding process has advantages and disadvantages that help determine the most suitable process for a project.
For instance, TIG welding's precision makes it ideal for intricate metal fabrication tasks where high-quality welds are essential.
The Future of Welding in Heavy-Duty Applications
The field of welding is witnessing rapid technological advancements, paving the way for innovative approaches to welding processes in heavy-duty applications.
These advancements encompass several developments, including integrating robotic welding systems and using innovative materials.
Robotic welding has emerged as a game-changer in heavy-duty applications, offering unprecedented precision, efficiency, and safety. Advanced robotic welding systems have state-of-the-art sensors and programming capabilities that enable them to execute complex welds with unparalleled accuracy.
These systems have significantly reduced human error while enhancing productivity in industries such as automotive manufacturing, where intricate welds on vehicle components demand the utmost precision.
Integrating AI and machine learning algorithms has revolutionized robotic welding by enabling real-time adjustments based on environmental factors and material variations.
This adaptive capability ensures consistent weld quality across diverse workpieces, contributing to welded structures' overall reliability and durability in heavy-duty applications.
The Growing Demand for Exceptional Welding Services
As heavy-duty industries continue to evolve, there is a growing demand for exceptional welding services that meet the stringent requirements of modern infrastructure development and industrial fabrication.
The need for high-quality welds that exhibit superior strength, corrosion resistance, and structural integrity has become paramount in sectors such as aerospace engineering and offshore construction.
In response to this demand, service providers focus on enhancing their expertise in specialized welding techniques for heavy-duty applications.
For instance, Longevity's commitment to research and development has led to advanced welding equipment designed specifically for challenging materials and critical components in heavy-duty machinery.
There is an increasing emphasis on environmentally sustainable welding practices within heavy-duty industries. Adopting eco-friendly shielding gases and flux-cored wires aims to minimize environmental impact while maintaining exceptional weld quality.
This shift towards sustainability aligns with global efforts to reduce carbon emissions and promote greener manufacturing processes across various industrial sectors.
Making Informed Choices
Making informed choices in welding is paramount for achieving optimal results in heavy-duty applications.
People select the most suitable technique based on their project requirements by understanding the distinct characteristics and applications of various welding methods.
This informed decision-making ensures welds meet stringent quality standards while addressing specific challenges of different materials and fabrication tasks.
Staying abreast of technological advancements in robotic welding systems and innovative approaches to welding processes is essential for meeting the evolving demands of heavy-duty industries.
Integrating artificial intelligence (AI) and machine learning algorithms has revolutionized robotic welding by enabling real-time adjustments based on environmental factors and material variations.
In Sum
The future of welding in heavy-duty applications hinges on continuous technological advancements, sustainable practices, and the ability to make informed choices that align with the specific needs of industrial projects.
By embracing these principles and effectively leveraging diverse welding techniques, professionals contribute to developing robust structures and machinery that uphold safety standards while driving progress across various sectors.