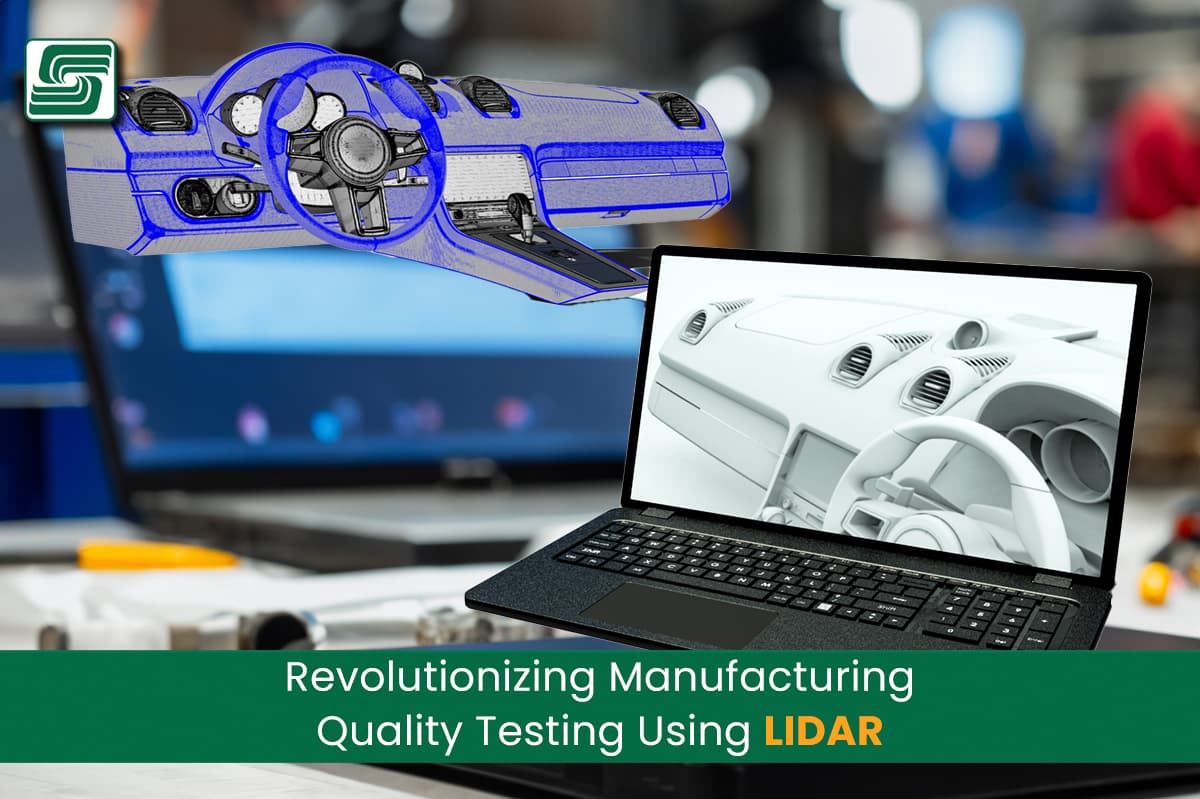
Technology has significantly revolutionized how industries function, particularly in manufacturing, where it has emerged as a top contender in refining manufacturing processes.
This innovative technology, which has its roots in meteorology and space exploration, is now playing an increasingly pivotal role in several sectors, including automotive, aerospace, construction, and, notably, in quality testing within manufacturing.
Quality control is critical in any production process; efficiently identifying defects saves corporations from substantial financial loss and reputation damage. Traditionally, these quality checks were performed manually, making ample room for human error.
Incorporating LIDAR technology into industrial processes, precision, and accuracy have been significantly improved while expediting the entire procedure. The magic happens when lasers measure distances or speeds or make digital 3D representations of target objects.
This incredible detail provides manufacturers with detailed insights into their products' structural integrity during various stages of the production process with unparalleled precision.
Not only does this help early detection of defects, but it also aids decision-making regarding improvements needed to enhance product performance.
LIDAR Basics
LIDAR, Light Detection and Ranging, is a remote sensing method that uses light—as a pulsed laser—to measure distances. This technology was conceived in the mid-20th century, concurrently with the laser. It has since escalated in prominence because of its pivotal role in various scientific and industrial applications. It relies on illuminating targets with a laser and analyzing the reflected light to find precise geometric information about objects or environments.
LIDAR operates like radar but employs light waves from a laser instead of radio waves. It emits bursts of infrared lasers—up to one million pulses per second—that bounce off exposed surfaces.
A sensor on the LIDAR instrument then measures how long it takes each pulse to return, producing millions of data points or "returns." The fundamental principle here is that distance is calculated using simple physics by knowing the speed of light and calculating how long it takes for each light pulse to return after hitting an object. LIDAR is now a potent tool for swiftly collecting highly accurate spatial data in manufacturing settings.
Its physical characteristics make it adept at penetrating semi-transparent substances like smoke or dust, common in many industrial environments. LIDAR's non-contact measurement capabilities allow manufacturers to quickly gain accurate data from complex surfaces at safe distances.
LIDAR's remarkable precision in capturing even the tiniest details not discernible to the naked eye and its swift data collection capability are two standout features that significantly enhance the quality assurance measures.
Mastery of these fundamental aspects aids in realizing why industries are increasingly leveraging advancements in remote sensing technology, such as LIDAR, for their quality control needs.
Its distinct advantages over conventional methods in terms of accuracy, speed, safety, and ability to operate in challenging environments align seamlessly with the evolving demands of contemporary industrial landscapes.
How LIDAR Works in Manufacturing
LIDAR technology offers non-contact measurement capabilities, enabling manufacturers to inspect parts without physically touching them or causing potential damage.
This hands-off approach is beneficial when dealing with sensitive materials or intricate geometries that may be easily affected by contact-based measuring methods.
Manufacturers use LIDAR for spatial analysis within their factories, helping them improve layout planning by creating accurate 3D maps of their facilities. Details illustrated from the maps allow for more efficient use of space and increased productivity.
LIDAR helps optimize product assembly lines by capturing high-resolution 3D images that detect anomalies or discrepancies in manufactured parts.
In quality testing, manufacturers use LIDAR as part of an integrated approach with advanced software algorithms to automatically pinpoint defects in products or components as they move along production lines.
Given its ability to accurately measure slight variations in distance down to micrometers level detail over sizable areas, it verifies dimensions against original design specifications with high precision, ensuring stringent adherence to quality standards.
The speed at which these measurements are carried out is another distinctive characteristic that makes this technology effective for quality testing applications. A few million points per second are sampled, allowing rapid inspection speeds compatible with modern production line rates. This speed facilitates real-time feedback loops between production processes and quality assurance, allowing immediate corrections.
LIDAR for Quality Testing
LIDAR offers a panoptic view of the manufacturing landscape. It expedites identifying flaws and defects in an assembly line, enhancing efficiency and productivity.
LIDAR allows precise measurements of complicated geometrical shapes by harnessing light's properties. Its laser beams bounce off surfaces and return to the sensor, enabling it to accurately map out the physical attributes of a product.
Applying LIDAR in quality testing provides an unprecedented perspective harnessed to enhance product accuracy. The digital twin generated from the LIDAR data is a virtual mirror image of the manufacturing process, capturing nuances that might escape traditional testing methods.
Manufacturers scrutinize this virtual model at any production stage to identify potential errors or inconsistencies. The advantages conferred by employing LIDAR technology are manifold; its precision and speed are chief among these.
Unlike manual measurements or older automated systems that require contacting the object under inspection, LIDAR tests without physical contact using high-speed lasers. This non-intrusive method ensures zero damage or alteration to delicate products while conducting tests.
It lends itself well to tackling bulk tasks effortlessly; regardless of complexity or size variations in manufactured objects, it consistently detects irregularities before they become costly mistakes. Thus, it eliminates issues like product recalls because of undetected faults during production, impacting revenue and brand reputation.
Yet another feather in LIDAR's cap is its compatibility with varied environments and materials—from glassy surfaces that reflect lights unabashedly to dark corners where visibility struggles; from smooth planes where light glides easily to uneven areas where it stumbles unpredictably; LIDAR easily handles them all with aplomb. It gauges distances between objects irrespective of their material composition - metal or plastic, opaque or transparent—delivering accurate readings every time.
LIDAR technology for quality testing redefines the manufacturing dynamic by reducing error margins, improving accuracy, and optimizing resource usage. It underscores the adage that prevention is better than cure—a fundamental principle forming the bedrock of manufacturing quality testing.
Benefits of Implementing LIDAR
Incorporating LIDAR technology into the manufacturing industry heralds many advantages that can optimize and streamline processes. It creates an environment where precision, accuracy, and speed are paramount.
LIDAR's light pulses, combined with other data recorded by the equipment, generate precise three-dimensional information about the shape and surface characteristics of the target object.
One such advantage is accuracy. LIDAR captures hundreds of thousands of data points per second with remarkable fidelity, providing highly accurate measurements.
This high level of precision is critical in manufacturing environments where even tiny discrepancies lead to significant problems down the line. With LIDAR technology, manufacturers ensure their products meet stringent quality standards.
Another significant benefit offered by LIDAR is speed. Traditional methods for quality testing often require manual efforts, which is time-consuming and less efficient.
LIDAR allows rapid data acquisition and analysis; it scans objects while maintaining a high resolution. The efficiency gains save valuable time and contribute to cost reductions in the long run, as there's less need for rework or corrective measures because of incorrect measurements.
Using LIDAR for quality testing adds another layer of reliability because it is non-contact technology—meaning it doesn't physically touch what it's measuring—thus eliminating potential damage or alteration to delicate parts during inspection processes. Beyond these tangible benefits, there's also an important intangible: peace of mind from knowing your product's quality has been thoroughly vetted using state-of-the-art technology that leaves no room for doubt or approximation.
Quality Testing Challenges
Implementing LIDAR technology in manufacturing processes for quality testing poses unique challenges. One of the primary concerns is the high initial investment cost required to install and implement this novel technology.
Small and medium enterprises (SMEs) may find it particularly daunting as they weigh the benefits against the steep financial commitment. However, it is important to consider that despite its high upfront costs, LIDAR saves significant resources in the long run by reducing waste, increasing efficiency, and ensuring consistent product quality.
Another challenge lies in integrating LIDAR technology with existing systems within a manufacturing environment. Many manufacturing facilities operate with established machinery and processes that have existed for years; introducing new technology into these systems requires careful planning and execution to avoid disruption.
Retrofitting existing equipment with LIDAR sensors is a complex task requiring significant technical expertise. In addition, there are also challenges related to data management associated with LIDAR usage.
Since this technology produces extensive detailed 3D mapping data, managing this massive amount of information becomes crucial. Companies must invest in robust data storage solutions and skilled personnel who analyze this complex data for quality assurance.
Training staff to properly use and maintain LIDAR equipment presents another hurdle for many organizations. To fully benefit from this advanced tool's capabilities, employees need detailed instructions on operating it correctly and safely, which may involve additional time and resources.
Despite these challenges, it's impossible not to recognize the immense potential of using LIDAR tech in quality testing within manufacturing scenarios. By carefully navigating these issues, industries revolutionize their production through enhanced accuracy, faster process times, and improved product output quality.
LIDAR vs. Other Quality Testing Methods
LIDAR is a unique quality testing method that stands out for its precision and reliability. However, to fully understand its effectiveness, comparing it with other commonly used technologies in the same field is important. Traditional quality testing methods typically involve either tactile probing or laser scanning. These instruments capture data points on an object's surface but frequently require physical contact during operation. These manual tasks restrict their utility in speed and versatility - key limitations that LIDAR efficiently circumvents.
While accurate to a certain degree, tactile probing causes direct contact with the object under scrutiny. Direct contact may lead to deformation or damage to the product, especially when dealing with delicate materials or intricate designs.
Laser scanning shares some similarities with LIDAR but suffers from slower data acquisition rates because of the need for multiple passes over an area for optimal data collection. When juxtaposed against these traditional techniques, LIDAR is a superior solution in several ways.
First, it operates based on the time-of-flight principle, which measures distance by calculating the time taken by light pulses emitted from the device to reach an object and return after reflection - eliminating any requirement for physical contact with objects under examination. Zero contact prevents potential damage and allows for much quicker scans.
Unlike other methods that might struggle in contrasting lighting conditions or encounter difficulties capturing details on dark or reflective surfaces, LIDAR maintains consistent performance irrespective of such variables because it uses infrared light beams, which are indifferent towards color variations or ambient light levels. It should be noted, though, that while each quality testing method has its unique advantages and disadvantages, ultimately, their selection would hinge on myriad factors, such as product complexity, budgetary constraints, and scale of operation, among others.
While tactile probing may still find relevance in some specific applications requiring ultra-high precision over smaller areas, the wide-ranging versatility coupled with rapid data acquisition capabilities makes LIDAR an increasingly attractive proposition for a considerable manufacturing industry segment.
However, while LIDAR technology significantly enhances the scope and reliability of quality testing methodologies, its optimal application is contingent upon understanding its strengths and limitations vis-à-vis other systems and tailoring its usage to best align with the specific demands of each manufacturing scenario.
Future Trends in LIDAR Technology
Looking to the future, LIDAR technology will experience significant growth and evolution. The future of LIDAR in manufacturing, particularly in quality testing, is teeming with potential.
A key trend to watch will be the miniaturization of LIDAR systems. This process involves reducing the size of LIDAR hardware without compromising its overall performance and functionality.
Miniaturization will make LIDAR systems more affordable and easier to incorporate into manufacturing processes, including quality testing procedures. Another noteworthy development involves solid-state LIDAR systems.
Unlike mechanical variants that require moving parts for scanning or steering lasers, solid-state iterations function without moving components, thus improving reliability and decreasing production costs. A solid-state system offers a robust framework for high-resolution spatial data acquisition useful in precision-focused activities like quality testing.
AI-integrated LIDAR systems are emerging as a revolutionary trend shaping the future manufacturing quality testing landscape. Incorporating artificial intelligence optimizes data analysis processes within these systems by rapidly identifying defects or inconsistencies that may get overlooked during manual inspection procedures.
Simultaneously, these advancements are expected to facilitate real-time feedback loops during production runs—an invaluable asset for time-sensitive industries requiring immediate rectification measures or adjustments during operation cycles. As for software trends accompanying this hardware evolution, open-source platforms are gaining momentum as enablers for wider accessibility and customization possibilities offered by LIDAR tech's versatility in data collection and processing tasks.
Amidst these rapid advancements in efficiency and efficacy lies an often-overlooked attribute: sustainability considerations within manufacturing technology innovations. Strides are being taken towards developing energy-efficient LIDAI components that contribute to reduced carbon footprints - a necessary and timely development given our heightened global emphasis on sustainable practices across all sectors.
Manufacturing is on the cusp of an exciting era because of advances to significantly alter our traditional manufacturing landscapes. Bolstered by ongoing research and development efforts, the future trajectory of LIDAR technology within the quality testing circuit is poised to be one characterized by continual innovation, escalating efficiency levels, and a steadfast commitment to sustainable practices.
In Sum
Promptly detecting errors mitigates the likelihood of faulty products reaching consumers, bolstering customer satisfaction and brand reputation. The comparative efficiency and accuracy of LIDAR to other methods advocate for its increasing adoption within varied industries.
Its growing prominence is reflected in its expanding reach beyond traditional sectors such as automotive and aerospace, including consumer electronics and healthcare. Given the benefits it can confer upon manufacturing processes regarding reliability and efficiency, LIDAR's integration appears to be a strategic move towards future-proofing operations.
Notwithstanding the challenges associated with cost and technological complexities, there is reason to remain confident about LIDAR's wider acceptance across industries. As technological advancements continue rapidly, easing these concerns may soon be within reach.