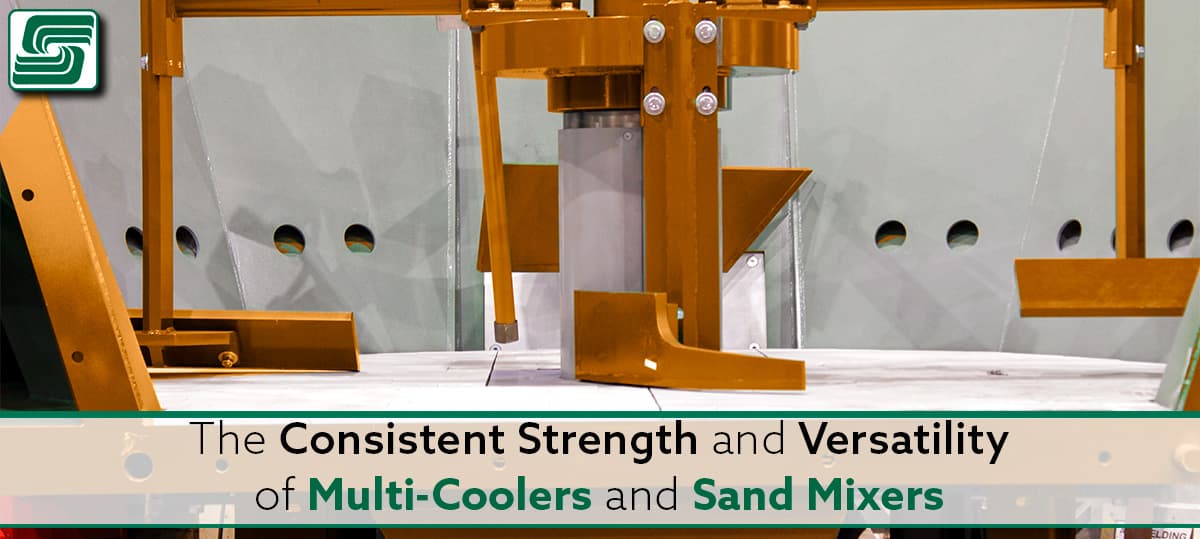
Living in central Wisconsin often allows me to travel to the state's western border. Closing in on the Minnesota border, especially in areas north of La Crosse, you'll see abundant sand mines.
Wisconsin has extensively mined sand for over 100 years, used extensively to manufacture glass, foundry molds, and golf trap systems, besides its traditional purpose of oil extraction. Frac sand is a fluid suspension of grains of quartz sand of a specific size and shape that is used for fracking oil and gas wells. Mining companies have recently made the process more efficient with the increased demand for frac sand. In addition, creating new frac fractures open existing fractures up from the high-pressure fluid flowing through them. Depositing the sand in the fractures keeps them open after removing the fluid. Quartz sand must be nearly pure, well-rounded, extremely hard, and of uniform size before being sent to the factory to be washed, sorted, and dried.
Companies mine frac sand from sandstone formations in western and central Wisconsin. The same formations are less well-exposed and generally more fine-grained in the eastern and southern parts of the state. Because sand from younger glacial deposits, as well as most beach and riverbank sand, is too impure and too angular to be used as frac sand, it is being mined from sandstone formations in the western and central parts of the state.
Foundries use the same sand; unlike sand mines, it needs a few more steps before use. This step is where multi-coolers and sand mixers enter our conversation.
Multi-Coolers and Sand Mixers
Multi-coolers, also called evaporative coolers, are special devices that reduce the temperature of liquids and gases by transferring heat from one medium to another. Industries using multi-coolers include:
- Mining
- Chemical
- Wastewater treatment
- Food and beverage
- Olive oil production
A multi-cooler is an assembly of devices used together to transfer heat energy from one medium (liquid or gas) to another. Each device has its own function and achieves optimal cooling performance when working together as a system.
When considering the design of a multi-cooler system, focus on each subcomponent's properties and their application during manufacturing while maintaining their performance characteristics.
Multi-Cooler System Designs
Various processes use cooling systems to remove heat from a stream, either to maintain temperatures at desired levels or to produce cooling water for other applications. The cooling tower is the most recognizable cooling system used in power plants, chemical and paper mills, and other industries requiring large volumes of cooling water.
A cooling tower is a tall, open structure containing an arrangement of sprays that drizzle warm process fluid inside the tower's surface. The warm fluid evaporates, forming a mist that rises to the tower's top. Cooling ponds are shallow ponds where the warm fluid circulates through submerged pipes.
Evaporation of water in the pond increases the temperature of the warm fluid while pumping the cooled water out and reusing it. They can also use process air as a cooling medium, mainly in the paper and chemical industries, not needing large quantities of cooling water. The aluminum smelting industry uses air-cooled condensers.
Fabrication Materials
Different materials, such as metal alloys, make up multi-coolers, depending on the end application, such as metal, plastic, or fibrous materials. Metal alloys commonly used for multi-cooler fabrication include:
- Carbon Steel
- Stainless Steel
- Aluminum Alloys
Carbon steel is easy to weld and fabricate and is suitable for low-cost, high-volume production. On the other hand, aluminum alloys are suitable for high-cost, low-volume production.
Metal alloys for multi-cooler fabrication must have low thermal conductivity and high chemical resistance because the inlet and outlet flow streams are highly corrosive.
The classifications of materials used for multi-coolers are:
- U-tubing
- C-channel
- I-beam
- T-shaped profile
- V-shaped profile
- Angle
- Curved profiles
- Rounded corners
- Sheet metal
Multi-Coolers Processing
The three facets of manufacturing multi-coolers include extrusion, casting, and electric motors. Extrusion is suitable for short, large-diameter, and high-production designs. Meanwhile, casting suits short, small diameter, and medium to low production designs.
Extrusion is an ideal choice for manufacturing multi-coolers because it is suitable for many designs and fabricates long, large-diameter designs. Additionally, altering the multi-cooler configuration becomes simple during the design phase because extrusion does not require expensive molds, dies, or equipment.
However, consider the thermal behavior of the materials, the configuration of the inlet and outlet fittings, and the system's operating temperature while selecting the extrusion process.
Sand Mixer Design and Manufacturing
A sand mixer mixes granular materials, such as sand and concrete, with water to form a slurry, which is widely used in construction because it mixes materials efficiently and effectively. Sand mixers come in different designs and materials and are classified into one of the following categories:
- Belt-type sand mixer
- Bucket-type sand mixer
- Drum-type sand mixer
- Screw-type sand mixer
- Twin-screw sand mixer
Belt-type sand mixers are suitable for coarse-grained materials and large-volume applications, such as concrete batching and slurry mixing. They manufacture sand mixers from metal, plastic, or fibrous materials.
Bucket-type sand mixers are suitable for attaining a high water penetration rate and mixing coarse-grained materials, such as concrete batching and slurry mixing. They manufacture sand mixers from metal and fibrous materials.
Sand mixers manufactured from metal and fibrous materials are suitable for dense-grained materials while used for concrete batching and slurry mixing. These sand mixers are suitable for dense-grained materials.
In Sum
Fracking and foundries use the industrials sand mined in Wisconsin and Minnesota; however, there are others:
- Building Products
- Ceramics and Refractories
- Chemical Production
- Filtration and Water Production
- Glassmaking
- Metallurgical
- Paint and Coatings
- Recreational
Each industry processes sand differently, using different equipment and methods. Multi-coolers and sand mixers play important parts in foundries and other industries.