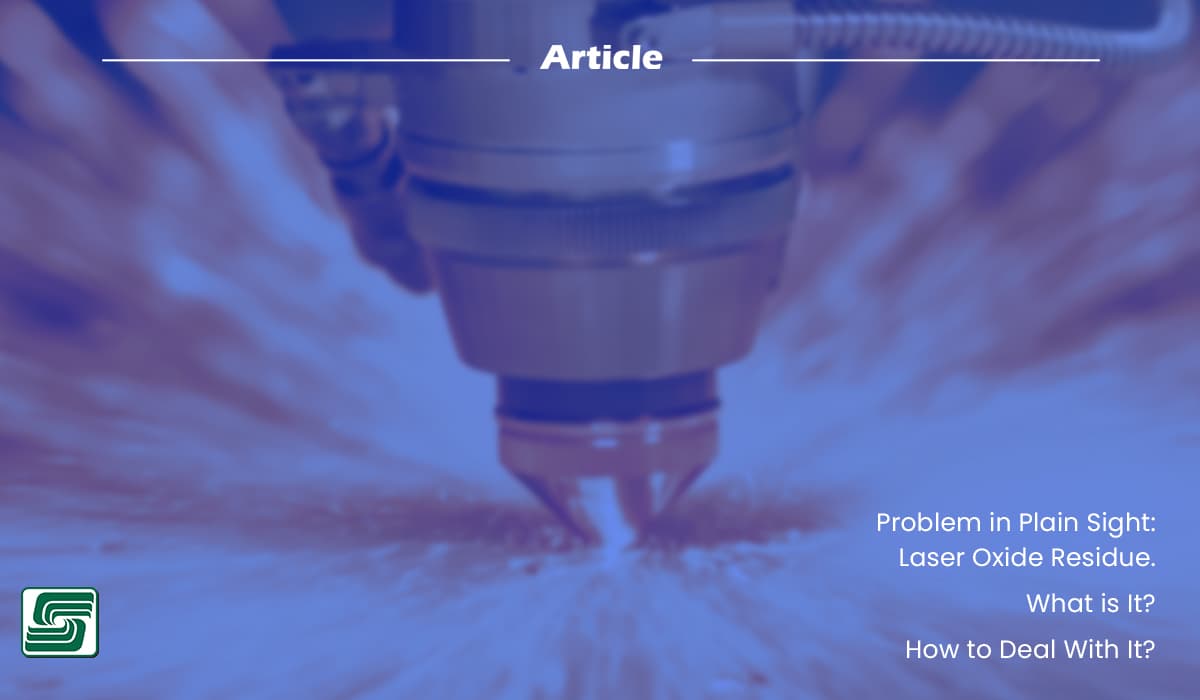
Iron oxide is a chemical compound formed when iron reacts with oxygen. It is commonly known as rust and appears as a reddish-brown powdery substance. Iron oxide residue significantly impacts the cut metal's quality in laser cutting.
Why Does Iron Oxide Matter in Laser Cutting?
When the laser interacts with the metal, it forms an iron oxide residue. This residue affects the precision of the cut and alters the material properties, leading to potential issues with wear and tear.
The laser cutting process involves using a high-powered laser to cut through materials such as metal. The laser beam is focused on the workpiece, melting, burning, or vaporizing the material along the predetermined cut line.
The role of oxygen in laser cutting is crucial. Oxygen serves as an assist gas that aids in the cutting process by creating an exothermic reaction. This reaction generates heat, accelerating the laser's ability to cut through the metal efficiently.
The Science Behind Iron Oxide Formation
A chemical reaction occurs when iron comes into contact with oxygen during laser cutting. This reaction, known as oxidation, leads to the creation of iron oxide residue. Without the presence of oxygen, this reaction cannot occur. Iron oxide is formed when the laser interacts with the metal by combining oxygen molecules and iron atoms.
Factors Influencing Iron Oxide Formation
- Temperature: The temperature within the cutting zone plays a crucial role in forming iron oxide. Higher temperatures speed up oxidation, leading to a more significant residue buildup. The intense heat generated by the laser contributes to this reaction, influencing the amount of iron oxide produced during cutting.
- Cutting Speed: Another factor that influences the formation of iron oxide is the cutting speed. When the laser moves at high speeds through the metal, it creates conditions that promote rapid oxidation. Faster cutting speeds may cause increased iron oxide production, affecting the quality and efficiency of the laser cutting process.
How Iron Oxide Affects Laser Cutting Quality
Iron oxide residue resulting from the laser cutting process significantly impacts the overall quality of the cut metal.
Understanding how this residue affects cutting precision and material properties is crucial for optimizing laser cutting outcomes.
- Cut Edges: The iron oxide residue notably influences the cut edges' quality. As the laser interacts with the metal, the formation of iron oxide may cause irregularities along the cut lines. These irregularities result in rough or uneven edges, affecting the overall precision of the cut. The accumulation of iron oxide also reduces sharpness and smoothness, impacting the final quality of the cut metal pieces.
- Maintaining Accuracy: Iron oxide residue challenges maintaining accuracy during laser cutting processes. The buildup of this residue interferes with the precise execution of cuts, leading to deviations from intended measurements and shapes. Controlling and minimizing iron oxide formation is essential for ensuring that laser-cutting operations maintain high levels of accuracy and consistency.
The Impact on Material Properties
- Material Strength Changes: The presence of iron oxide residue changes the strength properties of the cut metal. As oxidation occurs during laser cutting, it may alter the material's structural integrity, potentially compromising its strength characteristics. This alteration in material strength because of iron oxide formation emphasizes the importance of managing this residue to preserve the structural reliability of cut metal components.
- Potential for Increased Wear and Tear: Iron oxide residue has implications for increased wear and tear on cut metal surfaces. The formation of this residue introduces surface irregularities and weaknesses, making the material more susceptible to wear. These alterations may affect how well components interact with other parts within various applications, potentially impacting their longevity and performance.
Managing Iron Oxide Residue for Better Results
Now that the impact of iron oxide residue on laser cutting processes has been unveiled, it's essential to explore techniques for reducing its formation and effective cleaning and maintenance strategies.
Techniques for Reducing Iron Oxide Formation
- Adjusting Laser Parameters: One effective approach to minimizing the formation of iron oxide is to adjust the laser parameters. Fine-tuning the power levels, pulse duration, and laser focal point helps optimize the cutting process. By carefully calibrating these parameters, the intensity of the laser beam can be controlled, reducing excessive oxidation and mitigating the buildup of iron oxide residue.
- Using Protective Coatings: Another strategy involves using protective coatings on metal surfaces before laser cutting. These coatings act as a barrier between metal and oxygen, inhibiting rapid oxidation during cutting. By applying specialized coatings designed to withstand high-temperature environments, manufacturers effectively minimize the formation of iron oxide, leading to improved cut quality and reduced post-cutting cleanup efforts.
Pre-Wash Systems: A Solution to Laser Oxide Scale
Pre-wash systems offer an effective solution to address the challenges of laser oxide scale in metal fabrication processes. These systems incorporate multi-stage processes, including chemical showers, to remove oxide scale from metal surfaces before further processing.
The benefits of using pre-wash systems are clear: They eliminate the potentially destructive impact of oxide scale exposure to air and moisture, enhancing the quality and durability of fabricated components.
Case studies and examples show the effectiveness of pre-wash systems in efficiently removing oxide scale compared to traditional methods.
These studies include a comparison highlighting the superior results achieved through pre-wash systems, emphasizing their role in elevating the quality of fabricated metal components.
Integrating pre-wash systems into metal fabrication processes requires careful consideration and best practices.
Selecting the right pre-wash system for specific applications involves evaluating material type, component size, and production volume.
In Sum
Recognizing the impact of iron oxide residue in laser cutting processes and prioritizing effective management strategies, manufacturers achieve superior results while upholding the integrity and durability of their cut metal products.