![]()
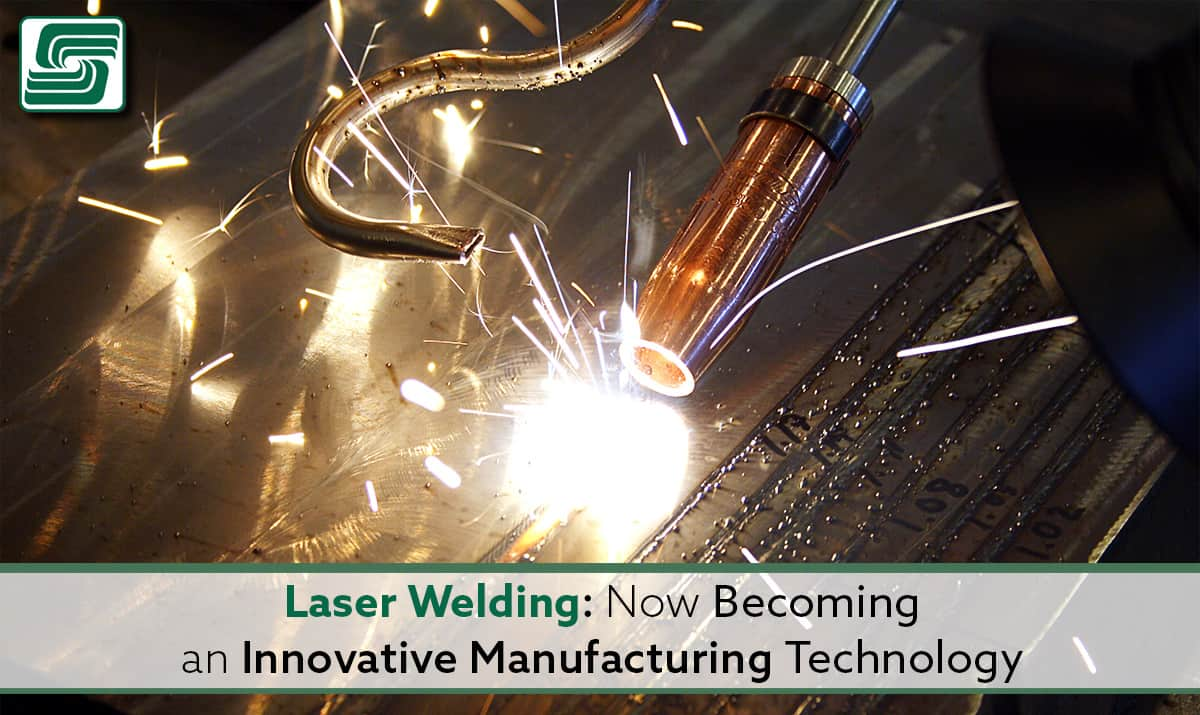
Laser Welding is an innovative and cost-effective industrial manufacturing process used to fuse materials with high accuracy and precision. The technology uses a laser as its primary energy source to produce welded parts with excellent mechanical properties, minimum distortion, and minimal chemical impact on the base material.
Laser welding is also known as CO2 laser welding or infrared laser welding. The technique has many benefits for manufacturers in a wide range of industries used for spot or seam welding of metals, plastics, or other materials in various applications, including aerospace, automotive, food processing, medical devices, and oil and gas production.
This post explores the advantages of using laser welding over other common methods such as hot air or spark welding.
What Makes Laser Welding Different?
Lasers can switch from continuous seams to stitching during one continuous operation, providing a replacement for spot welding. Car factories continuously weld automobile door frames across the front and rear of the door frame using continuous seams, where hinge loads and side-impact resistance are important, using stitch welds at the roofline and door sill. There are several advantages to assembling without having to change equipment or methods.
Laser configuration includes focus spot size and light frequency. Butt welds are typically joined with a gap between the sheets of 3 percent to 10 percent, with the general guideline being the thinnest sheet. The reflectivity of the metal being welded is an important factor, which is why semiconductor lasers (disc, fiber, and YAG) are particularly efficient at welding reflective metals.
Because of the laser's high temperature and concentration, autogenous laser welding is typically done without filler. A filler is needed, however, to prevent hot cracking in 2000-series aluminum alloys. Laser welding is effective with many materials, including stainless steel, titanium, tough materials such as high-strength steels used in vehicles, and supply chain subassemblies. It is also applied in hot stamping operations, which use boron-containing alloys.
Laser welding may be used with chromium steels with a carbon content of up to 3% or 3.5% - 4%, as long as the carbon content is less than 3%.
Laser Welding Benefits
Laser welding offers several benefits over other welding technologies. These include high penetration rate, no fusion zone, high consistency, and excellent finish. Laser welding has a higher penetration rate than hot air or sparks welding, meaning it fuses thicker materials than those welded using a hot air or spark welding process.
Since laser welding does not create a fusion zone, it is ideal for welding different metals. Laser welding is a highly consistent process. This means it produces consistent welds, regardless of who operates the laser welder. The process produces an excellent smooth weld finish, making it suitable for applications where aesthetics matter, such as in the medical industry.
Simple Design and Setup
Laser welding is a relatively simple process that generally involves placing the materials to be welded under the laser head, setting the parameters for the weld, and then striking an arc between the materials. The welded parts must be clean and free from dirt, oil, or other contaminants achieved by using cleaning fluid or sandpaper to remove any dirt from the surface of the parts.
The design and setup of a laser weld system are relatively simple compared to other welding processes, such as arc welding, resistance welding, or electron beam welding. This means that laser welding systems are easier to establish and operate and better suited for entry-level welders.
High Rate of Penetration
Laser welding has a high penetration rate, so it is suitable for welding thicker materials than welded with hot air or spark welding. As a result, aerospace and automotive industries prefer laser welding for thick sheet materials such as aluminum, copper, and steel. Since laser welding does not create a fusion zone, it is ideal for welding different metals.
Reliable and Durable Joints
Since laser welding does not create a fusion zone, it is ideal for welding dissimilar metals. When laser welding, the materials do not mix or chemically react, but fuse two distinct materials to create a joint with both properties. Laser welding can be used either in the focused or defocused condition when welding non-metallic materials such as ceramics, paper, or plastics.
When the laser is in the focused condition, it has a limited spot size, which enables it to create strong welds with high penetration rates. When the laser is in the defocused condition, it produces a larger spot size and is suitable for welding thicker materials.
Environmentally Friendly
Laser welding produces little to no waste compared to other welding methods, such as arc welding. Laser welding is environmentally friendly and suitable for eco-friendly manufacturing environments. When laser welding, the only waste is the CO2 used for the process.
In comparison, arc welding produces slag, smoke, and fumes, while resistance welding produces fumes. Laser welding does not require a shielding gas as arc welding does.
Limitations of Laser Welding
As with any welding process, laser welding has a few limitations. These include the need for a clean, flat, and vibration-free surface, limited weld joint strength, and some materials that cannot be welded. When welding materials that are not perfectly clean or flat, there is a chance for distortion in the weld, avoided easily by ensuring a clean surface and leveling the materials.
Further, laser welding has a limited weld joint strength. When welding metals, the joint strength is approximately ten times higher than the strength of the base metals.
However, when welding plastics and other materials, the joint strength is approximately five times lower than the strength of the base material.
In Sum
Since introducing laser welding, this process has become popular in manufacturing industries. Companies often use it in place of other welding processes, such as hot air or spark welding. We also know the laser welding process as CO2 laser welding, infrared laser welding, CO2 arc welding, and CO2 friction welding.
Laser welding is an industrial manufacturing process in which one or more laser beams are used to fuse different materials. The process takes advantage of the properties of CO2 gas and a high-power CO2 laser to produce an excellent weld with excellent finish, strength, and minimal chemical impact on the base materials.
Laser welding offers several benefits over other welding processes. These include high penetration rate, no fusion zone, high consistency, and excellent finish. Laser welding has a higher penetration rate than hot air or spark welding, meaning it fuses thicker materials than those welded using a hot air or spark welding process.
Since laser welding does not create a fusion zone, it is ideal for welding dissimilar metals.
Image Attribution: Cover Image • Laser Welding Pipeline