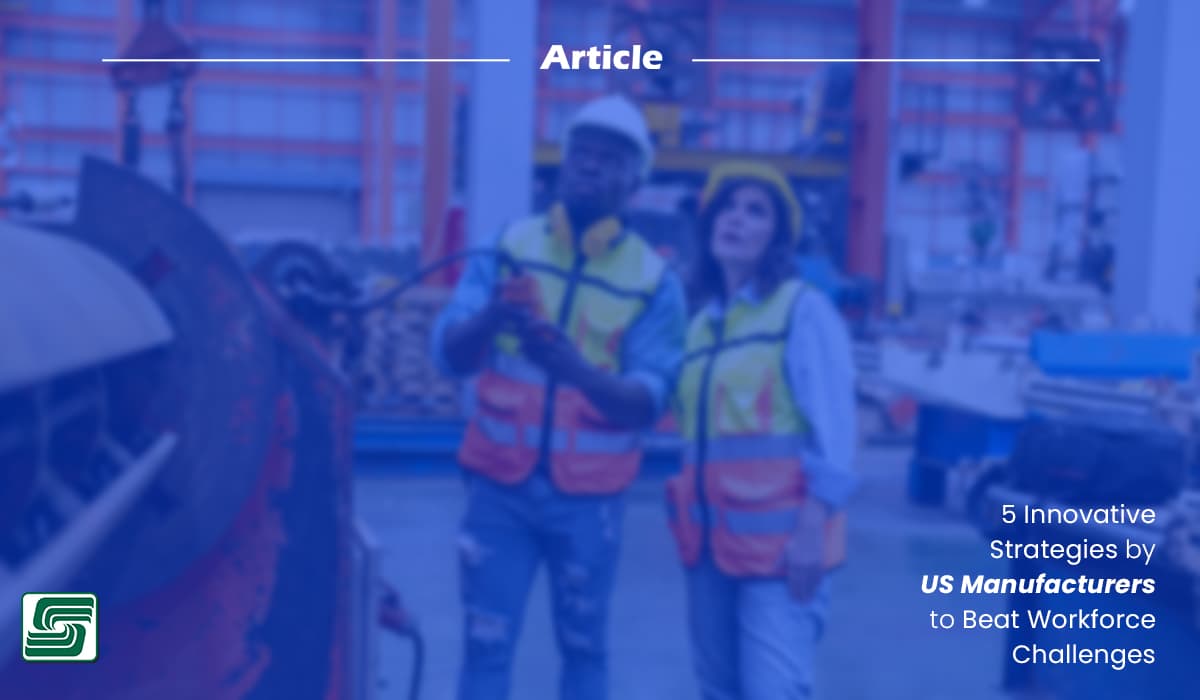
The United States manufacturing companies sector faces significant workforce challenges, with a projected need for 3.8 million new employees between 2024 and 2033. Failure to bridge the skills and applicant gap could leave 1.9 million jobs unfilled.
US manufacturing companies are using innovative strategies to combat this issue—here are five next-gen approaches.
Fostering a Positive Workplace Culture
A positive workplace culture is crucial for US manufacturing companies. This approach is vital for talent attraction and retention, ensuring company growth.
Importance of Workplace Culture
- Attracting Top Talent: Creating a vibrant workplace culture entices skilled individuals and keeps them within the organization. Manufacturing companies attract top-tier professionals by creating a supportive and inclusive environment where their contributions are valued and appreciated.
- Keeping Existing Employees: A positive workplace culture is crucial for retaining employees. Employees who feel valued and connected are likelier to stay loyal. Loyalty leads to higher productivity and lower turnover, benefiting the organization.
Investing in Training and Development
Skill Enhancement Programs
- On-the-Job Training: On-the-job training is essential for skill enhancement programs. The program allows employees to gain practical experience. Immersive learning efficiently enhances skill proficiency and fosters a deeper understanding of job responsibilities.
- Continuous Learning Opportunities: Continuous learning is vital for employee growth in manufacturing companies. Organizations use training sessions, workshops, and online resources to stay updated on industry trends and technological advancements. Continuous learning enhances both individual skills and company growth.
Benefits of Training Investments
- Increased Productivity: Employee training leads to significant productivity gains. Well-trained employees display higher efficiency, reduced errors, and improved output quality. Manufacturing companies improve productivity by training staff.
- Employee Satisfaction: Investing in training boosts employee satisfaction. Customized training values employees and boosts engagement. Recognition leads to a positive work environment, higher motivation, job satisfaction, and morale.
US manufacturing companies address these workforce challenges by prioritizing skill enhancement programs and continuous learning opportunities.
Embracing Technology: Automation and Robotics
- Reducing Manual Labor: Automation and robotics replace manual tasks in manufacturing. Companies use advanced technologies to streamline production lines and reduce reliance on manpower.
- Increasing Efficiency: Integrating automation and robotics boosts manufacturing efficiency. These technologies enhance workflow, reduce errors, and expedite production. Companies meet consumer demands promptly and maintain high-quality standards.
Digital Transformation
-
Smart Manufacturing: Digital transformation modernizes manufacturing practices with smart technology integration. Interconnected systems, real-time data analytics, and seamless coordination enhance manufacturers’ productivity.
- Data-Driven Decision-Making: Digital transformation enables data-driven decision-making for manufacturers. Advanced analytics tools help companies assess performance, identify areas for improvement, and respond to market trends. Data-driven planning promotes sustainable growth in manufacturing.
Providing Flexible Work Arrangements
Remote work allows employees to work from outside the office.
- Remote Work: Flexibility allows individuals to efficiently manage tasks and personal commitments. Remote-friendly companies value diverse work styles and work-life integration.
- Flexible Hours: Introducing flexible hours enables employees to customize their work schedules. This approach fosters a sense of control over professional and personal obligations.
Flexible work hours improves employee happiness and motivation, increasing employee involvement and overall company performance.
Impact on Workforce
- Work-Life Balance: Prioritizing work-life balance with flexibility is crucial for employee well-being. Companies promote work-life balance by offering flexible schedules. Striking this balance improves mental health and work performance.
- Employee Retention: Flexible work arrangements boost employee retention rates by valuing individual needs. Trust and empowerment lead to employee loyalty. Better retention rates lead to reduced turnover costs, increased operational continuity, and a stronger team commitment.
US manufacturing companies cultivate a positive workplace culture to attract and nurture top talent for long-term success.
Collaborating with Educational Institutions
Partnerships with Schools and Colleges
Manufacturers actively partner with educational institutions to bridge the skills gap and cultivate a robust talent pool. These collaborations extend beyond traditional recruitment methods, focusing on fostering meaningful relationships that benefit students and companies alike.
- Internship Programs: Internship programs provide hands-on manufacturing experience for students. Manufacturers offer internships to schools and colleges, providing students with practical industry insights and identifying future talents.
- Apprenticeships: Apprenticeships are vital for nurturing skilled professionals in manufacturing. Through training and mentorship, apprentices develop specialized knowledge and skills. This approach prepares individuals for specific roles and eases their entry into the workforce after completing the apprenticeship.
Long-Term Benefits
Collaborating with educational institutions benefits manufacturers and students in the long run, shaping the industry’s future.
- Workforce Pipeline: Creating partnerships with educational institutions ensures a consistent supply of skilled workers for the manufacturing industry. Engaging earlier with educational institutions allows manufacturers to shape curricula and produce skilled graduates.
- Industry-Academia Collaboration: Collaboration between industry and academia promotes innovation and knowledge exchange. These partnerships advance technology, processes, and skills by sharing resources, research, and best practices. This approach benefits students and manufacturers alike.
In Sum
US manufacturers must continuously innovate to stay competitive, grow, and satisfy customers. Embracing technology and fostering innovation improves workplace efficiency, quality, and safety.
The future of US manufacturing depends on adopting next-gen strategies to address workforce challenges. Continuous improvement and forward-thinking initiatives help manufacturers thrive in a changing landscape.