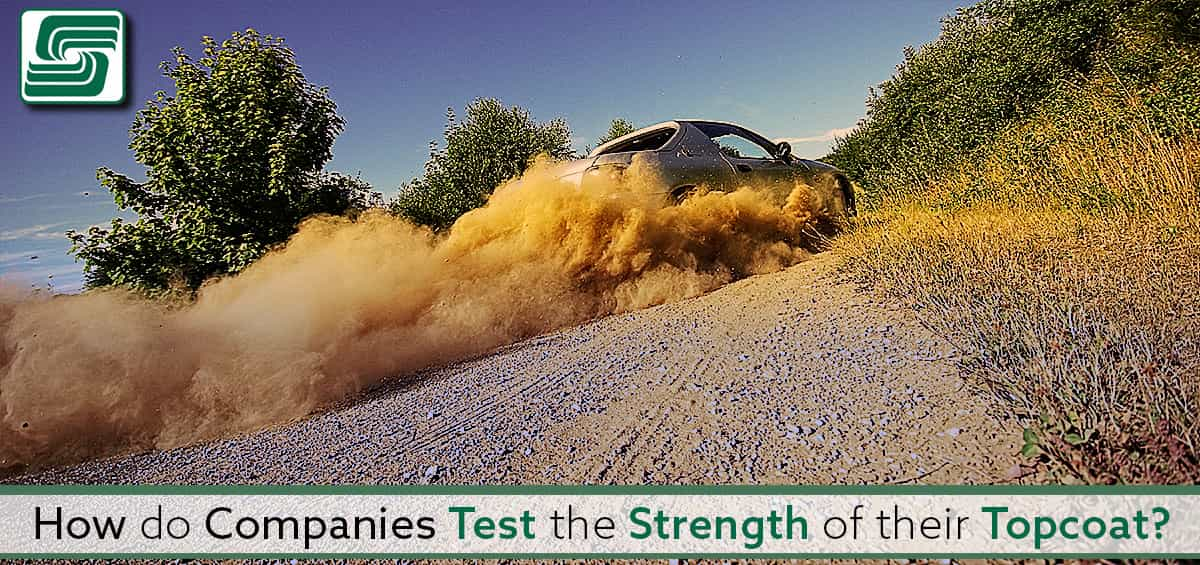
Several years ago, I owned a comfortable car that drove smoothly. Unfortunately, the outside looked like the surface of an asteroid. It was an inexpensive hail-damaged car that caught the look of anybody on the street.
I joked that the indentations helped streamline the car as dimples did for a golf ball. What I thought remarkable was that with so many dents, the golf ball, as we called the car, didn't have any rust.
The significant hail damage didn't affect the integrity of the car's topcoat. Some of the blemishes were a quarter-inch deep, yet there wasn't any corrosion.
That fact illustrated the technology behind the sophisticated process of protecting the car from any chipping damages. I think it's safe to assume modern automotive paint processes are the opposite of Earl Scheib's model of finishing.
Note: This article is the third of a series comparing protective metal finishing process methods.
Part 1: Two-Coat Systems Using E-Coating
Part 2: Is a Third Coat Necessary?
Part 3: Testing Topcoat Strength
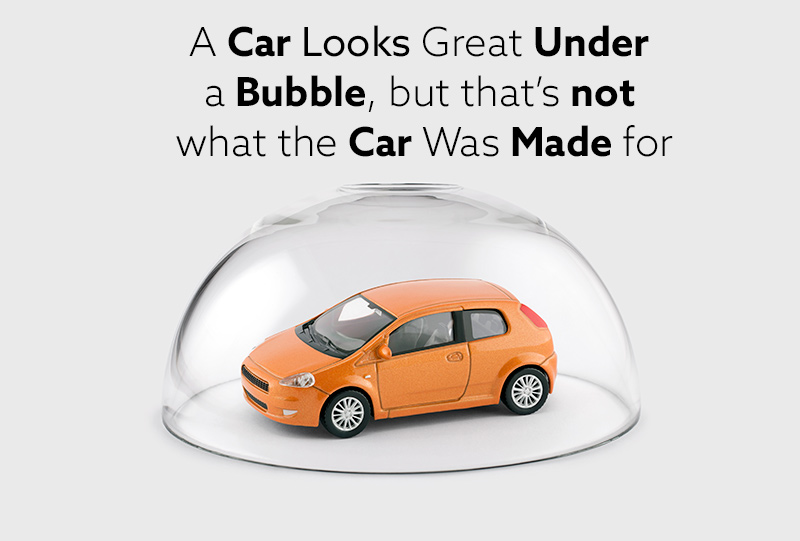
Level of Standards
Nearly all the things we use in the United States undergo some testing. The office furniture industry uses standards set by BIFMA, for example. Manufacturers submit their furniture to BIFMA-approved testing sites to see if their pieces meet the organization's standards.
Automobile manufacturers providing protective topcoats would use standards respective to their industry if it wasn't for these standards than any auto company can make grandiose claims about their topcoat without the worry of repercussions.
Fortunately, early on in the auto industry, people with foresight learned to work together to pull society out of horse-drawn carriages.
Birth of the SAE
First organized in 1905, the Society of Automobile Engineers (SAE) goals were to protect patents, share common technical design problems, and develop engineering standards.
After a few years, it became apparent the importance of creating industry standards. For those of us in the finishing industry, the J400 chip resistance test became paramount.
A similar organization is the American Society for Testing and Materials (ASTM). The ASTM has no role in enforcing or requiring compliance with its standards. Finishing companies may be required to meet those levels because of prospective contracts.
SAE J400 and the Gravelometer
Finishing companies submit their components for testing to meet SAE J400 standards. J400 testing evaluates and tests the resistance of the topcoat to chipping from gravel impacts.
It sounds simple, which it is, but how consistent would the testing topcoats from different companies located throughout the United States. Gravel isn't the same everywhere. Individual rocks vary in size. How fast would the vehicle need to travel?
The gravelometer answers all those questions. Gravelometers meet technical standards set by ASTM/ASE. The machine simulates the impacts of gravel or other debris on coated automotive components.
Topcoat Testing Procedure
Chip testing blasts approximately 300 pieces of gravel on a 4-inch × 12-inch test panel at 70 psi. The next step of the test is gently wiping the surface with a cloth, followed by applying a layer of tape. When removed, the tape pulls off any loose coating fragments.
This short clip demonstrates the J400 testing method:
Technicians compare the test results to standard transparencies provided by the SAE to determine chipping ratings. The Plastics Technology Laboratories summaries the ratings:
Chipping Ratings consist of one or more letter-number combinations. The letter designates the chip sizes counted, and the number designates the number of chips of that size.
For example, B6 indicates 10-24 chips 1 to 3 mm in size. Point of Failure describes the coating layer, where the primary failures are occurring. For example, P/T indicates that the point of failure is between the primer and the topcoat.
Test Results
Comparing the chipping damage to the attached chart determines the Chip Rating for a topcoat protective layer.
Because of these standards and testing methods, an apple-to-apple comparison between various topcoats is fair.
Salt Spray Testing
Another method of measuring the strength of a topcoat is an extended salt spray test. We submitted samples for salt spray testing at three levels: 500 hours, 1,000 hours, and 1,500 hours.
Check out our E-Coat Top Coat page. This page provides before and after sliding scales for 500, 1,000, and 1,500 hours of salt spray testing.
Reading about e-coating's effectiveness is one thing; seeing it is another.
In Sum
Without these standards, the market becomes a Wild West filled with a diverse range of companies offering a smorgasbord of topcoats, most of which are unregulated and unproven. Without standards, there’s no assurance that these products do what they claim to do.
There’s no way to know whether they’re safe or effective. And there’s no way to know whether they’re even what you’re looking for.