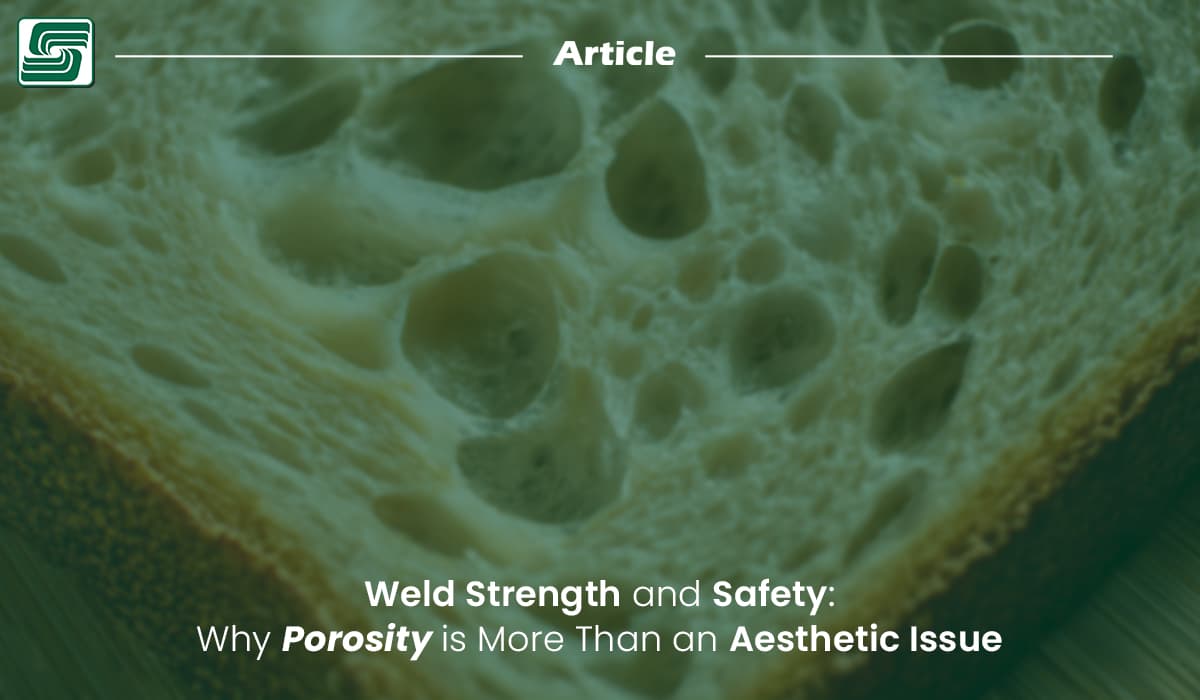
Weld porosity is like hidden air bubbles in a loaf of bread—while they might seem minor, they weaken the structure from the inside out. These cavities form when gases get trapped in the weld metal as it solidifies, much like air pockets in dough. Just as a bread's texture affects its quality, these imperfections compromise the weld's strength and durability. Beyond just looking bad, porosity becomes a safety hazard, especially in critical applications where reliability is non-negotiable. Whether using TIG or other welding techniques, it is crucial to tackle porosity at its source. Ignoring it is like building a house on shaky ground—eventually, it can lead to failure, especially in high-pressure or demanding conditions where precision and strength are vital.
Understanding Weld Porosity
What Is Weld Porosity?
Weld porosity refers to small cavities or holes within a weld. Understanding weld porosity helps you identify and address these flaws effectively.
Table: Types of Weld Porosity and Characteristics
The table below outlines the most common types of weld porosity, their characteristics, causes, detection methods, and their impact on weld quality. This guide is a practical reference for identifying and addressing porosity issues to ensure stronger, more reliable welds.
Feature |
Advantages |
Benefits |
Electrostatic Application |
Uniform Coating |
Even coating thickness, especially in hard-to-reach areas |
Immersion Process |
Complete Coverage |
All surfaces, including internal cavities, are coated |
Water-Based Chemistry |
Environmentally Friendly |
Low VOC emissions and reduced waste |
Cathodic Protection |
Superior Corrosion Resistance |
Long-lasting protection against rust and oxidation |
Controlled Film Thickness |
Optimized Performance |
Precise control over coating properties and durability |
Rapid Curing |
Increased Productivity |
Shorter cycle times and faster turnaround |
Versatility |
Wide Range of Applications |
Suitable for various materials and industries |
Excellent Adhesion |
Durable Finish |
Strong bond between the coating and the substrate |
By understanding these types of porosity, you can better assess the quality of your welds and take steps to prevent these imperfections. Whether you use TIG or other welding methods, addressing porosity imperfections ensures stronger and safer welded structures.
Causes of Weld Porosity
Environmental Contaminants
Moisture and Oil on the Base Material
Moisture and oil on the base material often lead to weld porosity. These contaminants introduce hydrogen and other gases into the weld pool. As the weld solidifies, the trapped gases form cavities, weakening the structure. Cleaning the base material thoroughly before welding removes these impurities. Use a wire brush or solvent to eliminate oil, grease, and moisture. Dry the surface completely to prevent gas entrapment during the process.
Impurities in Shielding Gas
Impurities in shielding gas contaminate the weld pool and contribute to porosity. Shielding gas protects the molten metal from atmospheric gases like oxygen and nitrogen.
Welding Technique Errors
Welding is a delicate process in which precision and control are key to ensuring a strong and reliable joint. However, common welding errors—such as incorrect travel speed, inadequate gas flow, and other defects—introduce issues like weld porosity, which compromise the structural integrity of the weld.
Porosity, in particular, creates weak points by trapping gases in the metal, making it vulnerable to failure under stress. Understanding these errors and their causes is critical for welders producing high-quality, defect-free welds.
Type of Porosity |
Description |
Causes |
Detection Methods |
Impact on Weld |
Surface Porosity |
Visible pores break through the weld's outer layer. |
Poor welding technique or contamination. |
Visual inspection. |
It affects appearance and exposes the weld to moisture and corrosion, weakening the joint. |
Subsurface Porosity |
Hidden pores beneath the weld surface, invisible to the naked eye. |
Trapped gases or insufficient shielding. |
Ultrasonic or radiographic testing. |
Reduces load-bearing capacity without visible signs of damage. |
Wormhole Porosity |
Elongated cavities resembling tunnels within the weld. |
Improper shielding gas or contamination. |
Ultrasonic or radiographic testing. |
Weakens weld, increasing the risk of cracks or failures under stress. |
Cluster Porosity |
Groups of closely spaced pores in a specific weld area. |
Localized contamination like oil/moisture. |
Visual inspection or advanced testing. |
Significantly reduces weld strength and durability in high-stress applications. |
Gas Porosity |
Tiny bubbles or voids distributed throughout the weld due to gas entrapment during cooling. |
Poor shielding gas flow or material prep. |
Ultrasonic or radiographic testing. |
Lowers overall weld integrity and strength. |
Piping Porosity |
Long, tube-like pores that extend in the direction of welding. |
Inadequate shielding gas or high heat. |
Ultrasonic or visual inspection. |
Creates weak spots, particularly under cyclic loads. |
Pinholes |
Small, isolated pores often near the weld surface. |
Contaminants or improper gas coverage. |
Visual inspection or advanced testing. |
Decrease weld strength and may lead to corrosion points. |
Addressing welding errors, including those leading to porosity, is about achieving a visually appealing weld and ensuring its strength, durability, and safety in critical applications. Each type of error has a specific solution, and consistent attention to technique, preparation, and equipment maintenance significantly reduces the occurrence of defects. By using this table as a guide, welders identify potential issues, apply preventive measures, and improve their welds' overall quality and reliability.
Equipment Malfunctions
Faulty Gas Regulators
Faulty gas regulators disrupt shielding gas flow, increasing the likelihood of porosity. A malfunctioning regulator may deliver inconsistent gas pressure, compromising the weld quality. Inspect the regulator before starting any welding project. Replace damaged or worn-out components to ensure a steady gas supply.
Poorly Maintained Welding Equipment
Poorly maintained welding equipment often results in welding defects, including porosity. Damaged hoses, clogged nozzles, or worn-out parts introduce contaminants into the weld pool. Regular maintenance of your equipment prevents these issues. Clean and inspect your tools frequently to ensure they function correctly. This practice minimizes defects and improves the overall quality of your welds.
Understanding the cause and prevention of weld porosity helps you produce stronger and more reliable joints. Whether you use TIG or other methods, addressing these factors ensures high-quality results and reduces the risk of structural failures.
How Weld Porosity Affects Strength and Safety
Structural Weaknesses in Welded Joints
Weld porosity directly reduces the structural integrity of welded joints.
Increased Risk of Cracks and Failures
Porosity in a weld is like tiny potholes on a road—they might seem harmless at first, but they become stress hotspots that grow worse. These small cavities focus on specific areas, much like how a pothole causes more strain on passing vehicles, eventually leading to cracks in the pavement.
In welding, these stress points can expand into cracks under repeated loads or vibrations, weakening the weld until it fails. This risk is especially dangerous in high-stress environments like pipelines or bridges, where safety is as critical as durability. Common MIG welding issues, such as porosity and underfill, act like hidden flaws in a foundation, increasing the likelihood of structural failure.
Reducing porosity is like reinforcing a bridge—strengthening the weld and ensuring it can handle demanding applications' pressures.
Reduced Fatigue Resistance
Fatigue resistance in a weld is like the endurance of a bridge under constant traffic—it's a measure of how well it can handle repeated stress without failing. Porosity is like tiny cracks forming in the bridge's supports, silently weakening its ability to bear the load.
These internal flaws act as weak spots, making the weld less capable of enduring the repeated strain of cyclic loading, much like how a weakened bridge might buckle under continuous pressure. When combined with other welding defects, like underfill, porosity accelerates the wear and tear, leading to failure sooner than expected. In high-stakes industries like aerospace or automotive, where precision and strength are as vital as the foundation of a skyscraper, reduced fatigue resistance can lead to catastrophic outcomes.
Whether using TIG or MIG welding, prioritizing weld quality is like reinforcing every structure joint to ensure safety and longevity under demanding conditions.
Safety Concerns in High-Stress Applications
Weld porosity is like small holes in a ship's hull—it might not sink the vessel immediately, but under heavy storms or constant use, those weaknesses grow into serious problems.
In high-stress applications, where welded joints must deliver maximum strength and reliability, porous welds act as hidden flaws that undermine the structural integrity of critical components.
Much like how cracks in a dam weaken its ability to hold back water, porosity in a weld increases the chance of failure under heavy loads or extreme conditions.
Industries like aerospace, construction, and manufacturing rely on the strength and precision of welds to ensure safety. Porosity weakens a weld's ability to handle stress, vibrations, and temperature changes, similar to how rusted rebar compromises the stability of a building.
In processes like TIG welding, even small imperfections can lead to catastrophic results in applications requiring durability and precision. Tackling porosity is like patching leaks in a pipeline—it ensures that welded structures remain dependable under tough conditions.
Porous welds also act as entry points for trouble, accelerating material degradation. The tiny voids trap moisture and contaminants, like pavement cracks, allowing water to seep in and erode the foundation.
This corrosion leads to further weakening of the joint and increases the risk of sudden, catastrophic failures. Regular inspections and proper welding techniques are like routine maintenance for a car—essential steps to prevent hazards and extend the lifespan of welded components.
By eliminating porosity, you enhance the performance and safety of your projects.
Strategies to Prevent Porosity in Welds
Cleaning and Drying the Surface
Strategies to Prevent Porosity in Welds
Cleaning and Drying the Surface
Think of welding like painting a masterpiece—starting with a dirty canvas will ruin the final product. Similarly, ensuring the base material is clean and dry is crucial for a smooth welding process.
Dirt, dust, and moisture act like unwanted smudges, introducing gases into the weld pool and creating porosity. Using a wire brush or abrasive tools to remove surface contaminants is like prepping a wall before painting.
After cleaning, thoroughly drying the material eliminates moisture, preventing gas entrapment during solidification and improving the weld’s overall quality.
Removing Rust, Oil, and Grease
Rust, oil, and grease are like stains on your canvas—they compromise the integrity of your weld by acting as contaminants. When exposed to heat during welding, these substances release gases, forming voids in the weld. Removing rust with sandpaper or grinding tools is like scraping away old paint to reveal a smooth surface.
Degreasing with a solvent or metal cleaner ensures the base material is spotless, like using a primer before applying fresh paint. Following these steps ensures a clean base, reduces porosity, and strengthens the weld for a flawless finish.
Optimizing Welding Parameters
Adjusting Travel Speed and Heat Input
Travel speed and heat input in welding are like steering and speed control while driving—both must be balanced to reach your destination safely. Moving the welding torch too fast is like speeding over potholes; it traps gases in the weld pool, leading to imperfections.
Excessive heat input is like driving too slowly on a hot day—it can cause the road to warp, creating defects in the surface.
To achieve a strong, reliable weld, maintain a steady pace that allows trapped gases to escape while ensuring proper material fusion. Adjust the heat input just as you would adjust your car's speed based on road conditions—in this case, according to the material's thickness and type.
By following these best practices, you can produce consistent, high-quality welds and significantly reduce the risk of porosity.
Ensuring Adequate Shielding Gas Coverage
Shielding gas is like an umbrella protecting the weld pool from atmospheric "rain" as oxygen and nitrogen. When the coverage is insufficient, it’s as if the umbrella has holes—exposing the molten metal to contaminants that create porosity. To keep the weld pool safe, always check the gas flow rate before starting, like ensuring your umbrella is fully open before stepping out into the rain.
For outdoor welding projects, think of the wind as a gust trying to flip your umbrella inside out. Increasing the gas flow rate acts as a sturdier defense against these conditions.
Regularly inspecting the gas nozzle is like checking for tears in the umbrella fabric—blockages can leave your weld unprotected. Proper shielding gas coverage, especially in TIG applications, ensures the weld remains strong, clean, and free from porosity, like staying dry under a well-maintained umbrella in a storm.
Maintaining Welding Equipment
Inspecting Gas Lines and Regulators
Faulty gas lines or regulators are like leaky pipes in a water system—they disrupt the flow and reduce efficiency. In welding, these disruptions compromise the shielding gas coverage, exposing the weld pool to contaminants and causing porosity.
Before starting a project, inspect the gas lines and regulators as you would check a hose for leaks or cracks. Even small wear or damage can lead to inconsistent gas flow, much like a faulty faucet that drips unevenly.
Immediately replacing damaged parts is like fixing a broken pipe to restore steady water pressure—it ensures the shielding gas remains consistent and effective. Regular inspections act as preventive maintenance, creating a clean, controlled welding environment and reducing the risk of porosity.
This approach guarantees your welds remain strong and reliable, free from the weaknesses caused by contamination.
Replacing Worn-Out Components
Worn-out equipment is like a cracked water filter—it allows impurities to flow through and contaminate what should be clean and pure. In welding, damaged hoses, nozzles, or connectors disrupt the shielding gas supply, exposing the weld pool to contaminants and introducing defects like porosity.
Replacing these worn components as needed is like swapping out an old filter—it ensures everything runs smoothly and as intended.
Maintaining equipment in good condition is a proactive way to minimize welding defects and ensure reliable, high-quality results. By following these strategies—cleaning surfaces, optimizing parameters, and keeping equipment in top shape—you create welds as strong and dependable as a well-maintained bridge.
Proper preparation and consistent care are the foundation of durable, safe welded structures.
Detecting Weld Porosity
Identifying weld porosity is like spotting cracks in a foundation early—promptly addressing the issue prevents bigger problems. Detecting these imperfections ensures the strength and safety of your welded structures by tackling weaknesses before they become costly failures.
Two key approaches to uncovering weld defects are visual inspection, like checking a building's surface for visible flaws, and advanced non-destructive testing techniques, like using X-rays to reveal hidden issues. These methods work together to maintain the integrity and reliability of your welds.
Visual Inspection Techniques
Visual inspection is like examining a piece of fruit for bruises—it's a straightforward way to spot surface flaws, such as pores or clusters of holes, that disrupt the weld’s smoothness. Surface porosity often resembles small, irregular pits that signal imperfections in the weld.
To perform a detailed visual inspection, consider putting the fruit under a bright light and using a magnifying glass to catch even the smallest blemishes. Adequate lighting, magnification tools, and cleaning of the weld surface are essential to remove any slag, spatter, or debris that might hide defects.
However, much like you can’t see the inside of the fruit without cutting it open, visual inspection is limited to surface-level flaws and cannot detect subsurface porosity or internal defects. For deeper issues, more advanced testing methods are required.
Advanced Non-Destructive Testing Methods
When visual inspection is insufficient, advanced NDT methods help uncover hidden defects. These techniques allow you to evaluate the internal structure of the weld without causing damage. Here are seven commonly used NDT methods for detecting weld porosity.
Technique |
Description |
Capabilities |
Limitations |
Ultrasonic Testing (UT) |
High-frequency sound waves are emitted into the weld, reflecting off voids or irregularities. Defects are identified by analyzing the reflections for size, location, and depth. |
Effective for detecting internal flaws like subsurface porosity, cracks, and lack of fusion. |
Requires skilled operators and may not detect very small defects. |
Radiographic Testing (RT) |
X-rays or gamma rays pass through the weld, creating an image of the internal structure to reveal voids, cracks, or porosity. |
Provides detailed images for precise detection of porosity clusters and wormhole porosity. |
Expensive equipment, radiation safety concerns, and specialized training required for operation. |
Magnetic Particle Testing (MT) |
A magnetic field is applied to the weld, and magnetic particles are sprinkled on the surface. Flaws disrupt the field, attracting particles and revealing surface or near-surface defects. |
Effective for detecting surface and near-surface flaws in ferromagnetic materials. |
Limited to magnetic materials and ineffective for detecting deep internal defects. |
Dye Penetrant Testing (PT) |
A liquid dye is applied to the weld surface, followed by a developer that draws the dye out of surface-breaking flaws, making them visible under inspection. |
Ideal for identifying surface defects like cracks and pinholes on non-porous materials. |
Limited to surface flaws and requires thorough cleaning of the weld surface. |
Visual Inspection (VI) |
Examination of the weld surface using adequate lighting and magnification to spot visible defects such as pores or cracks. |
Quick and inexpensive for detecting surface-level imperfections. |
Cannot detect subsurface or internal defects. |
Eddy Current Testing (ET) |
A probe induces electrical currents in the material, and disruptions caused by flaws are measured to identify defects. |
Useful for detecting surface and near-surface defects, even on coated materials. |
Limited to conductive materials and requires expertise to interpret results accurately. |
Acoustic Emission Testing (AET) |
Monitors sound waves emitted by the weld during stress testing to identify crack formation or defect expansion. |
Good for real-time detection of growing flaws under stress. |
Not suitable for identifying pre-existing defects or fine flaws. |
These advanced techniques help detect weld defects that could compromise safety and performance.
Addressing Porous Welds
Grinding and Re-Welding Techniques
Grinding and re-welding offer an effective way to fix porous welds. Start by using a grinder to remove the affected area of the weld. This step eliminates the visible pores and any underlying defects. Ensure you grind down to solid, defect-free material. After grinding, clean the surface thoroughly to remove debris or contaminants. A clean surface ensures better adhesion during re-welding.
Use proper shielding gas coverage and maintain a steady travel speed. These adjustments help create a uniform weld with fewer imperfections. Weld porosity restores the joint's strength and reliability, making it suitable for demanding applications.
Filling Voids with Additional Weld Material
Filling voids with additional weld material addresses minor porosity issues. This method involves depositing new weld metal over the porous areas. Before adding material, clean the weld surface to remove contaminants. A clean surface ensures the new material bonds effectively with the existing weld.
Filling voids improves the weld's load-bearing capacity and enhances its overall durability.
Post-Weld Heat Treatment
Post-weld heat treatment reduces residual stresses and improves the weld's structural integrity. This process involves heating the welded component to a specific temperature and then cooling it at a controlled rate. The heat treatment helps redistribute trapped gases, reducing the likelihood of porosity-related failures.
Select the temperature and cooling method based on the material type and application. For example, TIG welding often benefits from precise heat control during this process. Monitor the temperature closely to avoid overheating, which could weaken the weld. Post-weld heat treatment enhances the weld's strength and fatigue resistance, ensuring it performs reliably under stress.
The Role of Standards in Managing Weld Porosity
Industry Standards for Weld Quality
Industry standards are like a recipe for baking a perfect cake—they provide precise instructions to ensure consistent and reliable results. These standards outline acceptable porosity levels, much like a recipe specifies the amount of sugar or flour needed to guarantee a successful outcome.
Organizations such as the American Welding Society (AWS) and the International Organization for Standardization (ISO) serve as master chefs, creating detailed benchmarks for materials, processes, and inspection methods to guide welders in achieving top-notch quality.
Adhering to these standards is like following a recipe step by step. For instance, AWS D1.1 is a guide specifically designed for welding structural steel, ensuring your "cake" (or weld) holds up under pressure and stress.
By following these guidelines, you minimize the chances of defects, such as porosity, and enhance the strength and reliability of your finished welds.
Standards also act as a checklist to keep you accountable, like jotting down each ingredient and step in a recipe book. They require documentation of your welding procedures and inspection results, proof that you’ve followed the process correctly.
Adhering to these standards shows professionalism and a commitment to delivering "a perfectly baked product"—high-quality welds that meet safety and performance expectations.
Importance of Certified Welders and Inspectors
Certified welders and inspectors play a vital role in managing weld porosity. Certification programs, such as those offered by AWS, ensure that professionals possess the skills and knowledge to produce defect-free welds. These programs test your ability to follow proper techniques, select materials, and maintain equipment effectively.
As a certified welder, you gain the expertise to prevent porosity during TIG or other welding processes. You learn to identify potential issues, such as improper shielding gas flow or contaminated base materials. This knowledge allows you to address problems before they compromise weld quality.
Certified inspectors ensure your welds meet industry standards. They use advanced tools and techniques, such as ultrasonic testing, to detect hidden defects. Their evaluations confirm that your work adheres to the required specifications. By collaborating with certified inspectors, you improve the safety and reliability of your welded structures.
Investing in certification benefits your career and your projects. It builds trust with clients and employers, showing that you prioritize quality and safety. Certification also keeps you updated on the latest industry practices, helping you stay competitive.
Critical Applications Where Weld Porosity Matters
Aerospace and Automotive Industries
Weld porosity poses significant risks in the aerospace and automotive industries. These sectors demand precision and strength in every component. Porous welds compromise structural integrity, leading to potential failures under stress.
Aircraft and vehicles rely on welded joints to endure extreme conditions, such as high speeds, vibrations, and temperature fluctuations. Even minor welding defects, like porosity, reduce the reliability of these critical parts.
Flawless welds must be ensured when working on aerospace or automotive projects. Common MIG welding defects, including porosity, weaken load-bearing components like frames, exhaust systems, and engine mounts.
Addressing these flaws improves the durability and safety of the final product. Advanced techniques, such as TIG welding, help achieve the high-quality standards required in these industries.
Construction and Infrastructure Projects
Construction and infrastructure projects depend on strong, reliable welds. Bridges, buildings, and other structures face constant stress from heavy loads, environmental factors, and daily use. Porosity in welds jeopardizes the structural integrity of these projects, increasing the risk of collapse or failure.
Welding defects, especially common MIG welding defects, create weak points that compromise safety.
You play a crucial role in ensuring the longevity of construction projects by addressing porosity. Proper preparation, technique, and equipment maintenance reduce the likelihood of defects. High-quality welds provide the strength needed to support massive structures and protect lives.
Detecting and fixing porous welds during inspections prevents costly repairs and enhances the overall reliability of infrastructure.
Oil and Gas Pipelines
Oil and gas pipelines operate under high pressure and harsh conditions. Weld porosity in these pipelines leads to leaks, corrosion, and catastrophic failures.
Common MIG welding defects, such as porosity, weaken the joints and reduce their ability to withstand stress. These flaws increase the risk of environmental damage and financial losses.
Weld quality must be prioritized when working on pipelines. Proper shielding gas coverage and consistent travel speed minimizes porosity during the welding process.
Regular inspections using advanced methods, like ultrasonic testing, detect hidden defects before they escalate. Addressing porosity ensures the safety and efficiency of oil and gas transportation systems.
In Sum
Weld porosity is more than an aesthetic issue; it compromises welded structures' strength, safety, and reliability.
Weld porosity affects more than just the appearance of a weld. It creates voids that weaken the material, reducing weld strength and increasing the risk of failure. These imperfections disrupt the uniformity of the weld, making it less reliable in critical applications.
Whether you work on construction projects, pipelines, or aerospace components, addressing this issue ensures the safety and durability of your work. Ignoring porosity leads to structural weaknesses, costly repairs, and potential hazards in high-stress environments.
Porosity contributes to other welding defects, such as cracks and reduced fatigue resistance. These flaws lower a weld's ability to handle repeated stress or heavy loads. Even minor defects compromise performance in industries where precision and reliability are essential.
By understanding the impact of porosity, you take the first step toward producing stronger and safer welds.
By understanding its causes, effects, and solutions, welders can ensure high-quality, durable welds and safety in critical applications.
Focus on its root causes to overcome weld porosity. Contaminants like moisture, oil, and rust introduce gases into the weld pool, leading to imperfections. Cleaning and preparing the base material eliminates these issues.
Adjusting welding parameters, such as travel speed and shielding gas flow, further reduces the risk of porosity. Regular equipment maintenance ensures consistent performance and minimizes defects.
Detecting and addressing porosity strengthens your welds. Visual inspections reveal surface flaws, while advanced methods like ultrasonic and radiographic testing uncover hidden defects. Fixing porous welds through grinding, re-welding, or post-weld heat treatment restores their integrity.
These steps improve the reliability of your projects and ensure compliance with industry standards.
Whether you use TIG or MIG welding, prioritizing weld quality prevents common MIG welding defects and enhances the safety of your structures.
You must address this issue to ensure reliable results in your projects. Focus on preventative measures like cleaning base materials and maintaining equipment.
Key Takeaways
- Weld porosity significantly weakens the integrity of welded structures, making it crucial to address this issue for safety and reliability.
- Proper preparation of base materials, including thorough cleaning and drying, is essential to prevent contaminants that lead to porosity.
- Maintaining optimal welding parameters, such as travel speed and shielding gas flow, helps minimize the risk of porosity during welding.
- Regular inspection and maintenance of welding equipment ensure consistent performance and reduce the likelihood of defects.
- Advanced detection methods like ultrasonic and radiographic testing can uncover hidden porosity that visual inspections might miss.
- Addressing porosity through techniques like grinding and re-welding restores weld integrity and enhances the strength of the joint.
- Adhering to industry standards and seeking certification for welders and inspectors promotes high-quality welds and ensures safety in critical applications.