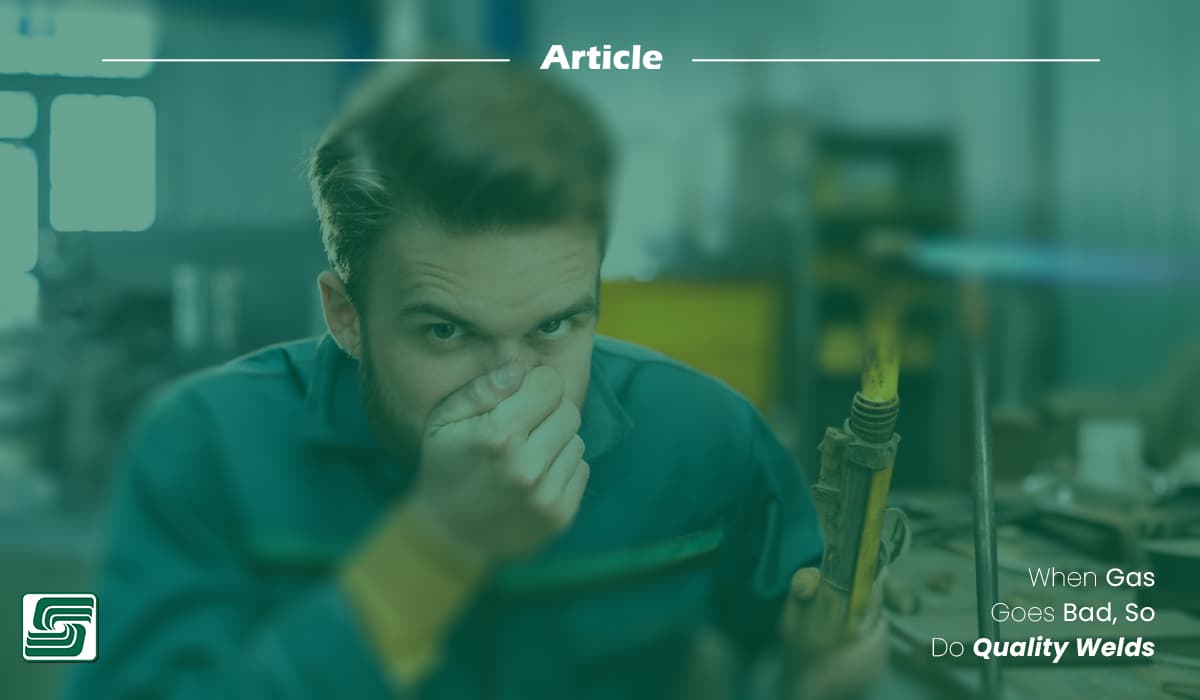
Welding quality holds paramount importance in various industries. Shielding gases play a crucial role in ensuring high-quality welds. These gases create a protective barrier around the weld, preventing exposure to atmospheric gases like oxygen and nitrogen. This blog aims to explore how improper shielding gas affects welding quality.
The Role of Shielding Gas in Welding
What is Shielding Gas?
Definition and Purpose
Shielding gas blocks welding, preventing atmospheric gases such as oxygen and nitrogen from contaminating the weld. This protection ensures that the weld remains strong and free from defects.
Common Types of Shielding Gases
Several types of shielding gases are commonly used in welding:
- Argon: Argon provides a stable arc and effective cleaning action. Welders gain excellent control over the welding arc and puddle.
- Helium: Helium offers high heat input because of its high voltage gradient. It is ideal for applications requiring maximum heat.
- Carbon Dioxide: Carbon dioxide enhances weld penetration because of its high heat conductivity.
- Hydrogen: Hydrogen increases welding speed and compatibility with certain materials. It is valuable for stainless steel welding.
- Oxygen: Oxygen improves welding speed, material soundness, and weld penetration.
How Shielding Gas Protects the Weld
Preventing Oxidation
Shielding gases prevent oxidation by creating a barrier between the weld and atmospheric gases. This barrier stops oxygen from reacting with the molten metal, causing defects such as porosity and weak weld joints.
Stabilizing the Arc
Shielding gases stabilize the welding arc. A stable arc ensures consistent heat distribution and smooth weld bead formation. Argon, for example, provides the most stable arc among shielding gases.
Selection Criteria for Shielding Gas
Material Type
The type of material being welded influences the choice of shielding gas. Argon is suitable for non-ferrous metals, while hydrogen mixtures are recommended for stainless steel.
Welding Process
Different welding processes require specific shielding gases. MIG welding often uses carbon dioxide or argon-carbon dioxide mixtures. TIG welding typically employs inert gases like argon or helium.
Effects of Improper Shielding Gas
Common Issues with Incorrect Shielding Gas
Porosity in Welds
Inadequate shielding gas leads to porosity in welds. Porosity occurs when gas pockets form within the weld metal. These pockets weaken the weld and compromise its structural integrity. Proper shielding gas flow and pressure are crucial to prevent porosity. For example, improper blowing of shielding gas increases weld porosity.
Weak Weld Joints
Weak weld joints often result from inadequate shielding gas. The absence of a protective barrier allows atmospheric gases to contaminate the weld. Contaminants, like oxygen and nitrogen, cause weak weld joints. This contamination reduces the overall strength and durability of the weld.
Visual Defects in Welds
Discoloration
Discoloration is a common visual defect caused by inadequate shielding gas. Exposure to atmospheric gases during welding alters the color of the weld. Discoloration shows oxidation or other chemical reactions, which affect the weld's appearance and quality.
Inclusions
Inclusions refer to foreign materials trapped within the weld. Inadequate shielding gas allows contaminants to enter the weld pool, weakening the weld and leading to defects. Effective shielding gas use minimizes the risk of inclusions.
Long-term Consequences
Structural Failures
Proper shielding gas use can cause structural failures. Weak weld joints and porosity compromise the structural integrity of welded components, leading to catastrophic failures in critical applications.
Increased Maintenance Costs
Inadequate shielding gas increases maintenance costs. Poor weld quality often requires frequent repairs and replacements, which increases operational costs and downtime. Proper shielding gas selection and use helps avoid these expenses.
Case Studies of Shielding Gas Failures
Industrial Accidents
Case Study 1
An automotive manufacturing plant experienced a significant welding failure. The welds on critical components showed signs of porosity and weak joints. Investigations revealed that the shielding gas supply had been compromised. Contaminants entered the weld pool, causing structural weaknesses. The plant faced production delays and increased costs because of necessary repairs. Proper shielding gas management could have prevented this incident.
Lessons Learned
Importance of Proper Training
Proper training ensures that welders understand the significance of shielding gas. Training programs should cover the selection and handling of shielding gases. Knowledgeable welders identify and rectify issues related to shielding gas. Training reduces the risk of welding defects and enhances overall weld quality. Investing in training programs leads to safer and more reliable welding operations.
Implementing Best Practices
Implementing best practices in shielding gas usage is crucial. Regular inspections of gas delivery systems prevent contamination. Monitoring gas flow rates ensures adequate coverage during welding. Using high-quality shielding gases minimizes the risk of defects. Adhering to best practices improves weld integrity and reduces maintenance costs. Consistent application of these practices results in superior welds.
Best Practices for Using Shielding Gas
Proper Gas Selection
Matching Gas to Material
Selecting the appropriate shielding gas depends on the material being welded. Different materials require specific gases to achieve optimal results. For example, argon works well with non-ferrous metals like aluminum and copper. Carbon dioxide suits welding applications involving carbon steel. Helium provides high heat input, making it suitable for thick materials. Hydrogen enhances welding speed and compatibility with stainless steel. Each material demands a tailored approach to shielding gas selection.
Considering Environmental Factors
Environmental conditions influence the choice of shielding gas. High humidity affects gas performance. Welders must consider factors such as wind and temperature. Wind disperses the shielding gas, reducing its effectiveness. In outdoor settings, welders may need to increase gas flow rates. Temperature variations impact gas density and flow. Proper adjustments ensure consistent shielding and high-quality welds.
Equipment Maintenance
Regular Inspections
Regular inspections of welding equipment are crucial. Inspecting gas delivery systems prevents contamination, which compromises weld quality by entering the gas supply. Checking hoses, regulators, and connections ensures proper gas flow. Regular maintenance identifies worn or damaged components. Promptly addressing issues maintains the integrity of the shielding gas system.
Replacing Worn Components
Replacing worn components is essential for effective shielding gas use. Worn-out parts lead to gas leaks and inconsistent flow. Welders should replace hoses, seals, and nozzles regularly. Using high-quality replacement parts ensures reliable gas delivery. Consistent gas flow prevents defects, such as porosity and weak weld joints. Proper maintenance extends the lifespan of welding equipment.
Training and Certification
Importance of Skilled Welders
Skilled welders understand the importance of shielding gas. Proper training equips welders with knowledge about gas selection and handling. Welders are trained to identify and rectify gas-related issues. Knowledgeable welders ensure consistent gas flow and coverage. Skilled welders produce high-quality welds with minimal defects. Investing in training programs enhances overall welding performance.
Certification Programs
Certification programs validate a welder's expertise. They show proficiency in shielding gas and cover various aspects of gas selection and usage. These programs include practical training and theoretical knowledge. Certified welders adhere to industry standards and best practices, ensuring they maintain high-quality welding standards.
Advanced Gas Mixtures
Advanced gas mixtures offer significant benefits in welding. Mixed gases combine the properties of different shielding gases to enhance weld quality. For example, argon-helium mixtures provide both stability and high heat input, improving weld penetration and bead appearance. Mixed gases also reduce spatter and improve arc stability, leading to cleaner and stronger welds.
Applications in Modern Welding
Modern welding processes use advanced gas mixtures for various applications—industries such as aerospace and automotive benefit from these innovations. Mixed gases enable precise control over the welding process, resulting in higher-quality welds with fewer defects. Advanced gas mixtures also support automated welding systems, which require consistent gas flow and composition. Mixed gases ensure optimal performance in these demanding applications.
Automated Gas Delivery Systems
Precision and Consistency
Automated gas delivery systems provide precision and consistency in shielding gas applications. These systems regulate gas flow rates accurately. Precise regulation ensures uniform coverage of the weld area. Consistent gas flow prevents contamination and defects. Automated systems also adjust gas flow based on welding parameters. This adaptability enhances weld quality across different materials and processes.
Reducing Human Error
Automated gas delivery systems reduce human error in welding. Manual adjustments lead to inconsistent gas flow, which increases the risk of weld defects. Automated systems eliminate this variability and maintain optimal gas flow throughout the welding process. Reduced human error leads to more reliable and high-quality welds. Automation also improves efficiency and reduces downtime.
Environmental and Safety Considerations
Environmental Impact of Shielding Gases
Greenhouse Gas Emissions
Shielding gases, such as argon, helium, and carbon dioxide, contribute to greenhouse gas emissions. Carbon dioxide, in particular, has a significant impact on the environment. The production and use of these gases release carbon dioxide into the atmosphere, contributing to global warming and climate change. Reducing the use of carbon dioxide in welding helps mitigate environmental damage.
Eco-friendly Alternatives
Eco-friendly alternatives to traditional shielding gases exist. Nitrogen and hydrogen offer more sustainable options. These gases have a lower environmental impact compared to carbon dioxide. Using eco-friendly gases reduces greenhouse gas emissions. Industries should adopt these alternatives for a greener approach to welding. Implementing eco-friendly practices supports environmental conservation efforts.
Safety Protocols
Handling and Storage
Proper handling and storage of shielding gases are crucial for safety. Welders must store gases in well-ventilated areas, as proper ventilation prevents the buildup of harmful gases. Secure gas cylinders to prevent them from falling or tipping over. Regularly inspect cylinders for leaks or damage. Follow manufacturer guidelines for safe handling procedures. Adhering to these protocols ensures a safe working environment.
Personal Protective Equipment (PPE)
Personal protective equipment (PPE) is essential for welders. PPE includes gloves, helmets, and protective clothing. Gloves protect hands from burns and cuts. Helmets shield the face and eyes from sparks and UV radiation. Protective clothing prevents exposure to heat and molten metal. Wearing appropriate PPE reduces the risk of injuries. Ensuring that welders use PPE enhances overall safety during welding operations.
Aluminum MIG Welding and Shielding Gas
Importance of Shielding Gas in Aluminum MIG Welding
Preventing Oxidation
Shielding gas plays a critical role in preventing oxidation during Aluminum MIG Welding. Oxidation occurs when aluminum reacts with oxygen in the air, forming an oxide layer on the weld. This oxide layer weakens the weld and leads to defects. ARGON creates a protective barrier around the weld pool, pushing away atmospheric gases and preventing oxidation, ensuring the weld remains clean and free from contaminants.
Ensuring Weld Quality
Proper shielding gas selection is essential for achieving high-quality welds in Aluminum MIG Welding. ARGON provides a stable arc and smooth weld bead formation. The stability of the arc ensures consistent heat distribution, which is crucial for welding aluminum. ARGON also helps reduce spatter and improve the weld's overall appearance. Using the right shielding gas enhances the mechanical properties of the weld, ensuring strength and durability.
Common Shielding Gases for Aluminum MIG Welding
Argon
ARGON is the most popular choice for MIG welding aluminum. Pure argon is commonly used for welding up to approximately 12.5mm aluminum sheets. As an inert gas, ARGON remains stable at high temperatures and effectively pushes other gases away from the welding puddle. This stability makes ARGON ideal for MIG welding non-ferrous metals like aluminum, magnesium, and titanium. ARGON provides easier starts with alternating current applications and supports longer welding arcs at low voltages.
Helium
Helium is another common shielding gas used in Aluminum MIG Welding. Helium increases the heat input to the base material, enhancing penetration and improving weld puddle fluidity. When working with aluminum, a combination of argon and helium, with a helium content ranging from 25 to 50 percent, shields both GMAW and GTAW processes. This combination offers the benefits of both gases, providing stability and high heat input. Helium's high voltage gradient makes it suitable for applications requiring maximum heat.
In Sum
Shielding gas plays a critical role in welding. Proper shielding gas selection ensures weld quality and prevents defects. Inadequate shielding gas usage leads to issues like porosity and weak weld joints. Using best practices in shielding gas applications is essential. Continuous learning and proper training enhance welding outcomes. The welding industry must prioritize using shielding gas correctly to maintain high standards.