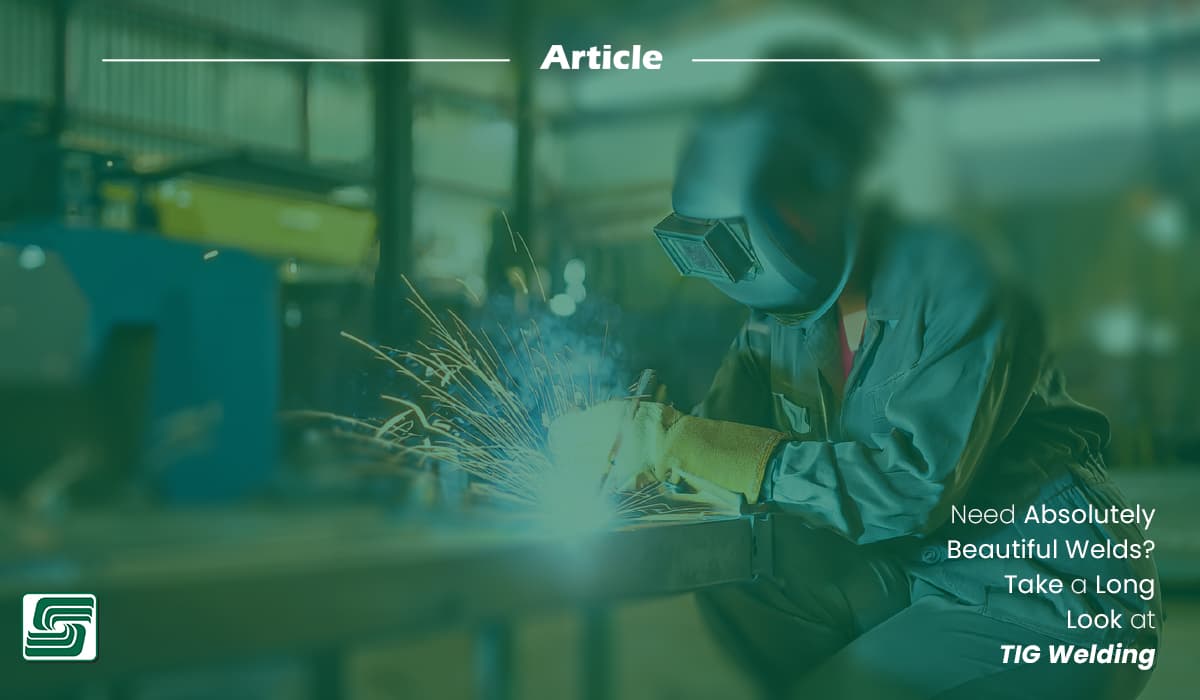
TIG welding is a gas-shielded process that produces welds using a non-consumable tungsten electrode. If a high-purity weld is needed, TIG is the preferred method.
The exact nature of TIG welding contains a steep learning curve. The process is slow compared to MIG, yet it produces cleaner and more accurate welds.
Development
This welding method comes from the English term Tungsten Inert Gas, but one can sometimes encounter the term WIG welding from the German term Wolfram Inert Gas. Tungsten and Wolfram are both names for the same metal.
TIG welding became popular during World War II because it could join aluminum and magnesium. The process developed into a worthy replacement for manual and gas metal arc welding because its reliance on inert shielding gas from environmental contamination instead of slag led to cleaner, higher-quality welds.
Russell Meredith, who worked for Northrop Aircraft Co, patented a process called "Heli-Arc Welding," a precursor to today's TIG/GAW welding process. The company Linde, which purchased the patent, continued developing this welding process primarily because of the use of inert gases. Development continued by constructing and applying different burners, nozzles, and shielding gas flow studies.
Process
Watch the following video providing an overview of the TIG welding process:
Three things are needed for using the TIG welding method: shielding, filler material, and heat.
Inert gases, such as argon and helium, shield a TIG weld. The filler material is wire melted by the arc. Electricity passing through the tungsten electrode creates an arc supplying the needed heat.
Learning to TIG weld is difficult because the welder's two hands must coordinate. One hand feeds the filler metal, while the other holds the electrode.
Power Source
A constant power source, AC or DC, is needed for TIG welding.
TIG welding must be operated with a drooping, constant current power source - either DC or AC. A constant current power source is essential to avoid excessively high currents being drawn when the electrode is short-circuited on to the workpiece surface. This could happen either deliberately during arc starting or inadvertently during welding. If, as in MIG welding, a flat characteristic power source is used, any contact with the workpiece surface would damage the electrode tip or fuse the electrode to the workpiece surface. In DC, because it distributes arc heat approximately one-third at the cathode (negative) and two-thirds at the anode (positive), the electrode is always negative polarity to prevent overheating and melting. However, the alternative power source connection of DC electrode positive polarity has the advantage in that when the cathode is on the workpiece; the surface is cleaned of oxide contamination. For this reason, AC is used when welding materials with a tenacious surface oxide film, such as aluminum.
Starting the Arc
The most common method of jump-starting the arc is high-frequency (HF). The HF-generated high-voltage sparks last a few microseconds, breaking down the workpiece gap. Current from the power source flows from the formed electron/ion cloud.
Tungsten Electrodes
Tungsten is a brittle, slightly radioactive, and hard metal. It is used in heating elements, rocket engines, and light bulbs—extremely high-temperature applications. Since TIG welding uses either AC or DC, there are two types of tungsten electrodes.
The electrode operates at higher temperatures during AC welding. Because of these higher temps, zirconia is added to the tungsten, reducing electrode erosion.
Electrodes used in DC welding have 1% to 4% thoria added to the pure tungsten. The thoria additives improve the ignition of the arc. Other additives used as alternatives to thoria are cerium oxide and lanthanum oxide, which may provide outstanding performance regarding lower electrode consumption and starting the arc.
Tungsten has the highest melting point of any metal in the Periodic Table, which helps when temperatures reach over 6,000 ºF. Because the electrode isn't consumable, there's no need to balance the heat input.
Shielding Gases
Using the proper shielding gas coverage is critical for achieving quality TIG welds. As previously discussed, inert shielding gases protect the welds from atmospheric contamination.
The three most common gas options used in TIG welding are argon, helium, and a mix of the two.
Shielding Gas |
Description |
100% Argon |
Argon is primarily used for GTAW due to its availability, cost, and arc-starting characteristics. Due to its lower ionization potential, argon produces consistent high-frequency arc starts and a more stable arc than helium. |
100% Helium |
Because it has higher thermal conductivity than argon, helium can be used for GTAW to produce higher heat inputs. These higher heat inputs result in faster travel speeds and higher depth-to-width ratios and are suitable for welding thicker materials. Helium does have a higher ionization potential, resulting in inconsistent arc starts. |
Argon/Helium |
An argon/helium mix is typically used to achieve the higher heat inputs of helium while maintaining the superior arc offered by argon. These mixes commonly contain 25 to 75 percent helium. As helium content increases, the arc becomes hotter, but high-frequency arc starting performance and stability decrease. |
Advantages of TIG Welding
There are several primary advantages and disadvantages of using the TIG welding method:
Advantages |
Explanation |
Precision |
The ability to control temperature reduces spattering. This reduced spatter and clear visibility allow the welder to monitor the electrode and work while in the weld puddle, leading to good-looking, quality welds. |
Strength |
The shielding gas prevents air from penetrating the molten pool, preventing oxidation. As a result, TIG welds are more robust, corrosive, and ductile resistant. |
Versatility |
TIG welding is a multi-tool in the welding world. Materials, positions, thickness dimensions, sizes, shapes, and restricted and narrow spaces become possible. TIG allows for welding non-ferrous, non-ferrous, and dissimilar metals. |
Complexity |
High heat-resistant materials like tantalum have high melting points. The heat generated by the TIG arc allows for molybdenum, niobium, titanium, and tungsten welding. Materials other welding methods have a hard time with. |
Non-Consumable Electrode |
Avoiding the need for replacing the electrode frequently allows the welder to create near-perfect joints. |
Cleanliness |
With reduced sparks and splatter comes less clean-up—the precision and control of TIG welding results in completed welds requiring less touch-up. |
Disadvantages |
Explanation |
Time |
Because of its slow disposition rates, TIG requires much time and slower welding speeds. |
Learning Curve |
The complicated equipment and the need for a deft touch steepen the learning curve. It is also complicated to learn to use both hands and start the arc. |
Thickness |
The nature of TIG typically means thicker sheets of metal require different welding methods. |
Cost |
TIG welding isn't cheap. It's one of the most expensive welding methods. The welding machines and replacement inert gases have high price tags. The cost of labor also runs higher with TIG welding. Because it's a specialized process, experienced welders create higher salaries or training costs. |
Environment |
Any breeze near a TIG welding job disrupts the protection given by shielding gases. These disruptions result in contamination of the tungsten and weld porosity. |
Safety |
The arc's intense brightness is more significant than other welding methods because of the absence of smoke and fumes. The formation of nitrous and ozone oxides increases the number of UV rays illuminated by the arc. |
Cleanliness |
Yes, this is also a disadvantage. Similar to MIG welding, the work surface of the welded metal must be spotless. |
In Sum
Augustus was Rome's first emperor, whose motto was Festina lente, which means 'more haste, less speed.' The same motto can be shared with TIG welders, too. The idea behind the saying is to train for the job slowly, perfecting the technique. This sounds contradictory, but moving thoughtfully and deliberately quickens the process, i.e., doing it right the first time.
Applying this adage to TIG welding might be cheating, but correctly using this method at a slower production speed results in better and stronger welds.