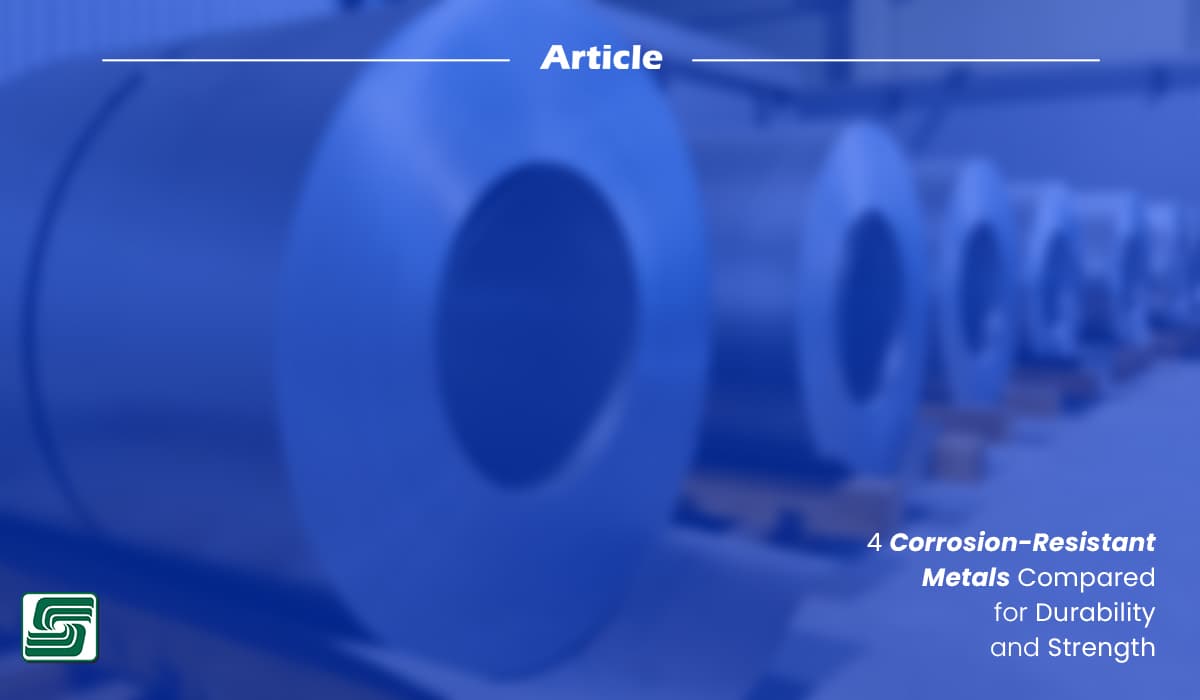
Corrosion is a pervasive and costly issue that affects various industries and infrastructures worldwide. The global cost of corrosion is staggering, estimated to be US $2.5 trillion, equivalent to 3.4% of the global GDP. This significant financial burden underscores the importance of addressing corrosion through effective measures and materials.
According to data from the Financial Times, corrosion in its many forms is estimated to cost the global economy $3 trillion annually because of damage to steel buildings and infrastructure. A study from the University of Edinburgh revealed that corrosion and wear cost the UK approximately £80 billion annually.
NACE International conducted a global study on corrosion costs, estimating that the global cost of corrosion accounts for approximately 3.4% of the global GDP. Despite these alarming figures, governments and industries often pay little attention to corrosion, except in high-risk areas such as aircraft and pipelines.
The call for corrosion professionals to join forces in educating industry stakeholders, harmonizing standards and practices, as well as communicating and sharing corrosion mitigation technologies is crucial in addressing this widespread issue.
In this blog post, we compare four prominent metals and aim to provide valuable insights into their respective strengths in resisting corrosion.
- Stainless Steel
- Aluminum
- Copper
- Titanium
Understanding these materials' unique properties can aid industries in making informed decisions when selecting materials for various applications.
Why does material choice play a pivotal role in combating corrosion effectively?
Why Material Matters in Fighting Corrosion
Corrosion is a natural process when metal is exposed to environmental factors such as moisture, oxygen, and chemicals. The result is the gradual deterioration of the metal, leading to structural weakness and potential failure. This phenomenon affects various industries, including construction, transportation, and manufacturing. The consequences of corrosion can be dire, ranging from safety hazards to significant financial burdens.
How the Right Material Can Make a Difference
Selecting the correct material is critical in effectively combating corrosion resistance. Each metal possesses unique properties that determine its ability to withstand corrosion. Chemical composition, protective coatings, and environmental suitability are crucial in determining a material's effectiveness in resisting corrosion.
When addressing material matters in fighting corrosion, it's essential to consider the specific environmental conditions the metal will be exposed to. For instance, stainless steel excels in environments with high moisture content because of its chromium content, which forms a protective oxide layer on the surface. Aluminum's lightweight nature and natural oxide layer make it ideal for applications requiring strength and corrosion resistance.
Stainless Steel: A Champion in Corrosion Resistance
Stainless steel is renowned for its exceptional corrosion resistance and durability, making it a champion in various industries. The key to its remarkable performance lies in the presence of chromium, an essential alloying element that enhances its resistance to corrosion.
High-strength corrosion-resistant stainless steel alloys typically contain 17 to 28% chromium (Cr), significantly contributing to their ability to withstand harsh environmental conditions.
Stainless steel often incorporates varying proportions of nickel, molybdenum, and nitrogen to further enhance its corrosion resistance properties.
These elements play a crucial role in forming a protective passive film on the surface of the metal, effectively shielding it from corrosive agents such as chloride ions and sulfuric acid.
Stainless steel's unique composition and microstructure enable it to exhibit superior mechanical properties while maintaining its corrosion resistance.
This combination of strength and durability makes it an ideal choice for applications where both structural integrity and protection against corrosion are paramount.
The Role of Chromium
Chromium is the cornerstone of stainless steel's corrosion resistance. When exposed to oxygen, it forms a stable oxide layer on the metal's surface.
This oxide layer acts as a barrier, preventing further oxidation and corrosion.
Chromium enhances the material's high-temperature strength and oxidation resistance, making stainless steel suitable for elevated-temperature applications.
Applications in Everyday Life
Stainless steel's versatility extends across many everyday applications because of its exceptional corrosion resistance properties.
From kitchen utensils and appliances to architectural structures and medical equipment, stainless steel ensures longevity and reliability.
Its use in food processing equipment is noteworthy because of its non-reactive nature, ensuring hygiene and safety in food handling processes.
Comparing Stainless Steel to Other Metals
Compared with other metals renowned for their corrosion resistance, such as aluminum, copper, and titanium, stainless steel stands out for its balanced combination of strength, durability, and chemical stability.
While aluminum offers lightweight corrosion protection, and copper boasts natural antimicrobial properties, stainless steel provides comprehensive corrosion resistance across diverse environmental conditions.
Aluminum: Lightweight and Rust-Resistant
Aluminum is renowned for its exceptional corrosion resistance and lightweight properties, making it a highly sought-after material in various industries. Its ability to withstand corrosion without additional coatings sets it apart from many other metals.
The Benefits of Aluminum in Corrosion Resistance
Its natural oxide layer is one key factor contributing to aluminum's corrosion resistance. When exposed to oxygen, aluminum forms a thin but robust oxide layer on its surface, effectively shielding it from corrosive elements.
This protective layer acts as a barrier, preventing further oxidation and corrosion. As a result, aluminum can be used with no coating in most environments, making it an ideal choice for applications where weight reduction and durability are essential.
Where You'll Find Aluminum
Aluminum's versatility extends across many industries because of its exceptional corrosion resistance and lightweight nature. It is widely used in aerospace engineering for aircraft components, where its strength-to-weight ratio plays a pivotal role in enhancing fuel efficiency and overall performance. Aluminum finds extensive use in automotive manufacturing for body panels and structural components, contributing to improved fuel economy and reduced emissions.
Aluminum vs. Other Corrosion-Resistant Metals
When comparing aluminum with other corrosion-resistant metals such as stainless steel, copper, and titanium, several key differences emerge:
- Aluminum's Purity: Aluminum's resistance to corrosion increases as its purity increases. Pure aluminum exhibits the best corrosion resistance naturally but may experience compromised quality when alloys are added.
- Malleability and Ductility: Aluminum is more malleable and ductile than stainless steel, offering greater flexibility in shaping and forming processes.
- Corrosion Resistance of Alloys: While pure aluminum shows excellent corrosion resistance, certain alloys may not exhibit the same exceptional properties. Alloys of the 2XXX series and 7XXX series have lower corrosion resistance than pure aluminum.
Copper: The Ancient Metal with Modern Resistance
Copper, an ancient metal revered for its versatility and durability, possesses a natural ability to resist corrosion, making it a valuable choice in various industries. Its inherent corrosion resistance stems from forming a protective patina over time, which shields the metal from environmental degradation.
The Patina Effect
One of copper's most remarkable attributes is its propensity to develop a patina—a greenish film—over its surface as it reacts with atmospheric elements. This patina is a protective layer, significantly extending the lifespan of copper components exposed to outdoor conditions. The development of this patina not only enhances the aesthetic appeal of copper structures but also reinforces their resistance to corrosion, ensuring long-term durability.
Copper in Architecture and Plumbing
In architecture, copper has been used for centuries because of its exceptional corrosion resistance and timeless aesthetic appeal. From iconic domes and spires to intricate façades and roofing systems, copper has adorned some of the world's most renowned structures. It is a testament to its enduring strength and resilience against environmental factors.
Copper's corrosion-resistant properties have made it an indispensable material for conveying water and gas in plumbing applications. Its reliability in withstanding corrosive elements ensures the integrity of plumbing systems over extended periods, reducing maintenance requirements and enhancing overall safety.
Copper Compared to Modern Metals
When comparing copper with modern metals such as stainless steel, aluminum, and titanium in terms of corrosion resistance, several distinct characteristics emerge:
- Durability: Copper's natural patina protects against corrosion without compromising its structural integrity.
- Aesthetic Appeal: The development of the greenish patina adds an elegant touch to architectural designs while serving as a robust defense mechanism against corrosion.
- Applications: While stainless steel excels in street furniture construction because of its remarkable resistance to corrosion and rust, copper is widely used in architectural ornamentation and plumbing systems for its unique blend of functionality and aesthetics.
Titanium: The Strong and Corrosion-Resistant Metal
Titanium, known for its exceptional strength and corrosion resistance, is a highly sought-after metal in various industrial applications. Its unique properties make it an ideal choice for demanding environments where durability and reliability are paramount.
Exceptional Strength and Durability: Why Titanium Stands Out
One of titanium's most remarkable attributes is its exceptional strength-to-weight ratio, surpassing that of stainless steel and aluminum. This inherent strength and its lightweight nature make titanium a preferred material in aerospace engineering, where structural integrity and fuel efficiency are critical considerations. Titanium's impressive tensile strength and corrosion resistance render it indispensable in marine applications, where it withstands the harsh conditions of seawater without succumbing to corrosion.
Uses of Titanium in High-End Applications
The aerospace industry extensively uses titanium because of its unparalleled strength and corrosion resistance. From aircraft components to spacecraft structures, titanium enhances performance while ensuring longevity in extreme operating conditions. The medical field benefits from titanium's biocompatibility and resistance to bodily fluids, making it an ideal choice for surgical implants, orthopedic devices, and dental fixtures.
Titanium's Place Among Corrosion-Resistant Metals
When evaluating titanium alongside other corrosion-resistant metals such as stainless steel, aluminum, and copper, several distinguishing factors come to light:
- Biocompatibility: Titanium's biocompatibility makes it a preferred choice for medical implants compared to stainless steel or copper because it integrates seamlessly into the human body without triggering adverse reactions.
- High-Temperature Stability: In high-temperature environments where traditional metals may falter because of oxidation or thermal degradation, titanium maintains its structural integrity and corrosion resistance.
- Aerospace Applications: While aluminum offers lightweight properties suitable for aerospace applications, titanium surpasses it in terms of overall strength and resilience against corrosive elements.
Giving These Metals Some Help
The significance of material selection in combating corrosion cannot be overstated. The choice of metals for various applications plays a pivotal role in ensuring the reliability and efficiency of systems while safeguarding against potential hazards caused by corrosion. This is crucial as the material property of corrosion resistance is one of the most important factors in practical applications and determines the lifetime of each product.
Corrosion-resistant coatings also emerge as a workable alternative to selecting exotic materials for achieving asset integrity and service life. Choosing the optimal corrosion-resistant coating requires a comprehensive evaluation of various factors, including the operating environment, substrate material, application method, and desired longevity.
Material science offers corrosion engineers design options in corrosion control with advanced materials.Engineered properties created through specialized processing and synthesis technologies give advanced materials superior performance over conventional materials. This presents an opportunity for industries to leverage innovative materials that offer enhanced durability and resistance to corrosion.
The evidence supporting these conclusions is compelling. Corrosion of engineering materials has been a significant problem in industrial conditions, often causing substantial economic losses and catastrophic damage to technical facilities. Therefore, industries must prioritize material selection based on their specific environmental requirements and operational demands.
Addressing corrosion through strategic material selection mitigates financial burdens and ensures the safety and longevity of critical infrastructure across diverse sectors. By understanding the unique properties of metals such as stainless steel, aluminum, copper, and titanium, industries can make informed decisions that contribute to sustainable operations and long-term asset preservation.
In Sum
Ultimately, proper material selection plays a vital role in ensuring the reliability and efficiency of systems while safeguarding against potential hazards caused by corrosion. As industries continue to innovate and advance in material science, the fight against corrosion will undoubtedly benefit from proactive measures grounded in informed decision-making.
By embracing advancements in materials technology and adopting proactive strategies for combating corrosion, industries can enhance sustainability, safety, and operational excellence.