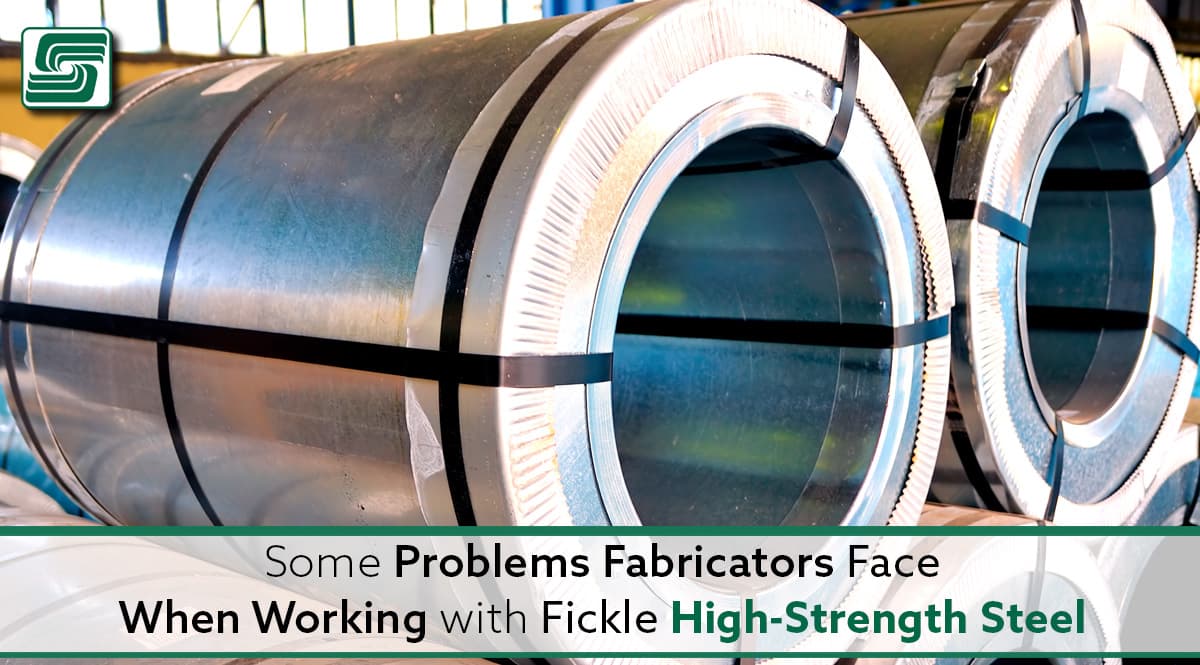
Have you ever tried moving something heavy using a lever? The heavier the weight, the stronger the lever you had to use. In short, you needed a stronger tool to move something heavier. That same theory holds when working with stronger forms of steel.
High-strength steel is a material with a high amount of strength, usually above 370 MPA, while being the material of choice for structural or stress applications.
High-strength steel has many properties that make it ideal for these structural components. It has a much higher tensile strength than standard carbon or alloy steel, which means they withstand much more force without breaking as easily. High-strength steel needs strengthening to support greater loads without needing to be thicker than a weaker material like standard carbon steel.
Fabricators of high-strength steel face many challenges when working with this metal fabrication project because traditional methods cannot process most high-strength steel. Developing new processes for machining high-strength steel or adding secondary operations reduces the risk of breakage during primary operations.
Let’s explore those problems:
How Common are High-Strength Steel Projects?
Fabrication and construction industries use high-strength steel in structural components like cranes, excavator buckets, structural beams, support columns, and vehicle panels, such as the roof and floor. These parts must be strong enough to carry heavy loads yet lightweight enough to be moved.
You'll find high-strength steel in:
- Power plants
- Mining rigs
- The aviation industry, such as the fuselage, wings, and undercarriage
- Military vehicles and equipment
- And other heavy machinery
Tight Tolerances
When fabricating high-strength steel, the designer’s tolerance for error is much smaller than standard carbon or alloy steel. Traditional methods can't machine high-strength steel, creating the need for secondary operations for removing excess material.
The likelihood of breaking the material is high when attempting a typical cutoff operation. Therefore, tolerances must be much tighter to guarantee the correct size. Taper grinding, grinding, or other grooving methods remove excess material, needing greater precision.
The equipment and the operator must be extremely accurate to remove the right amount, but not so much making the part too small.
High-Strength Steel Makes Accuracy Harder
Standard equipment can't cut, drill, or machine high-strength steel. Plus, the strength of the material means normal carbon steel tools aren't strong enough to machine them, either. Therefore, the fabricator needs to develop new ways to machine high-strength steel.
While standard methods work on some parts, using them on high-strength steel likely breaks them. High-strength steel requires extremely high machine spindle speeds above 15,000 RPM—if turning standard high-strength steel parts.
The Material Isn't Soft
High-strength steel is very hard when first produced, meaning it needs to be annealed to make it softer and easier to machine. Several methods are available, such as flame, induction, and salt bath annealing.
An induction furnace is one of the most common softening high-strength steel. The furnace uses an electromagnetic field to heat the steel to its annealing temperature while also controlling the steel's cooling rate.
High-Strength Steel is Harder to Drill and Cut
Drilling holes in high-strength steel is difficult because the material is very hard. It may be possible to use carbide-tipped drill bits to cut the holes in the part, but it is not always practical. Another option is to make internal holes with a boring tool.
However, this is also difficult because high-strength steel doesn't allow the part to cool quickly enough to prevent warping. Sometimes, performing secondary operations for making holes becomes necessary.
For example, a boring bar can make a hole on one side of the part, while a tap creates internal threads in the hole.
Welding Becomes an Issue with High-Strength Steel
High-strength steel is difficult to weld because the high-strength material is more prone to thermal cracking caused by the higher amount of heat created when welding the material. Fabricators reduce thermal cracking by preheating the part, which expands it while reducing internal stresses using a torch or by submerging the part in a bath of water or nitrogen gas.
However, high-strength steel may not be suitable for welding because it is brittle when first produced, so annealing becomes necessary.
Weakened Steel
When cutting and machining high-strength steel, the material becomes brittle, meaning it doesn't have the same strength as the original high-strength steel. The amount of brittleness and the amount of strength lost vary based on the type of high-strength steel.
The methods used to machine the part also affected softness. For example, flame cutting and electro-galvanizing will likely make the part significantly more brittle.
In Sum
High-strength steel fabricators face many challenges when working on metal fabrication projects because traditional methods can't process most high-strength steel, requiring developing new or secondary processes to reduce the risk of breakage during primary operations.
Like using that lever we talked about before: you wouldn't use an old broom handle when trying to lift an engine block, right?