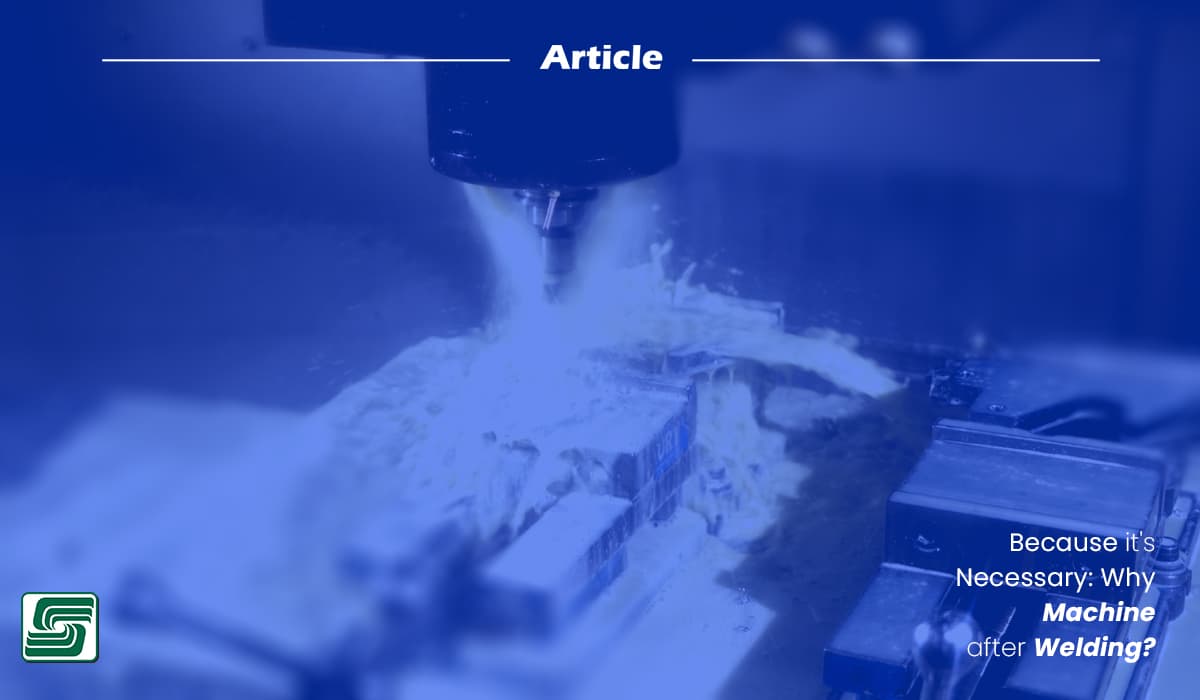
Machining plays an important role in the welding process. Precise fit and functionality remain important for any manufacturing project, and machining ensures that components meet exact specifications.
Important factors include correcting distortions and achieving tight tolerances. Eliminating residual stresses is also important. Machining contributes to the overall quality and reliability of the final product.
Understanding the importance of machining helps in achieving superior results. Precision and accuracy are important in the manufacturing industry.
The Importance of Machining in Welding Projects
Machining involves removing material from a workpiece to achieve a desired shape or finish. This process uses tools like lathes, mills, and drills to ensure dimensions and surface quality precision.
Various industries rely on machining to create components that meet exact specifications.
Why is it Necessary After Welding?
Welding introduces distortions and residual stresses in materials. Machining corrects these issues by refining the welded parts.
Post-weld machining restores dimensional accuracy and enhances component fit. This step is crucial for achieving tight tolerances in the final product.
Machining after welding ensures the reliability and functionality of assemblies.
Historical Context
The evolution of machining techniques has transformed the manufacturing landscape. Early machining relied on manual operations with basic tools.
Introducing CNC machining marked a significant advancement. CNC technology automates the machining process through computerized control, allowing for precision and speed in executing complex designs.
Industrial automation further simplified production processes. Automation improved material handling, assembly, and finishing tasks.
Impact on Modern Manufacturing
Modern manufacturing benefits from advanced machining technologies. Precision machining technology plays a vital role in industries like aerospace and automotive, which demand parts with exact measurements and high-quality finishes. Machining ensures that components meet stringent industry standards.
Integrating CNC and automation enhances efficiency in the manufacturing process. These advancements contribute to the production of reliable and precise products.
Challenges in Machining After Welding
Material distortion occurs because of the expansion and contraction of weld metal and adjacent base metal during the heating and cooling cycle. The welding process introduces heat, causing the metal to expand.
As the metal cools, it contracts, leading to distortion. The metal's physical and mechanical properties change with heat application.
These changes significantly influence shrinkage and distortion. Alternating welds from one side to the other reduces distortion compared to welding on one side only.
Mitigation Strategies
Several strategies exist to mitigate material distortion in welded components:
- Balanced Welding: Alternate welds from one side to another to balance the forces acting on the metal.
- Preheating: Apply heat to the metal before welding to reduce temperature gradients.
- Clamping: Use clamps to hold parts in place during welding, minimizing movement.
- Backstep Welding: Employ a technique where welding progresses opposite to the overall weld progression.
Implementing these strategies helps maintain welded parts' structural integrity and dimensional accuracy.
Heat-Affected Zones
The heat-affected zone (HAZ) is the area of the base metal that has not melted but has undergone microstructural changes because of the heat from welding.
The HAZ experiences alterations in mechanical properties, affecting the welded component performance.
The extent of the HAZ depends on factors like welding speed, heat input, and material type.
Techniques to Minimize Effects
Minimizing the effects of heat-affected zones involves several techniques:
- Controlled Cooling: Manage the cooling rate to prevent excessive hardening or softening.
- Post-Weld Heat Treatment: Apply heat treatment after welding to relieve stresses and restore mechanical properties.
- Proper Welding Parameters: Adjust welding speed and heat input to control the size of the HAZ.
- Material Selection: Choose materials with suitable thermal properties to withstand welding heat.
These techniques ensure the welded components keep their desired properties and functionality.
Specific Methodologies for Machining
CNC Machining Advantages
CNC machining offers significant benefits in the manufacturing industry. This technology provides high precision and repeatability, ensuring each part meets specifications.
Automated systems in CNC machines enhance productivity by reducing human error. Industries like aerospace and automotive rely on CNC machining to produce parts with consistent quality.
The process allows for complex geometries that manual methods cannot achieve. CNC machines also improve efficiency by minimizing downtime and maximizing output.
CNC's Role in Welding Applications
CNC machining is crucial in welding applications. The process corrects distortions caused by welding, ensuring parts fit accurately.
CNC machines handle intricate designs required in welded assemblies. The technology maintains tight tolerances essential for product reliability.
Manufacturers use CNC machining to refine welded parts, enhancing overall quality. The process supports various industries by delivering the precise components necessary for complex assemblies.
Manual Machining Techniques
Despite technological advancements, manual machining remains valuable in certain scenarios. Operators use manual machines for small-scale projects or when flexibility is needed.
Skilled machinists perform tasks requiring a personal touch or adjustments during the process. Manual machining suits situations where setup time for CNC machines is impractical.
The technique benefits projects with unique or one-off parts that do not justify automated processes.
What are the Pros and Cons of Manual Machining?
Manual machining has distinct advantages and disadvantages. Skilled operators produce high-quality parts with attention to detail. The process allows for immediate adjustments, offering flexibility in production.
However, manual machining requires significant skill and experience to achieve desired results. It is slower and less precise than CNC machining.
Manual methods may lead to inconsistencies in parts, affecting overall product quality.
Despite these challenges, manual machining remains a valuable tool for specific applications.
Tolerance and Precision in Machining
Tolerance, which refers to the permissible limit of variation in a physical dimension, is crucial in welding and machining.
Engineers consider tolerance an essential element for evaluating manufacturing quality. Tolerance impacts the structural integrity and functionality of the final product.
The aerospace industry relies on tight tolerances to maintain safety and performance standards. Welding introduces distortions that affect tolerance levels.
Machining corrects these distortions to ensure components meet engineering tolerances.
Methods to Ensure Precision
Manufacturers employ various methods to ensure precision in machining. CNC machining offers high accuracy by automating the cutting process.
Skilled machinists use manual techniques for projects requiring flexibility. Quality control measures, such as inspections, verify that parts meet specified tolerances.
Advanced software helps designers create components with precise dimensions. Manufacturers use these methods to achieve tight fits in assemblies.
Precision machining ensures the reliability of the final product in demanding applications.
Role of Machining in Precision Projects
- Precision Welding in Aerospace Manufacturing: The aerospace sector demands components with exact measurements. Machining ensures parts fit perfectly within assemblies. Precision machining technology creates intricate geometries required for aircraft. The industry benefits from machining's ability to maintain tight tolerances. This precision contributes to the safety and performance of aircraft.
- The Essential Craft of Welding 2023's Industry Report: The report highlights the significance of welding in manufacturing. Precision-engineered components drive demand in various industries. Machining plays a vital role in achieving precision in welded parts. The process ensures components meet industry standards for quality and reliability.
Industry Applications
Machining finds applications in multiple industries requiring precision.
- Automotive: relies on machining to produce engine components.
- Medical: using machining to craft surgical instruments. These tight tolerances ensure the functionality and safety of medical devices.
- Construction: benefits from machining to create structural elements, supporting the production of reliable and durable infrastructure.
Cost Implications of Machining After Welding
- Equipment and Labor Costs: Machining after welding involves significant equipment costs. CNC machines and manual tools require substantial investment. The cost of acquiring and maintaining these machines impacts the overall budget. Labor costs also play a crucial role in machining expenses. Skilled machinists demand competitive wages because of their expertise. Training programs for machinists add to labor expenses. Companies must allocate resources for both equipment and skilled labor.
- Material Costs: Different metals and alloys come at various price points. Rare metals often incur higher material costs. Machining processes generate waste material, which affects overall expenses. Efficient material usage helps reduce waste and control costs. Companies must consider the type of metal used in manufacturing. Choosing cost-effective materials without compromising quality is essential.
Indirect Costs
- Downtime and Maintenance: Machining operations lead to downtime during maintenance. Regular upkeep of machines ensures optimal performance and maintenance schedules prevent unexpected breakdowns. Downtime affects production timelines and delivery schedules. Companies must plan for maintenance to minimize disruptions. Operating and maintenance expenses include consumables like welding wire and gas.
- Long-Term Financial Benefits: Investing in machining after welding offers long-term financial benefits. Precision machining enhances product quality and reliability. High-quality products reduce warranty claims and returns. Satisfied customers lead to repeat business and positive referrals. Machining ensures components meet industry standards, enhancing brand reputation. Companies benefit from reduced rework and scrap rates. Long-term savings outweigh initial investments in equipment and labor.
Types of Machining Equipment
Machining relies on various types of equipment to achieve precision.
- CNC Machining Automation stands out for its high precision and consistent quality. CNC machines efficiently perform complex cuts and shapes. Manual machines, though less precise, offer flexibility for unique tasks.
- Precision Machining Technology uses computer-controlled tools to create intricate geometries. This technology is essential in industries such as aerospace and automotive.
Choosing the Right Equipment
Selecting the equipment depends on the project's requirements.
- CNC Machining Automation suits large production runs needing precision. Manual machines fit small-scale projects where flexibility is crucial.
- Specialty Equipment may be necessary for specific industry needs.
Understanding the capabilities of each machine type helps make informed decisions. The right choice enhances productivity and ensures quality outcomes.
Technological Advancements
Recent innovations have transformed machining processes. Precision Machining Technology now allows for tighter tolerances.
High-velocity machining speeds up production without sacrificing quality. Computer-controlled tools enable the creation of complex parts.
These advancements contribute to the efficiency of manufacturing operations. Industries benefit from reduced waste and improved product reliability.
Future Trends
Future trends in machining focus on further automation and precision.
- MFI (Machining Future Innovations): aims to integrate AI into smarter operations.
- Enhanced Equipment: offers greater capabilities for intricate designs.
- Specialty Equipment: evolves to meet specific industry demands.
The focus remains on improving accuracy and reducing production time. These trends promise to revolutionize the manufacturing landscape.
Risk Management in Machining After Welding
Machining after welding presents several common risks. Material distortion occurs because of residual stresses.
Heat-affected zones may alter the mechanical properties of components. Equipment variability leads to inconsistencies in machining outcomes.
Improper tool and material handling poses safety hazards. Each risk affects the overall quality and functionality of the final product.
Risk Assessment Techniques
Risk management requires effective assessment techniques. Engineers evaluate the potential impact of each risk on the manufacturing process.
Tolerance levels help determine acceptable variations in dimensions. Regular inspections identify deviations from specified tolerances.
Monitoring equipment performance ensures consistent machining results. Comprehensive risk assessments guide decision-making in manufacturing operations.
What are Risk Mitigation Strategies?
- Implementing Safety Protocols: Safety protocols play a crucial role in risk management. Proper training equips operators with the skills to handle machinery safely. Protective gear reduces the risk of injury during machining operations. Clear guidelines outline the steps for safe equipment usage. Regular maintenance checks prevent unexpected equipment failures. Safety protocols enhance the overall safety of the manufacturing environment.
- Training and Skill Development: Training and skill development contribute to effective risk management. Skilled machinists understand the importance of maintaining tolerance levels. Continuous education keeps operators updated on the latest machining techniques. Hands-on training sessions improve proficiency in using advanced equipment. Skill development programs focus on minimizing errors during machining. Well-trained personnel ensure high-quality outcomes in manufacturing projects.
The Role of Powder Coating in Machining
Benefits of Powder Coating Benefits: Powder coating offers a durable, wear-resistant surface finish. This method provides a cost-effective solution for metal parts, increases longevity, and is resistant to harsh environments. The process uses powdered plastic material and chemical agents, adding a robust finish to metal parts. Powder coating resists wear and tear, like chipping and scratching, making it more effective than traditional paint.
Application Techniques: Proper application techniques ensure the effectiveness of powder coating. Maintaining excellent ground during the powder application process is crucial. This practice significantly improves the surface topography of coated parts. In-house facilities often handle the powder coating process. In-house manufacturing allows for better control over quality and consistency. Proper equipment and skilled personnel enhance the application process. In-house teams adjust techniques to meet specific project requirements.
Compatibility with Machined Parts
Ensuring adhesion is vital for powder coating compatibility with machined parts. The surface preparation process plays a key role in adhesion. Cleaning and degreasing remove contaminants that hinder adhesion.
In-house teams often perform these tasks to maintain quality control. Abrasive blasting or chemical etching creates a rough surface for better adhesion, and these facilities tailor these processes to specific materials.
Avoiding Common Issues
Avoiding common issues ensures the success of powder coating on machined parts. Poor adhesion leads to peeling or flaking.
In-house quality checks help identify potential problems early. Temperature control during curing prevents defects in the coating, and in-house expertise allows for adjustments in curing parameters.
Regular inspections ensure the coating meets industry standards. In-house manufacturing teams play a crucial role in maintaining quality throughout the process.
In Sum
Machining after welding is immensely important in manufacturing. This process ensures optimal fit and functionality by correcting distortions and achieving precise tolerances.
Machining enhances the quality of components, making them reliable for various applications, including the food and beverage industry.
Companies benefit from adopting best practices in machining to maintain high standards.