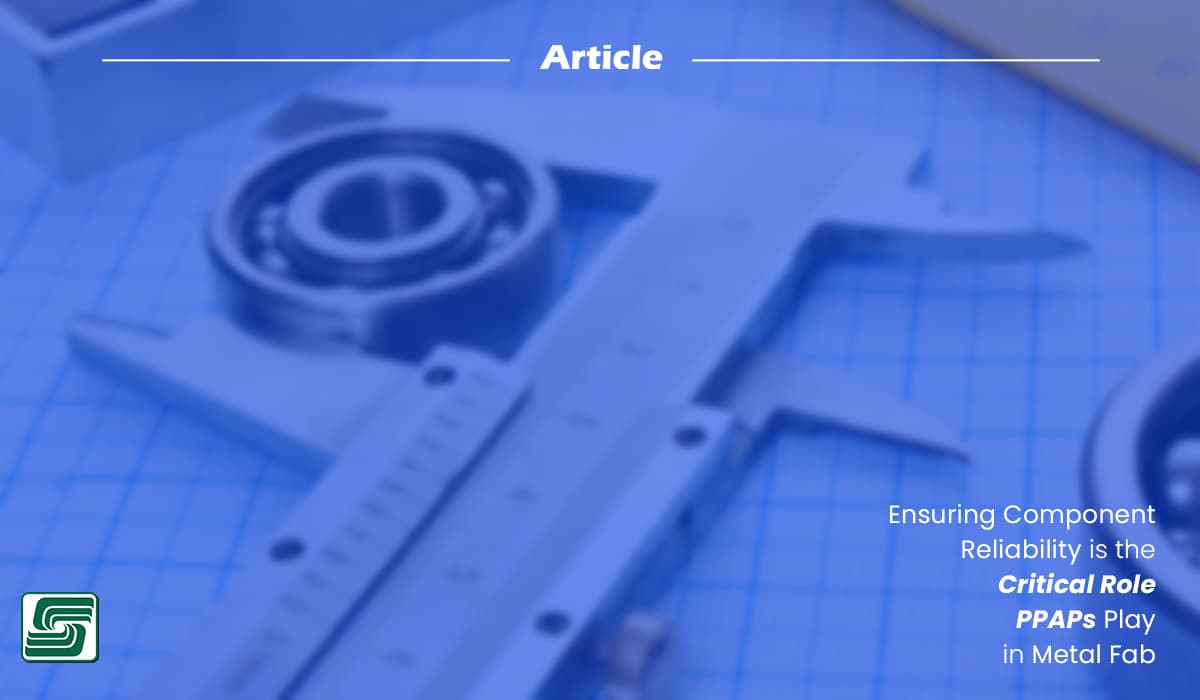
The Production Part Approval Process (PPAP) ensures components' reliability within the metal fabrication realm. This standardized process guarantees that suppliers consistently deliver products and services, meeting specified requirements. By adhering to the PPAP process, manufacturers identify and mitigate potential risks in the production of components, enhancing overall reliability. When manufacturers implement PPAP, they streamline their production processes, enhance component reliability, and increase customer satisfaction.
Key Takeaways:
- PPAP is fundamental in enhancing component reliability.
- Adhering to PPAP standards leads to improved product quality and reduced risks.
- Collaboration between suppliers and OEMs is crucial for successful PPAP implementation.
By upholding the rigorous requirements of PPAP, manufacturers solidify their position in the market while delivering reliable components that meet stringent industry standards.
Understanding PPAP
The Production Part Approval Process (PPAP) is a standardized method to ensure suppliers consistently deliver products and services that meet specified requirements. This process plays a pivotal role in identifying and mitigating potential risks within the production process, contributing to enhanced component reliability.
The Production Part Approval Process (PPAP) is a standardized method to ensure suppliers consistently deliver products and services that meet specific requirements.
Key Elements of PPAP
- Submitting various PPAP documents, including design records, engineering change documents, and more, is integral to the approval process.
- PPAP encompasses essential elements such as dimensional results, material certifications, and process flow diagrams. Collectively, these components contribute to the thorough validation of the production processes.
Benefits of PPAP
Enhanced Component Reliability
- Implementing PPAP ensures components are manufactured to the highest standards, minimizing the risk of defects and failures. This meticulous approach to production improves component reliability, resulting in heightened customer satisfaction and trust.
Cost Savings and Efficiency
- One of PPAP's significant advantages is its ability to identify and address potential issues early in production, which helps avert costly rework and delays and streamlines the manufacturing process.
- This streamlined approach leads to cost savings and significantly improves overall efficiency.
Manufacturers achieve enhanced component reliability by adhering to the PPAP requirements while optimizing production processes for better cost-effectiveness and operational efficiency.
PPAP process: Implementing PPAP ensures components are manufactured to the highest standards, reducing the risk of defects and failures. It also helps identify and address potential issues early in production, leading to significant cost savings and improved efficiency.
Key Steps in PPAP
The Production Part Approval Process (PPAP) involves several key steps to ensure components' reliability in metal fabrication.
Document Submission
- The first step in the PPAP process is submitting documents, including design records and engineering change documents. These documents play a pivotal role in demonstrating the supplier's ability to meet specific requirements outlined in the PPAP manual.
- Each submitted document must adhere to stringent guidelines and standards, ensuring comprehensive production process documentation.
Evaluation and Approval
- After submitting the documents, a thorough evaluation is conducted to assess their compliance with customer requirements and industry standards. This evaluation aims to verify that all necessary criteria are met before approving production.
- Upon successful evaluation, the approval for production is granted, signifying that the components have undergone rigorous scrutiny and validation as per the PPAP requirements.
The meticulous submission, evaluation, and approval processes within PPAP are fundamental in upholding component reliability and ensuring that manufacturers consistently deliver products that meet stringent quality standards.
Successful Case Studies
Improved Quality and Customer Satisfaction
Manufacturers have witnessed a noticeable improvement in the quality of their components when they stick to the stringent PPAP requirements. This improvement has directly translated into increased customer satisfaction because end-users have experienced products consistently meeting or exceeding their expectations.
The meticulous validation and scrutiny of the PPAP process have instilled customer confidence, strengthening the relationship between suppliers and OEMs. As a result, manufacturers have built trust and credibility by delivering components that align with the highest quality standards, solidifying their market position.
Reduced Defect Rates and Rework
Successful case studies within various industries have underscored significant reductions in defect rates and rework following the implementation of PPAP. Manufacturers leveraging the PPAP process have reported substantial cost savings from minimized defects and rework instances. This reduction improves operational efficiency and reflects a consistent commitment to delivering reliable, high-quality components.
By meticulously adhering to the PPAP requirements, manufacturers proactively identify potential issues early in the production process, mitigating risks associated with defects and rework. The structured approach offered by PPAP has proven instrumental in achieving consistent quality while minimizing costly setbacks related to defects and rework.
Comparison with Other Methods
When comparing the Production Part Approval Process (PPAP) with traditional quality assurance methods, it becomes evident that PPAP offers distinct advantages and a more comprehensive approach to validating production processes and enhancing component reliability.
Advantages of Traditional Quality Assurance
PPAP stands out by offering a structured framework for verifying suppliers' capability and ensuring thorough validation of production processes. Unlike traditional quality assurance methods, PPAP encompasses a meticulous approach that involves submitting various documents, such as design records and engineering change documents, to demonstrate compliance with specific requirements. This comprehensive validation process plays a pivotal role in upholding component reliability and instilling confidence in the quality of manufactured components.
Efficiency and Risk Mitigation
Compared to other methods, PPAP is more effective in identifying and mitigating risks early in production. By requiring the submission of essential documents and dimensional results, PPAP streamlines the approval process, leading to improved efficiency and reduced time to market. This structured approach enhances component reliability and minimizes potential risks associated with defects or failures.
Regulatory Requirements and Trends
Compliance with Industry Standards
PPAP plays a critical role in ensuring compliance with industry-specific standards and regulatory requirements, catering to the unique needs of the metal fabrication industry. Manufacturers navigate the intricate landscape of quality management systems and regulatory frameworks by adhering to the Production Part Approval Process. This adherence guarantees the reliability of components and demonstrates a commitment to upholding industry standards and meeting the stringent requirements set forth by regulatory bodies.
"Adhering to PPAP ensures compliance with industry-specific standards and regulatory requirements, addressing the unique needs of the metal fabrication industry."
Emerging Trends in PPAP
The evolution of PPAP is marked by a shift towards digitalization and automation aimed at enhancing efficiency throughout the submission and evaluation process. These emerging trends focus on leveraging digital tools and automated systems to streamline various stages of PPAP, ultimately leading to improved efficiency and effectiveness. Manufacturers are encouraged to adapt to these trends as they are essential for staying ahead in the rapidly evolving metal fabrication landscape. Embracing digitalization and automation within PPAP enhances operational processes and positions manufacturers at the forefront of technological advancements.
- Digitalization and Automation: Integrating digital tools and automated systems is revolutionizing PPAP and streamlining processes for enhanced efficiency.
- Staying Ahead: Adapting to emerging trends is crucial for manufacturers aiming to stay competitive in an ever-evolving metal fabrication landscape.
Implementing PPAP
Implementing PPAP involves seamlessly integrating best practices to ensure that the Production Part Approval Process is effectively incorporated into the metal fabrication processes. By adopting proactive strategies and fostering collaboration between suppliers and Original Equipment Manufacturers (OEMs), manufacturers enhance customer satisfaction and build trust and credibility.
Best Practices for Integration
- Clear Communication Channels: Clear communication channels between suppliers and OEMs is fundamental to successful PPAP implementation. Transparent and open communication fosters collaboration, ensuring that all parties are aligned with the requirements of the PPAP process.
- Proactive Approach: Adopting a proactive approach to PPAP implementation is crucial. This involves staying ahead of potential issues, promptly addressing them, and continuously seeking opportunities for improvement within the production processes. Proactivity ensures that challenges are mitigated early on, leading to smoother integration.
Enhancing Customer Satisfaction
- Consistent Product Quality: Implementing PPAP contributes to consistent product quality and reliability. Manufacturers deliver components that consistently meet or exceed customer expectations by adhering to the rigorous standards outlined in the PPAP process.
- Trust and Credibility: PPAP implementation builds trust and credibility between suppliers and OEMs. Through meticulous adherence to the PPAP requirements, manufacturers demonstrate their commitment to delivering reliable components manufactured according to the highest industry standards.
In Sum
The Production Part Approval Process (PPAP) is a cornerstone in ensuring the reliability of components in metal fabrication. By meticulously adhering to PPAP standards and best practices, manufacturers significantly enhance product quality, reduce risks associated with defects and failures, and ultimately build customer trust.
The Production Part Approval Process (PPAP) plays a pivotal role in ensuring the reliability of components within the realm of metal fabrication.
Implementing PPAP involves a structured approach that validates production processes and fosters collaboration between suppliers and Original Equipment Manufacturers (OEMs). This proactive integration ensures that components are consistently manufactured to the highest standards, meeting or exceeding customer expectations.
By embracing digitalization and automation trends within PPAP, manufacturers streamline processes for enhanced efficiency, positioning themselves at the forefront of technological advancements in the rapidly evolving metal fabrication landscape.