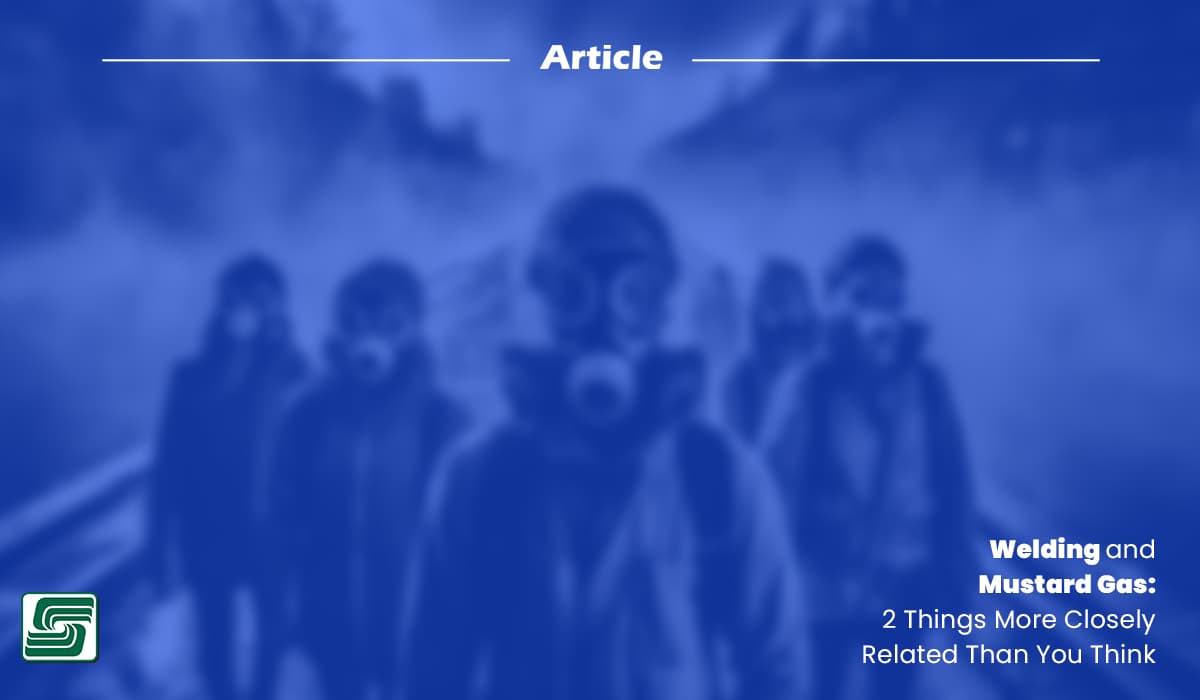
An experienced welder is in place, lights up, and starts heating some metal. Suddenly, the welder collapses in a coughing fit.
What happened?
He's a certified welder with several years of experience. He did everything right.
Right?
Chess is among the few games where a person makes all the right moves yet still loses the match.
That player has played for several years and played error-free, yet was beaten.
He did everything right.
Right?
Fortunately, our welder was okay. He was briefly exposed to a toxic fume that killed around 90,000 people over 100 years ago.
Mustard gas.
World War I
Mustard gas was used during World War I, primarily by the German forces. It was first used on July 12, 1917, causing more than 2,100 casualties. The Allies also began using mustard gas against German troops in June 1918.
Mustard gas was a significant chemical weapon during the war, causing more casualties than other chemical weapons such as chlorine and phosgene.
Although the mortality rate from mustard gas was *only* 2-3%, those who suffered chemical burns and respiratory problems dealt with long hospitalizations and, if they recovered, were thought to be at higher risk of developing cancers during later life.
Hidden Danger in Plain Sight
Why am I talking about mustard gas?
Brake cleaner is a popular tool for cleaning metal due to its degreasing properties and ability to remove oils, fats, and other contaminants from metal surfaces.
However, the danger existed because of a single ingredient: chloride.
When heated, chloride forms phosgene gas.
This gas has another name: mustard gas!
Welding Risks
Welding poses significant risks to workers, including exposure to hazardous chemicals. The metal joining process involves various hazards that impact the health and safety of welders.
From high temperatures to toxic fumes, welding environments demand strict safety measures to protect workers from potential harm.
Safety Importance
Exploring potential hazards and understanding the associated dangers with welding is essential to ensure worker safety. Two safety aspects are Protective Gear and Training and Education.
Protective Gear
In welding, using appropriate protective gear is crucial for ensuring the safety and well-being of welders. These protective measures minimize exposure to harmful substances and mitigate the potential risks associated with metal joining processes.
Safety goggles are vital in shielding the eyes from sparks, debris, and intense light generated during welding. Gloves protect against burns, cuts, and exposure to hazardous materials.
Respiratory masks are also indispensable for safeguarding welders against inhaling toxic fumes and airborne particles.
Training and Education
Proper training and education are fundamental to promoting welding safety. All welding personnel should receive comprehensive instruction on handling chemicals and adherence to safety protocols.
These instructions must include understanding the potential hazards associated with welding processes and how to effectively mitigate these risks.
Regular safety workshops and training programs should be implemented to ensure that all welders thoroughly understand safety procedures and best practices.
By equipping workers with the knowledge and skills, employers significantly reduce the likelihood of accidents or injuries in welding environments.
Chlorinated Cleaner Risks
Chlorinated brake cleaner, commonly used in welding for metal cleaning, presents significant risks to the health and safety of welders. Understanding the dangers of using chlorinated brake cleaner is crucial for implementing effective safety measures in welding environments.
Toxic Chemical Composition
- Chlorinated brake cleaners contain a combination of toxic chemicals, including chlorinated solvents and other hazardous substances. These chemicals pose serious health risks to welders upon exposure.
- The toxic composition of chlorinated brake cleaner leads to respiratory issues and other severe health complications, making it imperative for welders to minimize their exposure to these harmful substances.
Potential Hazards
- When chlorinated brake cleaner is used in welding processes, there is a significant risk of poisonous gas formation. Obviously, dangerous gas endangers the health of welders working in the vicinity.
- Inhalation of these toxic gases results in immediate symptoms such as dizziness and nausea, while prolonged exposure leads to long-term health problems. Workers must know these potential hazards and take necessary precautions when using chlorinated brake cleaner for metal cleaning in welding operations.
Implementing safe alternatives and stringent safety measures is vital for protecting welders from the dangers associated with chlorinated brake cleaners.
Chemical Reactions
When chlorinated brake cleaner comes into contact with metal surfaces during welding, it starts chemical reactions that produce harmful by-products. These reactions release toxic fumes and compounds, posing a significant risk to the health and safety of welders.
Understanding Chemical Interactions
The chemical interactions between chlorinated brake cleaner and metal surfaces are complex and result in the formation of hazardous substances. The cleaner reacts with the metal during welding, releasing potentially harmful reaction products into the surrounding environment. These reaction products may include volatile organic compounds (VOCs) and other chemical emissions threatening workers' well-being.
Impact on Welding Environment
The chemical reactions involving chlorinated brake cleaner have a detrimental impact on the welding environment. The release of toxic fumes and compounds contaminate the air within the workspace, endangering the health of nearby workers. Proper ventilation and containment measures are essential to mitigate these risks and prevent exposure to harmful chemical emissions.
Proper Ventilation: Implementing effective ventilation systems is crucial for removing hazardous fumes and compounds from the welding environment, safeguarding the well-being of workers.
Poisonous Gas Dangers
Exposure to poisonous gases generated during welding with chlorinated brake cleaner has severe health impacts. The inhalation of these toxic fumes leads to respiratory issues, causing breathing difficulties and discomfort for welders. Prolonged exposure to these hazardous gases may also result in neurological effects, affecting cognitive functions and overall well-being. The long-term implications of exposure to poisonous gases include chronic health complications, posing a significant risk to the overall health of welders.
Occupational Safety Measures
Implementing strict occupational safety measures is crucial to minimize the risks of exposure to poisonous gases in welding environments. Regular air quality checks and monitoring should be conducted to assess toxic fumes and ensure that the working environment meets safety standards.
Employers ensure their workers' safety in welding environments. Creating these safer environments includes implementing effective ventilation systems to remove hazardous gases and providing comprehensive training on recognizing and responding to potential gas hazards. Employers create a safe and secure workplace for welders by prioritizing these measures.
Safe Alternatives
Non-Chlorinated Brake Cleaner
In welding applications, non-chlorinated brake cleaners are a safer metal cleaning alternative. These cleaners are developed to remove contaminants from metal surfaces without posing the same risks of toxic gas formation associated with chlorinated cleaners.
Non-chlorinated brake cleaners, chlorine-free cleaners, offer a more environmentally friendly approach to metal cleaning in welding operations. Their composition eliminates chlorinated solvents and other toxic chemicals, making them a preferred choice for promoting workplace safety and environmental responsibility.
Benefits of Alternative Cleaners
Using non-chlorinated brake cleaners presents several benefits, contributing to a healthier and safer work environment for welders. Welding operations mitigate the potential health hazards associated with chlorinated products by opting for these alternative cleaners while effectively addressing the need for metal surface cleaning.
These alternative cleaners act as non-toxic degreasers, thoroughly cleaning metal surfaces without introducing harmful chemical residues or by-products. This precaution not only safeguards the well-being of welders but also minimizes the risk of environmental contamination within the workspace.
Employing non-chlorinated brake cleaners promotes a comprehensive approach to workplace safety and sustainability. Employers are committed to protecting their workers and the surrounding environment from avoidable harm by prioritizing using environmentally safe solvents in welding applications.
Safety Measures
Ventilation Systems
Proper ventilation systems ensure welders' safety and well-being in a welding environment. These systems are designed to effectively remove harmful fumes and gases from welding processes, reducing chemical exposure risks.
Installing efficient ventilation systems is pivotal in maintaining air quality in the workspace. By continuously extracting and replacing contaminated air with fresh, clean air, these systems create a healthier and safer environment for welders. Proper ventilation minimizes the concentration of hazardous substances and helps prevent the buildup of toxic fumes, thus reducing the potential health risks for workers.
Employers should prioritize regular ventilation system maintenance and inspections to ensure optimal functionality. Conducting air quality checks at specified intervals provides valuable insights into these systems' effectiveness in safeguarding welders' respiratory health.
Personal Protective Equipment (PPE)
Personal protective equipment (PPE) safeguards welders against chemical exposure during welding operations. Employers should emphasize the importance of wearing appropriate PPE as safety protocols to mitigate potential risks.
Respiratory masks are essential components of PPE for welders, serving as a crucial defense against inhaling toxic fumes and airborne particles. These masks act as a barrier, preventing exposure to hazardous substances in the welding environment. Employers must ensure that respiratory masks are readily available and welders are trained properly.
Besides respiratory masks, other forms of PPE, such as safety goggles and protective clothing, play an integral role in minimizing physical contact with harmful materials and preventing injuries related to metalworking processes. Employers effectively protect their workers from potential occupational hazards by providing comprehensive training on PPE usage and enforcing its consistent application.
Ensuring Safety
In conclusion, prioritizing safety measures and implementing safe alternatives is paramount for safeguarding welders from the potential dangers of chlorinated brake cleaners in welding environments.
Safety First: Protecting the well-being of welders should always be the top priority in any welding operation.
In Sum
Sometimes, article inspiration is as simple as seeing a headline in a trade publication. Other times, it's walking out to our shop floor.
I did that this morning when walking out to our machine shop, and I needed information from Frank, our incredibly talented Renaissance Man. As I spoke to him, my "Look! A Squirrel!" kicked in and I looked down to see an aerosol can that declared itself chlorine-free and was curious, so I asked Frank about it.
He told me that one of our previous safety coordinators learned about it while he was in the military and shared that information.
Frank told me he was lucky: he experienced those toxic fumes first-hand, hitting him like a hammer.
Luckily, his exposure was brief, but he still vividly remembers it.
Employers and welding personnel must adhere to safety protocols and adopt preventive measures to minimize risks.
By embracing safe alternatives and stringent safety practices, the overall workplace environment is significantly enhanced, promoting a culture of safety and well-being for all individuals involved in metal joining processes.