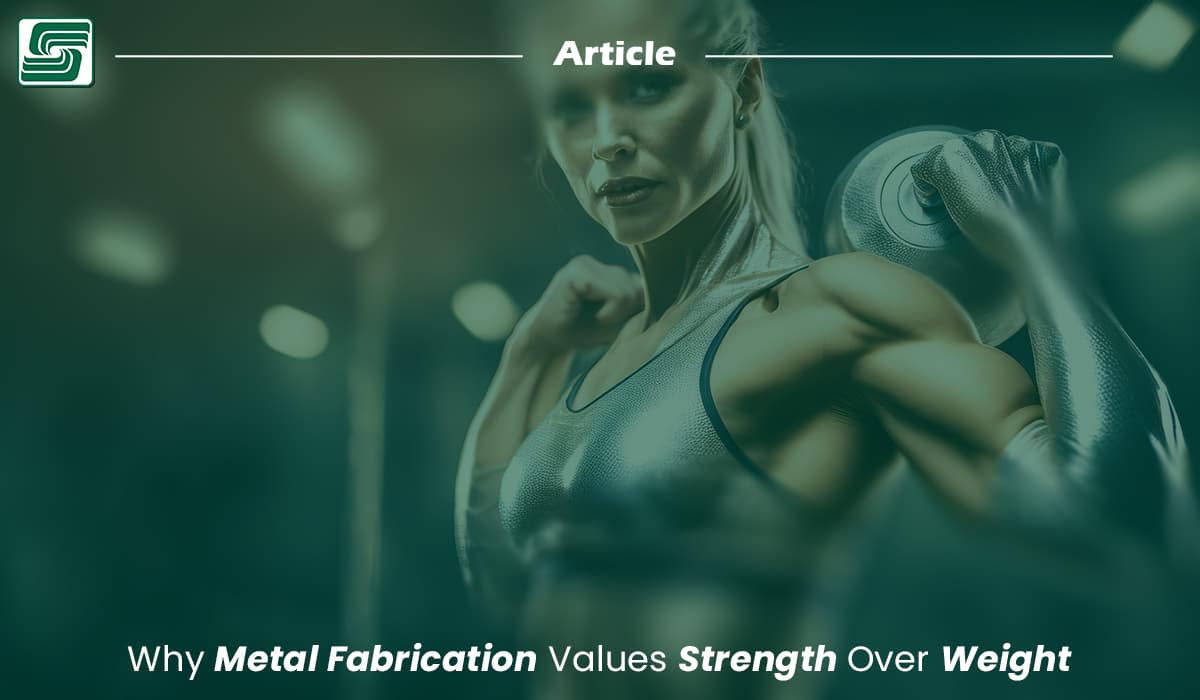
Metal fabrication plays a crucial role in modern industries. It shapes the backbone of sectors like aerospace and automotive, which demand materials that withstand immense stress while maintaining structural integrity. The debate between strength and weight often arises in this context.
Why do engineers prioritize strength over weight?
The answer lies in the need for durability and safety. Stronger materials ensure structures endure harsh conditions without compromising performance.
This focus on strength supports creating reliable and long-lasting products, essential for advancing technology and innovation.
Understanding Metal Fabrication
Metal fabrication involves transforming raw materials into functional products. This process requires a deep understanding of metals' properties. Engineers and fabricators must consider both strength and weight to ensure optimal performance.
Metal's Basic Properties
Property |
Definition |
Impact on Metal Fabrication |
Strength |
Ability to withstand forces without breaking or deforming |
Ensures safety, reliability, and durability in structures and components. |
Weight |
Mass of a metal |
It influences ease of handling, transportation, and fuel efficiency. Requires balancing with strength for optimal performance. |
Common Metals Used
- Steel's remarkable strength and long-lasting nature set it apart. It supports heavy loads and resists corrosion, making it a popular choice in construction and infrastructure.
- Aluminum is known for its lightweight properties compared to steel. These properties make aluminum perfect for aerospace and automotive industries, where weight reduction is essential.
- Titanium is known for its exceptional strength and lightweight, providing a superior strength-to-weight ratio. Because of these specific properties, titanium is favored for advanced applications in aerospace and medical devices.
Metal |
Strength |
Weight |
Applications |
Steel |
High strength, durable |
Heavy |
Construction, infrastructure, automotive (heavy-duty components), shipbuilding |
Aluminum |
Strong, good strength-to-weight ratio |
Lightweight |
Aerospace, automotive (lightweight components), packaging, consumer electronics |
Titanium |
High strength-to-weight ratio, corrosion-resistant |
Lightweight |
Aerospace, medical devices, high-performance applications Export to Sheets |
The Importance of Strength in Metal Fabrication
Structural Integrity
In metal fabrication, structural integrity is paramount. Engineers prioritize strength to ensure that structures withstand external forces without collapsing. Strong metals maintain their shape and function under stress, which is crucial for buildings, bridges, and other infrastructure. They resist deformation, ensuring the structure remains safe and reliable. This focus on strength prevents catastrophic failures, protecting the structure and its users.
Safety Considerations
Safety remains a top priority in metal fabrication. Strong materials safeguard against potential hazards and support heavy loads, reducing the risk of structural failure. Safety considerations drive the choice of materials in industries like construction and transportation. Engineers select metals that offer the highest strength to protect lives and property. This emphasis on strength ensures that structures meet safety standards and regulations, minimizing the risk of accidents.
Resistance to Wear and Tear
Durability defines a material's ability to withstand wear and tear. In metal fabrication, strong metals resist damage from environmental factors such as weather, friction, and impact. This resistance extends the lifespan of products, reducing the need for frequent replacements. Engineers value strength because it contributes to the durability of structures and components. Choosing durable materials ensures products remain functional and efficient.
Maintenance and Repair
Maintenance and repair costs significantly impact a project's overall expense. Strong metals require less maintenance, as they resist damage and degradation, which reduces the frequency and cost of repairs, making them a cost-effective choice in metal fabrication. Engineers consider the long-term benefits of using strong materials, as they contribute to lower maintenance costs and increased reliability. By prioritizing strength, they create products that offer lasting value and performance.
The Role of Weight in Metal Fabrication
Weight plays a significant role in metal fabrication, influencing performance and cost. Engineers must deliberate weight when selecting materials for various applications.
Transportation Fuel Efficiency
In transportation, weight directly affects fuel efficiency. Lighter vehicles consume less fuel, making them more economical and environmentally friendly. Engineers often choose lightweight metals like aluminum to enhance fuel efficiency in cars and airplanes. This choice reduces operational costs and minimizes environmental impact, aligning with global sustainability goals.
Handling and Installation Ease
Weight also impacts the ease of handling and installation. Lighter metals simplify the fabrication process, reducing labor and time requirements. Workers find it easier to maneuver and install lighter components, which speeds up construction and manufacturing projects. This efficiency translates into cost savings and increased productivity, making lightweight metals attractive in many industries.
Cost Implications
Material costs vary significantly based on weight. Lightweight metals often have a higher price tag because of their specialized properties. However, the long-term savings in fuel and handling offset these initial costs. Engineers must weigh the upfront expense against potential savings to make informed decisions in metal fabrication.
Transportation and Logistics
Transportation and logistics costs also depend on weight. Heavier materials incur higher shipping expenses, impacting the overall project budget. By choosing lighter metals, companies reduce transportation costs, making projects more financially viable. This consideration is crucial in industries where logistics play a significant supply chain role.
Comparing Metals: Strength vs. Weight
Feature |
Steel |
Aluminum |
Strength |
Remarkable strength, ideal for heavy-duty applications like bridges and skyscrapers. |
Strong, but not as strong as steel. However, it offers a good strength-to-weight ratio. |
Weight |
Heavier, which can impact fuel efficiency and transportation costs. |
Lightweight, which improves fuel efficiency and reduces transportation costs. |
Cost |
Generally less expensive. |
Often more expensive due to specialized processing techniques. |
Corrosion Resistance |
Susceptible to rust, especially in humid environments. |
It is highly resistant to corrosion, making it suitable for outdoor applications. |
Workability |
More difficult to work with, requiring specialized equipment and techniques. |
Easier to work with, can be formed and shaped more readily. |
Applications |
Construction, infrastructure, automotive (heavy-duty components), shipbuilding. |
Aerospace, automotive (lightweight components), packaging, consumer electronics. |
Real-World Applications and Trade-offs
Factor |
Considerations |
Goal |
Project Requirements |
Load-bearing capacity, durability, safety standards |
Meeting specific needs of the project |
Environmental Considerations |
Carbon footprint, energy efficiency, recyclability, resource conservation |
Minimizing negative environmental impact |
Balancing Strength and Weight |
Achieving the optimal combination of strength and weight |
Maximizing performance and efficiency |
Innovative Solutions |
Exploring new alloys and composite materials |
Developing lighter, stronger, and more sustainable products Export to Sheets |
Automotive Industry
In the automotive industry, engineers prioritize strength in chassis and frame design. A strong chassis ensures vehicles withstand impacts and maintain structural integrity, enhancing safety and performance. Engineers select materials that support the vehicle's weight and dynamic forces. By choosing strong metals, they create vehicles that endure harsh conditions and offer a reliable driving experience.
Safety Features
Vehicle safety features rely heavily on strong materials. Engineers design crumple zones and reinforcement bars to absorb impact energy during collisions. Strong metals protect passengers by maintaining the vehicle's shape and preventing intrusion. This emphasis on strength in safety features reduces the risk of injury and enhances occupant protection. Engineers continually innovate to improve safety standards, ensuring vehicles meet rigorous regulations.
Construction and Infrastructure
Bridges and skyscrapers demand materials with exceptional strength in construction. Engineers prioritize strong metals to support immense loads and resist environmental forces. Steel, known for its strength, is crucial in these structures. It provides the support to maintain stability and safety. By using strong materials, engineers ensure that bridges and skyscrapers stand the test of time, enduring natural disasters and heavy usage.
Reinforcement Techniques
Reinforcement techniques in construction enhance the strength of structures. Engineers use strong metals to reinforce concrete, increasing its load-bearing capacity. This approach prevents cracking and extends the lifespan of buildings and infrastructure. Engineers create structures that withstand wear and tear by prioritizing strength and reducing maintenance needs. These techniques ensure buildings remain safe and functional for decades.
Decision-Making in Metal Fabrication
In metal fabrication, decision-making involves evaluating various factors to select the most suitable materials. Engineers must consider both project requirements and environmental considerations to ensure optimal outcomes.
Factors Influencing Material Choice
Factor |
Considerations |
Goal |
Project Requirements |
Load-bearing capacity, durability, safety standards |
Meeting specific needs of the project |
Environmental Considerations |
Carbon footprint, energy efficiency, recyclability, resource conservation |
Minimizing negative environmental impact |
Balancing Strength and Weight |
Achieving the optimal combination of strength and weight |
Maximizing performance and efficiency |
Innovative Solutions |
Exploring new alloys and composite materials |
Developing lighter, stronger, and more sustainable products |
Future Trends in Metal Fabrication
New Alloys
Metal fabrication continues to evolve with the development of new alloys. These innovative materials offer enhanced properties, such as increased strength and corrosion resistance.
Engineers explore these alloys to meet the demands of modern industries, looking for materials that provide superior performance while maintaining cost-effectiveness.
New alloys enable the creation of lighter and stronger structures, which benefit sectors like aerospace and automotive.
By adopting these advancements, engineers push the boundaries of what metal fabrication can achieve.
Composite Materials
Composite materials represent another significant advancement in metal fabrication. These materials combine different substances to create a product with unique properties. Engineers use composites to balance strength and weight. For example, carbon fiber composites offer high strength while remaining lightweight, making them ideal for applications where reducing weight is crucial. Using composite materials in metal fabrication leads to innovative designs and improved performance across various industries.
Sustainable Fabrication Practices
Recycling and Reuse
Metal fabrication is increasingly focused on sustainable practices to minimize environmental impact.
- Recycling metals reduces the need to extract raw materials, conserving natural resources.
- Reusing materials further decreases waste, aligning with global efforts to promote eco-friendly manufacturing.
Energy Efficiency
Engineers reduce costs and environmental impact by optimizing energy use during manufacturing.
- Renewable energy sources such as solar or wind power can significantly lower the industry's carbon footprint.
- Improving production methods streamlines processes and reduces energy consumption, contributing to a more sustainable future for metal fabrication.
In Sum
The future of metal fabrication looks promising, with ongoing innovations. Engineers explore new alloys and composite materials that offer improved strength-to-weight ratios. These advancements enable the creation of lighter yet stronger structures, enhancing efficiency and performance. By embracing leading-edge technologies, engineers push the boundaries of what is possible in metal fabrication. This forward-thinking approach leads to developing products that meet evolving industry demands and set new standards for excellence.
The potential for growth in metal fabrication remains vast. As industries evolve, the demand for strong and lightweight materials increases. Engineers play a crucial role in meeting this demand by developing innovative solutions. The focus on sustainability and energy efficiency drives the industry forward. By prioritizing these aspects, engineers contribute to a more sustainable future. The metal fabrication industry stands poised for growth, offering exciting opportunities for advancement and innovation.
Metal fabrication values strength over weight because of its critical role in ensuring safety and durability. Strong materials withstand stress and maintain structural integrity, which is essential for the aerospace and automotive industries. Continued innovation in metal fabrication promises exciting advancements. Engineers explore new materials and techniques to enhance performance and efficiency. The industry's future looks bright, with potential growth driven by the demand for strong, lightweight solutions. This focus on strength and innovation supports the development of reliable and sustainable products.