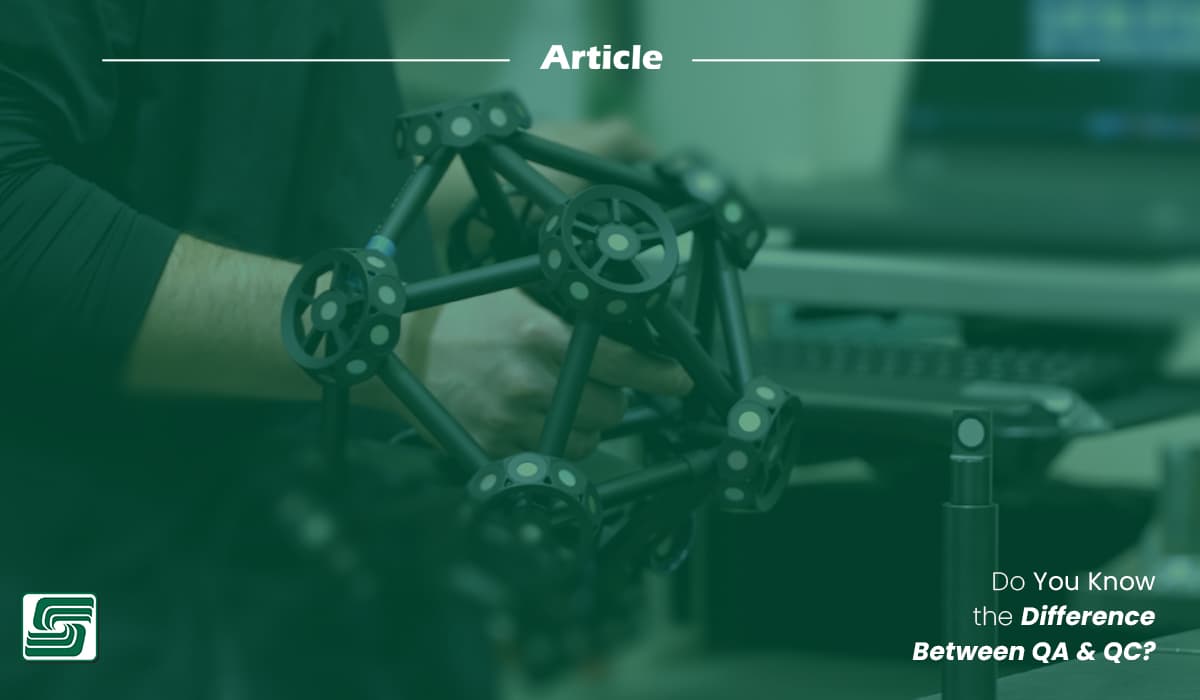
When opening the box containing your new circular saw, does the thought of blade misalignment occur to you? If you're anything like me, I turn into my inner alpha male, craving the chance to cut something in half!
Without thinking, I'd line the saw with the board and press the trigger. Imagine the potential damage and injury from using a saw that failed quality tests yet was still shipped to the unknowing customer: me.
Our free market has developed such effective Quality Management Systems (QMS) that we no longer consider any possible mechanical problems related to our new purchases.
Effective QMS processes fall under the lean manufacturing umbrella and, when properly implemented, are a tremendous tool for manufacturers.
What is Quality Assurance?
Quality assurance (QA) is a process-oriented managerial tool developed to ensure quality in product development processes. It aims to prevent defects by focusing on the process used to make the product. QA is a proactive quality process.
What is Quality Control?
Quality Control is a product-oriented corrective tool developed to identify product defects after assembly and before release. It is a reactive process that locates and eliminates sources of quality problems using tools and equipment to prevent future defects.
Quality Assurance Audits
Quality Assurance Audits, also called QA audits, are among the most critical aspects of quality assurance in manufacturing. They consist of activities to ensure companies provide their customers with the best possible service or product. Quality assurance aims to ensure that these processes efficiently and effectively meet predetermined quality standards.
Quality Assurance Testing
Quality Assurance (QA) tests prevent companies from manufacturing inferior or poorly functioning products. QA is the process of monitoring a product, ensuring that no part of the finished product fails in any way.
QA follows a defined cycle referred to as the PDCA or Deming Cycle.
Although simplistic, these steps, often repeated, ensure that processes the organization developed are improved and evaluated periodically. PDCA cycles include:
-
Plan: Organizations should plan and establish the process-related objectives and determine the processes required to deliver a high-quality end product.
-
Do: Development and testing of processes and changes in the processes.
-
Check: Monitoring processes, modifying them, and checking whether they meet the predetermined objectives.
-
Act: Implement actions that are necessary to achieve improvements in the processes.
Using QA ensures the resulting component was designed and implemented using correct methods, reducing errors and problems. In the case of manufacturing, it includes testing individual pieces during the manufacturing process itself and evaluating the quality of its components. However, there are two indispensable quality assurance and control tools—machines and software.
A Coordinating Measuring Machine (CMM) measures the geometry of objects by placing sensors on different points on an object's surface using a probe. The resulting measurements confirm whether or not the part conforms to specifications.
CMM Components
CMM systems include a solid table, probes, and a spring-loaded stylus connected to a gantry. The stylus and probe rotate independently, accessing the complete area of the examined piece.
Probes use physical contact instead of lasers or optical light, relying on spherical tips of rigid, stable materials. The tips mustn't be affected by weather fluctuations, as any changes in size ruin testing consistency.
There are two essential aspects of collecting information from the various points of the product.
The purpose of collecting these points is two-fold. Individual points are used to confirm measurements of actual parts against a customer's CAD file data for the purpose of quality assurance.
Or these points can be collected to create a "point cloud," outlining the shape of the part.
This is useful when a single sample of a part is used as the foundation of a CAD program to make more parts, such as with CNC machining.
CMMs can be particularly useful when measuring points inside of holes or bores. These recessed areas can be difficult or impossible to measure with optical systems because the light tends to reflect and bounce around inside the feature, causing interference and inaccuracy.
Several types of probes, including optical, laser, white light, and mechanical, are used with CMMs.
Quality Testing Software
Despite our best efforts, perfection is impossible for humans. Nothing is perfect. However, being and realizing we're imperfect pushes us to develop tools to reach near perfection.
Quality departments need a tool to interpret probe data to produce near-flawless products. Today's testing software represents decades of experience.
Ground Rules
However, sophisticated software that displays information doesn't matter much unless there are ground rules for the testing process.
- Testing Shows Presence of Mistakes: Testing aims to detect the defects within a piece of software. But no matter how thoroughly the product is tested, we can never be 100 percent sure there are no defects. We can only use testing to reduce the number of unfound issues.
- Exhaustive testing is impossible: There is no way to test all combinations of data inputs, scenarios, and preconditions within an application. For example, if a single app screen contains 10 input fields with three possible value options each, this means to cover all possible combinations, test engineers would need to create 59,049 (310) test scenarios. And what if the app contains 50+ of such screens? To avoid spending weeks creating millions of such less possible scenarios, it is better to focus on potentially more significant ones.
- Early Testing: As mentioned above, the cost of an error grows exponentially throughout the SDLC stages. Therefore, it is important to start testing the software as soon as possible so that the detected issues are resolved and do not snowball.
- Deflect Clustering: This principle is often called an application of the Pareto Principle to software testing. Approximately 80 percent of all errors are usually found in only 20 percent of the system modules. Therefore, if a defect is found in a particular module of a software program, the chances are there might be other defects. That is why it makes sense to thoroughly test that area of the product.
- Pesticide Paradox: Running the same set of tests repeatedly won't help you find more issues. As soon as the detected errors are fixed, these test scenarios become useless. Therefore, it is important to review and update the tests regularly to adapt and potentially find more errors.
- Testing is Context-Dependent. Different applications should be tested differently, Depending on their purpose or industry. While safety could be of primary importance for a fintech product, it is less important for a corporate website. The latter, in turn, emphasizes usability and speed.
- Absence-of-Errors Fallacy: Your product's complete absence of errors does not necessarily mean its success. No matter how much time you have spent polishing your code or improving the functionality, if your product is not useful or meets user expectations, it won't be adopted by the target audience.
After determining the ground rules, QA's job is continually identifying and correcting weaknesses resulting in continual improvement.
Quality Control
Often confused with QA, quality control (QC) examines the results. QC is essential for any company that wants to ensure product quality is maintained and continually improved. Quality improvement is analyzing the feedback received by the quality control team and workers from other aspects of the manufacturing process. Examples of quality and control activities include quality assurance audits, quality control, and quality control.
QC Benefits
Using an effective QC program provides several benefits, including
- Increased customer loyalty
- Gain repeat business
- Gain new customers from referrals
- Maintain or improve your position in the market
- Improve safety
- Reduce liability risks
- Contribute to the overall positive branding of your product
Costs correlating with recalls and injury settlements far exceed profits from the end product. The chances of a product recall or risking a customer's safety by using lousy products dramatically decrease.
Comparing QA and QC
QA and QC are two aspects of a quality management system. Although the two processes work together, they are each defined differently. Typically, QA responsibilities cover the whole quality system. QC is a subset of QA.
What is the Difference Between QA and QC
Here's a direct comparison illustrating the differences between QA and QC.
|
Quality Assurance |
Quality Control |
Definition |
QA is a set of activities for ensuring quality in the processes by which products are developed. |
QC is a set of activities for ensuring the quality of products. The activities focus on identifying defects in the actual products produced. |
Focus On |
QA aims to prevent defects, focusing on the process used to make the product. It is a proactive quality process. |
QC aims to identify (and correct) defects in the finished product. Therefore, quality control is a reactive process. |
Goal |
QA aims to improve development and test processes so that defects do not arise during product development. |
QC aims to identify defects after a product is developed and before it's released. |
How |
Establish a good quality management system and assess its adequacy. Conduct periodic conformance audits of the system's operations. |
Using tools and equipment, we find and eliminate sources of quality problems so that customers' requirements are continually met. |
What |
Prevention of quality problems through planned and systematic activities, including documentation. |
The activities or techniques used to achieve and maintain the product quality, process, and service. |
Responsibility |
Everyone on the team developing the product is responsible for quality assurance. |
Quality control is usually the responsibility of a specific team that tests the product for defects. |
Example |
Verification is an example of QA |
Validation/Software Testing is an example of QC |
Statistical Techniques |
Statistical Tools & Techniques can be applied in both QA & QC. When applied to processes (process inputs & operational parameters), they are called Statistical Process Control (SPC); & it becomes part of QA. |
When statistical tools and techniques are applied to finished products (process outputs), they are called Statistical Quality Control (SQC) and fall under QC. |
As a Tool |
QA is a managerial tool |
QC is a corrective tool |
Orientation |
QA is process-oriented |
QC is product-oriented |
In Sum
As consumers, it's remarkable how we take product safety for granted. Statistically speaking, large product recalls are rare events. Accidents caused by failed quality management systems are more unusual still.
Comprehensive quality management systems are difficult tools to implement and require discipline for any continuous improvements. Perhaps manufacturers aren't altruistic in their goals for QA and QC processes. Yet, we reap the benefits every time we pull the trigger for that new circular saw.