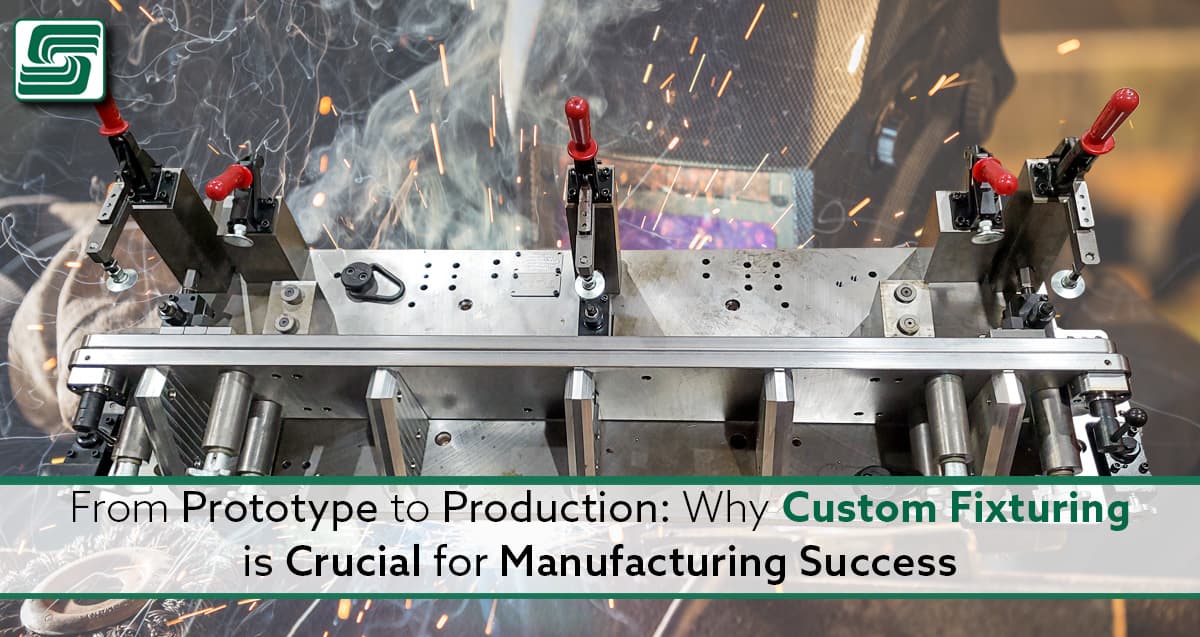
Manufacturing is a complex process that requires precision, attention to detail, and the right tools to produce high-quality products. One of the critical components of the manufacturing process is custom fixturing, and fixtures are essential tools that hold and position parts and components during manufacturing.
Custom fixturing, in particular, is an integral part of the production process as it ensures the accurate placement of the manufactured parts as an important part of an efficient manufacturing process.
Understanding Custom Fixturing in Manufacturing
Custom fixturing is designing and building fixtures tailored to the specific needs of a manufacturing process that hold parts and components in place during production, holding them in place accurately and securely.
Using custom fixturing can significantly improve the efficiency and accuracy of the manufacturing process. Rather than using a one-size-fits-all approach, custom fixturing considers the unique needs of a particular manufacturing process, resulting in a more streamlined and efficient process.
Many manufacturing processes use custom fixtures, from automotive to aerospace and everything in between. It is useful in high-volume manufacturing processes, where precision and efficiency are critical.
Benefits of custom fixturing
Custom fixturing has many benefits—increasing efficiency is one of the most significant. Manufacturers reduce the time to produce a part or component using custom fixtures, resulting in a more streamlined and efficient manufacturing process.
Benefits of custom fixturing include:
- Increased efficiency
- Accurate and secure holding of parts
- Improved quality control
- Higher-quality products and greater customer satisfaction
- Greater flexibility in the manufacturing process
- Customized fixtures tailored to the specific needs of a manufacturing process
- Quick and easy adaptation to changes in demand or design
Importance of Precision in Manufacturing
Precision is critical in manufacturing—the slightest deviation results in a defective product. Custom fixturing is essential in ensuring that parts and components are held accurately and securely during manufacturing, helping to minimize the risk of errors and defects and ensuring that the final product meets the specifications.
Besides ensuring precision in the manufacturing process, custom fixturing reduces waste. By holding parts and components in the correct position during production, manufacturers reduce the likelihood of errors and defects, resulting in less waste and a more environmentally friendly manufacturing process.
Types of Custom Fixtures and Their Uses
There are many different types of custom fixtures, each designed to meet the unique needs of a particular manufacturing process. Each type of custom fixture has its unique uses and benefits.
Some of the most common types of custom fixtures include:
- Jigs: Jigs hold and guide tools during drilling and milling operations.
- Fixtures: Fixtures hold parts in place during high-volume manufacturing processes.
- Gauges: Gauges measure the accuracy of parts and components, and quality departments use them to ensure that parts meet the intended specifications.
- Chucks: Chucks hold round or cylindrical parts, often used in lathing operations.
- Clamps: Clamps hold parts in place during welding and assembly operations.
Manufacturers must select the right type of fixture for their specific needs to achieve the desired results.
Designing Custom Fixtures
Designing custom fixtures for a manufacturing process requires a thorough understanding of the process and the manufactured parts.
- Identify the specific needs of the manufacturing process
- Understand the dimensions and tolerances of the manufactured parts
- Consider the specific tools and equipment used in the process
- Design the custom fixtures
- Create a detailed plan considering the unique needs of the manufacturing process
- Include detailed drawings and specifications for the fixtures
- Develop a timeline for the construction of the fixtures
- Build the fixtures
- Use specialized equipment and materials
- Skilled, experienced technicians in fabricating custom fixtures may be required
- Test the fixtures to ensure they meet intended specifications and perform as expected
Once built, the technicians must test the fixtures to ensure they meet the intended specifications and perform as expected.
Custom Fixturing Improves Quality
Custom fixturing can significantly improve the quality of products by ensuring that parts and components are held accurately and securely during the manufacturing process reducing the likelihood of errors and defects in the final product. Custom fixtures also allow for greater precision and consistency in the manufacturing process, resulting in higher-quality products.
In addition to improving the quality of products, custom fixturing can also help improve the manufacturing process's efficiency. By holding parts and components in the correct position during production, manufacturers can reduce the time it takes to produce a part or component, resulting in a more streamlined and efficient process.
The Cost-Effectiveness of Custom Fixturing
Although the initial investment in custom fixturing can be significant, the long-term cost-effectiveness of custom fixturing makes it a worthwhile investment for manufacturers.
Manufacturers can reduce the time it takes to produce a part or component by using custom fixtures, resulting in a more streamlined and efficient manufacturing process reducing the overall cost of production, and can result in significant savings over time.
In addition to reducing the cost of production, custom fixturing can also help to reduce waste and improve the quality of products, resulting in greater customer satisfaction and increased revenue.
Overcoming Common Challenges in custom fixturing
Custom fixturing can be a complex process, and there are many challenges that manufacturers may face when designing and building custom fixtures. Some of the most common challenges include:
- Design challenges: Designing custom fixtures requires a thorough understanding of the manufacturing process and the specific needs of the process. Manufacturers may face challenges in designing fixtures that meet the unique needs of their process.
- Cost challenges: The initial investment in custom fixturing can be significant, and manufacturers may face challenges in finding cost-effective solutions that meet their specific needs.
- Time challenges: Designing and building custom fixtures can be time-consuming, and manufacturers may face challenges meeting tight production deadlines.
To overcome these challenges, manufacturers should work with experienced custom fixturing providers who can help to design and build fixtures that meet their specific needs.
Custom fixturing providers can also help to ensure that the fixtures are built on time and within budget, reducing the impact on production schedules.
In Sum
Custom fixturing is a crucial component of the manufacturing process. It ensures parts and components are held accurately and securely during manufacturing, resulting in higher-quality products and greater customer satisfaction.
Custom fixturing also improves the efficiency and cost-effectiveness of the manufacturing process, resulting in significant savings over time. To achieve manufacturing success, it is essential to invest in custom fixturing and work with experienced providers who can design and build fixtures tailored to the specific needs of your process.
By doing so, manufacturers achieve greater precision, efficiency, and quality in their manufacturing processes.