Building beautiful metal structures brings challenges unique to metal craft. As we’ve explored, exposed metal in a corrosive environment comes at a cost: corrosion.
Fortunately, there are several ways of protecting metal in such harsh and surprisingly not-so-hard, environments, and we’ll touch on those protective measures in this article.
Protective Coatings: the Series
For a more in-depth review of protective metal coatings, I invite you to follow this link to a series of articles we’ve shared. For now, though, here’s a brief look at this industry.
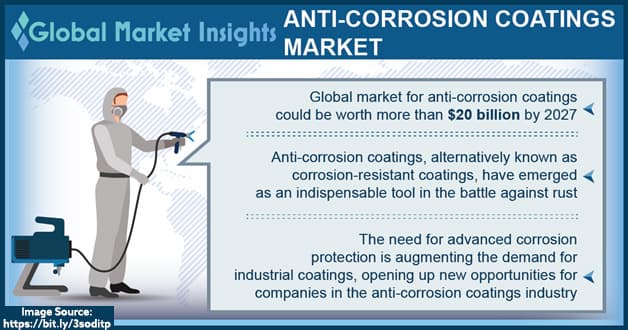
Not Just Ugly on the Surface
Corrosion isn’t just ugly; it’s expensive. Worldwide, it costs an estimated 2.2 trillion dollars each year to control corrosion, roughly 3% of the world’s gross domestic product.
Corrosion isn’t just ugly and expensive; it’s dangerous. It challenges our safety from affected roads, buildings, and bridges. Corrosion prevention becomes an essential aim.
Strategies to Fight Corrosion
There are many ways to fight rust, but for this article, we’ll focus on ten:
- Painting
- Galvanization
- Alloy
- Coating with Oil
- Proper Storage
- E-Coating
- Powder Coating
- Bluing
- Packaging
Painting
Simple paint covers a substrate, but it needs to accomplish more than making it look good. If you know moisture exposure exists, water-based paint is less than ideal. You must also ensure the paint sticks to metal while monitoring areas where a finish exists.
Galvanization
Applying a zinc coating to iron or steel using galvanization is the most common way to protect the metal. Zinc corrodes at a much slower rate than iron and is economically viable.
Alloys
All metal rusts and some metal rusts slower than others. When combining two metals, it creates alloys. The best example of rust protection using an alloy is stainless steel—basically a rust-resistant metal.
Coating with Oil
An oil coating not only lubricates but also protects the metal. Oil creates a protective barrier, preventing moisture from reaching the substrate.
Proper Storage
Storing metal components in a dry or low-moisture environment slows the process of corrosion.
E-Coating
An e-coat is like electroplating, where an electric current is added to epoxy, water-based solution, or paint while dipping the substrate into a bath. The effect is a near-complete bath for the metal, coating hard-to-reach areas.
Powder Coating
Using current to adhere paint powder, followed by curing, creates an extremely tough barrier against moisture.
Bluing
Bluing steel has existed for hundreds of years, the earliest examples in ancient Japanese swords. Bluing steel describes applying a black oxide coating to a metal substrate, resulting in a blue-black appearance of the resulting finish.
VCI Packaging
Vapor corrosion inhibitors (VCI) are chemical compounds that protect metals from rust and corrosion. Infusing VCIs with poly films, chipboard, paper, etc., activates and ‘fill-up’ vapor space inside the packaging, forming a shield of protection displacing moisture. Properly used, VCIs eliminate excess grease or oils, making uncrating components time-consuming.
Each of these methods of protecting metal works well enough on its own. However, there are significant limitations and challenges. Combining any of these processes creates a formidable protective barrier. An e-coat/powder coat combination is one of the most effective barriers to combating corrosion.
In Sum
Combining protective coatings with a good maintenance program certainly is an effective way to combat rust. Corrosion is a natural process that reverses metal to its original state. Rust weakens the metal, endangering people and structures, and protecting metal has become a multi-billion-dollar industry.
There are hundreds of ways to improve the lifespan of metal architecture, and each has its advantages and limitations. Approaching the problem using a holistic approach is the right way to start. Component design and geometry, environmental factors, and metal selection are vital ingredients for a successful and sustainable project.