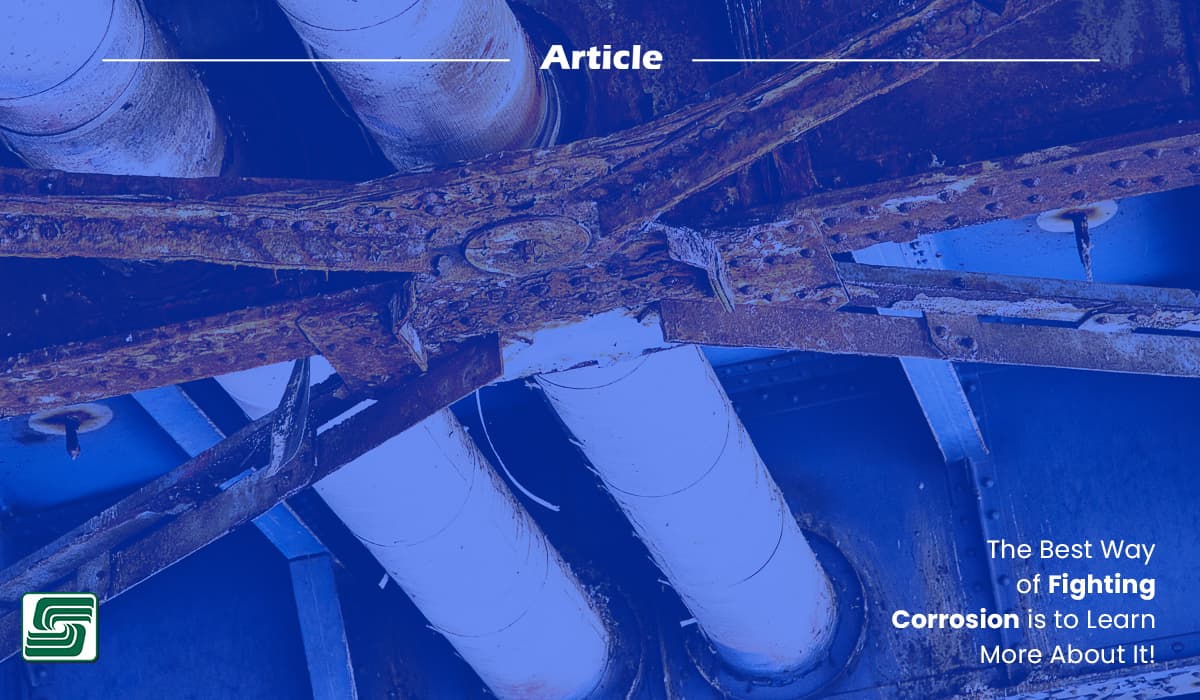
If something breaks, we fix it.
Whether the reason is safety or aesthetics, broken things tend to get fixed.
You slip on ice and break a leg. What do you do?
Obviously, the first thing you do is get yourself to see a doctor to fix your broken leg! The second would be to spread ice melt on the ice so nobody else gets hurt.
What if the ice keeps coming back? The best solution to your ice problem is to find where the water is coming from. If it's a leak, plug it. If it's runoff from rain or snowmelt, create a barrier so the water stays away.
To solve the icing problem, you used root cause analysis to identify the most basic reason for a problem. Eliminating or correcting this reason prevents the problem from recurring.
Corrosion is a problem for the metal industry. Some try solving the problem by cleaning up and painting over rusty areas. Others, however, go further. To fight corrosion, they need to understand the root cause of the problem and then fix it.
Understanding Corrosion
Corrosion, a common issue in the metal industry, causes rust and deterioration of metal components. When metals are exposed to certain environmental factors, such as moisture and salt air, they undergo a chemical reaction leading to rust formation.
This process ultimately weakens the metal, causing it to deteriorate over time. Understanding the causes and effects of corrosion is crucial in implementing effective preventative measures to protect metal surfaces from rust formation and degradation.
By understanding corrosion and its preventive measures, companies extend the lifespan of metal products and reduce the risk of costly repairs or replacements.
Rust Formation
Rust formation is a common concern for metal surfaces because of the impact of environmental factors such as moisture and salt air. These elements play a significant role in the deterioration of metal components, leading to rust formation and eventual degradation.
Impact of Moisture and Salt Air
- Moisture, whether in the form of rain, humidity, or condensation, accelerates the oxidation process on metal surfaces, leading to the formation of rust.
- Salt Air, prevalent in coastal regions, contains corrosive salts that expedite the corrosion process on metal surfaces, making them more susceptible to rust formation.
Corrosion Prevention Methods
- Using corrosion-resistant coatings is an effective method for preventing rust formation. These coatings act as a protective barrier against moisture and salt air, inhibiting their direct contact with the metal surface and reducing the risk of rust formation.
- Regularly applying these coatings significantly enhances metal protection and prolongs its lifespan by minimizing moisture and salt air exposure.
Moisture and Salt Air
Effects of Moisture on Rust Formation
- Moisture Exposure: When metal surfaces are exposed to moisture as rain, humidity, or dampness, the oxidation process speeds up, leading to the rapid formation of rust. The presence of moisture creates an environment conducive to corrosion, ultimately weakening the metal and causing deterioration.
- Increased Susceptibility: Metal components in humid or wet environments are susceptible to rust formation from prolonged exposure to moisture. Prolonged exposure is especially problematic in areas with high humidity or frequent rainfall.
What are Some Preventative Measures for Salt Air Corrosion?
Developing preventative measures is essential for protecting metal components from moisture's detrimental effects. Regular inspections and cleaning help identify and address areas where moisture accumulation may occur, reducing the risk of rust formation.
- Protective Coatings: In coastal regions where salt air is prevalent, corrosion-resistant coatings protect against corrosive salts. These coatings act as a shield, preventing direct contact between the metal surface and salt air, thus minimizing the risk of corrosion and rust formation.
- Routine Cleaning: Regularly cleaning metal surfaces exposed to salt air helps remove corrosive residues and prevent the buildup of salts that contribute to corrosion. This proactive measure is crucial for maintaining the integrity and longevity of metal components in coastal environments.
By understanding the impact of moisture on rust formation and implementing preventative measures for salt air corrosion, individuals effectively safeguard metal surfaces from deterioration and extend their lifespan.
Corrosion by Acids and Chemicals
Impact of Acids on Metal Corrosion
When metal comes into contact with acids, it undergoes a rapid deterioration from corrosion. Acids break down the molecular structure of metals, leading to their degradation and weakening over time.
The impact of acids on metal corrosion is severe, causing damage and compromising the integrity of the metal components.
Chemical Corrosion Prevention
Preventing damage from chemical erosion requires the use of corrosion-resistant materials. These materials are specifically designed to withstand exposure to various types of chemicals, minimizing the risk of corrosion and degradation.
Using such materials in constructing and maintaining metal structures effectively protects against chemical erosion and prolongs the lifespan of metal components.
Unusual Sources of Corrosion
Stress Corrosion Cracking
Stress corrosion cracking is a phenomenon leading to unexpected metal failure.
This type of corrosion occurs under a combination of tensile stress and a specific corrosive environment, causing cracks to form in the metal. It is particularly insidious as the cracks rapidly reproduce with little warning, leading to sudden and catastrophic failure of the affected metal components.
Microbial and Fretting Corrosion
Understanding microbial and fretting corrosion is crucial to comprehensive corrosion prevention.
Microbial corrosion, or bio-corrosion, occurs when microorganisms such as bacteria or fungi interact with metal surfaces, leading to decay and deterioration.
Fretting corrosion, also called wear oxidation or friction oxidation, results from repetitive wear or friction between metal surfaces in contact with each other, often leading to localized damage and accelerated degradation.
Preventive Measures
Implementing regular inspections and maintenance protocols helps identify early signs of:
- Stress Corrosion Cracking
- Microbial Corrosion
- Fretting Corrosion
By addressing these issues proactively, individuals mitigate the risk of unexpected metal failure and prevent extensive damage caused by these unusual sources of corrosion.
Proactive Steps for Prevention
Importance of Preventative Maintenance
Regular maintenance is crucial in preventing corrosion and extending the lifespan of metal products.
By implementing a proactive maintenance schedule, individuals identify and address potential corrosion risks before they escalate, minimizing the impact of environmental factors and other corrosive elements on metal surfaces.
Preventative Maintenance Practices
Regular inspections, cleaning, and upkeep of metal components are essential for detecting early signs of corrosion. Early detection includes:
- Identifying areas of moisture accumulation.
- Checking for signs of rust formation.
- Ensuring that protective coatings remain intact.
Addressing structural vulnerabilities or wear and tear through timely repairs significantly prevents corrosion-related damage.
Corrosion Risk Assessment
Conducting periodic assessments to evaluate the susceptibility of metal components to corrosion is an integral part of preventative maintenance.
By identifying factors such as exposure to moisture, salt air, acids, or chemicals, individuals develop targeted strategies for mitigating these risks and preserving the integrity of metal surfaces.
Using Corrosion-Resistant Coatings
Applying corrosion-resistant coatings serves as an effective proactive measure for preventing metal corrosion. These specialized coatings act as a protective barrier against environmental elements and corrosive substances that could lead to rust formation and degradation.
By creating a barrier between the metal surface and external factors, such as moisture, salt air, acids, and chemicals, these coatings help minimize direct contact with corrosive agents.
Benefits of Corrosion-Resistant Coatings
The application of these coatings not only provides immediate protection but also offers long-term benefits by extending the lifespan of metal products. These coatings contribute to cost savings by reducing the need for frequent repairs or premature replacements from corrosion-related damage.
Tailored Solutions
A corrosion-resistant coating is critical and should be chosen based on specific usage requirements and environmental conditions.
Consider factors such as exposure levels to moisture or chemicals when choosing from a range of coating options to ensure optimal protection against corrosion.
Regular preventative maintenance practices and corrosion-resistant coatings help safeguard metal products from corrosion-related deterioration while prolonging their lifespan.
In Sum
Taking proactive measures is crucial when preserving metal products and minimizing the need for costly repairs or replacements. Corrosion-resistant coatings protect against environmental elements, reducing the risk of rust formation and degradation. Regular preventative maintenance is vital in identifying and addressing potential corrosion risks before they escalate.
By integrating these strategies, individuals effectively extend the lifespan of metal products while safeguarding them from the detrimental effects of corrosion. This proactive approach ensures the longevity of metal components and contributes to cost savings by minimizing the impact of corrosion-related damage.
Incorporating corrosion-resistant coatings and preventative maintenance practices is essential for upholding the integrity and durability of metal products in various environmental conditions.