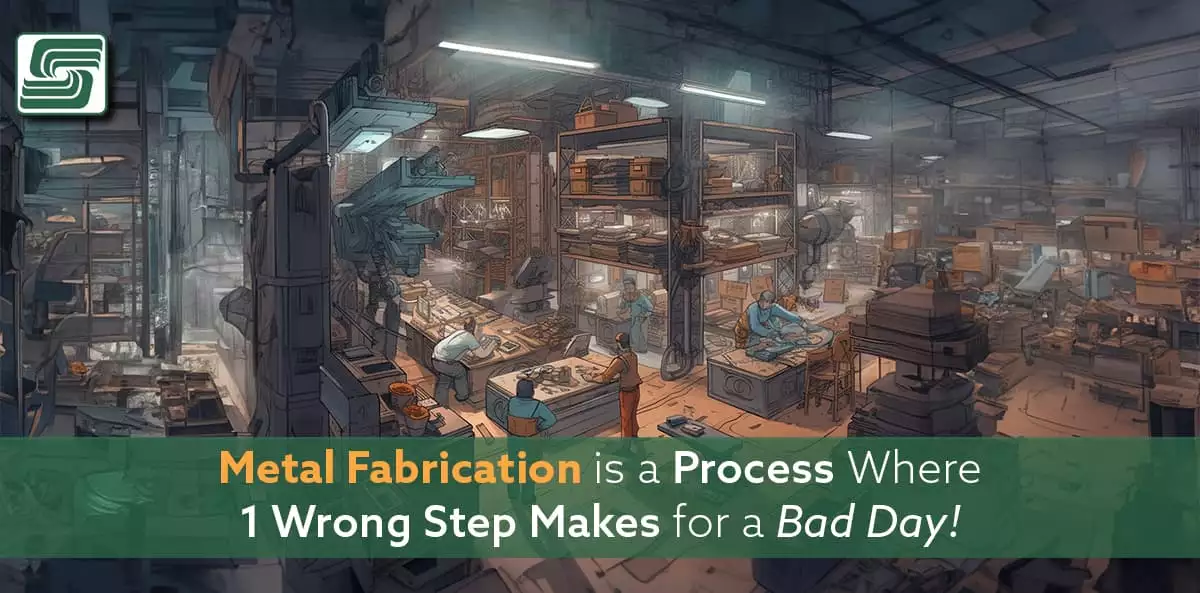
Metal fabrication, or making things out of metal, is very important. It helps many industries like car-making, building, and airplane production.
This piece talks about four big problems in metal fabrication. These are: getting materials is tough, costs too much, rules are hard to follow, and new technology is hard to use.
By looking at these problems, we can learn about the industry and how to improve it.
Metal Fabrication 101
The metal fabrication industry turns raw metal into different products, done by cutting, bending, welding, and putting together. These products can be simple things like brackets, pipes, or complex parts used in advanced tech.
Metal fabrication is a mix of art and precision. It needs skilled workers who can work with metals like steel, aluminum, and copper.
Metal Fabrication Projects Importance
Metal fabrication is vital in many areas. In construction, metal structures give strength and look good. Cars use a lot of fabricated metal for the body and other parts, ensuring safety and good performance. Companies that make airplanes need exact metal parts to meet high standards. They need to work well in extreme conditions.
Other industries also use metal fabrication. These include energy production facilities that need custom equipment and the medical industry that requires precision parts. All sectors use metal fabrication for their needs.
Connected Challenges?
These four challenges aren't separate. They are linked and often make each other worse.For example, costs go up if it's hard to get materials because of higher transport costs.
Similarly, following rules can also make things more expensive. It might mean extra training or better safety measures.Understanding these links can help us tackle these problems.
Meeting These Challenges
Metal fabrication projects are important. They link with many industries. Because of this, we need to deal with the challenges. We must solve problems like supply chain issues, costs, rule-following, new technology, and lack of skills. To do this, we need innovative, cooperative, and adaptable solutions.
Problem 1: Supply Chain Issues
What is the Metal Fabrication Supply Chain?
Metal fabrication projects have a complicated supply chain, which includes getting raw materials and delivering the final product.
The supply chain manages all the steps needed to turn raw materials into finished metal products, including getting materials like steel or aluminum. These materials are then transported to factories and turned into products through cutting, welding, and other processes. After this, they're sent to the customers.
How do Global Events Affect the Supply Chain?
Global events like COVID-19 really affected the supply chain in metal fabrication. It caused problems in transportation, a lack of workers, and factories closing.
These problems delayed getting materials and slowed down production, leading to projects being delayed and costs going up. Things like trade issues or natural disasters can also cause problems.
For example, sudden extra costs on imported steel can raise prices. Natural disasters can damage transport routes and delay deliveries.
Solving Supply Chain Solutions
To solve these problems, companies need to have a plan:
- Use different suppliers: Companies shouldn't rely on one supplier. They should use many ones to avoid issues.
- Local sourcing: Using local suppliers is less risky. They are not affected by global events and can deliver faster.
- Strong relationships: Good relationships with suppliers can help. It makes communication easier, meaning companies react better to problems, spot risks, and plan for issues.
- Good inventory management: Keeping enough stock can help during unexpected events. Companies can use just-in-time strategies or safety stock.
- Use technology: Technology like supply chain management software can help monitor materials. It can spot issues in the supply chain and stop problems before they happen.
By using these strategies, metal fabrication projects can be more ready for problems. They can keep running smoothly, even when things are tough.
Problem 2: Costs Going Up
Why are Costs Rising?
There are many reasons costs go up in metal projects. These affect how much money the projects make. One big reason is that the price of raw materials like steel, aluminum, and copper can change a lot.
Prices can change because of things like worldwide demand, global events, and trade rules. When raw materials cost more, the whole project becomes more expensive, making it hard for metal workers to make a profit.
Another reason is labor costs. Metal projects need skilled workers who can do things like cutting, welding, and assembly. But there aren't always enough of these workers, which means they can ask for higher wages, which increases labor costs. The need for special training or certifications also adds to the expenses.
Affects on Project Budgets and Profits?
Rising costs really hurt project budgets and profits. When raw materials or labor costs more than expected, it puts a lot of pressure on the project's budget.
Companies may have to pay these extra costs or charge their clients more, lowering profits in this very competitive industry.
Metal companies have little room for error because of tough competition and market demands. If costs go up without more revenue, companies may not make as much profit or even lose money if they're not careful.
What Can be Done?
Companies can try different ways to save money to deal with costs going up. One way is by making their processes more efficient. By identifying and eliminating wasteful practices, metal workers can be more productive.
Not only does this save money, but it also makes the final products better. Another way to save money is automation.
With advanced machines and robots, companies can work more accurately and quickly and need fewer workers. Automation can lower labor costs and increase efficiency while keeping quality high.
Companies can also find different ways to get raw materials, including finding better-priced suppliers or using cheaper materials that work.
Working with clients throughout the project also helps save money. By involving clients early on, both sides can work together to improve the design and materials without worsening performance or quality.
Dealing with costs going up needs a complete plan, including efficient processes, new technology, smart decisions on where to get materials, and good partnerships.
By using these money-saving methods, metal businesses can deal with rising costs, helping keep making money and be successful in the long term.
Problem 3: Following Rules and Regulations
What Rules Does the Metal Industry Follow?
The metal industry needs to follow a lot of rules. These are important for keeping people safe, protecting the environment, and ensuring things are done right.
Environmental rules help control the effect of metalwork on things like air quality, water, and waste. These rules often include limits on pollution, how to get rid of dangerous waste, and saving resources.
Safety rules are there to protect workers. These can include taking care of equipment, wearing the right safety gear, and knowing what to do in an emergency. Metal workers also have to follow other rules depending on their work.
For example, companies that work on cars or airplanes must follow strict quality control rules. Companies must also follow labor laws and ethical rules to ensure workers are treated fairly.
What problems?
Following these rules can be hard for metal workers. One big problem is dealing with a lot of paperwork. Companies must keep track of things like pollution levels, how they handle waste, keep workers safe, and control quality.
Getting this information is hard and takes a lot of time and resources. Training is another problem. Companies must spend much time and effort teaching their workers the rules and how to do their jobs safely.
Keeping up with changing rules is also a challenge. Rules can change because of new technology or because people's priorities change. Companies that don't keep up can get in trouble or hurt their reputation.
Rules aren't just Words
- Following rules is not just a legal requirement. It's also important for a company's reputation and for staying in business in the long term.
- Following environmental rules show that a company cares about the environment, making customers, investors, and the public think more highly of the company and attract clients who care about the environment.
- Safety rules help create a workplace where employees feel safe. These rules may attract skilled workers and reduce the risk of accidents, protecting workers and the company from legal problems.
- Quality control rules help improve the products and keep customers happy. Companies that meet or even go beyond these standards can get ahead of their competition. They show they can consistently deliver good products that meet customers' expectations.
- Following rules is a key part of metalwork. Understanding the many environmental, safety, labor, and quality control rules is important for success.
Companies must overcome problems with paperwork, training, and keeping up with changing rules. Following these rules ensures companies meet their legal requirements, improves their reputation, and is key for staying in business in this changing industry.
Problem 4: New Technology and Need for Skills
New Technology
Every day, new technology is changing how metalwork is done. One example is CNC machining, which uses computer software to control machines with great precision. It eliminates manual work and makes metalwork projects more productive, accurate, and efficient.
Another new technology is additive manufacturing, also known as 3D printing. This technique builds complex metal structures layer by layer, which opens up new design possibilities and reduces waste.
The Need for Skills
While new technology has much potential to improve metalwork, it also creates a skills gap problem. As technology changes quickly, workers need to keep learning new skills. But, many companies have trouble finding workers with the right skills to use and care for advanced machines.
This shortage slows down work and stops new ideas in the industry. Schools and the industry need to work together to fix this skills gap.
Training programs can teach workers the necessary skills. They can learn how to use new equipment through hands-on experience. Apprenticeships provide a chance for new workers to learn from experienced ones.
How Automation Affects Metal Work
Automation is changing how metalwork is done. Robots can do repetitive tasks, like welding or moving materials, accurately and efficiently, speeding up production and reducing errors.
Robots also make the workplace safer by doing dangerous tasks. However, automation doesn't mean humans will lose their jobs.
Instead, it's a chance for workers to learn new skills and move to higher-level jobs. Companies can train workers to use and care for automated systems, creating a team combining human expertise with technology.
Adapting to Changes
To succeed in the face of new technology and the skills gap, metalwork companies must keep learning and trying new things, which means investing in research to stay up-to-date with new technology.
Working with schools, industry groups, and tech companies can help businesses get the latest knowledge and tools. A work environment encouraging creativity and problem-solving can help workers adapt to new technology more easily.
Companies can form teams with diverse skills and viewpoints to foster collaboration. Metalwork companies can overcome challenges and discover new opportunities by developing talent within their organizations.
Denique
As we enter a new era of metalwork, embracing new technology is crucial for staying competitive. Although new technology can create problems like the skills gap, it also brings exciting opportunities for growth and new ideas.
Companies can adapt to these changes by investing in training, working with schools, using automation wisely, and promoting a culture of continuous learning. In this era of progress, where machines work alongside skilled workers, there's no limit to what we can achieve in metalwork projects.
Every challenge we overcome, whether it's disruptions in the supply chain or rising costs, strengthens us. The future is bright for those who are bold enough to adapt!