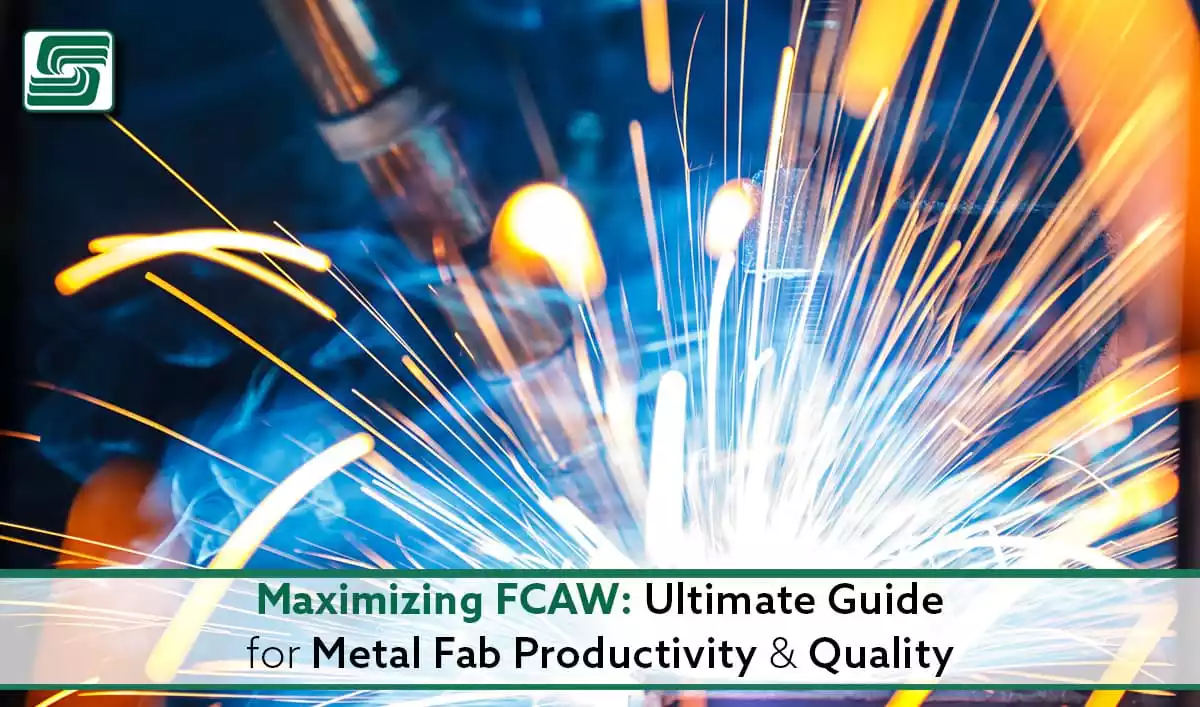
Metal fabrication is essential in various industries, from construction to manufacturing. A crucial part of metal fabrication is welding, which can be a time-consuming and expensive process. However, advancements in welding technology have made it easier and more efficient than ever.
One of these technologies is Flux Cored Arc Welding (FCAW).
This article is the third in a series of three exploring aspects of FCAW. You can read the series here:
What is FCAW?
Definition and Explanation of the Process
Flux-cored arc welding (FCAW) is a popular process involving a tubular wire electrode with a flux core. The flux core provides a shielding gas to protect the weld from contaminants in the air, such as oxygen and nitrogen. The electrode is continuously fed through a wire feed system, maintaining a consistent arc length and deposition rate.
The FCAW process can be used for both thick and thin metal sections, making it versatile in various applications. It is commonly used in shipbuilding, construction, pipe welding, and other heavy-duty industries.
Comparison with Other Welding Processes
FCAW has some significant advantages over other welding processes, such as Gas Metal Arc Welding (GMAW), also known as MIG (Metal Inert Gas) welding, or Shielded Metal Arc Welding (SMAW), otherwise known as Stick welding. Compared to GMAW or MIG welding, FCAW uses less expensive equipment because it does not require an external shielding gas supply, making it more cost-effective for certain applications. FCAW also produces higher deposition rates than GMAW due to its use of larger-diameter electrodes.
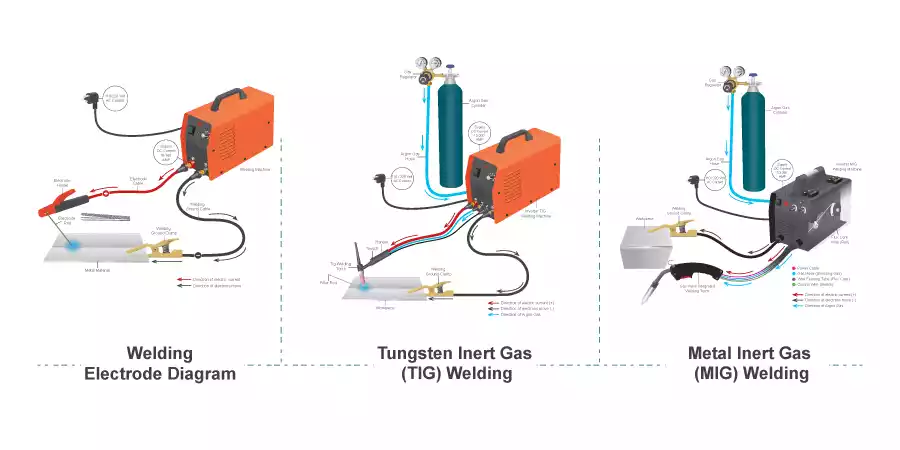
Compared to SMAW or stick welding, which often requires difficult joint preparation techniques such as grinding before the actual weld can begin, FCAW allows for easier preparation since slag removal is minimal. Additionally, since FCAW produces less smoke during the process than SMAW, it is more environmentally friendly.
In comparison to Tungsten Inert Gas (TIG) or Gas Tungsten Arc Welding (GTAW), which requires more skillful manipulation by operators due to its slower travel speed and smaller electrode size, FCAW uses larger diameter electrodes, produces higher deposition rates, and allows for a higher travel speed.
Advantages of FCAW in Metal Fabrication
Higher Deposition Rates
FCAW is a high-productivity welding process that provides a higher deposition rate than many other processes because the wire used in FCAW is much thicker than MIG or TIG welding wire. Its flux coating allows the welder to quickly put down a lot of metal, which can be especially useful when working on large projects or when time is limited.
However, it's important to note that deposition rates are affected by several factors, including the type of metal being welded and the thickness of the metal. So while FCAW can be very productive, it's not always the fastest option in all situations.
Improved Weld Quality
One of the biggest advantages of FCAW over other welding processes is its ability to produce high-quality welds because of two main factors: deep penetration and reduced porosity. Deep penetration means the weld penetrates deep into the joint, creating a strong bond between the two pieces of metal being welded.
The penetration helps ensure that the finished product is structurally sound and can withstand stress and pressure. Reduced porosity means fewer air pockets or voids in the finished weld. These voids can weaken the overall structure of the weld and lead to failure over time.
With FCAW, however, because there's a flux coating on the wire used for welding, it helps protect against contaminants like oxygen and nitrogen, which can cause porosity issues with other welding methods.
Versatility in Welding Different Types of Metals and Thicknesses
Another significant advantage of FCAW welding is its versatility when welding different types of metals and thicknesses. It can be used for ferrous (iron-based) and non-ferrous metals, which means it can be used to weld steel, stainless steel, aluminum, and even some exotic materials.
In addition to being able to weld a wide range of metals, FCAW is also useful for welding thicker materials because the high deposition rate makes it possible to put down more metal in less time.
However, it's worth noting that FCAW may not be the best option for thinner materials as it can sometimes cause warping or distortion.
Reduced Welding Costs
Another benefit of FCAW is its relatively low cost compared to other welding processes because the equipment needed for FCAW is generally less expensive than other welding equipment like TIG or MIG welders.
Furthermore, since FCAW can lay down more metal faster than other methods, overall welding time and labor costs are reduced, making FCAW an attractive option for large-scale projects where cost efficiency is a significant factor.
Easy to Learn and Use
Another advantage of FCAW is that it's relatively easy to learn and use compared to other welding processes. While there are still techniques and skills that must be developed over time with practice, many welders find that they can quickly pick up the basics of FCAW without extensive training or experience.
This ease of use means that even those who may not have had much experience with welding before can quickly become proficient with the process. And its productivity-boosting capabilities combined with these benefits in quality control and material versatility make FCAW a smart choice for many fabricators looking to improve their operations' bottom line.
Choosing the Right Filler Metal for Your Application
Factors to Consider When Selecting Filler Metal
When selecting a filler metal for your FCAW welding application, it is important to consider several factors. First, you need to determine the base metal you will be welding, which determines the classification of the filler metal and ensure that it has similar properties to the base metal. Additionally, joint design is also important when selecting filler metal.
For example, if you are welding a butt joint between two thick pieces of steel, you may want to use a higher-strength filler wire. On the other hand, if you are welding a lap joint between thin pieces of steel, using a lower-strength wire may be appropriate.
Welding position is another factor to consider when selecting filler metal. Horizontal or vertical up welding typically requires thinner wires with faster freezing characteristics to prevent sagging or drooping.
Overview of Common Filler Metals Used in FCAW
Several common types of filler metals are used in FCAW welding:
It's important to note that many other types of filler metals are available depending on your specific application.
Selection Guides
Most filler metals come with a selection guide to help you determine the appropriate wire for your application. These guides typically consider the base metal type, joint design, and welding position. Be sure to follow the manufacturer's recommendations for best results.
It is also important to ensure that your filler metal is properly stored to prevent moisture absorption, which can lead to porosity in welds. Store your wire in a dry location and use a moisture-resistant packaging or container.
Equipment Needed for FCAW Welding
Power Sources
To start FCAW, the first thing required is a power source. The power supply must provide a current level corresponding to the wire size and thickness of the metal being welded. A good quality power source should provide stable electrical output to ensure smooth welding operation.
It's essential to consider input voltage, duty cycle, and output voltage factors while selecting a power source. A good tip is to prioritize a portable and inverter-based welder, as they are easier to move around.
Wire Feeders
The wire feeder is essential for FCAW welding because it moves the electrode wire through the gun cable and into the weld pool.
Choosing a wire feeder compatible with your chosen FCAW process, wire type, and size is important. Wire feeders come in two types: stationary bench-top models that can only be moved with considerable effort; or portable models with wheels that can easily be moved around any worksite.
Guns & Nozzles
FCAW process guns come in various sizes based on their amperage ratings, ranging from 150-600 amps.
Guns also vary by length; common lengths include 8 feet, 10 feet, or 12 feet. The choice of length depends on how far away you need to stand from your workpiece when welding. The guns also come in different ergonomic designs depending on your preference or comfort level.
The nozzle is an integral part of the gun assembly and helps direct gas flow into your weld pool while protecting it from contaminants such as dirt or debris. While selecting nozzles for your gun assembly, ensure they're compatible with both the electrode size and shielding gas type.
Shielding Gas Systems
FCAW welding requires using a shielding gas, usually carbon dioxide (CO2) or a combination of CO2 and argon gas. The shielding gas helps to protect the weld area from atmospheric contamination, such as oxygen or moisture. An appropriate shielding gas system should be selected based on your application requirements.
Tips for Maintaining Equipment to Ensure Optimal Performance
Proper maintenance of equipment ensures optimal performance. Keeping your equipment clean and free from debris and dirt accumulating over time is essential.
- Check your cables regularly for damage or wear that can cause electrical shorts or disruptions in your welding process.
- Periodically recalibrate your machine settings based on the material being welded and the electrode size, ensuring you're always operating at peak efficiency while minimizing errors and downtime.
- The right equipment for FCAW welding is essential for productivity and quality in metal fabrication.
- The power sources, wire feeders, guns & nozzles, and shielding gas systems all work together to ensure smooth operation during FCAW welding.
- Always maintain your equipment properly to last longer while providing consistent results with less downtime.
Techniques for Successful FCAW Welding
Preparation steps before welding.
Before starting any welding project, preparation is key to a successful outcome. The following preparation steps should be taken before FCAW welding:
- Clean the Metal: Ensure that the metal surfaces to be welded are free of rust, dirt, oil, or other contaminants. Use a wire brush or grinder to clean up the surface.
- Select the Correct Wire and Equipment: Choose the appropriate wire size and type based on the joint design and base metal thickness. Select proper equipment such as power sources, wire feeders, and shielding gas systems.
- Check Your Settings: Adjust equipment according to the manufacturer’s specifications for maximum efficiency. Make sure that all connections are tight.
- Select Proper Joint Design: Choose an appropriate joint design based on the application and weld position.
Taking these steps before beginning your project will reduce unexpected issues and ensure a smooth welding process.
Tips for proper electrode manipulation
Proper electrode manipulation is critical for successful FCAW welding. Here are some tips to ensure that you’re effectively managing your electrode:
- Maintain Consistent Contact Angle: The contact angle between the electrode and workpiece should be approximately 15 degrees from vertical. Maintaining this angle will allow adequate penetration into the metal while reducing spatter.
- Straight Line Travel Pattern: Move in a straight line along with weld path while maintaining consistent travel speed. Moving in a zigzag pattern can lead to poor weld quality and increased porosity.
- Arc Length Control: Keep arc length consistent throughout the entire weld process by monitoring the distance between the electrode tip and the workpiece at all times.
By following these tips, you can maintain optimal electrode performance throughout your FCAW welding process.
Common mistakes to avoid
Here are some common FCAW welding mistakes you should avoid:
- Excessive Spatter: Excessive spatter can occur when the electrode is not properly positioned, or the welder travels too slowly. Adjust speed, voltage, or current settings to decrease spatter.
- Inconsistent Travel Speed: Inconsistent travel speed can lead to uneven bead formation and poor weld quality. The use of a travel gauge can help maintain a consistent speed.
- Inadequate Penetration: Inadequate penetration can occur when the voltage or wire feed speed is too low. Increase either setting as necessary for deeper penetration.
- Wrong Joint Design: Joint design should be appropriate for the application and position of the weld. Choosing an inappropriate joint design leads to poor-quality welding.
By being aware of and avoiding these common mistakes, you maximize your productivity and produce high-quality welds using FCAW welding techniques.
Troubleshooting Common Issues with FCAW Welding
Identifying and Solving Problems in FCAW Welding
FCAW welding can sometimes be tricky to master, and even experienced welders may encounter problems that require some troubleshooting. Two common issues are porosity and lack of fusion. Porosity is the presence of small holes or gas pockets in the weld, which can weaken its strength.
Lack of fusion happens when the weld bead doesn't penetrate fully into the base metal or fails to fuse correctly with previously deposited metal. Both issues can result in a structurally unsound weld and prone to failure.
Steps for Troubleshooting Porosity
To fix porosity, you need to identify its root cause first. Here are some common reasons for porosity in FCAW welding:
- Contaminated Base Metal: Check for rust, dirt, oil, or other debris on your workpiece before welding.
- Improper Shielding Gas: Ensure your shielding gas flow rate is correct according to manufacturer guidelines.
- Incorrect Voltage Setting: Adjust your voltage settings according to the thickness of your metal. If none help solves the issue, change the filler wire type or diameter.
Steps for Troubleshooting Lack of Fusion
Lack of fusion could arise from several factors as well. Some possible solutions include:
- Reviewing Joint Preparation Techniques
- Adjusting Travel Speed
- Increasing Amperage Setting
If these steps do not solve the problem, consider using a different type of filler wire that works better with your particular combination of base metals.
In Sum
FCAW welding provides tremendous advantages over other welding processes for certain applications, but getting it right requires practice and patience. By following our guide on FCAW welding and troubleshooting common issues, you will be well on your way to boosting productivity and increasing the quality of your welds.
Always follow safety guidelines when welding to keep yourself and others safe. With practice, you can become an expert FCAW welder and achieve high-quality welds for your metal fabrication projects.
There's a lot to wrap your head around. Did we miss anything?