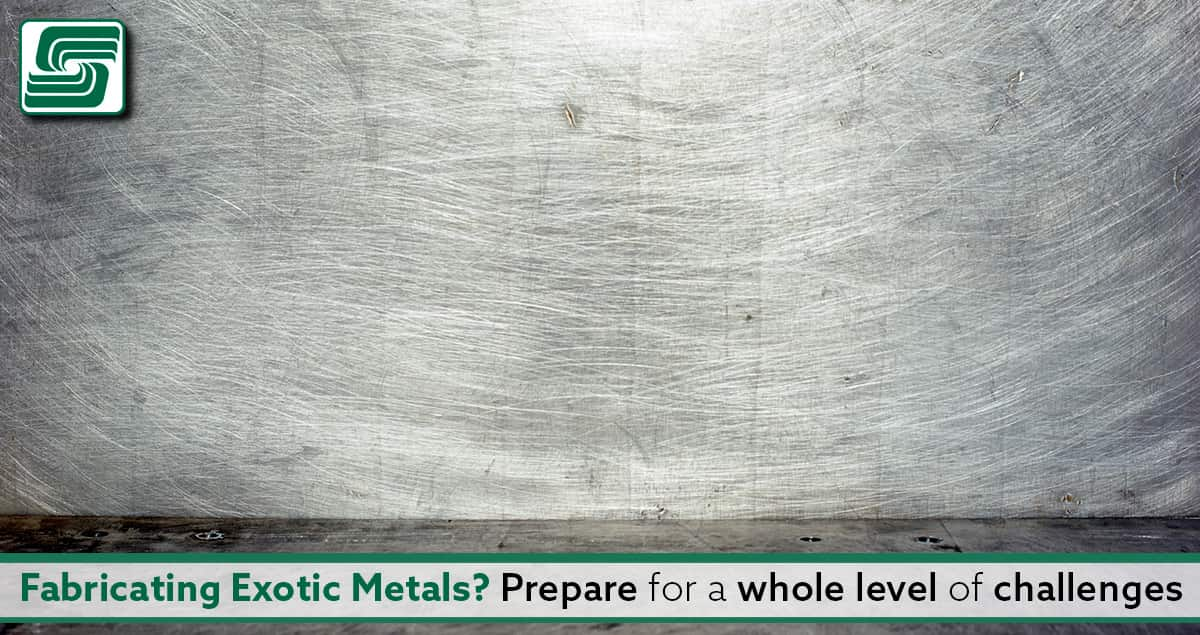
When fabricating using exotic materials, there are several important considerations to factor into the design phase.
These materials can be challenging from a fabrication standpoint because they require non-standard tooling and processes. Some of these metals are just too brittle for some end uses, such as machining or grinding. They also have different thermal expansion properties compared to most common metals.
There is also a limited number of suppliers for Ti, Waspaloy, Inconel, and other commonly used exotic metals. It’s important to learn about the availability of raw materials and finished components made from these materials. This article will highlight some primary considerations when using exotic metals in manufacturing.
Exotic Metals Require Non-Standard Tooling
Most exotic metals have very different thermal properties than metals such as steels, titanium, or Inconel®, which impacts the type of tooling needed to machine these materials. For example, tools may need to be larger than standard materials.
Exotic metals also have different thermal expansion properties than common steels. Therefore, a standard machine tool may not work well for these. Some metals can have thermal gradients 50-100 times greater than steel.
Exotic metals generally need a higher spindle speed, higher horsepower, and more horsepower per tooth than steels, which is particularly true when machining hard materials.
Exotic Metals Have Different Thermal Properties Than Common Metals
Most exotic metals have very different thermal properties compared to common steels impacting the type of equipment used to machine, grind or form these materials.
For example, the tooling may need to be larger than standard materials. Exotic metals also have different thermal expansion properties than common steels; therefore, a standard machine tool may not work well for these. Some materials can have thermal gradients 50-100 times greater than steel.
Exotic metals generally need a higher spindle speed, higher horsepower, and more horsepower per tooth than steel, which is true when machining hard materials.
Exotic Metals Are Usually Very Brittle and May Fracture During Machining or Grinding
Most exotic metals are very brittle and fracture easily. Therefore, it’s important to use gentle machine techniques, such as reduced spindle speed, low horsepower, and smaller tooling. You should avoid any vibration and keep the spindle load to a minimum.
Exotic metals also chip and shatter, making it difficult to machine intricate shapes, which is challenging when forming these materials by pressing. In some instances, it may be necessary to pre-process the material by rolling it, forging it, or extruding it.
Exotic metals may also experience thermal cracking, particularly in thin sections, where it’s more prevalent when the material is in its hardened condition.
Inconel Has A Tendency To Flaw during Fabrication
Inconel is very difficult to fabricate because of the tendency to “critical” or crack during fabrication, meaning it develops a crack without a specific load being applied. It’s important to follow recommended fabrication practices, such as using shear-to-break-off fixtures, tool temperature limits, and slow speeds.
Inconel also tends to work-harden, meaning the hardness increases as the material deforms, causing the part to fracture if formed too thin or if they leave the edges too sharp.
Machining Inconel isn't an easy task:
Machining
Inconel is a difficult metal to shape and to machine using traditional cold forming techniques due to rapid work hardening. After the first machining pass, work hardening tends to plastically deform either the workpiece or the tool on subsequent passes. For this reason, age-hardened Inconels such as 718 are typically machined using an aggressive but slow cut with a hard tool, minimizing the number of passes required. Alternatively, most of the machining can be performed with the workpiece in a "solutionized" form, with only the final steps being performed after age hardening. However, some claim that Inconel can be machined extremely quickly with very fast spindle speeds using a multi-fluted ceramic tool with a small depth of cut at high feed rates as this causes localized heating and softening in front of the flute.
External threads are machined using a lathe to "single-point" the threads or by rolling the threads in the solution-treated condition (for hardenable alloys) using a screw machine. Inconel 718 can also be roll-threaded after full aging by using induction heat to 700 °C (1,290 °F) without increasing the grain size. Holes with internal threads are made by thread milling. Internal threads can also be formed using a sinker electrical discharge machining (EDM).
More often than machining, water-jet or laser grinding is a preferred and economical method for forming nickel alloy components to shape and finish. Due to the hardness of the abrasives, the grinding wheels are not as affected by the hardening material and remain sharp and durable.
Joining
Welding of some Inconel alloys (especially the gamma prime precipitation hardened family, e.g., Waspalloy and X-750) can be difficult due to cracking and microstructural segregation of alloying elements in the heat-affected zone. However, several alloys, such as 625 and 718, have been designed to overcome these problems. The most common welding methods are gas tungsten arc welding and electron-beam welding.
Waspaloy Is Harder To Weld Than Common Steels
Waspaloy® is an age-hardening austenitic nickel-based superalloy typically used in higher temperature applications, such as gas turbines.
The alloy is much harder to weld than common steel, such as carbon steel, Inconel, or stainless steel, because it has a very low carbon content, making it more difficult to achieve sufficient penetration.
Waspaloy also has a very low thermal conductivity, making the heat-affected zone more severe. When welding Waspaloy, it’s important to use a low-hydrogen-content filler metal, such as ER70S-6.
Via Wikipedia, here are the properties and uses of Waspaloy:
Properties
Waspaloy is an age-hardenable, nickel-based superalloy with excellent strength properties through temperatures of roughly 980°C (1800°F). Other characteristics of Waspaloy include good corrosion resistance and being relatively impervious to oxidation, making it well suited for service in extreme environments.
Waspaloy has useful strength at temperatures up to 760-870°C (1400-1600°F), and good oxidation resistance in gas turbine engine atmospheres up to 870°C (1600°F). The creep rupture strength of Waspaloy is superior to that of Alloy 718 at temperatures above 620-650°C (1150-1200°F). Short-time hot tensile strength is inferior to RA718 at temperatures up to 730°C (1350°F).
Uses
Waspaloy is often used in extreme environments. It is common in gas turbine blades, seals, rings, shafts, and turbine disks. The NIST-certified reference material 1243, a standard for X-ray fluorescence spectroscopy, is made from Waspaloy.
The British Aircraft Corporation TSR-2, a supersonic strike aircraft developed in the late 1950s, had a fairing to its rear fuselage around the exhaust nozzles. Owing to the high temperatures in this area, the fairing was formed of Waspaloy and left unpainted. Fabrication of this alloy was described as 'very intractable' and was carried out by the engine specialists Bristol, rather than the airframe builders BAC.
Tools Need to Be Sharp and Ultra-High Speed
Exotic metals are usually very brittle, and tools must be extremely sharp to prevent deflection and breakage. It may also be necessary to employ ultra-high-speed spindle speeds to avoid material sticking and excessive tool wear. Exotic metals are often difficult to chip, so it may be necessary to use a break-off or shut-off technique, particularly when milling or grinding.
Summary
When fabricating using exotic materials, consider several important considerations to factor into the design phase. Exotic materials are challenging from a fabrication standpoint because they require non-standard tooling and processes. Most exotic metals are very brittle and fracture easily.
It’s important to use machine techniques that aren’t as rough, such as reduced spindle speed, low horsepower, and smaller tooling. Avoid vibration and keep the spindle load to a minimum. Exotic metals tend to chip and shatter, making it difficult to machine intricate shapes, creating a challenge when forming these materials by pressing. It may sometimes be necessary to pre-process the material by rolling it, forging it, or extruding it.
Inconel is very difficult to fabricate because of the tendency to “critical” or crack during fabrication. It’s important to follow recommended fabrication practices, such as using shear-to-break-off fixtures, tool temperature limits, and slow speeds.
Waspaloy is much harder to weld than common steel, carbon steel, Inconel, or stainless steel. This is because the alloy has a very low carbon content, which makes it more difficult to achieve sufficient penetration. Waspaloy also has a very low thermal conductivity, which makes the heat-affected zone more severe.
When welding Waspaloy, it’s important to use a low-hydrogen-content filler metal, such as ER70S-6. Tools must be sharp and at ultra-high speed when working with exotic metals. Exotic metals are usually very brittle, and tools must be extremely sharp to prevent deflection and breakage.