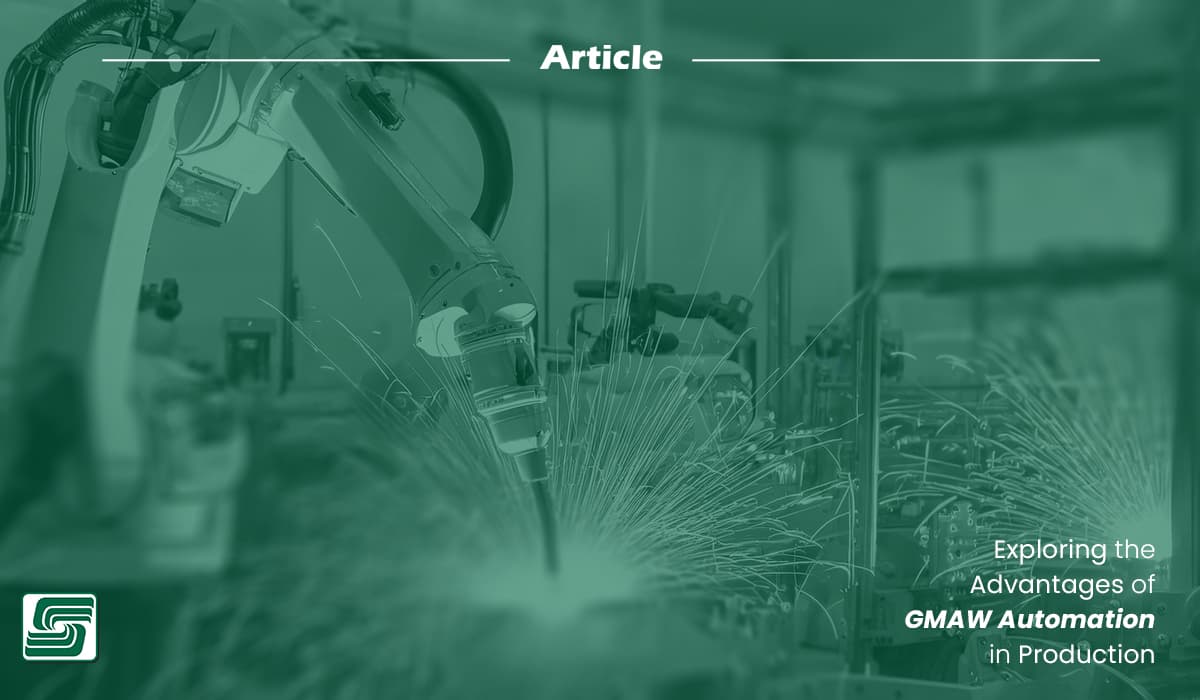
Gas Metal Arc Welding (GMAW) automation revolutionizes modern production by enhancing efficiency and precision. This technology integrates seamlessly into manufacturing processes, offering significant advantages.
Manufacturers increasingly adopt GMAW automation to boost productivity and ensure consistent weld quality while reducing labor costs and minimizing errors, making it indispensable in today's competitive industrial landscape.
Understanding GMAW Automation
Gas Metal Arc Welding (GMAW) is a cornerstone of modern industrial welding. GMAW creates an electric arc between a continuous, consumable wire electrode and the weld pool. The heat generated melts the electrode and the base metal, forming a strong weld.
GMAW is renowned for its speed and versatility, making it a preferred choice in various industries. The process accommodates many materials, including aluminum, stainless steel, and regular steel, with thicknesses ranging from 26-gauge to large structural components.
Key Components
Several key components drive the GMAW process. These include:
- Welding Power Source: Supplies the electrical energy to create the arc.
- Wire Feeding Mechanism: Continuously feeds the consumable wire electrode into the weld pool.
- Protective Gas Feeding Mechanism: Delivers shielding gas to protect the weld from atmospheric contamination.
- Welding Torch: Directs the wire and gas to the weld area.
These components work together to ensure efficient and high-quality welds.
GMAW Welding Automation
Robotics plays a pivotal role in automating GMAW.
Robots:
- Enhance precision and consistency
- Reducing human error
- Increasing production rates
Robotic GMAW systems easily perform complex welding tasks thanks to advanced control systems. They often integrate features like joint tracking and positioning systems, further improving accuracy.
This automation allows manufacturers to achieve high deposition rates, making it ideal for large-scale industrial operations.
Production Line Integration
Integrating GMAW automation into production lines offers many benefits.
- Automated systems streamline the welding process, ensuring seamless operation within manufacturing environments.
- They work alongside other automated systems, such as material handling robots and turntables, to optimize workflow.
- This integration boosts productivity and enhances the overall efficiency of production lines.
By adopting GMAW automation, manufacturers meet the demands of modern industrial production, ensuring consistent weld quality and reduced downtime.
GMAW in Production Automation
Feature |
Advantages |
Benefits |
Versatility |
Capable of welding a wide range of metals and thicknesses. |
Can handle diverse production requirements, reducing the need for multiple welding processes. |
Productivity |
High deposition rates and fast travel speeds. |
Increases production efficiency and reduces cycle times. |
Portability |
Can be used in various environments, including outdoors and confined spaces. |
Offers flexibility in production setups and reduces the need for specialized welding areas. |
Cost-Effectiveness |
Relatively low equipment costs and consumable expenses. |
Contributes to lower production costs and improves profitability. |
Joint quality |
Produces strong, reliable welds with good penetration. |
Ensures product quality and durability. |
Automation Capabilities |
Easily adaptable to automated welding systems. |
Enables consistent, high-quality welds with minimal operator intervention. |
The Role of MIG Welding in Automation
MIG Welding Robots have transformed the landscape of industrial welding. Several versions of these robots are available, each designed to meet specific production needs.
- Articulated Robots offer flexibility with their multiple joints, allowing them to reach complex angles.
- Gantry Robots provide stability and precision, ideal for large-scale projects.
Each type of MIG Robot enhances the efficiency of welding processes by minimizing human error and ensuring consistent weld quality. MIG welding robots have transformed the landscape of industrial welding.
Industry Applications
MIG welding robots find applications across diverse industries.
- Automotive Industry: assembles vehicle frames with precision.
- Aerospace Industry: constructs aircraft components, where accuracy is paramount.
- Construction Industry: builds robust structures.
By integrating MIG welding robots, industries achieve higher productivity and maintain superior product quality. Automating MIG welding increases production and ensures a safer workplace by reducing human exposure to hazardous environments.
MIG Cobot Integration
Collaborative robots, or Cobots, have emerged as a game-changer in welding. Unlike traditional robots, Cobots:
- Work alongside human operators, enhancing flexibility and safety.
- Adapt to various tasks, making them suitable for small and medium-sized enterprises.
- Weld fast, improving production timelines without compromising quality.
Their ability to collaborate with humans allows for more efficient workflows, as they handle repetitive tasks while skilled workers focus on complex operations.
MIG Cobots Benefits
Integrating MIG Cobots offers many benefits, including:
- Reduce Labor Costs: Cobots reduce labor costs by performing tasks that would otherwise require multiple workers.
- Improve Weld Quality: Cobots improve weld quality by maintaining consistent speed and precision.
- Enhance Workplace Safety: Cobots enhance workplace safety by minimizing human exposure to welding fumes and reducing the risk of accidents.
- Speed: Cobots weld fast, increasing production rates and meeting tight deadlines.
Efficiency Improvements with GMAW Automation
GMAW automation significantly boosts welding speed. Automated systems perform tasks faster than manual methods, reducing production time.
Benefit |
Description |
Increased Efficiency |
Faster welding speeds, Reduced production time, Enhanced productivity |
Consistent Weld Quality |
Quality Minimized human error, Uniform welds, Improved weld integrity, Reduced waste |
Reduced Downtime |
Automated maintenance alerts, Predictive maintenance, Quick changeovers |
Precision and Accuracy |
Minimized human error, Computer vision-based tracking (precision within ±0.3 mm), Reduced errors and waste |
Improved Weld Integrity |
Consistent penetration and fusion, Reduced defects and rework |
Cost Benefits of GMAW Automation
GMAW automation offers significant benefits in terms of labor efficiency and cost reduction.
- Reduced reliance on manual labor: GMAW automation decreases the need for skilled welders.
- Efficient allocation of human resources: Companies focus their workforce on more complex tasks.
- Decreased labor costs: Automation leads to lower labor expenses.
- Enhanced productivity: Automated systems perform tasks faster and more efficiently than manual methods.
By automating repetitive welding tasks, manufacturers free up their skilled workforce to focus on more strategic and value-adding activities, ultimately improving overall productivity and competitiveness.
Workforce Reallocation
GMAW automation enables a strategic reallocation of the workforce.
- Upskilling of employees: Workers previously engaged in manual welding can transition to roles requiring critical thinking and problem-solving skills.
- Enhanced workforce dynamics: This reallocation fosters a more dynamic and skilled workforce.
- Business growth: A more skilled workforce can contribute to overall business growth.
- Improved operational efficiency: Companies benefit from having people oversee automated systems, troubleshoot issues, and innovate processes.
Material Savings
GMAW automation optimizes consumables, such as wire electrodes and shielding gases. Automated systems control the welding process, ensuring materials are used efficiently.
This precision minimizes waste and reduces the overall consumption of consumables.
As a result, manufacturers experience cost savings and contribute to more sustainable production practices.
Waste Reduction
GMAW automation offers significant benefits in terms of material waste reduction.
- Reduced defects: Automated systems produce high-quality welds with minimal defects.
- Decreased rework and scrap: Consistent welding parameters minimize the need for rework and scrap.
- Cost savings: Reduced waste leads to substantial cost savings.
- Environmental sustainability: Waste reduction aligns with environmental goals, making GMAW automation an attractive option for eco-conscious manufacturers.
GMAW automation improves profitability by reducing material waste and contributes to a more sustainable manufacturing process.
Safety Improvements in Welding
Automation in welding significantly enhances safety by reducing workers' exposure to hazardous fumes. Robotic systems perform tasks in environments that may pose risks to human health.
By taking over these duties, robots minimize inhaling harmful gases and particles. This shift protects workers and aligns with stringent occupational safety standards. As a result, automated welding processes contribute to healthier workplaces.
Reducing Accident Risk
Robotic welding systems also play a crucial role in minimizing workplace accidents. They operate in conditions that might be dangerous for human welders, such as:
- Extreme Heat
- Noise
- Weld Flash
By handling these tasks, robots reduce the likelihood of injuries associated with manual welding. This reduction in risk leads to safer working environments and fewer incidents.
Manufacturers benefit from decreased downtime and improved worker morale.
Ergonomic Benefits
Automation in welding eases the physical strain experienced by workers.
- Robotic systems take on repetitive and labor-intensive tasks, allowing human operators to focus on supervision and quality control.
- This shift reduces the physical demands placed on workers, leading to fewer musculoskeletal injuries.
By minimizing the need for strenuous manual labor, automation promotes long-term health and well-being among employees.
Improved Working Conditions
Integrating automation in welding processes results in improved working conditions.
- Robots handle tasks in hazardous environments, enabling human workers to operate in safer and more comfortable settings.
- This transition enhances job satisfaction and productivity. Automated systems maintain consistent quality, reducing the stress associated with error correction and rework.
Overall, automation fosters a more positive and efficient workplace atmosphere.
Scalability and Flexibility in Production
In the fast-paced world of manufacturing, adaptability is crucial.
- Automated GMAW systems offer easy reprogramming capabilities, allowing manufacturers to swiftly adjust to new tasks.
- This flexibility ensures production lines quickly adapt to changing demands without significant downtime.
Manufacturers tackle different applications by reprogramming robots, enhancing their ability to meet market needs efficiently.
Handling Diverse Product Lines
Manufacturers often deal with diverse product lines, each requiring specific welding processes.
- Automated systems excel in handling this diversity, seamlessly switching between welding tasks and ensuring consistent quality across various products.
- This capability boosts productivity and allows manufacturers to maintain high standards, regardless of the complexity or variety of their product offerings.
Expansion Capabilities
Scalability is a key advantage of GMAW automation.
- Automated systems integrate smoothly with existing production setups, allowing manufacturers to expand their operations without overhauling their infrastructure.
- This integration ensures that new automated systems work together with current equipment, optimizing workflow and minimizing disruptions.
As a result, manufacturers scale their production capabilities to match growing business demands.
Future-Proofing Production
Future-proofing production is essential in today's ever-evolving industrial landscape.
- Automated GMAW systems provide this assurance by offering flexibility and adaptability.
- These systems accommodate future technological advancements, ensuring that manufacturers remain competitive.
By investing in automation, companies prepare for future challenges, secure their position in the market, and ensure long-term success.
GMAW Automation Environmental Impact
GMAW automation significantly reduces energy consumption in welding processes.
- Automated systems operate with precision, ensuring that energy is used efficiently. These systems minimize the time and resources needed for each weld, leading to lower energy usage.
- This efficiency not only cuts costs but also lessens the environmental footprint of manufacturing operations.
By optimizing energy use, GMAW automation supports sustainable production practices.
Using Sustainable Practices
Manufacturers increasingly adopt sustainable practices in GMAW automation. These practices include using energy-efficient equipment and implementing eco-friendly technologies.
- Automated systems often incorporate features that reduce emissions and waste.
- For example, they may use advanced control systems to optimize gas flow, minimizing the release of harmful substances.
Manufacturers contribute to environmental conservation by integrating sustainable practices while maintaining high production standards.
Waste Management
GMAW automation excels in minimizing scrap during welding.
- Automated systems maintain consistent welding parameters, reducing the likelihood of errors and defects. This consistency leads to fewer rejected parts and less material waste.
- Manufacturers reduce the scrap generated by producing high-quality welds, resulting in cost savings and a smaller environmental impact.
Efficient waste management aligns with the goals of sustainable manufacturing.
Recycling and Reuse Initiatives
Recycling and reuse initiatives play a crucial role in the environmental strategy of GMAW automation.
- Manufacturers implement programs to recycle materials like metal scraps and consumables. Automated systems facilitate these initiatives by producing uniform and predictable waste streams.
- This predictability makes it easier to sort and recycle materials effectively.
By embracing recycling and reuse, manufacturers reduce their reliance on raw materials and promote a circular economy, benefiting both the environment and their bottom line.
How MIG Welding Speed Affects Production
High welding speeds serve as a beacon of efficiency in modern production. They significantly impact production timelines by reducing the time required to complete welding tasks.
- When manufacturers maximize welding speed, they meet tight deadlines and increase output. However, balancing speed and quality remains crucial.
- Welding speed is often critical for production profitability and weld quality. This balance ensures that, while production accelerates, the integrity of the welds remains uncompromised.
- High welding speed paired with precision transform production processes. It allows manufacturers to leverage robotic welding speed to maintain consistent quality across large volumes.
- This consistency is vital in industries where precision and reliability are paramount.
By optimizing welding speeds with beacon-like precision, manufacturers enhance their competitive edge in the market.
Set The Welding Speed
Setting the welding speed involves considering several factors, such as:
- Material Type
- Thickness
- Desired Weld Quality
For instance, thicker materials may require slower speeds to ensure proper penetration, while thinner materials benefit from faster speeds to prevent burn-through.
- Manufacturers must carefully set the welding speed to match these variables, ensuring optimal results.
Optimizing for different materials requires an understanding of their unique properties. Aluminum, for example, demands a different approach compared to stainless steel.
- Manufacturers consistently achieve high-quality welds by tailoring the welding speed to each material.
This optimization enhances product quality and reduces waste and rework, contributing to overall efficiency.
In Sum
Understanding how MIG welding speed affects production is essential for manufacturers aiming to maximize efficiency and quality. They achieve superior results by setting the welding speed appropriately and balancing it with quality.
When optimized, high welding speeds become a beacon of productivity, guiding manufacturers toward success in a competitive market.
GMAW automation offers many advantages to production. It enhances welding speed, ensuring consistent quality and efficiency.
Automated systems reduce labor costs and minimize errors, making them essential in modern manufacturing.
By adopting automation, manufacturers improve productivity and maintain high standards.
The future of automated welding looks promising, with technological advancements driving further improvements.
Embracing these innovations allows industries to stay competitive and meet the demands of a rapidly evolving market.