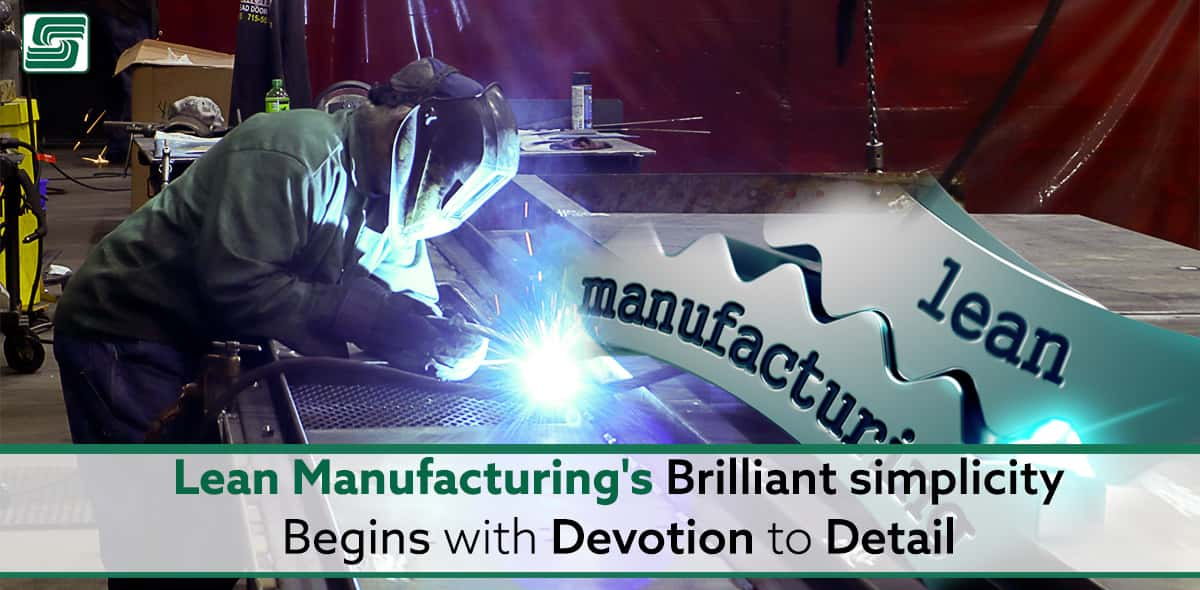
Lean manufacturing principles are rooted in common sense, but that doesn’t make them any less revolutionary. For decades, conventional business wisdom had been managing processes from beginning to end as one complete unit rather than breaking work into individual steps and reassembling the final product.
In other words, lean thinking suggests they should build a car from start to finish without having its parts reassembled after painting or installing seats and windows. The old approach was more of a supply chain management system, planning every step of production, leaving nothing to chance.
But there’s a catch-22. Any system cutting out all waste must be incredibly detailed — making it difficult for anyone to understand. That’s why many companies selectively implement lean principles rather than completely revamping their process.
Pressure on manufacturers to be efficient and eliminate waste continues to grow as the manufacturing industry competes in the global marketplace, especially in developed countries. For many organizations, applying Lean Integration methodologies to automation relieves the pressure by preventing mistakes, providing value for the customer, and allowing for the agility required to remain successful in a highly competitive environment.
Lean manufacturing has been used in the United States for over 20 years. Based on the methods Kiichiro Toyoda implemented in Japan, the concept of lean changed the focus from what the manufacturer wants to make to what the end-user prefers.
This is the first of two articles exploring aspects of lean integration in the manufacturing sector.
Benefits of Lean Integration Include:
Lower automation costs
- Better use of floor space
- Simpler implementation
- More flexibility for set and material flow
- Operator utilization maximized
- Provision of data for future solutions and continuous improvement.
Other integration approaches have been and still used. Most focus on the part of the problem or approach problems when they happen. Different integration strategies use customized hand-coded solutions, project-by-project, with no master plan. The results can be a patchwork of solutions that costs more to maintain; it's hard to change. It offers little to no flexibility—leaving an organization continually putting out fires and struggling to play catch-up to the shifts in the environment.
Lean integration is different. Lean organizations are agile. They can stay ahead of market shifts, the plethora of regulatory demands, and information technology (IT) complexity. Simply defined, lean integration is a data-driven methodology that uses metrics to ensure continuous quality and performance.
Lean methodology generates:
- Up to 90% reduction in project lead time
- A 50% gain in the integration of team productivity
- Significant and continuous improvements in project quality
- More cooperation across internal work teams
Element of Integration
Lean integration focuses on making independent applications work together in an ongoing interconnected system. The integration of technology solutions breaks down into two solution styles: Process Integration and Data Integration.
Lean integration is a repeatable, teachable, and agile science, enabling the organization to change rapidly without increasing risk or compromising on quality. Reusable components, enhanced data, metrics designed to drive continuous improvement, innovation facilitated by a fact-based approach, and an engaged IT staff are the glue that holds lean integration together.
Lean manufacturers produce more with fewer employees, less cost, and faster products to market—largely due to advances in computer-aided capabilities and communication technologies.
The result is less waste and a more streamlined production line, allowing long-term advantages for manufacturers. There are many useful tool sets available-the cautionary tale is to pay close attention to the approach to increase the opportunity for success.
What is Lean Manufacturing?
Defining Lean
Although the phrase lean manufacturing has become ubiquitous, it's a good idea to explain what it is first.
Author James Edge defines lean as
...a business strategy that is meant to eliminate waste so that the customer is happier and gets what they want. Whenever the customer is satisfied, the business can have more positive returns, which are going to increase their sales and goodwill.
Eliminating any waste in a process is a good thing. But what is waste?
Waste is defined as any activity that does not add value from the customer's perspective. According to research conducted by the Lean Enterprise Research Centre (LERC), fully 60% of production activities in a typical manufacturing operation are waste – they add no value at all for the customer.
8 Types of Waste
Eliminating waste is one of the most important principles of lean manufacturing, and eight types are identified:
Overproduction
Overproduction occurs when making a component before it's needed, creating excessive lead times, high storage expenses, and finding defects becomes more difficult.
Waiting
Waiting is a waste from the times when components are not moving. In traditional manufacturing, more than 99% of the life of a component is spent waiting for the next step in manufacturing. These delays occur because of poor material flow, excessively long production runs, and vast distances between work centers.
Transporting
The waste of transporting is directly related to waiting. The transportation of components between processes adds cost without adding value to the final product.
Inappropriate Processing
Occam's Razor is a philosophical idea that in any set of explanations for an event, the simplest explanation is often the correct one. Occam's Razor is an apt analogy to the waste of inappropriate processing where many companies use expensive, sophisticated equipment when more straightforward tools work just fine.
Unnecessary Inventory
Excess inventories tend to hide issues found on the plant floor. Spending time locating and resolving these issues adds cost to improving operating performance. Higher inventory increases lead times take up productive space, delays problem identification, and hurts communication.
Unnecessary / Excess Motion
Ergonomics plays a significant role in this waste. Excessive motion injuries are reduced with bending and stretching programs.
Defects
Defective components hurt the bottom line. Parts with defects need to be reworked or scrapped. For many companies, defect total costs is often a large percentage of the total manufacturing cost.
Underutilization of Employees
Companies sometimes forget that in addition to their skills, employees provide creative solutions to the other seven wastes and improve their performance with continuous improvements.
Lean manufacturing focuses on customer satisfaction. If a manufacturer follows its lean business model, they'll make cheaper products and better reduce shipping times, streamlining the company's efficiency.
Lean Principles
Before implementing lean techniques, manufacturing companies must complete a five-step process. Edge wrote that this isn't an easy task.
You will find that these goals are not always going to be easy to implement, but with time, patience, and practice, you will be able to.
- Know the views of the customers on the basis of your products to specify your value.
- The steps of the value stream should be written down for every product family. What steps can you get rid of because they are not adding value to your product?
- The steps that create value should be in sequence tightly with the products so that the production line runs as smoothly as possible.
- While your flow is introduced, you should allow your customers to pull some value from another upstream activity.
- Once your value has been specified, then your value streams will be identified, and you can get rid of any wasted steps, which will introduce your flow and pull. To begin this process again, you have to continue until you reach a state of perfection, which will be the moment wherein there is no waste, and your perfect value is created.
What's Next
With an understanding of lean manufacturing, our next post explores setting goals with Lean Integration.
In Sum
Many believe businesses only talk about managing costs when they are lean. In reality, doing so is only one aspect of lean manufacturing. The other key aspect is improving the quality of the products being produced. If it is not possible to produce something of a high enough quality, then the business will not be successful.
So, what types of waste are associated with these two aspects of lean manufacturing? Here are some examples of the waste associated with lean manufacturing: one benefit is eliminating waste. It's difficult to determine exactly what types of waste an organization is dealing with. However, there are eight identified different wastes.
When lean businesses eliminate waste, they realize cost savings and profit increases. On top of these benefits, lean manufacturing increases workforce satisfaction and creates a more positive work environment for employees.
Paying attention to the waste in your business can help you and your team recognize how much is present, how much is being generated, and how to eliminate it.