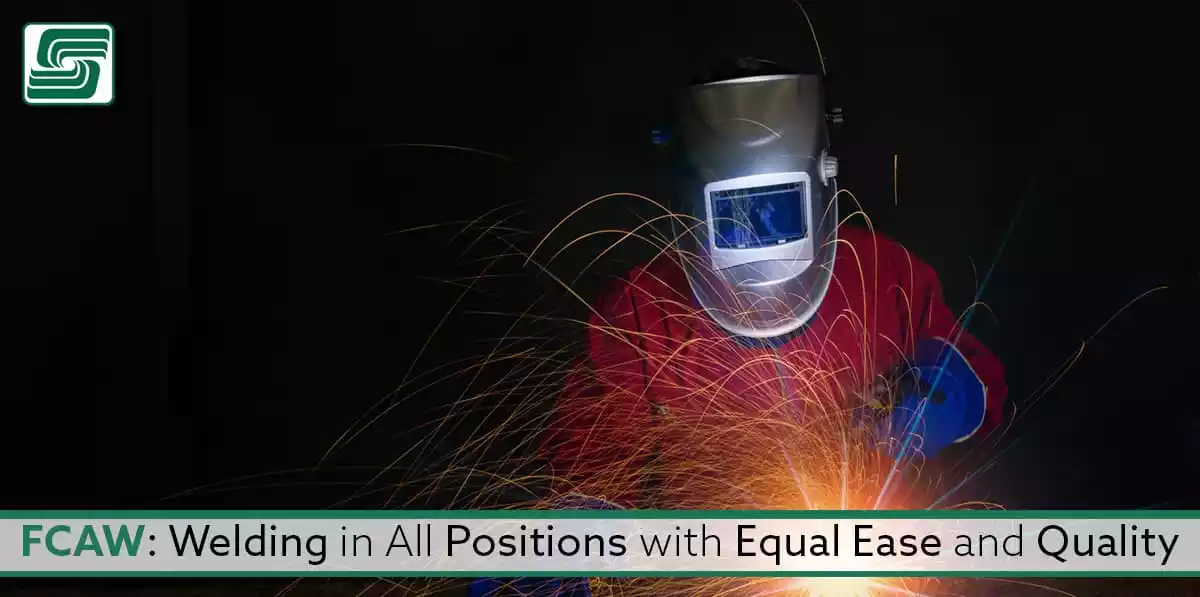
Flux-cored arc welding (FCAW) is a versatile and efficient process offering numerous advantages over other welding methods. One of the key benefits of FCAW is its ability to weld in all positions with equal ease and quality.
In this article—the second in our series of three—we explore the various aspects of FCAW, including its history, development, types, advantages and disadvantages, and applications in different industries.
(Check out our first article, 8 Things you Might Not Have Read About When it Comes to FCAW)
As you read, you'll understand why FCAW is a popular choice for various welding projects and how to use it to achieve consistent results in all positions.
Introduction to FCAW
FCAW is a semi-automatic or fully automatic arc welding technique that utilizes a continuously fed consumable electrode containing a flux. This flux is essential for protecting the weld from contaminants and oxidation. FCAW offers many advantages, such as speed, efficiency, cost-effectiveness, and ease of use. Additionally, FCAW is a relatively safe welding process, as the flux-cored wire helps protect the weld from oxidation and contamination.
Development and History
FCAW has roots in the 1940s and has since become a widely used welding process in various industries, beginning with carbon steel welding applications. Still, technological advancements have made it suitable for a wider variety of materials, including stainless steel, aluminum, and other alloys. This versatility has made FCAW a popular choice for many welding projects.
Types of FCAW
There are two main types of FCAW:
Self-Shielded FCAW
In this type of FCAW, the flux-cored electrode generates its own protective gas to shield the weld, eliminating the need for an external shielding gas system and making the process more cost-effective and easier to set up. Self-shielded FCAW is particularly effective for thinner, flat-position metals and outdoor or windy environments that would dissipate a shielding gas.
Gas-Shielded FCAW
For welding thicker, out-of-position metals, especially in structural steel welding, FCAW can be used with shielding gas for enhanced quality and consistency, which is often referred to as "dual shield" welding since both the shielding gas and the flux are used to protect the weld. This process is better suited for controlled environments, such as fabrication shops, where the wind won't interfere with the shielding gas.
FCAW in All Positions
One of the key advantages of FCAW is its ability to weld in all positions with equal ease and quality, meaning welders can use this process for various applications, from horizontal and vertical welding to overhead and flat welding. The following sections will discuss the benefits of using FCAW in each of these positions.
Horizontal Welding
FCAW is particularly suitable for horizontal welding due to its high deposition rate, which allows for faster welding speeds and increased productivity. The flux in the electrode protects the weld, ensuring consistent quality even when working in a horizontal position.
Vertical Welding
Vertical welding can be challenging due to the effects of gravity on the molten weld pool. However, FCAW's flux-cored wire helps maintain a stable weld pool, preventing sagging and ensuring consistent quality in vertical welding applications while becoming easily adjusted to accommodate the specific requirements of vertical welding, such as controlling the travel speed and voltage.
Overhead Welding
Overhead welding can be difficult because of the potential for molten metal to fall onto the welder. With FCAW, the flux-cored wire helps create a protective slag layer over the molten metal, reducing the risk of falling molten metal and ensuring consistent weld quality in overhead applications.
Flat Welding
FCAW offers excellent weld penetration and a high deposition rate in flat welding applications. The process is also relatively easy to learn compared to other welding processes, making it an ideal choice for flat welding projects.
Advantages of FCAW in All Positions
Using FCAW for welding in all positions offers several advantages over other welding processes. Some of these benefits include:
- High welding productivity: FCAW has a high deposition rate, meaning that the filler metal is applied quickly, which allows for increased welding productivity.
- Easy to learn: FCAW is relatively easy to learn compared to other welding processes, making it accessible to a wide range of welders.
- Forgiving of base metal contaminants: FCAW is more forgiving of rust, scale, and other base metal contaminants than other welding processes, ensuring consistent weld quality even in less-than-ideal conditions.
- Suitable for outdoor welding: The self-shielded FCAW process can be used outdoors and in windy conditions, where a shielding gas blows away, ensuring consistent weld quality regardless of environmental factors.
- Excellent weld penetration: FCAW provides excellent weld penetration, resulting in strong and durable welds.
Disadvantages of FCAW in All Positions
Despite its many advantages, FCAW does have some drawbacks when used in all positions. These include:
- Increased fumes: FCAW can produce a higher level of noxious fumes than other welding processes, requiring proper ventilation or outdoor welding.
- Higher electrode wire cost: The cost of the consumable electrode wire for FCAW can be higher than solid electrode wires used in other processes.
- Slag removal: The slag produced during the FCAW process must be removed after welding, which can be time-consuming and labor-intensive.
- Mechanical issues: Problems such as melted contact tips, irregular wire feed, or weld porosity can occur during FCAW, affecting weld quality.
Applications of FCAW in Different Industries
Several industries use FCAW due to its versatility and ability to weld in all positions with equal ease and quality. Some of the most common industries using FCAW:
Shipbuilding
FCAW is well-suited for shipbuilding applications because of its ability to weld thick joints in all directions. The process can be easily adjusted to accommodate different angles, ensuring consistent weld quality and strength throughout the ship's structure.
Pipeline Welding
Pipeline welders need several positions for welding, from horizontal and vertical to overhead. FCAW's ability to weld consistently in all positions makes it an ideal choice for pipeline welding projects.
Structural Steel Welding
FCAW is common in structural steel welding because of its excellent weld penetration and high deposition rate. The process can be easily adjusted to accommodate various positions, ensuring consistent weld quality and strength in structural steel applications.
Automotive Welding
The automotive industry uses FCAW for welding frames, exhaust systems, and components made from steel and aluminum parts. The process is easy to learn, making it accessible to a wide range of welders, and offers consistent weld quality in various positions.
FCAW Equipment and Accessories
To perform FCAW in all positions, welders require specific equipment and accessories. These include:
- Flux-cored wire: The consumable electrode used in the FCAW process, available in various diameters and materials to suit different applications.
- Welding power source: A constant-voltage or constant-current welding power supply is required for FCAW, ensuring consistent heat input and weld quality.
- Wire feeder: A wire feeder system controls the speed at which the flux-cored wire is fed into the weld pool, allowing for precise control over the welding process.
- Welding torch or gun: The welding torch or gun directs the flux-cored wire and welding current to the workpiece, ensuring accurate and consistent weld placement.
- Shielding gas system—if required: For gas-shielded FCAW, the required shielding gas system provides additional protection to the weld from contaminants and oxidation.
Safety Considerations for FCAW in All Positions
When using FCAW in all positions, it is crucial to follow safety guidelines to ensure the well-being of the welder and those working nearby. Some safety considerations include:
- Wearing appropriate safety gear, such as a welding helmet, gloves, and a welding jacket.
- Being aware of your surroundings and potential hazards.
- Using the correct welding machine and settings for the project.
- Keeping the welding area clean and free from flammable materials.
- Inspecting the consumable electrode before use and replacing it if it is damaged or contaminated.
- Adjusting the wire feed speed to the correct level to ensure a consistent weld.
FCAW Techniques for All Positions
To achieve consistent weld quality in all positions, welders must master specific FCAW techniques. These include:
- Adjusting travel speed and voltage to suit the specific position.
- Controlling the welding current, ensuring that the arc remains stable and consistent.
- Manipulating the welding torch or gun to maintain the correct angle and distance from the workpiece.
- Using the appropriate flux-cored wire and shielding gas (if required) for the specific application.
Troubleshooting Common FCAW Issues
Welders may encounter various issues when using FCAW in all positions. Some common problems and solutions include:
- Porosity: Caused by improper shielding gas coverage, incorrect wire feed speed, or a contaminated electrode, which ensures the shielding gas flows correctly, adjust the wire feed speed and inspect the electrode before use.
- Lack of fusion: A welding current that's too low requires the welding current or slow travel speed to ensure proper fusion.
- Excessive spatter: Caused by a welding current or voltage that's too high. Decrease the welding current or voltage to reduce the spatter.
In Sum
FCAW is a versatile and efficient welding process used almost everywhere with equal ease and quality. Its ability to weld various materials and accommodate different welding positions makes it popular for several industries and applications. By understanding the advantages and disadvantages of FCAW and mastering the techniques required for each position, welders can achieve consistent weld quality and strength in their projects.