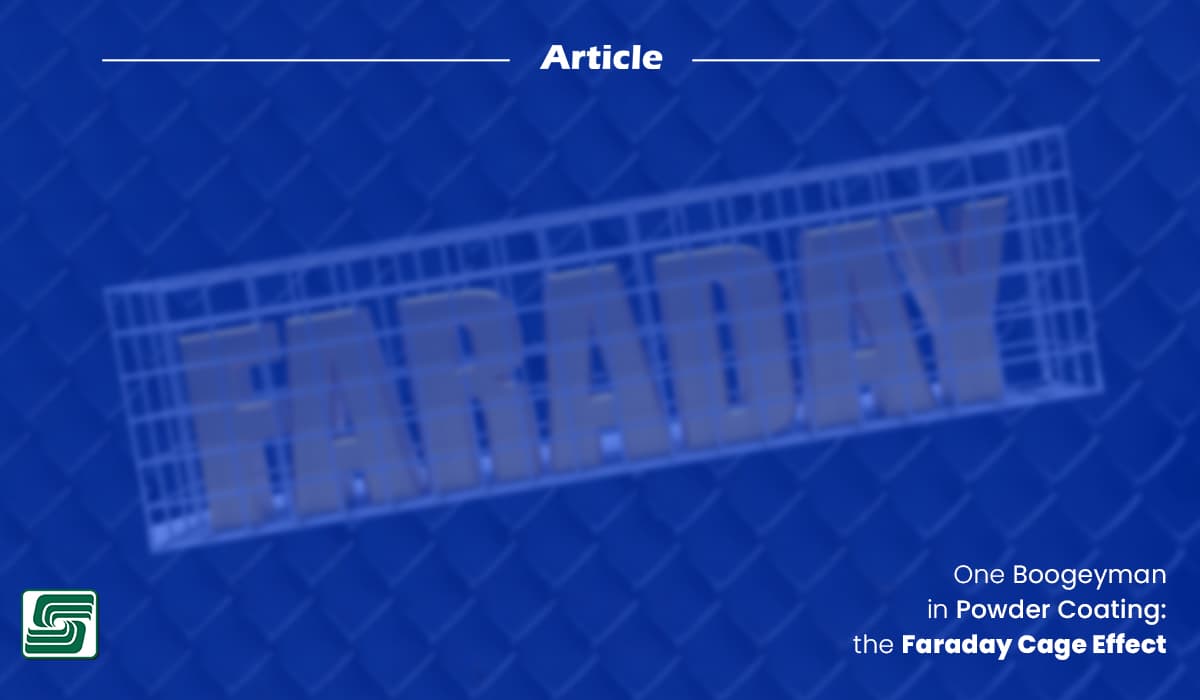
The Faraday cage concept stems from Michael Faraday's groundbreaking invention. In 1836, he discovered that an enclosure made of conductive material could effectively block electromagnetic fields. This invention had a profound impact on protecting electronic equipment and shielding it from electric currents.
Scientific Principles Behind the Effect
Scientific research findings have revealed that Faraday cages distribute electric charges within the conducting material to cancel out the external field's effect inside the cage. These cages block electromagnetic radiation across the spectrum, including radio waves and microwaves, making them indispensable for various applications.
Faraday Cage in Everyday Life
Faraday cages are widely used in modern technology to shield sensitive equipment from external interference, lightning strikes, and electrostatic discharges. They are commonly employed in hospitals, laboratories, and even kitchens to protect electronic devices from electromagnetic radiation.
Importance in Electrical Engineering
Faraday cages are pivotal in reducing noise introduced by electromagnetic interference in electrical engineering. For accurate and reliable nanoelectrochemical measurements, it is important to use equipment that provides optimal exclusion of electromagnetic interference.
The Challenge of the Faraday Cage Effect in Powder Coating
The Faraday cage effect presents a significant challenge in powder coating, impacting the quality and uniformity of the coating application. Knowing its implications and concerns is key to understanding how it affects industrial applications.
- Impact on Powder Coating Quality: The Faraday cage effect significantly affects powder coating quality, particularly in challenging areas such as recesses and corners. When charged parts with sharp edges or recessed locations are subjected to powder coating, the Faraday cage effect hinders the proper deposition of powder particles into these areas. Poor deposition results in an uneven and incomplete coating, leading to durability concerns and compromised aesthetic appeal.
- Specific Challenges in Coating Recesses and Corners: Applying powder coating can be challenging when dealing with the Faraday cage effect. This effect makes reaching certain substrate areas difficult, a significant obstacle. Changes must be made to the application process and equipment to ensure complete coverage and adhesion.
Why It Matters
- Implications for Industrial Applications: The implications of the Faraday cage effect extend to various industrial applications, especially those involving complex part geometries or intricate designs. Overcoming this challenge is essential for ensuring consistent and high-quality powder coating across diverse substrates, ultimately contributing to enhanced product performance and longevity.
- Quality and Durability Concerns: The Faraday cage effect raises concerns about coated products' overall quality and durability. Inadequate coverage from this phenomenon leads to premature wear, corrosion susceptibility, and diminished functional integrity. Addressing these concerns through effective mitigation strategies is imperative for upholding stringent quality standards within industrial settings.
New and innovative approaches are necessary to improve the efficiency of powder coating while reducing the negative effects of the Faraday cage phenomenon.
Strategies to Overcome the Faraday Cage Effect
The Faraday cage effect must be addressed if the goal is to improve the powder coating process. This goal will be met by exploring effective strategies that optimize the coating process and reduce the impact of the Faraday cage effect. Industry experts have shared valuable insights on enhancing powder coating, especially in areas with complex shapes and hidden surfaces.
Adjusting the Application Process
- Reducing KV Output Before Application: One key strategy for overcoming the Faraday cage effect involves adjusting the kilovolt (KV) output before applying the powder application. By reducing the KV output, the electrostatic charge on the powder particles is moderated, minimizing resistance and enabling a more uniform deposition. This change promotes improved coverage in recessed areas and corners where the Faraday cage effect typically poses challenges.
- Altering Spray Angles and Techniques: Industry experts emphasize the significance of altering spray angles and techniques to effectively address the Faraday cage effect. Comprehensive coverage across intricate part geometries becomes workable by modifying the direction of powder spray and adopting alternative techniques, such as indirect spraying or using lesser angles. This approach allows for enhanced adhesion and minimizes issues related to inadequate powder deposition in challenging areas.
Equipment and Technique Modifications
- Adjusting the Flow and Powder Output: An essential aspect of overcoming the Faraday cage effect involves changing equipment settings related to flow control and powder output. Adjusting these parameters allows the powder volume being dispensed to be regulated, ensuring a more controlled application process. This modification enables targeted coating in recessed portions susceptible to experiencing insufficient coverage because of this phenomenon.
- Changing Gun-to-Part Distance: Another critical technique industry experts recommend is changing the distance between the spray gun and the substrate surface. By optimizing this distance, powder particles can be better absorbed into recessed areas while mitigating issues associated with back ionization. This change contributes significantly to addressing challenges posed by complex part geometries affected by the Faraday cage effect.
Integrating these approaches enhances coating quality and ensures consistent performance across diverse substrates.
Innovations in Coating Technology
As the challenges posed by the Faraday cage effect continue to drive advancements in powder coating, notable innovations in coating technology have emerged to address these complexities. These innovations encompass a spectrum of developments, ranging from new equipment designs to using advanced materials and methods.
- New Equipment Developments: In response to the inherent limitations associated with conventional powder coating processes affected by the Faraday cage effect, Kevin J. Kittle introduced a groundbreaking concept through the Conformally Coated Faraday Cage patent. This innovative process enables coating substrate areas that are typically inaccessible because of this effect, revolutionizing traditional electrostatic coating methodologies.By leveraging this approach, it becomes workable to achieve comprehensive coverage in challenging geometries while enabling the formation of thinner coatings compared to conventional fluidized-bed processes.
- Advanced Materials and Methods: The patent titled Faraday-Cage Effect for Coating underscores the significance of addressing difficult access points, emphasizing the need for advanced materials and methods to overcome these challenges effectively. This theory highlights a pivotal shift towards developing novel materials tailored to mitigate the impact of the Faraday cage effect during powder coating. Advancements in application methods are being explored to optimize powder deposition in intricate part geometries affected by this phenomenon, ensuring uniform coverage and enhanced adhesion.
Looking Ahead
- Potential for Improved Efficiency and Quality: The ongoing research and development initiatives within the realm of powder coating hold tremendous potential for driving improved efficiency and quality across diverse industrial applications. By harnessing innovative technologies and methodologies to overcome Faraday cage challenges, there is a clear trajectory toward enhancing overall coating performance while optimizing resource utilization. These advancements present significant opportunities for streamlining production processes and elevating product durability through comprehensive coverage in recessed areas susceptible to this effect.
- The Role of Ongoing Research and Development: Ongoing research and development cannot be understated in shaping the future landscape of powder coating amidst Faraday cage challenges. Focusing on novel approaches, innovative materials, and refining techniques can potentially lead to transformative advancements in powder coating processes. This proactive pursuit of innovation is poised to redefine industry standards by mitigating limitations imposed by the Faraday cage effect while fostering continuous improvement in coating quality and durability.
In Sum
Powder coating technology is improving, and there is hope that Faraday cage challenges can be overcome. With new equipment designs, better materials, and ongoing research, industrial powder coating applications may become more efficient, higher quality, and more effective.