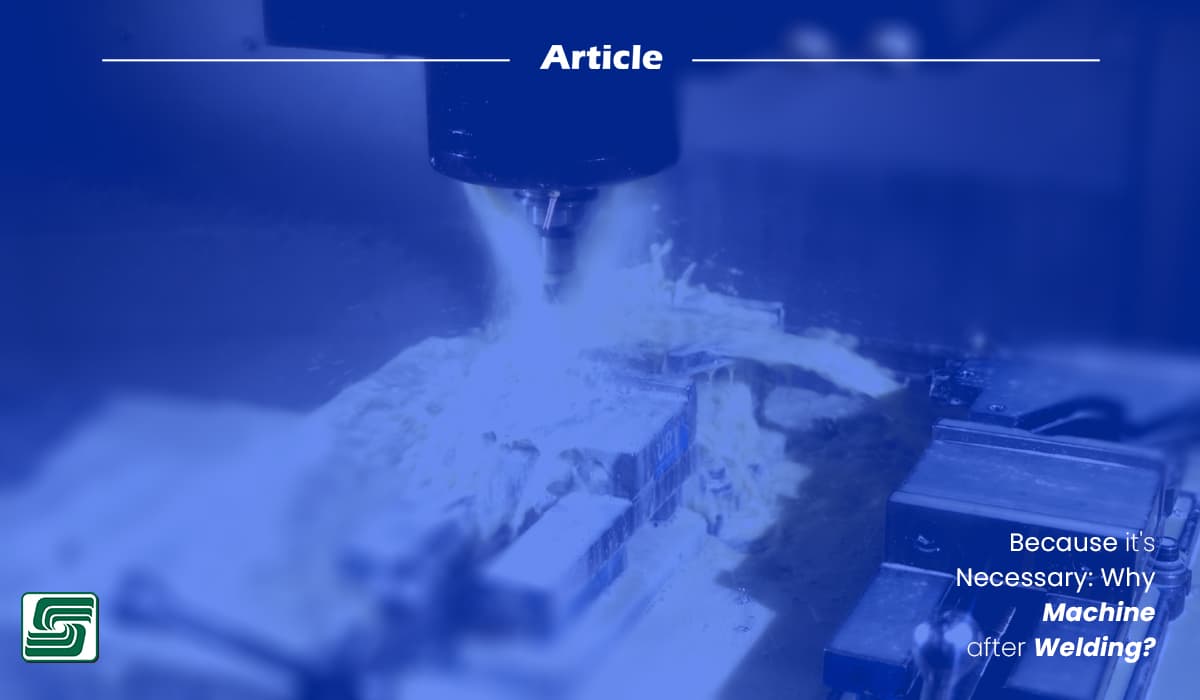
CNC machining revolutionizes manufacturing by automating precision tasks. Fluid cutting is crucial in this process, enhancing efficiency and accuracy.
CNC machining:
- Cools Tools
- Reduces Friction
- Improves Surface Finishes
Fluid cutting is indispensable in modern CNC machining because of its impact on productivity and quality.
Understanding CNC Machining
CNC stands for Computer Numerical Control Machining. It refers to a manufacturing process in which pre-programmed computer software dictates the movement of factory tools and machinery. This process allows for the production of complex parts with high precision.
The principal components of a CNC machine include:
- Computer
- Machine Control Unit
- Machine tool
The computer runs the software that controls the machine, while the machine control unit interprets the instructions and directs the machine tool to perform specific tasks.
How CNC Machines Work
CNC machines follow coded instructions, often written in G-code, that guide the machine's movements and operations.
The process begins with a digital design created using CAD (Computer-Aided Design) software.
- The design is converted into instructions that the CNC machine understands.
- The machine executes these instructions, moving the cutting tool along specified paths to shape the material into the desired form.
- The automation ensures consistent quality and reduces the likelihood of human error.
Evolution of CNC Machining
The origins of CNC machining trace back to the 1940s and 1950s when the first numerical control machines were developed. These early machines used punched tape to control their operations.
Over time, technological advancements led to the development of more sophisticated systems. Introducing computers in the 1960s marked a significant turning point, allowing for greater precision and flexibility in manufacturing processes.
Technological Advancements
Technological advancements have continually shaped the evolution of CNC machining. Integrating computer-aided design and manufacturing (CAD/CAM) systems has streamlined production.
Modern CNC machines now feature advanced capabilities, such as multi-axis machining, which allows intricate designs to be created.
Improvements in software and hardware have enhanced the speed and accuracy of CNC machines, making them indispensable in various industries.
What is Fluid Cutting?
Fluid cutting plays a pivotal role in CNC machining. It involves using cutting fluids to enhance the machining process. These fluids provide lubrication and cooling, essential for maintaining the quality and precision of the workpiece.
The Purpose of Cutting Fluid
Cutting fluids serve multiple purposes in CNC machining. They provide lubrication to reduce friction between the cutting tool and the workpiece. This reduction in friction minimizes wear on the tool, extending its life.
Cutting fluids provide cooling, which helps dissipate the heat generated during the cutting process. This cooling effect prevents thermal damage to the tool and the workpiece, ensuring a high-quality finish.
Types of Fluids Used
Various types of cutting fluids are used in CNC machining. These include:
- Water-based Fluids: These fluids provide excellent cooling properties. They are often mixed with additives to enhance their lubricating capabilities.
- Oil-based Fluids: Known for their superior lubrication, oil-based fluids provide a protective layer between the tool and the workpiece.
- Synthetic Fluids: These fluids provide a balance between cooling and lubrication. They are formulated to meet specific machining requirements.
Each fluid type provides unique benefits, making selecting the fluid for the specific machining operation essential.
Role in the Cutting Process
In the cutting process, fluids provide several critical functions.
- They reduce the temperature of the cutting zone, preventing overheating. This temperature control maintains the integrity of the workpiece material.
- Cutting fluids provide a smooth surface finish by minimizing tool wear and tear.
- They also provide chip removal, ensuring that debris does not interfere with the cutting process.
By providing these benefits, cutting fluids enhances the overall efficiency and effectiveness of CNC machining.
Fluid Cutting Benefits
Fluid cutting provides many advantages in CNC machining. These benefits contribute to improved productivity and quality in the manufacturing processes.
Enhanced Precision
Cutting fluids enhances precision in machining operations by reducing friction and heat. They also provide a stable cutting environment, which allows for more accurate cuts and results in parts with tight tolerances.
Using cutting fluids provides consistent results, which is crucial for high-precision applications.
Improved Tool Life
Using cutting fluids significantly improves tool life. By providing lubrication, they reduce the wear on cutting tools. This reduction in wear extends the lifespan of the tools, reducing the need for frequent replacements.
Cutting fluids provide cooling, which prevents thermal damage to the tools. This preservation of tool integrity provides cost savings and ensures uninterrupted production.
Machining Fluid Dynamics
Cutting fluids play a pivotal role in machining by influencing the cutting process in several ways. They reduce friction between the cutting tool and the workpiece, which minimizes wear and tear on the tool. This reduction in friction also leads to smoother cuts and improved surface finishes.
Cutting fluids in metal applications enhances the precision of the machining process by maintaining a stable cutting environment. The lubrication provided by these fluids ensures that the cutting tool operates efficiently, resulting in high-quality outputs.
Thermal Management
Thermal management is one of the critical functions of cutting fluids. During machining, the cutting process generates significant heat, damaging both the tool and the workpiece. Cutting fluids dissipate this heat, preventing thermal deformation and ensuring the integrity of the workpiece.
By maintaining optimal temperatures, these fluids extend the life of the cutting tools and improve the machining process's overall efficiency. Effective thermal management also produces parts with tight tolerances, which is essential in high-precision metalworking.
Material Compatibility
The compatibility of cutting fluids with different materials is crucial in machining. Metalworking fluids are specifically formulated to work with metals, providing lubrication and cooling to handle the unique challenges of metal materials.
In contrast, non-metal materials may require different fluids to achieve optimal results. The fluid choice depends on the material's properties, such as hardness and thermal conductivity.
Understanding the differences between metals and non-metals helps machinists select the fluids for each application, ensuring efficient and effective machining.
Fluid Selection Criteria
Selecting the right cutting fluid involves considering several factors. The type of material being machined, the machining operation, and the desired surface finish all influence the choice of fluid.
- Oil-based fluids offer superior lubrication, making them ideal for operations requiring high precision levels.
- Water-based fluids provide excellent cooling properties, which are beneficial in high-speed machining.
- Synthetic fluids balance lubrication and cooling, making them versatile for various applications.
Machinists must evaluate these criteria to choose the most suitable fluid, optimizing the performance and longevity of their tools.
Fluid Cutting Techniques
Fluid cutting techniques are vital in CNC machining, enhancing the process's efficiency and precision. These techniques use various fluids to achieve optimal results in metalworking operations.
Technique |
Fluid Type |
Application |
Advantages |
Disadvantages |
Flood Cooling |
Soluble Oil |
General Millworking |
Effective heat dissipation, consistent quality, excellent lubrication |
Higher fluid consumption, potential for environmental impact |
Mist Cooling |
Semi-Synthetic Fluid |
Operations where excessive fluid is not desirable |
Reduced fluid consumption, minimal environmental impact |
May require careful fluid selection for balance |
Cryogenic Cooling |
Liquid Nitrogen |
High-precision metalworking |
Reduces tool wear, improves surface quality, minimizes thermal distortion |
Requires specialized equipment and handling |
High-Pressure Jet Cutting |
Straight Oil |
Cutting complex shapes and hard materials |
Precise cutting, clean cuts, smooth finishes |
May require higher pressure and specialized equipment |
Whether common or advanced, fluid cutting techniques are vital in optimizing CNC machining operations, selecting appropriate fluids, such as soluble oil and semi-synthetic fluids, ensures efficient metalworking and high-quality outputs.
Fluid Cutting Challenges
Fluid cutting in CNC machining presents several challenges that machinists must address to maintain efficiency and quality. These challenges primarily revolve around environmental concerns and technical limitations.
Environmental Concerns
Disposal and Recycling
Disposing of metalworking fluids poses significant environmental challenges. These fluids, including straight oils and synthetic fluids, often contain additives that harm the environment if not properly managed. Machinists must implement effective disposal and recycling strategies to mitigate these impacts. Recycling metalworking fluids reduces waste and conserves resources, aligning with sustainable practices. Proper disposal ensures compliance with environmental regulations and minimizes potential harm to ecosystems.
Regulatory Compliance
Regulatory compliance is crucial in managing metalworking fluids. Various regulations govern these fluids' use, disposal, and recycling to protect the environment and human health. Machinists must stay informed about these regulations to ensure their operations remain compliant. Non-compliance causes legal penalties and damage to a company's reputation. By adhering to regulatory standards, machinists contribute to environmental protection and promote sustainable metalworking practices.
Technical Limitations
Equipment Wear and Tear
Fluid cutting leads to equipment wear and tear. The continuous use of cutting fluids, especially those containing abrasive additives, degrades machine components. This wear affects the precision and efficiency of machining operations. Regular maintenance and monitoring of equipment mitigate these effects. Machinists should use fluids with improved lubrication properties to extend the life of their tools and machinery.
Fluid Contamination
Contamination of metalworking fluids is a common challenge in machining.
- Contaminants such as metal particles, bacteria, and tramp oils compromise the performance of cutting fluids.
- Contaminated fluids reduce the effectiveness of lubrication and cooling, leading to poor machining results.
- Implementing filtration systems and regular fluid monitoring helps control contamination levels.
Choosing the correct cutting fluid and maintaining its purity ensures optimal performance and prolongs the life of both the fluid and the equipment.
Innovations in Fluid Cutting
Fluid cutting in CNC machining has seen significant advancements, enhancing efficiency and sustainability. These innovations focus on improving performance while addressing environmental concerns.
Eco-Friendly Fluids
Recent developments in fluid cutting have introduced eco-friendly fluids that prioritize sustainability.
- Manufacturers now produce cutting fluids with biodegradable components, reducing environmental impact.
- These fluids often replace traditional oils with vegetable-based alternatives, offering effective lubrication and cooling without harmful residues.
By adopting eco-friendly fluids, the metalworking industry minimizes its ecological footprint while maintaining high performance in machining operations.
Smart Fluid Systems
Smart fluid systems represent another breakthrough in fluid-cutting technology.
- These systems use sensors and data analytics to optimize fluid application during machining.
- By monitoring parameters such as temperature and density, smart systems adjust fluid flow in real-time, ensuring optimal performance.
- This precision reduces fluid waste and enhances the efficiency of cutting processes.
Smart fluid systems also extend the life of tools by providing consistent lubrication and cooling, ultimately improving the quality of machined parts.
Future Trends
The future of fluid cutting lies in automation and AI integration. Automated systems will manage fluid applications with minimal human intervention, increasing consistency and reducing errors.
AI algorithms will analyze machining data to predict fluid needs and adjust parameters for optimal performance.
This integration:
- Streamline Operations
- Enhance Precision
- Reduce Costs
As automation and AI become more prevalent, fluid cutting will continue to evolve, offering even greater efficiency in metalworking.
Sustainable Practices
Sustainable practices will shape the future of fluid cutting by:
- Reducing water and oil consumption
- Promoting recycling
- Developing more sustainable synthetic fluids
These efforts aim to minimize waste and conserve resources while maintaining high performance. The metalworking sector balances productivity and environmental responsibility by embracing sustainable practices. This commitment to sustainability will drive innovation and ensure the long-term viability of fluid cutting in CNC machining.
Machinist's Practical Considerations
Machinists must deliberate several factors when selecting and maintaining cutting fluids. These considerations ensure optimal performance and safety in CNC machining operations.
Selecting the Right Fluid
Choosing the appropriate cutting fluid involves evaluating various factors influencing machining efficiency and quality.
Factors to Consider
Machinists should assess:
- The machined material
- The cutting operation type
- The desired surface finish
Different materials require specific fluids to achieve the best results. For instance,
- Oil-based fluids offer superior lubrication, making them suitable for high-precision operations.
- Water-based fluids excel in cooling, ideal for high-speed machining.
- Synthetic fluids balance lubrication and cooling, making them versatile for various applications.
Understanding these factors helps machinists select the most effective fluid for their needs.
Cost vs. Performance
Balancing cost and performance is crucial when selecting cutting fluids. High-performance fluids may come at a higher price but often extend tool life and improve machining quality. Machinists should weigh the initial cost against the long-term benefits. Investing in quality fluids reduces tool wear, minimizes downtime, and enhances overall productivity. By considering cost and performance, machinists make informed decisions that optimize their operations.
Maintenance and Safety
Proper maintenance and adherence to safety protocols are essential for effective fluid cutting in CNC machining.
Regular Monitoring
Machinists must regularly monitor cutting fluids to maintain their effectiveness, which involves checking fluid levels, concentration, and contamination. Contaminants such as metal particles and tramp oils degrade fluid performance. Implementing filtration systems and routine testing helps control contamination levels. Regular monitoring ensures that fluids provide consistent lubrication and cooling, enhancing machining efficiency and tool longevity.
Safety Protocols
Adhering to safety protocols is vital when handling cutting fluids.
- Machinists should use PPE to prevent skin contact and inhalation of fumes.
- Proper ventilation in the workspace reduces exposure to harmful vapors.
- To prevent environmental harm, machinists must follow fluid storage and disposal guidelines.
By prioritizing safety, machinists protect themselves and maintain a safe working environment.
Skimmers and Their Importance
Skimmers play a crucial role in CNC machining by maintaining the quality and efficiency of cutting fluids. They remove unwanted substances from the fluid, ensuring optimal performance during machining operations.
Skimmers Functionality
Skimmers operate by extracting contaminants such as oil and debris from cutting fluids. This process helps maintain the fluid's purity, essential for effective lubrication and cooling. Skimmers remove these impurities and extend their usable life by preventing fluid degradation. This functionality enhances machining efficiency and reduces operational costs by minimizing fluid replacement frequency.
Skimmers Types
Several types of skimmers are available, each designed to address specific needs in machining environments:
Skimmer Type |
Method of Operation |
Applications |
Advantages |
Disadvantages |
Belt Skimmer |
Continuous belt collects oil |
General industrial applications |
Effective for removing floating oil, versatile |
May require more space for installation |
Disk Skimmer |
Rotating disk collects oil |
Applications with limited space |
Compact design, easy installation |
May not be as effective for large amounts of oil |
Tube Skimmer |
Flexible tube collects oil |
Tanks of various shapes and sizes |
Versatile, adaptable to different tank configurations |
May be less efficient for thicker oil |
Each type of skimmer offers unique advantages, so it is important to select one based on the specific requirements of the machining operation.
Machining Benefits
Using skimmers in CNC machining provides several benefits that enhance both productivity and environmental responsibility:
- Improved Fluid Quality: By removing contaminants, skimmers maintain the quality of cutting fluids, ensuring consistent lubrication and cooling, leading to better machining results and prolonged tool life.
- Cost Efficiency: Skimmers reduce the need for frequent fluid changes, resulting in cost savings. Extending the life of cutting fluids minimizes waste and lowers operational expenses.
- Environmental Impact: Skimmers contribute to sustainable practices by reducing fluid disposal and recycling needs. Maintaining clean fluids helps minimize environmental pollution and promotes responsible machining operations.
In Sum
Fluid cutting is a cornerstone in CNC machining, offering many advantages that enhance manufacturing. CNC machining is pivotal in:
- Cooling Tools
- Reducing Friction
- Improving Surface Finishes
These functions ensure CNC machines operate efficiently and produce high-quality parts. Fluid cutting also:
- Extends Tool Life
- Reducing Costs
- Increasing Productivity
Maintaining optimal temperatures and providing lubrication prevents thermal damage and wear on tools. This technology is indispensable for achieving precision and consistency in modern manufacturing.