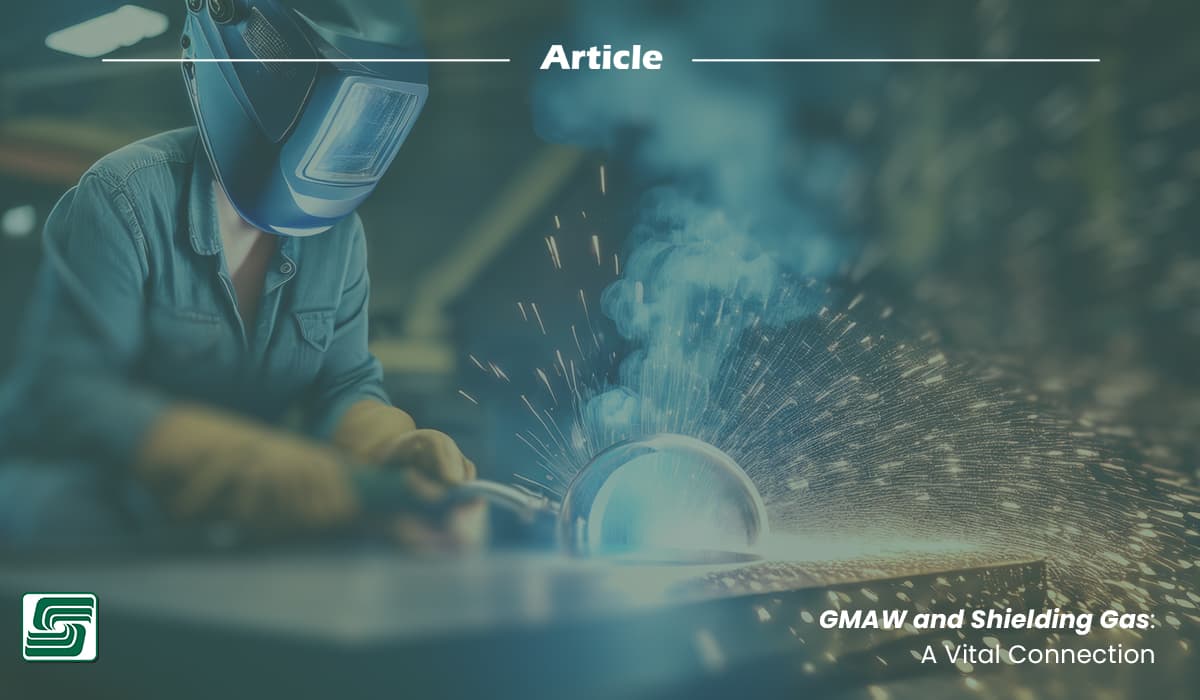
GMAW, or Gas Metal Arc Welding, is crucial in modern welding techniques. The process involves shielding gas to protect the weld pool from atmospheric contamination. Shielding gas selection holds significant importance. The right choice enhances weld quality and stability. Different gases impact the welding process in unique ways. Understanding the role of shielding gas ensures optimal results in various applications.
Basics of GMAW
GMAW is a popular welding process that uses an electric arc to join metals. The process involves a continuous wire feed as an electrode, and shielding gas protects the weld from contamination. GMAW offers efficiency and versatility in various applications.
Components of GMAW
GMAW comprises several key components. The power source provides the electrical energy. The wire feed system supplies the electrode continuously. The welding gun directs the wire and gas to the weld area. Shielding gas prevents atmospheric contamination. These components work together for effective welding.
Feature |
Advantage |
Benefits |
Continuous Electrode Feed |
Consistent arc and reduced downtime |
Faster welding speed, improved productivity |
Shielding Gas |
Protects weld from atmospheric contaminants |
High-quality welds, reduced porosity, and spatter |
Versatile Materials |
Welds various metals and alloys |
Wide-range of applications |
All-Position Welding |
Capable of welding in different positions |
Flexibility and adaptability |
Higher Disposition Rates |
Faster material transfer |
Increased productivity |
Minimal Post-Weld Cleaning |
No slag removal |
Reduced labor costs and time |
Adjustable Parameters |
Control over weld characteristics |
Customization for specific applications |
Automated Options |
Reduced operator skill requirement |
Increased efficiency and consistency |
Advantages of GMAW
GMAW presents several advantages:
- The process allows for high welding speeds.
- Operators achieve clean and precise welds.
- GMAW requires minimal post-weld cleaning.
- The method suits both thin and thick materials.
- GMAW offers flexibility across different industries.
Applications of GMAW
GMAW finds applications in various sectors, adapting to different environments and materials, giving industries several benefits.
Industries using GMAW
Many industries use GMAW.
- The automotive industry relies on it for vehicle assembly.
- Construction projects use GMAW for structural welding.
- Shipbuilding employs GMAW for hull fabrication.
- The aerospace sector benefits from GMAW's precision.
- Manufacturing plants incorporate GMAW into production lines.
Common materials welded with GMAW
GMAW handles a wide range of materials.
- Steel is commonly welded using GMAW
- Aluminum joins effectively with GMAW techniques
- Stainless steel benefits from GMAW's precision
- Copper and its alloys are suitable for GMAW
GMAW accommodates various material thicknesses.
Purpose of Shielding Gas
Shielding gas is critical in GMAW, acting as a protective barrier for the molten weld pool.
- Atmospheric gases like oxygen and nitrogen contaminate the weld, leading to defects and weakening the weld.
- Shielding gas prevents these issues by creating a stable environment.
The quality of the weld directly depends on the shielding gas. Proper shielding gas selection enhances arc stability, which ensures consistent heat and penetration. Consistent heat results in uniform welds with fewer defects, and high-quality welds improve the structure's overall strength.
How Shielding Gas Works
Shielding gas interacts with the welding arc in GMAW. The gas flows through the welding gun nozzle, enveloping the arc and weld pool. This interaction stabilizes the arc and controls the heat input, which allows precise manipulation of the weld.
The impact of shielding gas extends to weld penetration and bead shape. Different gases influence the depth of penetration. Deeper penetration creates stronger joints in thicker materials. The shape of the weld bead also varies with gas type. A smooth and even bead enhances the appearance and integrity of the weld.
Types of Shielding Gases
Shielding Gas |
Type |
Physical Properties |
Chemical Properties |
Influence on Metallurgical Properties |
Typical Applications |
Argon |
Inert |
High density, moderate thermal conductivity |
Minimal reactivity |
Smooth, uniform welds |
General-purpose welding, aluminum |
Helium |
Inert |
Low density, high thermal conductivity |
Minimal reactivity |
Deep penetration, high heat input |
Thick materials, stainless steel |
Carbon Dioxide |
Active |
Moderate density, moderate thermal conductivity |
Reactive |
Increased penetration, higher spatter |
Thicker materials, mild steel |
Oxygen (as an additive) |
Active |
Moderate density, moderate thermal conductivity |
Reactive |
Enhanced fluidity, increased arc stability |
Mild steel, stainless steel |
Considerations
Gas Availability
Gas availability impacts the choice of shielding gas in welding operations. Some gases are more readily available in certain regions.
- Argon is widely accessible and often preferred for its stability.
- Helium might be less available and more expensive.
Considering local availability helps in making cost-effective decisions.
Economic Impact on Welding Operations
Economic impact plays a vital role in selecting shielding gases. Different gases vary in cost, affecting overall welding expenses.
- Carbon dioxide offers a cost-effective option for many applications.
- Argon and helium might incur higher costs but provide superior weld quality.
Balancing cost with performance ensures efficient and economical welding operations.
Impact of Shielding Gas on GMAW Performance
Shielding gas plays a crucial role in performing GMAW. The choice of shielding gas directly influences weld quality and welding efficiency. Understanding these impacts helps in achieving optimal results.
Weld Quality
Porosity prevention
Porosity in welds often results from atmospheric contamination.
- Shielding gas acts as a protective barrier during GMAW.
- The gas prevents oxygen and nitrogen from entering the weld pool.
- Proper gas selection reduces the risk of porosity.
- A clean and defect-free weld enhances structural integrity.
Surface finish
The surface finish of a weld significantly affects its appearance and functionality.
- Shielding gas contributes to a smooth and even weld bead.
- Argon, for instance, minimizes spatter during GMAW.
- A high-quality surface finish requires careful gas selection.
- The right gas ensures an aesthetically pleasing and durable weld.
Welding Efficiency
Speed of welding
Welding speed is a critical factor in production efficiency.
- Shielding gas influences the rate at which welding occurs—active gases like carbon dioxide increase welding speed in GMAW.
- Faster welding reduces production time and costs.
- Selecting the correct gas enhances overall productivity.
Energy consumption
Energy consumption impacts the cost-effectiveness of welding operations.
- Shielding gas affects the energy required for GMAW.
- Inert gases like argon provide stable arc conditions, reducing welding energy waste.
- Efficient energy use leads to lower operational expenses.
Common Challenges and Solutions
Gas Flow Issues
Inadequate gas flow presents a common challenge in GMAW. Several factors contribute to this problem.
- Blockages in the gas line restrict the flow of shielding gas.
- Damaged or worn-out components, such as hoses or nozzles, impede gas flow.
- Incorrect settings on the welding equipment lead to insufficient gas delivery.
Solutions to gas flow problems involve several steps.
- Regular maintenance of the welding equipment ensures optimal performance.
- Inspecting and replacing damaged components prevents blockages.
- Adjusting the equipment settings to match the specific requirements of the welding process improves gas flow.
- Ensuring proper storage and handling of gas cylinders maintains consistent pressure and flow.
Gas Contamination
Gas contamination poses another challenge in GMAW.
- Various sources contribute to contamination.
- Moisture in the gas lines introduces impurities into the weld pool.
- The gas delivery system leaks allow atmospheric gases to mix with the shielding gas.
- Dirty or improperly stored gas cylinders also introduce contaminants.
Preventive measures help reduce gas contamination.
- Regularly checking and maintaining gas lines prevents moisture buildup.
- Ensuring tight connections in the gas delivery system eliminates leaks.
- Storing gas cylinders in a clean and dry environment reduces the risk of contamination.
- Using high-quality gas from reputable suppliers ensures purity and consistency.
In Sum
Shielding gas is vital in Gas Metal Arc Welding (GMAW). The gas protects the weld pool from atmospheric contamination. Proper shielding gas selection enhances weld quality and stability. Different gases influence the welding process uniquely. Understanding these factors ensures optimal results in various applications. Welders must consider the material type and welding position when choosing a shielding gas. Cost considerations also impact the decision-making process. Selecting the right shielding gas produces high-quality, efficient, and economical welding operations.