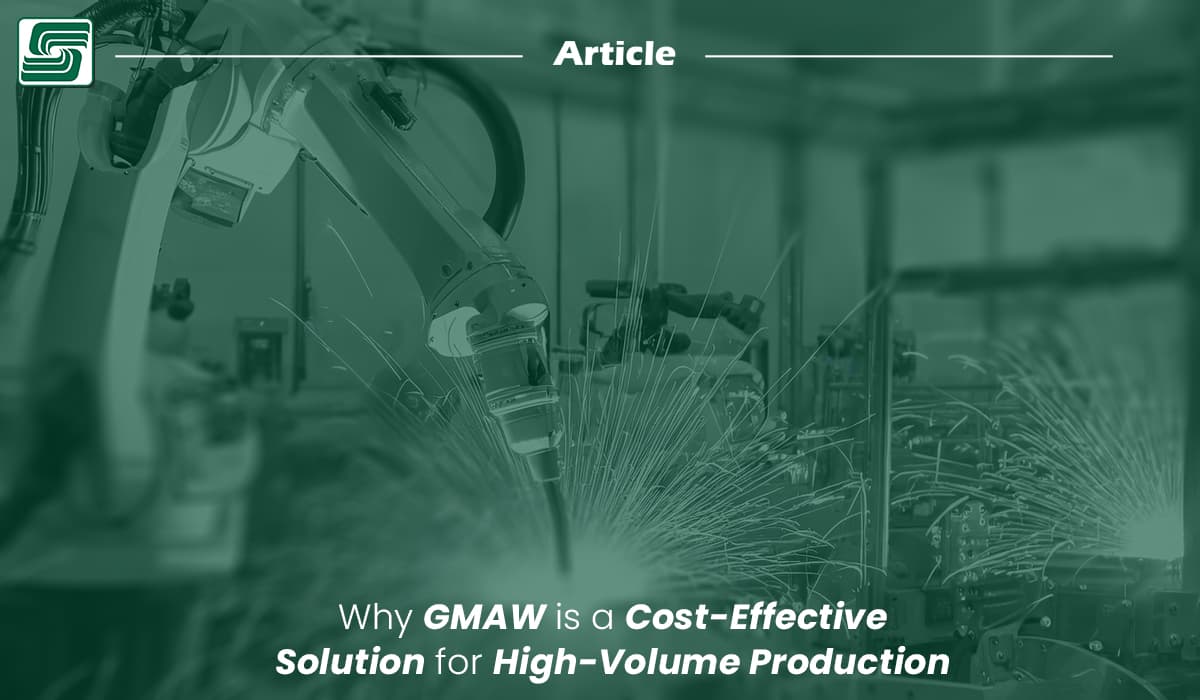
Gas Metal Arc Welding (GMAW) is a cost-effective solution for high-volume production. Its efficiency and material savings make it a preferred choice in various industries. The process achieves high-speed welds, which save time and ensure defect-free results. GMAW's ability to produce cleaner, higher-quality welds with minimal emissions further enhances its appeal.
This welding method also offers consistent quality, reducing the need for rework and boosting productivity.
With its high deposition rates and speed advantages, GMAW efficiently meets the demands of large-scale projects, making it an invaluable asset in manufacturing.
Table: Features, Advantages, and Benefits of GMAW
Feature |
Advantages |
Benefits |
Electrostatic Application |
Uniform Coating |
Even coating thickness, especially in hard-to-reach areas |
Immersion Process |
Complete Coverage |
All surfaces, including internal cavities, are coated |
Water-Based Chemistry |
Environmentally Friendly |
Low VOC emissions and reduced waste |
Cathodic Protection |
Superior Corrosion Resistance |
Long-lasting protection against rust and oxidation |
Controlled Film Thickness |
Optimized Performance |
Precise control over coating properties and durability |
Rapid Curing |
Increased Productivity |
Shorter cycle times and faster turnaround |
Versatility |
Wide Range of Applications |
Suitable for various materials and industries |
Excellent Adhesion |
Durable Finish |
Strong bond between the coating and the substrate |
GMAW Cost Benefits
Reduced Labor Costs
GMAW significantly reduces labor costs in high-volume production. The process allows for automation, which minimizes the need for manual intervention.
Automated systems handle repetitive tasks, freeing up skilled workers for more complex duties. This shift cuts down on labor expenses and enhances overall productivity. Compared to other welding methods, such as SMAW, GMAW requires less manual effort because of its continuous wire feed and shielding gas, which streamlines the welding process.
Material Efficiency
Material efficiency is a major advantage of GMAW. The process uses a continuously fed electrode wire, which ensures consistent material usage and reduces waste. This efficiency saves cost, as less material is wasted during production.
GMAW also produces cleaner welds with minimal spatter, eliminating the need for extensive post-weld cleaning.
This feature contrasts with methods like FCAW, where slag removal is necessary, adding extra steps and costs to the process.
Lower Energy Consumption
GMAW offers lower energy consumption compared to other welding techniques. The process operates at high speeds, reducing the time and energy required for each weld.
This efficiency translates into lower electricity costs, making GMAW an economical choice for large-scale operations. The reduced need for rework because of the high-quality welds produced by GMAW decreases energy usage.
GMAW supports both cost savings and environmental sustainability by optimizing energy consumption.
GMAW Efficiency
Speed of the Welding Process
GMAW excels in speed, making it a top choice for high-volume production. The process achieves rapid welding speeds because of its continuous wire feed system, which allows welders to complete tasks faster than traditional methods.
Various experts highlight that GMAW's one-hand operation enhances control, further boosting speed. Industries like sheet metal and automobile manufacturing benefit from this efficiency, as it reduces production time and increases output.
Automation Capabilities
Automation plays a crucial role in GMAW's efficiency. The process supports automated systems that handle repetitive tasks with precision. This capability minimizes manual intervention, allowing skilled workers to focus on complex projects.
Experts emphasize GMAW's ease of automation, contributing to its popularity in industrial settings. Businesses scale operations and maintain consistent quality by integrating automation and meeting large-scale production demands.
Minimal Downtime
GMAW ensures minimal downtime, a critical factor in maintaining productivity. The process produces clean welds with minimal spatter, reducing the need for post-weld cleaning. This efficiency translates into fewer interruptions and smoother workflow.
Experts note that GMAW's versatility and cleaner results make it a preferred method across various applications. GMAW helps industries maintain steady production rates and meet tight deadlines by minimizing downtime.
GMAW Quality Benefits
Consistent Weld Quality
Gas Metal Arc Welding (GMAW) ensures consistent weld quality, crucial for high-volume production. The process relies on precise parameter control, such as voltage and wire feed speed. This control minimizes defects and enhances the overall quality of the welds.
Research on GMAW Process Parameters' Influence on Carbon Steel Welding highlights the importance of controlling these parameters to achieve superior results. Industries benefit from this consistency, leading to fewer errors and higher first-pass success rates.
Reduced Rework and Waste
GMAW significantly reduces the need for rework and waste in manufacturing. The process produces clean welds with minimal spatter, eliminating the necessity for extensive post-weld cleaning. This efficiency translates into less material waste and fewer resources spent correcting errors.
GMAW minimizes the need for rework by achieving higher first-pass success rates, contributing to overall cost savings.
This waste reduction benefits the bottom line and supports sustainable manufacturing practices.
Enhanced Structural Integrity
The structural integrity of welded components is vital to their performance and longevity. GMAW enhances this integrity by producing strong, reliable welds.
The process's ability to join metals of varying thicknesses ensures components maintain strength under different conditions.
Remanufacturing Research on Failed Cutterheads identifies GMAW as the most suitable method for repairing hob cutter rings, emphasizing its effectiveness in maintaining structural integrity. Industries that rely on durable and robust components find GMAW invaluable for ensuring their products meet high standards.
Comparing GMAW with Other Welding Methods
GMAW vs. Shielded Metal Arc Welding
Gas Metal Arc Welding (GMAW) and Shielded Metal Arc Welding (SMAW) serve different purposes in the welding industry. GMAW excels in high productivity and continuous welding, making it ideal for volume production. It operates efficiently in controlled indoor environments, where automation enhances its effectiveness.
In contrast, SMAW, often known as stick welding, suits outdoor and less controlled settings. It requires more manual skill and results in slower production rates.
GMAW's minimal cleaning needs and ease of automation make it a preferred choice for industries focused on efficiency and speed.
GMAW vs. TIG (Tungsten Inert Gas) Welding
Tungsten Inert Gas (TIG) Welding offers precision and control, making it suitable for projects requiring detailed work.
However, GMAW provides advantages of speed and ease of use. TIG welding demands a high level of skill and patience, as it involves a slower process.
GMAW, with its continuous wire feed, allows for faster task completion. While TIG welding produces high-quality welds,
GMAW achieves similar results with less time and effort. Industries prioritizing rapid production and cost-effectiveness often choose GMAW over TIG welding.
GMAW vs. Flux-Cored Arc Welding
Flux-Cored Arc Welding (FCAW) shares similarities with GMAW but differs in several key aspects. GMAW incurs lower costs and produces cleaner welds. It emits less smoke and fumes, contributing to a safer working environment. FCAW, while effective in outdoor settings because of its flux core, often requires more cleanup.
GMAW's simplicity and cost-effectiveness in material usage and cleanup make it a favorable option for high-volume production.
Industries seeking to minimize expenses and maintain quality often prefer GMAW over FCAW.
TABLE: Comparing SMAW to SMAW, TIG, and FCAW
Aspect |
GMAW (MIG) |
SMAW (Stick) |
TIG |
FCAW |
Full Name |
Gas Metal Arc Welding |
Shielded Metal Arc Welding |
Tungsten Inert Gas Welding |
Flux-Cored Arc Welding |
Shielding Method |
Uses a shielding gas (typically Argon, CO₂, or a mixture) |
Flux coating on the electrode provides shielding |
It uses an external shielding gas (usually Argon) |
Flux within the electrode generates shielding gas |
Electrode Type |
Continuous wire electrode |
Consumable stick electrode |
Non-consumable tungsten electrode |
Continuous, flux-cored wire electrode |
Ease of Use |
Relatively easy to learn |
Easy to moderate; the skill required for stick control |
Requires high skill level |
Moderate; easier than TIG but more complex than GMAW |
Portability |
Moderate; requires gas cylinder |
Highly portable; minimal equipment needed |
Low gas cylinder and precise setup needed |
Moderate; can be portable but often requires shielding |
Weld Quality |
Produces high-quality, clean welds with minimal spatter |
Moderate quality; slag must be chipped off |
High-quality, precise welds with no spatter |
Produces high-quality welds but may have moderate spatter |
Common Applications |
Automotive, construction, manufacturing |
Construction, repair, maintenance |
Aerospace, automotive, pipe welding |
Construction, shipbuilding, heavy equipment fabrication |
Speed |
High welding speed |
Slower than GMAW and FCAW |
Slowest among the four but highly precise |
Fast, especially in outdoor conditions |
Material Compatibility |
Suitable for carbon steel, stainless steel, aluminum |
Works well on ferrous metals, some non-ferrous metals |
Excellent for thin metals, stainless steel, aluminum |
Primarily used for thick materials and structural steel |
Outdoor Suitability |
It is not ideal; shielding gas is affected by wind |
Excellent for outdoor use |
Poor shielding gas is easily disturbed by wind |
Good for outdoor use due to self-shielding flux |
Heat Input Control |
Moderate heat can be controlled by wire speed |
Lower control over heat input |
High control over heat input, suitable for thin metals |
Moderate; better control than SMAW, less precise than TIG |
Cost of Equipment |
Moderate; initial cost includes welder and gas cylinders |
Low; minimal equipment required |
High; precise equipment and gas cylinder needed |
Moderate to high, depending on the type of FCAW machine |
Post-Weld Cleanup |
Minimal; little to no spatter or slag |
High slag removal is required |
Minimal; no spatter or slag |
Moderate; may require slag removal |
Ideal User |
Beginner to intermediate; good for production welding |
Beginner: good for field repairs and outdoor work |
Advanced; requires precise control and patience |
Intermediate; good for high deposition in structural work |
Strengths |
Fast, efficient, versatile; good for high-production welding |
Portable, inexpensive, and good for outdoor conditions |
High-quality, precise welds with a good aesthetic finish |
Fast, handles thick materials, suited for outdoor welding |
Limitations |
Limited by shielding gas used in windy/outdoor settings |
Slag cleanup required, lower speed |
Requires high skill, slower speed, high setup cost |
It can produce fumes and requires ventilation indoors. |
GMAW in High-Volume Production Settings
Mass Production Suitability
Gas Metal Arc Welding (GMAW) proves highly suitable for mass production because of its efficiency and speed. Industries such as automotive and construction benefit from its ability to produce high-quality welds rapidly.
The continuous wire feed system allows uninterrupted welding, essential in large-scale manufacturing. This process reduces the time needed to complete projects, making it an ideal choice for companies aiming to meet tight deadlines.
GMAW's automation capabilities further enhance its suitability for mass production, as they streamline operations and reduce labor costs.
Different Materials Adaptability
GMAW is remarkably adaptable when working with various materials. It welds metals like steel, aluminum, and stainless steel, which are commonly used in manufacturing. This versatility makes GMAW a preferred method in industries that require joining different metals.
The process's handling of thin and thick materials meets diverse production needs. By adjusting parameters such as voltage and wire feed speed, operators achieve optimal results across different materials, enhancing the process's flexibility in high-volume settings.
Operations Scalability
The scalability of operations with GMAW makes it an attractive option for businesses looking to expand production. Its ease of automation allows companies to increase output without compromising quality.
As demand grows, manufacturers integrate robotic systems to handle repetitive tasks, maintaining consistent weld quality. This scalability supports businesses in adapting to market changes and meeting increased production demands.
GMAW's efficiency and adaptability ensure that operations scale smoothly, providing a reliable solution for high-volume production environments.
GMAW Long-Term Cost Savings
Reduced Maintenance Costs
GMAW offers significant long-term cost savings by reducing maintenance expenses. The equipment used in this welding process requires minimal upkeep because of its robust design and efficient operation. Unlike other welding methods,
GMAW produces cleaner welds with less spatter and slag, which means less wear and tear on the machinery. Reducing debris not only extends the equipment's lifespan but also decreases the frequency of maintenance checks.
Industries allocate resources more effectively, focusing on production rather than repairs by minimizing maintenance needs.
Equipment Longevity
The longevity of GMAW equipment contributes to its cost-effectiveness. The machines used in this process are built to withstand high-volume production demands. Their durability ensures that they remain operational for extended periods, reducing the need for frequent replacements.
The continuous wire feed system and shielding gas protection further enhance the equipment's lifespan by preventing overheating and damage.
As a result, businesses benefit from a reliable welding solution that supports long-term production goals without incurring excessive costs.
Lower Total Cost of Ownership
GMAW's efficiency and reliability lead to a lower total cost of ownership. The process's ability to produce high-quality welds with minimal rework reduces material waste and labor expenses. Its automation capabilities streamline operations, allowing companies to scale production without significant increases in overhead costs.
GMAW's versatility enables it to adapt to various materials and applications, providing a comprehensive solution for diverse manufacturing needs.
By investing in GMAW, businesses achieve substantial savings over time, making it a prudent choice for those seeking to optimize their production processes.
Environmental and Safety Advantages
Gas Metal Arc Welding (GMAW) offers significant environmental and safety benefits, making it a preferred choice in industrial settings.
These advantages contribute to a safer workplace and align with environmental regulations.
Reduced Emissions
GMAW significantly reduces emissions compared to other welding methods. The process produces fewer fumes and toxic metals, which minimizes air pollution—this reduction in emissions results from the cleaner welds and minimal production inherent in GMAW.
By substituting GMAW for traditional methods like Shielded Metal Arc Welding (SMAW), industries experience dramatic decreases in harmful emissions. This shift supports cleaner air quality and promotes healthier environments for workers and surrounding communities.
Improved Workplace Safety
Workers' safety remains a top priority in any industrial setting. GMAW enhances workplace safety by producing less smoke and fumes during welding. This reduction in airborne contaminants lowers the risk of respiratory issues among workers.
GMAW's ease of automation reduces the need for manual intervention, decreasing the likelihood of accidents.
The process's ability to produce high-quality welds with minimal spatter further contributes to a safer working environment, reducing the risk of burns and injuries.
Compliance with Environmental Regulations
Industries must adhere to strict environmental regulations to ensure sustainable operations. GMAW supports compliance by offering a welding solution with lower emission rates. The process aligns with environmental standards, helping companies meet regulatory requirements.
Businesses show their commitment to environmental responsibility and sustainability by choosing GMAW. This compliance avoids potential fines and penalties and enhances the company's reputation as an environmentally conscious entity.
In Sum
Gas Metal Arc Welding (GMAW) is a cost-effective solution for high-volume production. Its efficiency and material savings make it a preferred choice in various industries. The process achieves high-speed welds, which save time and ensure defect-free results.
GMAW's ability to produce cleaner, higher-quality welds with minimal emissions further enhances its appeal. This welding method also offers consistent quality, reducing the need for rework and boosting productivity. With its high deposition rates and speed advantages,
GMAW efficiently meets the demands of large-scale projects, making it an invaluable asset in manufacturing.
GMAW's ease of automation and learning further supports its widespread adoption. GMAW ensures industries maintain high standards while meeting production targets efficiently By providing high-quality welds with minimal spatter.
Industries seeking to enhance productivity and reduce costs should consider GMAW for future projects. Its efficiency, versatility, and ease of use make it valuable in any manufacturing setting. By choosing GMAW, businesses achieve significant cost savings and maintain consistent quality.
The process's adaptability to different materials and scalability of operations further supports its suitability for high-volume production. Embracing GMAW optimizes production processes and aligns with environmental and safety standards, ensuring sustainable and responsible manufacturing practices.