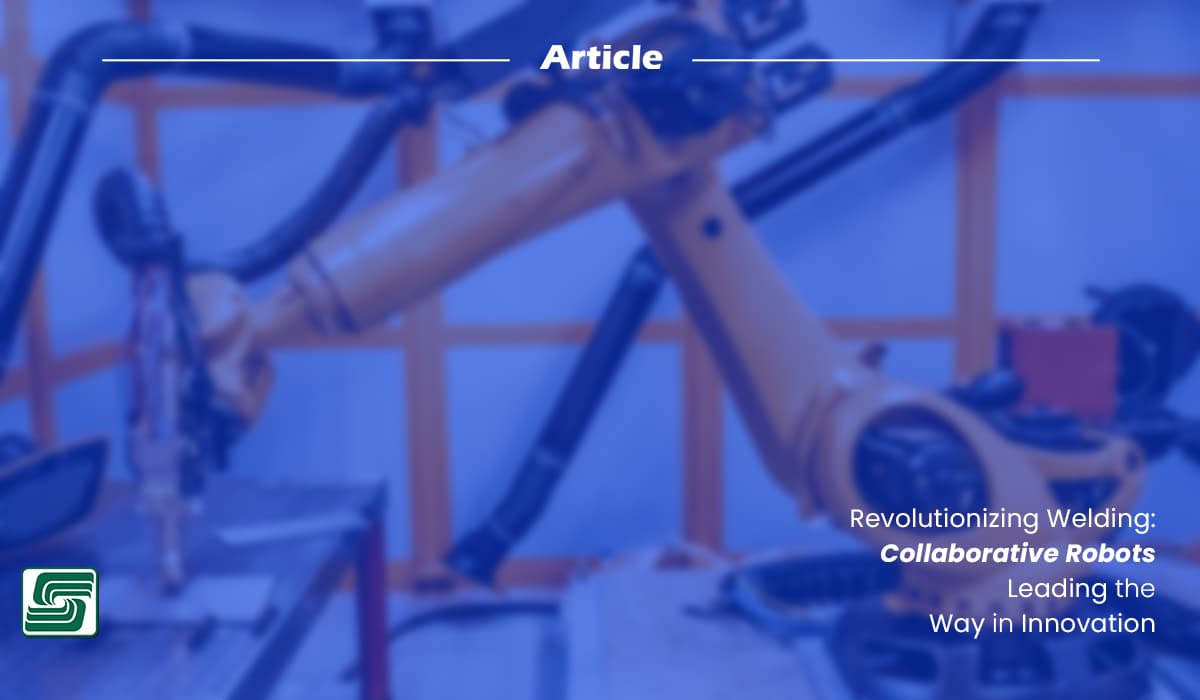
Collaborative welding robots are not just another tool in the welding industry; they are a game-changer. Their introduction marks a shift towards a new era of efficiency and precision in welding processes. These robots, designed for seamless human-robot collaboration, offer a unique perspective on the future of welding technology. The following sections will explore the definition and evolution of collaborative welding robots, emphasizing their unique features and the pivotal role they play in revolutionizing traditional welding practices.
Understanding Collaborative Welding Robots
In welding technology, collaborative welding robots stand out as innovative tools that redefine traditional welding practices. These robots are meticulously designed to work harmoniously with human welders, offering a seamless blend of human expertise and robotic precision.
Definition and Overview
The essence of collaborative welding robots lies in their ability to augment human capabilities with advanced technological prowess. Unlike conventional welding machines, these next-gen robots are equipped with state-of-the-art features that elevate the quality and efficiency of welding processes.
Evolution of Collaborative Welding Robots
The journey of collaborative welding robots has been marked by continuous innovation and refinement. From their inception to today, these robots have undergone significant advancements in functionality and adaptability. Their evolution mirrors the relentless pursuit of excellence within the welding industry.
Key Features
-
Vision Systems: One of the standout features of collaborative welding robots is their sophisticated vision systems. These systems enable the robots to perceive their surroundings with remarkable clarity, facilitating precise and accurate welds on various materials.
-
Safety Features: Safety is paramount in any welding environment, and collaborative welding robots excel. With robust safety protocols and built-in mechanisms, these robots ensure a secure working environment for humans and machines.
-
Sensors: Sensors play a crucial role in enhancing the functionality of collaborative welding robots. By leveraging advanced sensor technology, these robots can adapt to changing conditions in real-time, optimizing their performance for superior weld quality.
Technology Behind Collaborative Welding Robots
AI and Machine Learning Integration
AI and Machine Learning integration are at the core of collaborative welding robots, driving innovation and efficiency in the welding industry. By harnessing the power of artificial intelligence, these robots can analyze vast amounts of data to optimize welding processes. Machine Learning algorithms enable them to continuously improve their performance based on real-time feedback, ensuring unparalleled precision and adaptability.
Precision and Accuracy
Precision and accuracy are paramount in welding applications, and collaborative robots deliver exceptional results. Through advanced programming and next-gen technology, these robots can execute welds with micron-level precision. Their ability to maintain consistent motion and adhere to predefined parameters guarantees flawless welds on many materials, from steel to aluminum.
Human-Robot Collaboration
Human-robot collaboration is not about replacing human workers but about enhancing their capabilities. Collaborative welding robots work alongside skilled welders, not as their replacements but as their partners. They streamline production processes, boost efficiency, and ensure top-notch weld quality. This collaboration is a testament to the irreplaceable role of human workers in the welding industry.
Benefits of Collaborative Welding Robots
Improved Weld Quality
- Achieving impeccable weld quality is the primary aim of collaborative welding robots.
- These robots elevate the quality standards in welding processes to ensure precise and consistent welds.
- By maintaining a steady and controlled motion, collaborative robots produce flawless welds that meet stringent industry requirements.
- Integrating advanced technologies enables these robots to deliver superior weld quality on many materials.
Enhanced Productivity
- Collaborative welding robots help enhance productivity levels within welding operations.
- These robots optimize workflow efficiency by streamlining the welding process through seamless human-robot collaboration.
- Their ability to handle repetitive tasks quickly and accurately significantly boosts overall productivity.
- By automating certain aspects of welding, collaborative robots free up human workers to focus on more complex and strategic tasks.
Cost Efficiency
- Embracing collaborative welding robots translates to substantial cost savings for businesses in the long run.
- The efficiency and precision offered by these robots minimize material wastage, reducing overall production costs.
- With increased productivity and minimized errors, businesses can achieve higher output levels without compromising quality.
- The initial investment in collaborative welding robots is a cost-effective solution for long-term operational success.
Impact on the Welding Industry
Transforming Traditional Welding Practices
Collaborative welding robots are not just tools; they are catalysts for a transformation in traditional welding practices. They usher in a new era of efficiency and precision, integrating next-gen technology with human expertise. These robots redefine the quality and productivity standards in the welding industry, revolutionizing how welding tasks are approached and executed. This is not just a shift; it's a leap into the future of welding technology.
Introducing collaborative robots has streamlined welding processes, making them more efficient and cost-effective. These robots can handle repetitive tasks with unparalleled speed and accuracy, allowing human workers to focus on more intricate aspects of welding. As a result, businesses across various sectors are witnessing a significant improvement in their overall productivity levels.
Adoption in Various Sectors
Adopting collaborative welding robots is not limited to a single sector but spans diverse industries. From automotive manufacturing to shipbuilding, these robots have found applications in sectors where precision and reliability are paramount. Companies that embrace collaborative robot technology benefit from enhanced weld quality, increased production output, and reduced operational costs.
In the automotive industry, collaborative welding robots play a crucial role in ensuring the structural integrity of vehicles through precise and consistent welds. Similarly, these robots contribute to fabricating sturdy structures with superior weld quality in the construction sector. The versatility of collaborative robots allows them to adapt seamlessly to different welding requirements across various sectors.
Case Studies
COBOT Journey Atlas Welding
One notable case study showcasing the impact of collaborative welding robots is the COBOT Journey Atlas Welding project. This initiative exemplifies how innovative cobot technology can elevate traditional welding practices to new heights. By implementing collaborative robots in their welding processes, Atlas Welding Supply Company witnessed a remarkable improvement in weld quality and production efficiency.
Journey Atlas Welding Supply
Another compelling case study is that of Journey Atlas Welding Supply, where the integration of collaborative robot systems revolutionized their approach to welding operations. The partnership between skilled human welders and advanced cobots resulted in a significant reduction in errors and an increase in overall output capacity. This successful collaboration underscores the transformative power of adopting collaborative robot solutions.
Future of Collaborative Welding Robots
Emerging Trends
- Robotics technology continues to advance, paving the way for collaborative welding robots to become even more sophisticated and efficient.
- Integrating artificial intelligence and machine learning algorithms is expected to enhance the capabilities of collaborative welding robots, enabling them to analyze data in real time to optimize welding processes.
- Industry experts predict a surge in the development of collaborative robot applications across various sectors, showing a growing demand for these innovative solutions.
Potential Developments
- Future advancements may focus on enhancing the adaptability and versatility of collaborative welding robots, allowing them to seamlessly integrate into diverse manufacturing environments.
- Innovations in sensor technology could lead to the implementing more advanced sensors in collaborative robots, further improving their ability to perceive and respond to their surroundings with precision.
- The evolution of collaborative robot programming interfaces may simplify the setup and operation of these robots, making them more accessible to a broader range of users.
Industry Predictions
- Experts expect a significant increase in the adoption of collaborative welding robots across industries, driven by their potential to revolutionize traditional welding practices and boost overall productivity.
- As collaborative robot technology continues to evolve, it is projected that these robots will play a pivotal role in streamlining manufacturing processes and meeting the growing demands for high-quality welds.
- The future landscape of the welding industry is poised for transformation with the widespread integration of collaborative welding robots, which will offer businesses a competitive edge through enhanced efficiency and superior weld quality.
In Sum
Collaborative welding robots redefine traditional practices with enhanced efficiency and precision. Their significance lies in their ability to elevate weld quality and productivity in diverse industries.
The prospects for collaborative welding robots are promising, with advancements expected in AI integration and sensor technology.