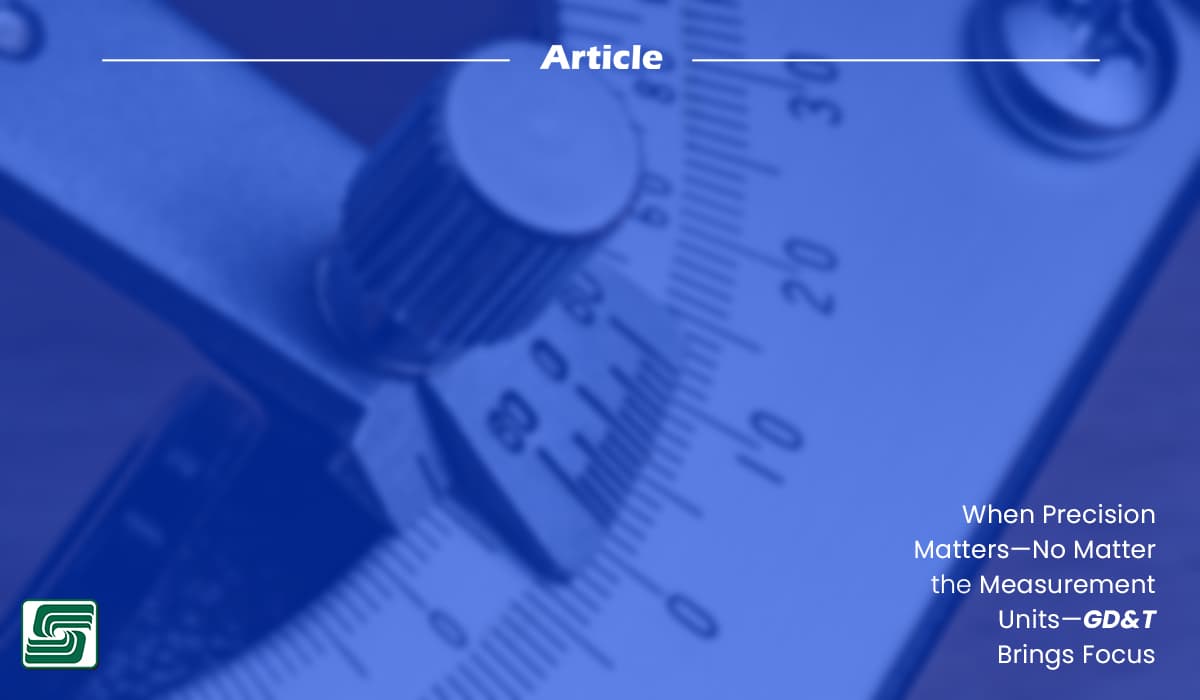
In manufacturing, Geometric Dimensioning and Tolerances. It’s a symbolic language communicating design specifications and tolerances for manufacturing processes. GD&T uses a set of symbols, rules, and definitions to define the allowable variation in form, size, orientation, and location of features on a part.
Why GD&T Matters in Manufacturing
Precision is crucial in the manufacturing industry. Even the smallest deviation from the intended specifications leads to faulty parts or components that don’t fit together. Making things fit is where GD&T shines—providing a clear and standardized way to define and communicate tolerances guarantees that every part produced meets the required specifications with high accuracy.
The Steps of Applying GD&T in Manufacturing
Once the foundational understanding of GD&T and its significance in manufacturing precision is established, the next crucial aspect is to comprehend the steps involved in applying GD&T to the manufacturing process. These three steps ensure the design specifications accurately translate into producing parts and components.
- Step 1: Understanding the Design
- Step 2: Applying GD&T to the Manufacturing Process
- Step 3: Quality Control with GD&T
Step 1: Understanding the Design
Understanding the design is the initial step in applying GD&T in manufacturing. Learning this process involves reading and interpreting GD&T symbols that convey specific geometric dimensioning and tolerancing information.
These symbols are a universal language for communicating precise engineering requirements, including:
- Dimensions
- Tolerances
- Other Technical Specifications
Reading and Interpreting GD&T Symbols
Interpreting GD&T symbols requires a comprehensive understanding of each symbol’s meaning and how it relates to the overall design intent.
Within a part or component, engineers and manufacturers rely on these symbols to determine:
- Critical Features
- Allowable Variations
- Geometric Relationships
Step 2: Applying GD&T to the Manufacturing Process
The next step involves applying GD&T principles to the actual manufacturing process.
This step includes using specialized tools and techniques that enable engineers and machinists to adhere to the specified geometric tolerances during production.
Tools and Techniques for Applying GD&T
Implementing GD&T involves leveraging advanced measurement tools like coordinate measuring machines (CMM) and optical comparators.
Computer-aided design (CAD) software plays a pivotal role in accurately defining geometric dimensions and tolerances before initiating the manufacturing process.
Step 3: Quality Control with GD&T
Incorporating GD&T into manufacturing processes requires a strong emphasis on quality control. This step focuses on checking parts for precision at various stages of production to ensure that they align with the specified geometric tolerances.
Checking Parts for Precision
Inspecting parts for precision involves using precision measurement tools, such as:
- Micrometers
- Calipers
- Height Gauges
These tools enable manufacturers to verify coordinate measuring machines (CMM) enables automotive companies to validate part dimensions accurately, ensuring seamless assembly during vehicle production and contributing to enhanced performance and durability of automotive systems.
Aerospace Industry
The aerospace industry showcases how GD&T plays a crucial role in maintaining precision while manufacturing aircraft components.
The precise standards for safety, reliability, and performance require the precise implementation of geometric dimensioning and tolerancing principles throughout production.
Precision in Airplane Components
From intricate turbine blades to structural airframe elements, each aircraft component undergoes a rigorous process. These components show where GD&T is an example of achieving unparalleled precision.
GD&T ensures dimensional accuracy and plays a pivotal role in maintaining aerodynamic profiles, which are crucial for optimal flight performance.
One remarkable instance is clear in the fabrication of wing assemblies. By applying precise geometric tolerances using GD&T, aerospace manufacturers ensure consistent wing profiles across multiple units.
This level of consistency enhances aerodynamic efficiency and simplifies maintenance and repair operations for airline operators.
Embracing Precision as a Standard
GD&T is a universal language enabling engineers, designers, and manufacturers to communicate precise engineering requirements with clarity and accuracy.
GD&T uses standardized symbols and rules to establish uniformity in:
- Part Dimensions
- Tolerances
- Geometric Relationships
This standardization reduces errors and fosters a culture of precision within the manufacturing processes.
In Sum
Manufacturers integrating GD&T into their processes uphold consistent quality standards across all facets of production.
The precise definition of geometric tolerances safeguards that every part adheres to standardized engineering requirements without compromise.
As a result, customers expect components that consistently meet or exceed quality expectations while enabling seamless interchangeability within assemblies.
Embracing GD&T as an integral part of manufacturing practices empowers professionals to achieve unparalleled precision, consistency, and efficiency while upholding uncompromising quality standards throughout every production stage.