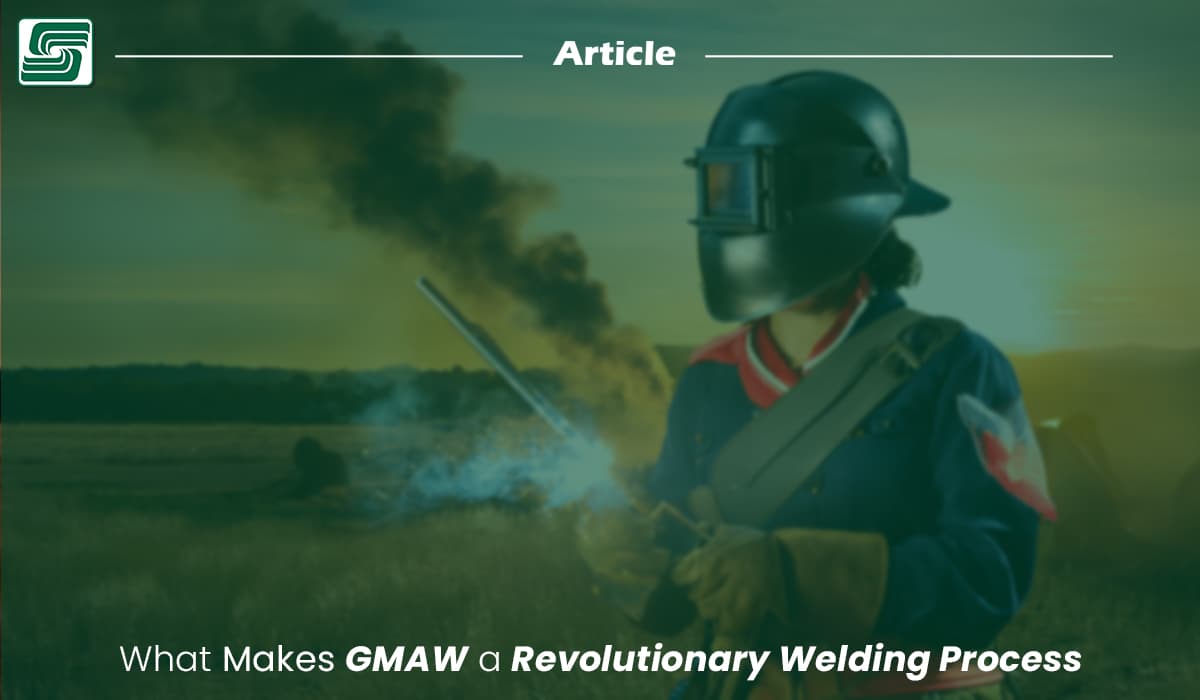
Gas Metal Arc Welding (GMAW) transformed the industry by delivering unmatched speed, precision, and adaptability. Unlike traditional methods, this process uses a continuous wire electrode and shielding gas to create clean, high-quality welds. Its efficiency reduces project completion times, while its versatility makes it suitable for various industries, including automotive, aerospace, and construction.
GMAW welding is a reliable solution for consistent results across different materials and applications. This innovation has become a cornerstone of modern manufacturing, shaping how industries approach welding tasks today.
Understanding GMAW: The Basics
Gas Metal Arc Welding (GMAW), or MIG welding, is a modern technique that uses electricity to join metals.
This method stands out for its efficiency and precision. Unlike older techniques, GMAW welding produces clean, high-quality welds with minimal spatter. It works well on various materials, including aluminum, steel, and stainless steel, making it a versatile choice for automotive, aerospace, and construction industries.
Key Components of GMAW Welding
- Wire Electrode: The wire electrode plays a critical role in GMAW welding. It acts as the filler material, melting to form the weld. Typically, the wire is made of mild steel and coated with a thin layer of copper. This copper coating improves electrical conductivity, extends the contact tip's life, and enhances overall arc performance. The continuous feed of the wire ensures a steady supply of filler material, allowing you to maintain consistent weld quality throughout the process.
- Shielding Gas: Shielding gas is essential in GMAW welding. It protects the molten weld pool from reacting with atmospheric gases like oxygen, nitrogen, and hydrogen. Without this protection, the weld could become porous or weak. Common shielding gases include carbon dioxide, argon, or both. Each type of gas offers unique benefits. For instance, carbon dioxide penetrates deeper, while argon ensures smoother welds. The shielding gas flows through the welding gun and protects the weld even as it cools, ensuring a strong and durable bond.
A Step-by-Step Guide on How GMAW Welding Works
- Preparation: Begin by setting up your equipment, including connecting the power supply, attaching the wire feed unit, and selecting the appropriate shielding gas. Ensure the welding gun is configured for DC positive polarity.
- Positioning: Secure the metal pieces you want to weld. Clean the surfaces to remove dirt, rust, or oil, which could affect the weld quality.
- Wire Feeding: Load the wire electrode into the wire feed unit. Adjust the feed speed to match the welding requirements.
- Shielding Gas Flow: Open the gas cylinder and set the flow rate. The gas will flow through the gun nozzle, creating a protective shield around the weld area.
- Welding: Hold the welding gun at the correct angle and distance from the workpiece. Pull the trigger to start the arc, which melts the wire electrode and the base metal. Move the gun steadily along the joint to create a uniform weld.
- Cooling: Let the weld cool naturally. The shielding gas will flow briefly after welding, protecting the molten metal as it solidifies.
Following these steps helps you achieve precise and reliable results with GMAW welding. This process simplifies complex welding tasks, making it accessible even for beginners while maintaining professional-grade quality.
The Historical Development of GMAW
The roots of modern welding trace back to the late 1800s when using an electric arc to join metals first emerged. Early arc welding methods, such as carbon arc welding, struggled with inefficiencies. Heat control was poor, and weld quality often lacked consistency. These limitations made early techniques unsuitable for large-scale industrial use.
In the 1920s, researchers began experimenting with shielding gases like argon and helium. These gases protected the molten weld pool from atmospheric contamination, improving weld quality. This innovation laid the groundwork for future advancements in welding technology.
By the 1930s, introducing consumable electrode wires allowed for continuous feeding, increasing efficiency and setting the stage for developing more advanced welding processes.
The Invention of Gas Metal Arc Welding (GMAW)
In the history of GMAW, the 1940s marked a turning point in welding history.
This invention offered significant advantages over older methods. GMAW provided higher deposition rates, which reduced welding time and increased productivity. It also produced cleaner welds, minimizing the need for post-weld cleanup. These benefits made GMAW a cost-effective alternative to other processes, like Gas Tungsten Arc Welding (GTAW).
Although early systems were expensive and required skilled operators, their potential to transform industrial welding was undeniable.
Key Milestones in MIG Welding History
Introduction of Shielding Gases: Introducing shielding gases was a pivotal moment in MIG welding history. Early GMAW systems relied on helium, which worked well for non-ferrous metals but was costly. In the 1950s, using carbon dioxide as a shielding gas made the process more affordable and versatile. While carbon dioxide produced deeper penetration but also created more spatter than argon. This trade-off expanded GMAW’s applications, particularly in welding steels.
Adoption of CO₂ as a Shielding Gas: The adoption of carbon dioxide further enhanced GMAW’s appeal. CO₂ offered a cost-effective solution for industries that required high welding speeds and deep penetration. This innovation made GMAW accessible to various industries, including automotive and construction. By the mid-20th century, GMAW had become a preferred method for welding various materials, from thin sheets to thick plates.
Rise of Robotic GMAW Systems: The 1980s saw the rise of automation in welding. Robotic GMAW systems transformed manufacturing processes by delivering consistent weld quality and high productivity. These systems became popular in the automotive industry, where precision and speed were critical. Automation allowed GMAW to handle complex tasks with minimal human intervention, solidifying its role as a cornerstone of modern fabrication.
Types of GMAW Welding Processes
Understanding these GMAW welding processes helps you choose the right approach for your project.
Short-Circuit Transfer
Short-circuit transfer, also known as dip transfer, is one of the most versatile methods in GMAW. In this process, the wire electrode touches the workpiece, creating a short circuit. The heat melts the wire tip, transferring the molten metal to the joint. This cycle repeats rapidly, often hundreds of times per second.
This method works well for thin materials and out-of-position welding, such as vertical or overhead joints. It produces minimal spatter, making it ideal for applications requiring clean welds. However, it operates at lower heat levels, which limits its use of thicker materials. This method is useful for automotive repairs or light fabrication tasks.
Globular Transfer
Globular transfer involves the formation of larger droplets of molten metal that transfer from the wire electrode to the workpiece. Unlike short-circuit transfer, the wire does not touch the workpiece. Instead, the droplets fall because of gravity, creating a less controlled process.
This method is suitable for welding thicker materials where deeper penetration is required. However, it generates more spatter and less aesthetic welds than other methods. You should use globular transfer when appearance is less critical, such as in structural welding or heavy equipment manufacturing. Its higher heat levels make it effective for joining steel and other robust materials.
Spray Transfer
Spray transfer offers a smooth and continuous flow of tiny molten metal droplets from the wire electrode to the workpiece. This process requires higher voltage and current settings, creating a stable arc and minimal spatter. The result is a clean, high-quality weld with excellent penetration.
This method excels at welding thick materials and is commonly used in industrial applications like shipbuilding and pipeline construction. Because of the high heat involved, it works best in flat or horizontal positions. Spray transfer is the go-to choice if your welds need precision and strength. It is particularly effective for non-ferrous metals like aluminum and stainless steel.
Transfer Type |
Key Features |
Best Applications |
Short-Circuit Transfer |
Low heat, minimal spatter, versatile |
Thin materials, out-of-position welding |
Globular Transfer |
Larger droplets, deeper penetration |
Structural welding, heavy equipment |
Spray Transfer |
Smooth flow, high-quality welds |
FThick materials, industrial applications |
Each welding process offers unique advantages. Understanding these metal transfer methods allows you to select the most effective approach for your welding needs.
Pulsed-Spray Transfer
Pulsed-spray transfer significantly advances Gas Metal Arc Welding (GMAW) technology.
The process creates a stable arc that periodically delivers bursts of energy. During the high-energy phase, molten metal droplets transfer from the wire electrode to the workpiece in a controlled manner. The low-energy phase allows the weld pool to cool slightly, preventing overheating and minimizing distortion. This cycle repeats rapidly, ensuring consistent weld quality and reducing spatter.
Advantages of Pulsed-Spray Transfer
- Versatility: Pulsed-spray transfer adapts to various materials and thicknesses, including aluminum, stainless steel, and thin sheets.
- Reduced Heat Input: The pulsing current minimizes the risk of warping or damaging heat-sensitive materials.
- Improved Weld Quality: This method produces clean, smooth welds with minimal spatter, reducing the need for post-weld cleanup.
- Out-of-Position Welding: The controlled heat input makes welding in vertical, overhead, or other challenging positions easier.
Applications of Pulsed-Spray Transfer
This method excels in industries where precision and adaptability are crucial. For example:
- Aerospace: Welding lightweight materials like aluminum with high accuracy
- Automotive: Joining thin panels and components without compromising structural integrity.
- Construction: Tackling complex welding tasks in various positions.
Feature |
Pulsed-Spray Transfer |
Spray Transfer |
Heat Input |
Lower, controlled |
Higher, constant |
Material Compatibility |
Thin and thick materials |
Primarily thick materials |
Welding Positions |
All positions |
Flat and horizontal only |
Spatter |
Minimal |
Minimal |
Mastering pulsed-spray transfer expands your welding capabilities and achieves professional-grade results across diverse projects. This method stands out among the GMAW welding processes for its balance of precision, efficiency, and versatility.
Advantages of GMAW Welding
Efficiency and Speed in Welding
GMAW welding stands out for its remarkable efficiency and speed. The continuous wire feed eliminates interruptions, allowing you to maintain a steady workflow.
Using advanced modes like pulsed-spray transfer further boosts efficiency. This method minimizes heat input while maintaining a stable arc by alternating between high and low current levels. This approach reduces spatter and improves control, enabling you to complete tasks faster without compromising quality. Whether working on automotive repairs or large construction projects, GMAW welding ensures you achieve your goals quickly and precisely.
Precision and High-Quality Welds
GMAW welding delivers exceptional precision, producing clean and high-quality welds. The shielding gas in this process protects the molten weld pool from atmospheric contamination, ensuring a strong and durable bond. This protective barrier prevents defects like porosity and oxidation, resulting in welds that meet professional standards. For example, pulsed spray GMAW offers improved control over the weld pool size and bead appearance, making it ideal for applications requiring meticulous attention to detail.
The versatility of GMAW welding techniques allows you to achieve consistent results across various materials.
Versatility Across Materials and Applications
GMAW welding offers versatility, making it suitable for various materials and applications. The process accommodates metal transfer methods, such as short-circuit, globular, spray, and pulsed-spray transfer. Each method caters to specific needs, allowing you to tackle diverse projects confidently. For instance, short-circuit transfer works well for thin and out-of-position welding, while spray transfer excels in welding thick materials with high heat input.
This adaptability extends to various industries. In construction, GMAW welding handles structural tasks with ease. It joins thin panels and components in the automotive sector without compromising strength. The aerospace industry benefits from its ability to weld lightweight materials like aluminum with precision. Even in small-scale projects, GMAW welding proves invaluable because of its ease of use and accessibility. Its ability to switch between MIG welding and MAG welding processes further enhances its flexibility, ensuring you can meet the demands of any task.
Ease of Use and Accessibility for Welders
Gas Metal Arc Welding (GMAW) simplifies the welding process, making it accessible to beginners and experienced welders. Its design prioritizes ease of operation, reducing the learning curve and enabling professional results with minimal training. Unlike traditional welding methods that require extensive skill and practice, GMAW provides a straightforward approach to joining metals.
One key feature that enhances usability is the continuous wire feed system. This system eliminates frequent electrode changes, allowing you to focus on maintaining a steady arc and consistent weld quality. The automated wire feeding ensures a smooth workflow, reducing interruptions and improving efficiency. Whether working on a small repair or a large industrial project, this feature keeps the process manageable and efficient.
Integrating pulsed-spray transfer modes further enhances accessibility. This advanced technique alternates between high and low current levels, creating a stable arc and reducing heat input. The controlled heat makes it easier to weld thinner materials and tackle out-of-position tasks, such as vertical or overhead welding. This mode gives you greater control over the weld pool, minimizing distortion and spatter. This precision allows you to achieve clean, high-quality welds without requiring extensive experience.
GMAW also offers versatility in material compatibility. You can weld various metals, including aluminum, stainless steel, and mild steel, by adjusting the settings and selecting the appropriate shielding gas. For instance, pulsed spray GMAW works exceptionally well with aluminum and stainless steel, delivering precise welds with minimal spatter. This adaptability ensures you can handle diverse projects without specialized equipment or techniques.
Modern GMAW systems often include user-friendly features like digital controls and pre-programmed settings. These innovations simplify parameter adjustments, allowing you to select the optimal settings for your material and application. For example, synergic systems automatically adjust voltage, current, and wire feed speed based on your chosen parameters. This automation reduces the guesswork, making the process more intuitive and accessible.
Limitations of GMAW Welding
Equipment Costs and Maintenance Requirements
GMAW welding requires specialized equipment, often with a higher upfront cost than other welding techniques.
Maintenance also plays a critical role in keeping the equipment functional. Ensuring consistent performance is possible because of regular upkeep, such as:
- Cleaning the welding gun nozzle
- Replacing worn-out contact tips
- Inspecting the wire feed system
Neglecting maintenance leads to equipment malfunctions, disrupting workflow, and increasing repair costs. While the initial investment and ongoing maintenance might seem daunting, they are necessary to maintain the efficiency and reliability of GMAW welding.
Sensitivity to Environmental Conditions
GMAW welding is highly sensitive to environmental conditions, particularly wind and humidity.
Humidity also poses challenges. Excess moisture causes the base metal to rust, compromising the weld quality. It may lead to hydrogen absorption in the weld, increasing the risk of cracking. To mitigate these issues, always ensure a clean and dry workspace. Using windshields or enclosures can help protect the welding area when working outdoors, but these measures add complexity to the process.
Challenges in Certain Welding Positions
While GMAW welding excels in flat and horizontal positions, it becomes more challenging in vertical or overhead positions. The molten weld pool sags or drips because of gravity, making it difficult to maintain control and achieve a uniform weld. This limitation restricts the use of GMAW in applications requiring out-of-position welding.
Advanced techniques, such as pulsed-spray transfer, offer some solutions by reducing heat input and improving control. However, these methods require precise parameter adjustments and a higher skill level. If your project involves complex welding positions, you may need to explore alternative welding techniques or invest additional time mastering advanced GMAW methods.
Comparing GMAW with Other Welding Methods
GMAW vs. SMAW
Gas Metal Arc Welding (GMAW) and Shielded Metal Arc Welding (SMAW) differ significantly in their approach and usability. GMAW uses a continuous wire electrode and shielding gas, while SMAW relies on a consumable stick electrode coated with flux. This fundamental difference impacts how you work with each method.
GMAW offers greater efficiency and ease of use. The continuous wire feed eliminates the need to stop and replace electrodes, allowing you to maintain a steady workflow. In contrast, SMAW requires frequent electrode changes, which interrupt your progress. If you're new to welding, GMAW provides a simpler learning curve. Its one-hand operation and automated wire feeding make it more accessible for beginners. SMAW, however, demands more skill and practice to master.
GMAW depends on shielding gas, which disperses easily in windy conditions.
Heat Input |
GMAW |
SMAW |
Electrode Type |
Continuous wire |
Consumable stick |
Learning Curve |
Easier for beginners |
Requires more skill |
Efficiency |
High |
Moderate |
Outdoor Suitability |
Limited |
Excellent |
GMAW vs. TIG Welding
The focus shifts to precision and versatility when comparing GMAW to tungsten inert gas (TIG) welding. TIG welding uses a non-consumable tungsten electrode, requiring you to feed filler material manually. This method gives you exceptional control over the weld, making it ideal for intricate tasks and thin materials.
GMAW, however, prioritizes speed and efficiency. Its continuous wire feed and automated process allow you to complete projects faster. TIG welding is slower because of its manual nature. If you're working on large-scale industrial tasks, GMAW proves more practical. TIG welding shines in applications where aesthetics and precision matter most, such as aerospace or artistic metalwork.
Another key difference lies in usability. GMAW is easier to learn and operate, making it suitable for welders of all skill levels. TIG welding demands a higher level of expertise. You must coordinate both hands and control the arc and filler material precisely. While TIG welding produces superior weld quality, it requires more time and effort to master.
Feature |
GMAW |
TIG Welding |
Speed |
Faster |
Slower |
Precision |
Moderate |
High |
Usability |
Beginner-friendly |
Advanced |
Applications |
Large-scale tasks |
Intricate and aesthetic projects |
GMAW vs. FCAW
Flux-Cored Arc Welding (FCAW) shares similarities with GMAW but differs in electrode and shielding methods.
GMAW excels in producing clean and precise welds. Its shielding gas creates a stable arc and minimizes spatter, producing high-quality welds. FCAW, while effective, produces more spatter and requires additional cleanup. If you're working on projects that demand a polished finish, GMAW is the better choice.
FCAW offers an advantage in welding thicker materials. Its flux core provides deeper penetration, making it ideal for heavy-duty applications like shipbuilding or structural welding. GMAW, while versatile, performs best on medium-thickness materials. For general-purpose tasks, GMAW provides a balance of efficiency and quality.
Feature |
GMAW |
FCAW |
Shielding Method |
External gas |
Flux core |
Outdoor Suitability |
Limited |
Excellent |
Weld Quality |
Cleaner, less spatter |
More spatter |
Material Thickness |
Medium |
Thick |
By understanding these comparisons, you can choose the welding technique that best suits your project requirements. Each method has unique strengths, making them valuable tools for different applications.
The Impact of GMAW on the Welding Industry
Transforming Manufacturing Processes
Gas Metal Arc Welding (GMAW) has revolutionized manufacturing by streamlining production and enhancing efficiency. This welding process introduced continuous wire feeding, eliminating interruptions caused by frequent electrode changes. As a result, you achieve faster welding speeds and higher deposition rates, making GMAW welding ideal for large-scale industrial tasks.
The adaptability of GMAW welding also plays a crucial role in its impact. Whether you work with aluminum, stainless steel, or mild steel, this process ensures high-quality results across various materials. Its ability to handle diverse applications, from lightweight components to heavy-duty structures, makes it indispensable in manufacturing. Integrating GMAW into your production line allows you to optimize workflows and maintain a competitive edge in today’s fast-paced industrial landscape.
Enhancing Productivity in Construction
GMAW welding has become a game-changer in construction by improving productivity and ensuring structural integrity. The process allows you to complete projects faster because of its high deposition rates and continuous operation. Unlike traditional methods, GMAW welding minimizes downtime, enabling you to focus on creating strong and durable welds. This efficiency proves invaluable in large-scale construction projects where time constraints are critical.
GMAW welding excels in joining thick materials, making it suitable for structural tasks like building frameworks and bridges. Its versatility extends to out-of-position welding, allowing you to easily tackle challenging angles and positions. Advanced techniques like pulsed-spray transfer enhance control and reduce heat input, ensuring precision even in complex welding scenarios. By adopting GMAW, you contribute to safer and more reliable construction practices while meeting tight deadlines.
Contributions to Automotive and Aerospace Industries
The automotive and aerospace industries have benefited from the innovations brought by GMAW welding.
GMAW plays a vital role in joining lightweight yet strong materials in aerospace. The precision offered by pulsed-spray transfer ensures critical components' structural integrity. Whether you work on aircraft frames or intricate engine parts, GMAW welding provides the reliability and accuracy required in this demanding industry. Its adaptability to various metal transfer methods allows you to address specific needs, from deep penetration to minimal spatter, ensuring optimal results.
The historical evolution of GMAW, as highlighted in MIG welding history, underscores its transformative impact on these industries. By embracing this advanced welding technology, you contribute to innovations that shape the future of transportation and engineering.
Innovations and Future Trends in GMAW Welding
Automation and Robotics in GMAW
Automation has reshaped how you approach Gas Metal Arc Welding (GMAW). Robotic systems equipped with GMAW technology deliver unmatched precision and consistency. These systems eliminate human error, ensuring every weld meets exact specifications. In industries like automotive and aerospace, robotic GMAW enhances productivity by handling repetitive tasks with speed and accuracy. You benefit from reduced production times and higher-quality results.
Robotic arms integrated with GMAW adapt to complex welding positions. They excel in tasks requiring intricate movements, such as welding curved surfaces or tight corners. Advanced sensors and programming allow these systems to adjust real-time parameters, maintaining optimal performance. For example, a robotic GMAW system can detect variations in material thickness and change the wire feed speed or voltage accordingly. This adaptability ensures consistent weld quality across diverse applications.
The rise of collaborative robots, or cobots, further expands your options. Cobots work alongside human welders, combining automation's precision with manual control's flexibility. You can use cobots to handle repetitive or hazardous tasks while focusing on more creative or complex aspects of welding. This partnership boosts efficiency and reduces fatigue, making your workflow more sustainable.
Advancements in GMAW Equipment and Technology
Modern GMAW equipment incorporates next-gen technology to simplify your welding process. Digital controls and programmable settings allow you to fine-tune parameters like voltage, current, and wire feed speed. These features reduce guesswork, ensuring optimal settings for each project. For instance, synergic systems automatically adjust parameters based on the selected material and shielding gas, streamlining your setup.
Inverter-based power sources have revolutionized GMAW equipment. These compact and lightweight machines offer greater portability, making them ideal for onsite applications. Despite their smaller size, inverter-based systems deliver high performance, providing stable arcs and precise control. You can achieve professional-grade welds without bulky equipment.
Advanced wire electrodes and shielding gas mixtures enhance GMAW’s versatility. Specialized wires improve compatibility with materials like stainless steel and aluminum. Shielding gas innovations reduce spatter and improve weld appearance, minimizing post-weld cleanup. These advancements expand your ability to tackle diverse projects with confidence.
Sustainability and Eco-Friendly Practices in GMAW
Sustainability has become a priority in GMAW welding. Eco-friendly practices reduce environmental impact while maintaining efficiency. Energy-efficient equipment minimizes power consumption, lowering operational costs and carbon footprints. For example, inverter-based systems consume less energy than traditional power sources, making them a greener choice.
Innovations in shielding gases also promote sustainability. Low-emission gas mixtures reduce harmful byproducts, improving air quality in your workspace. These gases protect the weld pool while aligning with environmental standards. By choosing eco-friendly options, you contribute to a cleaner and safer environment.
Recycling plays a vital role in sustainable GMAW practices. You can recycle scrap metal and leftover wire electrodes, reducing waste and conserving resources. Proper maintenance extends the lifespan of your equipment, minimizing the need for replacements. These small changes make a significant difference in creating a sustainable welding process.
Portable and Compact GMAW Machines
Portable and compact Gas Metal Arc Welding (GMAW) machines have revolutionized the way you approach welding tasks. These machines combine advanced technology with a lightweight design, making them ideal for onsite projects and hard-to-reach areas.
Unlike traditional bulky equipment, portable GMAW machines allow you to perform high-quality welding without being confined to a workshop.
The compact size of these machines does not compromise their performance. Inverter-based power sources, a key innovation in modern GMAW equipment, ensure stable arcs and precise control. These systems consume less energy, making them efficient and eco-friendly.
Whether you are working on automotive repairs, construction sites, or small-scale fabrication, portable GMAW machines deliver professional-grade results.
Benefits of Portable GMAW Machines:
- Transportation Ease: The lightweight design allows you to move the machine effortlessly between locations. This feature proves invaluable for fieldwork or remote job sites.
- Space Efficiency: Compact machines occupy minimal space, making them suitable for workshops with limited room. You can store and operate them without cluttering your workspace.
- Versatility: These machines handle various materials, including aluminum, stainless steel, and mild steel. Their adaptability ensures you can tackle diverse projects with a single device.
- Energy Efficiency: Inverter technology reduces power consumption, lowering operational costs. This efficiency aligns with sustainable practices, benefiting your budget and the environment.
- User-Friendly Features: Many portable GMAW machines include digital controls and pre-programmed settings. These features simplify parameter adjustments, ensuring optimal performance even for new welders.
Applications of Portable GMAW Machines:
- Automotive Repairs: Weld thin panels and delicate components with precision.
- Construction Projects: Join structural elements onsite without transporting heavy equipment.
- Maintenance Tasks: Perform quick repairs in factories or industrial facilities.
- DIY Projects: Handle small-scale welding tasks at home with ease.
Feature |
Portable GMAW Machines |
Traditional GMAW Machines |
Size |
Compact and lightweight |
Large and bulky |
Portability |
High |
Low |
Energy Efficiency |
Excellent |
Moderate |
Applications |
Onsite and remote work |
Workshop-based tasks |
Portable GMAW machines empower you to weld with flexibility and efficiency. Their compact design and advanced features make them an essential tool for modern welders, whether you are a professional or a hobbyist.
In Sum
Gas Metal Arc Welding has redefined the welding landscape with its unique speed, precision, and adaptability combination. Its continuous wire feed system ensures uninterrupted operation, significantly increasing productivity. Shielding gas protects the weld pool, resulting in clean, high-quality welds with minimal spatter. GMAW accommodates various materials, from aluminum to stainless steel, making it a versatile choice for industries.
This process delivers consistent results, whether working on thin sheets or thick plates. Its ability to integrate advanced techniques like pulsed-spray transfer further enhances its precision and control, especially for challenging applications.
The process also stands out for its accessibility. GMAW simplifies welding tasks, making it easier for beginners to achieve professional-grade results. Its efficiency and adaptability to different welding positions and materials make it indispensable in the automotive, construction, and aerospace industries.
These revolutionary features have positioned GMAW as a cornerstone of modern welding practices.
GMAW continues to dominate the welding industry due to its unmatched efficiency and versatility. Its high deposition rates and faster welding speeds reduce project completion times, making it ideal for large-scale industrial tasks.
Unlike traditional methods, GMAW minimizes downtime, allowing you to focus on delivering quality results. Its adaptability to various material thicknesses and welding positions ensures that it meets the demands of diverse applications.
The process also supports robotic systems to deliver consistent weld quality in high-volume production environments.
The future of GMAW looks promising, driven by ongoing innovations and technological advancements. Automation and robotics will play an even greater role, enhancing precision and efficiency. Robotic GMAW systems equipped with advanced sensors and programming will easily handle complex tasks, reducing human error and increasing productivity.
Collaborative robots, or cobots, will further expand possibilities by combining automation's precision with manual control's flexibility.
Sustainability will also shape the future of GMAW. Energy-efficient equipment and eco-friendly shielding gas mixtures will reduce environmental impact while maintaining high performance. Portable and compact GMAW machines will continue to gain popularity, offering flexibility for onsite and remote projects.
These advancements will make GMAW more accessible and efficient, ensuring its relevance in an ever-evolving industry.
As industries demand faster, cleaner, and more precise welding solutions, GMAW will remain at the forefront. Its ability to adapt to new challenges and integrate innovative technologies ensures it will continue to shape the future of welding for years to come.
GMAW has revolutionized welding by combining efficiency, precision, and adaptability. Its continuous wire feed and shielding gas system ensure clean, high-quality welds, making it a preferred choice for industries requiring speed and reliability. The process's rich history, from its origins in the 1940s to its modern applications, highlights its transformative role in shaping industrial practices.
As advancements in automation and equipment continue, GMAW remains at the forefront of welding innovation, offering solutions that meet the demands of both today and future demands.
Key Takeaways
- GMAW revolutionizes welding with its continuous wire feed and shielding gas, ensuring clean, high-quality welds with minimal spatter.
- This highly efficient process significantly reduces project completion times, making it ideal for large-scale industrial applications.
- GMAW is versatile and capable of welding various materials, such as aluminum, stainless steel, and mild steel, catering to diverse industries such as automotive and aerospace.
- GMAW's ease of use and accessibility make it suitable for beginners and experienced welders, simplifying complex welding tasks.
- Advanced techniques like pulsed-spray transfer enhance precision and control, allowing effective welding in challenging positions.
- Automation and robotics are transforming GMAW, increasing productivity and consistency in manufacturing processes.
- Sustainability practices in GMAW, such as energy-efficient equipment and eco-friendly shielding gases, are shaping the future of welding.