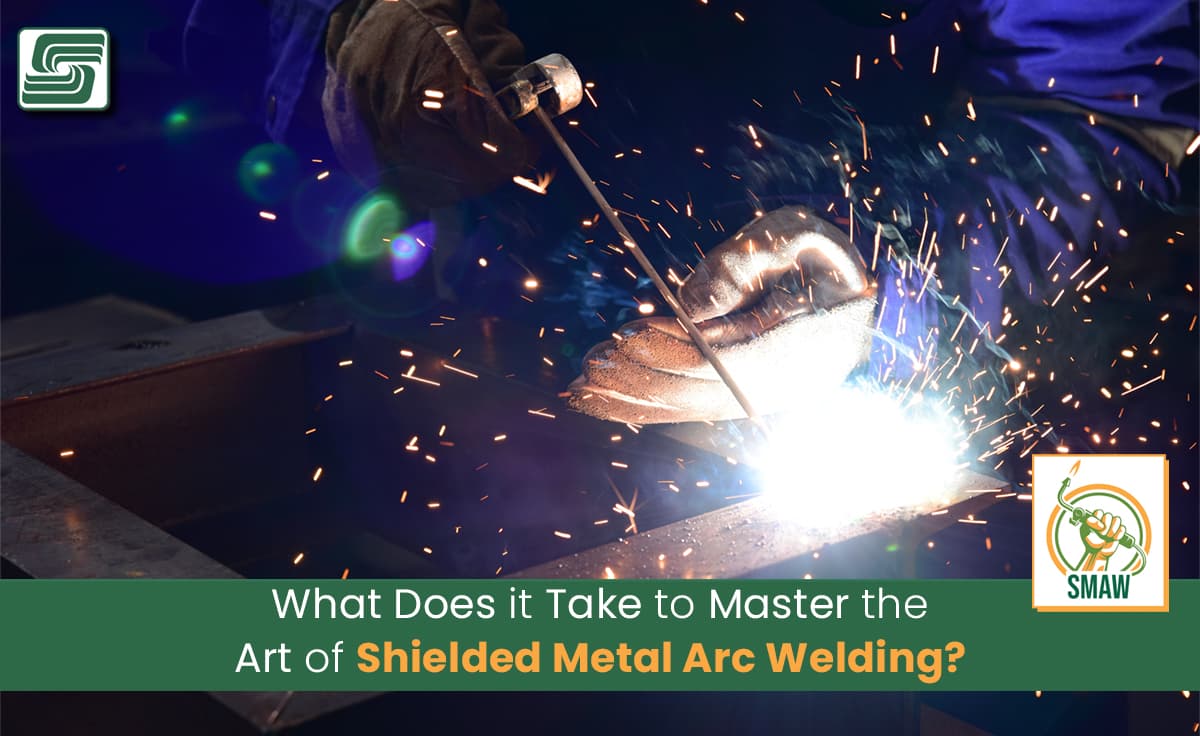
FAB Times SMAW Series
In our recent series on FAB Times, we delved deep into the world of Shielded Metal Arc Welding (SMAW). We focused on SMAW's nuances, starting with an overview of popular welding methods. The series also pits SMAW against other welding techniques, such as FCAW, GMAW, GTAW, and SAW, to help you understand which method best suits your needs.
Articles in the Series:
- How Well do You Know the 5 Most Popular Welding Methods?
Get a broad view of the top welding methods, including SMAW. Read More
- What Does it Take to Master the Art of Shielded Metal Arc Welding?
Learn what makes SMAW unique and how to master it. Read More
- SMAW vs. FCAW: Sparking a Debate About These Popular Welding Methods
Compare SMAW and FCAW to find out their pros and cons. Read More
- SMAW vs. GMAW: Unveiling the Key Differences to Decide Which is Better
Explore the differences between SMAW and GMAW. Read More
- Anyone Ever Teach you the Differences Between Stick and TIG Welding?
Understand how SMAW differs from GTAW, also known as TIG welding. Read More
- Speed Matters: How SAW Outpaces SMAW in Welding Efficiency
Learn why SAW is faster than SMAW and when to use each method. Read More
SMAW
Shielded metal arc welding (SMAW), also commonly known as stick welding, is a widely used welding process that involves the fusion of metal materials by applying intense heat generated by an electric arc. The electric arc is formed between a coated electrode, also called a "stick," and the base metal being welded. This versatile welding technique has existed for over a century and continues to be employed across various industries for its effectiveness and simplicity.
SMAW begins with an electrode composed of a solid metal core wire surrounded by a flux coating. The flux coating is essential, as it serves multiple purposes during welding.
- It provides a protective shield around the molten weld pool, preventing oxygen and other atmospheric contaminants from causing defects in the final weld.
- It acts as a deoxidizer, removing impurities from the base metal and electrode surface to ensure optimal weld quality.
An electrical current source is required to start the SMAW process. Typically, this involves using direct current (DC) or alternating current (AC) power supplies.
DC power offers better control and stability during welding procedures, since electrodes possess specific polarity requirements based on their composition. AC power is often chosen when working with magnetic materials or when portability is crucial because of limited power availability.
TL:DR: Quick Summary
Once the equipment is set up correctly and safety measures are in place, SMAW begins by striking an arc between the electrode tip and the workpiece surface through deliberate contact or scratch-starting techniques suitable for certain types of electrodes. As electricity flows through this connection, intense heat forms at the electrode tip because of electrical resistance within its core wire.
This heat generates temperatures reaching approximately 6,500 ºF (3,600 ºC), instantly melting both the electrode's filler material and base metal. During this molten state, an essential chemical reaction occurs within SMAW: vaporization of the flux coating.
The flux coating, containing various compounds, including minerals, metals, and organic substances, vaporizes when exposed to high temperatures. This vaporization generates a gaseous cloud around the welding area known as the shielding gas.
The purpose of this shield is twofold: it protects the weld pool from atmospheric contamination by isolating it from oxygen and nitrogen in the air while simultaneously allowing the molten metal to cool gradually, ensuring optimal strength and minimizing distortion. SMAW is a versatile welding process that uses an electric arc between a coated electrode and base metal to create strong and durable welds.
Its effectiveness stems from the flux coating on the electrode, which not only shields the weld pool but also deoxidizes impurities within the base material. SMAW is started using a suitable power source by striking an arc through electrical contact or scratch-starting techniques.
This process generates intense heat that melts both the electrode's filler material and base metal while creating a protective shield through vaporizing flux coatings. With its long history of usage and continued relevance in various industries, SMAW remains an indispensable technique for welding applications worldwide.
Development in 19th-Century
Shielded metal arc welding has a rich history of welding techniques dating back to the 19th century. Its development is attributed to several key figures who contributed significantly during this time.
One such individual was Sir Humphry Davy, an English chemist who 1800 invented the concept of electric arc welding. Although Davy's initial experiments were primarily focused on using arcs for lighting, his work laid the foundation for future advancements in welding techniques.
As the 19th century progressed, other inventors built upon Davy's discoveries. Notably, Auguste de Méritens and Nikolay Benardos developed a carbon arc welding method that used a carbon electrode, which produced the intense heat necessary for joining metals together.
This breakthrough led to further exploration into arc-based welding techniques and set the stage for Shielded Metal Arc Welding as we know it today. It wasn't until around 1881 that another pivotal moment occurred in the development of SMAW.
The Russian inventor N.G. Slavyanov patented an electrode holder design that allowed for better control over both current and electrode movement during welding processes. This innovative device paved the way for more precise and efficient metal joining applications.
The early usage of SMAW primarily revolved around repairing cast iron products such as machinery parts or agricultural equipment. The simplicity and versatility of SMAW made it an ideal choice for these applications during this period.
However, it is important to note that SMAW was not without its challenges at this stage; electrodes used back then lacked flux coatings, resulting in poor weld quality due to increased oxidation levels. Despite these initial setbacks, improvements continued throughout the late 19th century with advancements in flux technology and electrode designs.
These developments played a crucial role in enhancing weld quality and expanding SMAW's applications, including steel structures, pipelines, and shipbuilding. The 19th century saw significant milestones in developing and using shielded metal arc welding early.
From Davy's invention of electric arc welding to Slavyanov's electrode holder patent, these innovators laid the groundwork for future advancements. SMAW found its initial application in repairing cast iron products, but gradually expanded to encompass various industries because of continuous improvements in electrode designs and flux technology.
Equipment and Materials Required for SMAW
Welding Machine
The primary equipment needed for shielded metal arc welding is a welding machine, also known as a welding power source.
This machine provides the electrical current to create an arc between the electrode and the workpiece, enabling the joining of metals. The welding machine must be capable of generating direct current (DC) to perform SMAW effectively. The machine often includes various components, including a transformer, rectifier, and control panel.
Electrodes
Electrodes play a vital role in SMAW, as they serve as filler metal and a flux source. These consumable rods are made from a core wire coated with flux material that releases gas and slag during welding to protect the molten weld pool from atmospheric contamination.
Electrodes come in different types based on their composition, such as low carbon steel, stainless steel, or alloys like cast iron or nickel-based materials. Each type has specific characteristics suitable for different applications.
Welding Cables
Welding cables are essential for securely connecting the welding machine to the electrode holder, clamp, and workpiece.
They carry electric current from the power source to facilitate the arc formation and passage through the electrode to create heat for melting metals together during welding operations. These cables must have good flexibility, insulation properties to prevent electric shocks or short circuits, and sufficient current-carrying capacity based on the specific requirements of each job.
Personal Protective Equipment (PPE)
Safety is paramount in SMAW because of potential hazards such as intense heat, ultraviolet radiation, sparks, fumes, and flying debris.
Therefore, appropriate personal protective equipment (PPE) is crucial during welding operations. PPE includes a variety of items such as flame-resistant clothing (welding gloves, jacket), safety glasses with side shields or goggles designed specifically for welding protection against harmful light emissions), respiratory protection (like a welding mask or respirator), and ear protection to safeguard against noise generated during welding.
Various Tools and Accessories
Several tools and accessories are necessary to carry out SMAW efficiently.
These include an electrode holder or stinger, which clamps onto the electrode and lets the welder control its position during welding. A ground clamp secures the workpiece, establishing a proper electrical circuit for the current flow.
Additional tools may include:
- Wire brushes for cleaning welds.
- Chipping hammers for removing slag.
- Pliers for handling hot materials.
- Measuring instruments like calipers or gauges to ensure accuracy in weld dimensions
Using these essential components effectively while adhering to proper safety precautions, welders execute SMAW with precision and reliability in various applications across different industries.
SMAW Welding Step by Step
Workpiece Prep
Before beginning the SMAW process, it is crucial to prepare the workpiece properly. First, ensure that the metal surfaces to be joined are clean and free from contaminants such as rust, paint, or oil. Using a wire brush or grinder to remove unwanted materials ensures thorough cleaning. It is important to ensure that the edges of the workpiece are properly beveled or chamfered if necessary.
This preparation ensures optimal welding conditions and helps achieve strong and durable welds.
Selecting Electrodes
The second step in the SMAW process involves selecting appropriate electrodes for welding. Electrodes play a vital role in SMAW because they provide the filler metal and shielding gas required to create a strong bond between the workpieces.
The type of electrode chosen depends on factors such as the base metal being welded, desired weld characteristics, and environmental conditions. For instance, low hydrogen electrodes are commonly used when welding steels with high tensile strength to minimize hydrogen-induced cracking.
Cellulose-based electrodes are suitable for vertical down welding because of their fast-freezing slag.
Power Source
After selecting suitable electrodes, it is essential to correctly set up the power source for SMAW welding, which includes connecting cables, ensuring proper grounding, and adjusting amperage settings according to electrode size and material thickness.
The power source should provide a stable arc with sufficient heat input for proper fusion while avoiding excessive heat that could lead to distortion or burn-through.
Executing Welding Technique:
Once all preparations are complete, it is time to execute the actual SMAW process by striking an arc between the electrode tip and the workpiece surface. The arc starts when an electric current passes through the electrode's core wire onto its coated tip, known as flux.
As this arc is established, the electrode's flux coating melts, forming a protective gas shield around the weld area. The welder then moves the electrode along the joint in a controlled manner to deposit molten metal onto the workpiece, creating a bead.
Maintaining a consistent arc length and travel speed during this process is crucial for uniform penetration and proper fusion. These step-by-step procedures in shielded metal arc welding achieve high-quality welds with excellent integrity and strength.
Adequate preparation of the workpiece, careful selection of electrodes, proper setup of power source, and precise execution of welding technique all contribute to successful SMAW welding. Mastering these steps takes practice, but SMAW is a versatile and reliable method for joining metals across various industries and applications once learned.
SMAW Welding Advantages
One of the key advantages of SMAW is its versatility. SMAW applies to various materials, including carbon steel, stainless steel, cast iron, and various alloys—an invaluable technique for welders working in different industries. Whether for construction, automotive, or manufacturing purposes, SMAW tackles several welding projects.
Another advantage lies in the simplicity and affordability of SMAW equipment. SMAW uses relatively simple and portable equipment compared to other welding methods that require complex machinery and specialized tools.
A basic setup includes the power source (welding machine), electrode holder or stinger, cables, and clamps. This accessibility makes SMAW an attractive choice for small workshops or remote locations where more sophisticated welding setups may not work.
SMAW advantages also include:
- The ability to produce high-quality welds with strong mechanical properties. The welder's manual control allows precise manipulation of arc length, travel speed, and deposition rate, resulting in well-formed beads and minimal distortion.
- Versatile Electrodes: available in various compositions with different characteristics, such as tensile strength, crack resistance, and corrosion resistance. This versatility allows welders to select electrodes based on specific project requirements.
- Excellent adaptability to adverse conditions, such as windy environments or restricted access areas. Unlike other welding methods sensitive to wind drafts or requiring extensive preparation before use, SMAW can be performed outdoors or in challenging work environments without compromising its effectiveness.
The flux coating on the electrode acts as a shield against atmospheric contamination while providing stability to the arc, even in unfavorable conditions. Shielded metal arc welding boasts several advantages, contributing to its enduring popularity among welders worldwide.
Its versatility enables it to be applied across different materials and industries; its simplicity and affordability make it accessible to a wide range of welders; its ability to produce high-quality welds allows for strong mechanical properties and adaptability to various project requirements; and its resilience in adverse conditions ensures consistent performance in challenging environments. These advantages combined make SMAW a reliable and trusted welding technique for diverse applications.
SMAW Welding Disadvantages
The disadvantages of Shielded Metal Arc Welding (SMAW) are worth considering, as they influence the decision-making process when choosing a welding method for a specific project. While SMAW has many advantages, it has a few limitations that may affect its suitability in certain scenarios. This section will delve into the drawbacks of SMAW welding, highlighting four key areas of concern.
One notable disadvantage of SMAW welding is its relatively low deposition rate compared to other welding processes—meaning the speed at which metal is added during the welding is slower when using SMAW.
The manual nature of this technique, combined with the need for frequent electrode changing and restarting because of the short length of consumable electrodes, contributes to a slower overall production rate, which is a drawback when time is critical or when dealing with large-scale projects where higher productivity is desired.
Another limitation of SMAW is its relatively high skill level required to consistently achieve high-quality welds. The manual operation causes precise control over various factors, such as electrode angle, arc length, and travel speed.
The welder must possess excellent hand-eye coordination and experience to ensure proper penetration and fusion without defects, such as porosity or undercutting. Inexperienced welders may find it challenging to produce satisfactory results consistently, causing extensive training and practice.
Excess Spatter
SMAW typically generates more spatter than other welding methods, such as Gas Metal Arc Welding (GMAW). Spatter refers to tiny droplets of molten metal expelled during welding and lands on surrounding surfaces or equipment, causing damage or creating safety hazards if not managed effectively.
While spatter can be minimized by carefully adjusting parameters such as current settings and electrode manipulation techniques, SMAW remains an inherent aspect that requires additional post-weld cleanup efforts. Another disadvantage lies in the restrictions imposed by SMAW's limited positional capability.
SMAW is primarily suitable for flat or horizontal welds because of the welding process. Welding in vertical or overhead positions is more challenging because of the increased likelihood of slag falling and insufficient penetration.
In such cases, alternative welding methods, such as Flux-Cored Arc Welding (FCAW) or Gas Tungsten Arc Welding (GTAW), offer better control and adaptability in various positions. While SMAW possesses many advantages, it is important to acknowledge its limitations.
These include a slower deposition rate, the need for skilled welders, increased spatter generation, and limited positional capability. Understanding these disadvantages allows for more informed decisions when selecting a welding method that aligns with the specific requirements of a project.
Denique
Shielded metal arc welding (SMAW) is a time-tested and versatile welding process that has been in use for well over a century. Throughout its history, SMAW has continuously evolved and adapted to meet the changing needs of various industries.
From its early days as a rudimentary method employed by blacksmiths, it has transformed into a sophisticated welding technique used in construction, fabrication, and maintenance work. SMAW offers several advantages, making it an appealing choice for welders.
Its simplicity and portability make it accessible even in remote locations or areas with limited infrastructure. The ability to use SMAW on various metals, including steel, stainless steel, cast iron, and non-ferrous materials, further enhances its versatility.
The low equipment cost makes it an attractive option for small-scale welding projects. However, like any welding technique, SMAW also has its fair share of disadvantages.
The process itself can be slow compared to other modern methods, such as Gas Metal Arc Welding (GMAW). If improperly managed, the high heat generated during SMAW causes distortion or warping of the welded material.
With ongoing advancements to improve efficiency and overcome some of its limitations, such as speed and heat management, SMAW is poised to remain a steadfast and trusted option for welders across various industries. Embracing the tradition of SMAW while welcoming the innovation of newer methods will undoubtedly lead to a future where welding is an even more precise and efficient practice.