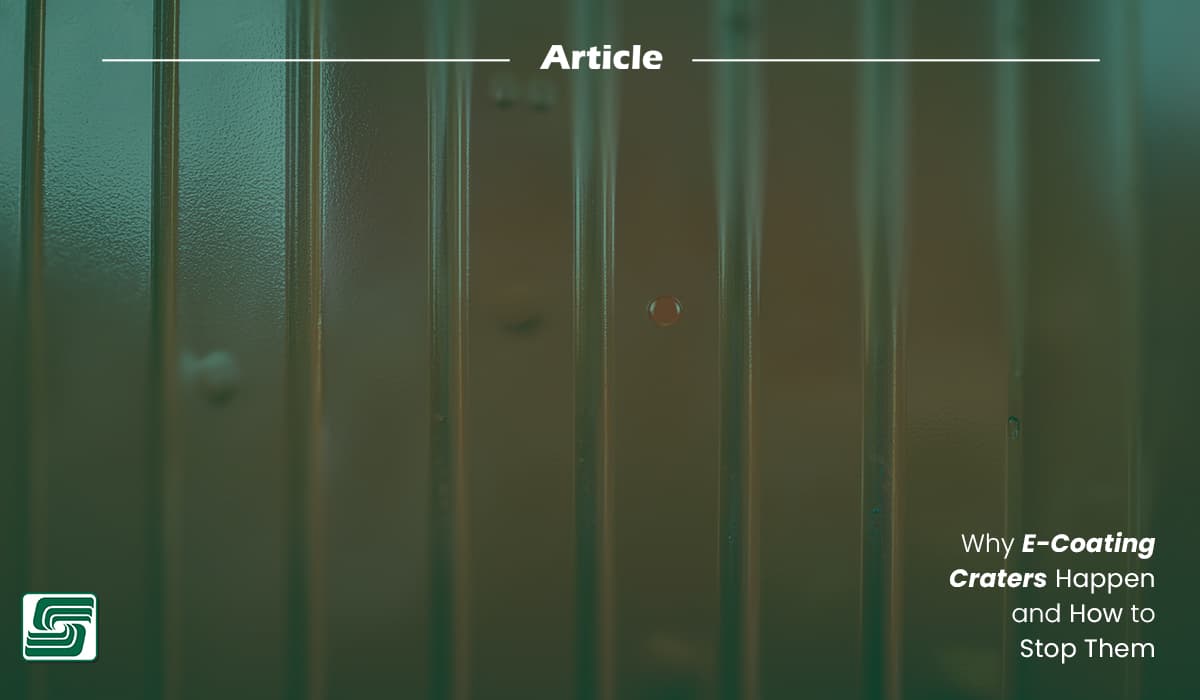
E-coating is crucial in industrial applications, providing various products with a durable and uniform finish. However, cratering poses a significant challenge in this process. These defects, often caused by temperature changes and surface conductivity issues, compromise the quality of the coating.
Addressing cratering is essential for maintaining high standards and ensuring product reliability. By understanding the underlying causes, industries implement effective strategies to prevent these imperfections and enhance overall performance.
Understanding E-Coating Craters
E-coating craters appear as small, bowl-shaped depressions on the coated surface. These imperfections disrupt the smoothness and uniformity of the finish.
Visual Identification of Craters
Craters are identified by their distinct circular shape and varying depths. They often resemble tiny pits or dimples, making them easily noticeable upon inspection.
Impact on Product Quality
Craters significantly affect product quality. They compromise the aesthetic appeal and lead to functional issues, such as reduced corrosion resistance.
This impact underscores the importance of addressing cratering in e-coating processes.
Common Occurrences in E-Coating Processes
Cratering is common in industries that rely on e-coating for protective and decorative finishes. Understanding where and how often these defects appear helps develop targeted prevention strategies.
Industries Most Affected
Industry |
Crater Frequency |
Patterns |
Automotive |
High |
Consistent throughout production |
Aerospace |
Medium |
Concentrated in specific components |
Electronics |
Low |
Occasional, often because of contamination |
Appliances |
Medium |
Varies, depending on the product |
Construction |
Low |
Mostly localized to specific applications |
Frequency and Patterns
Cratering follows specific patterns related to the coating environment and materials used. Low surface tension contamination, air bubbles, and dirt contribute to these patterns. Identifying these factors is essential for reducing crater frequency.
By understanding these elements, industries implement effective measures to minimize cratering and enhance the quality of e-coated products.
What Causes E-Coating Craters?
Understanding the causes of cratering in e-coating is crucial for preventing these defects. Various factors contribute to the formation of craters, each requiring specific attention and solutions.
Cause |
Description |
Contamination |
Dust, dirt, oils, and residues from previous processes |
Gas Entrapment |
Trapped air or gases during curing |
Improper Pretreatment |
Inadequate cleaning or chemical application |
Overspray |
Excess coating material beyond the target area |
Incorrect Curing Conditions |
Improper temperature, time, or atmosphere |
Prevention Strategies for E-Coating Craters
Thorough Cleaning Protocols
Effective cleaning protocols play a pivotal role in preventing e-coating craters. Industries significantly reduce the risk of defects by ensuring surfaces are free from contaminants.
Cleaning Aspect |
Recommended Methods |
Purpose |
Cleaning Agents |
Solvents, detergents (alkaline for organic contaminants, acidic for inorganic residues) |
Remove oils, dust, and residues from the surface. |
Cleaning Techniques |
Ultrasonic cleaning, high-pressure washing |
Ensure thorough removal of contaminants from complex surfaces. |
Pretreatment Processes |
Degreasing, rinsing, conversion coatings |
Prepare the surface for optimal e-coating adhesion and corrosion resistance. |
Equipment Maintenance |
Regular inspection, cleaning, and calibration of spray nozzles, tanks, and dosing systems |
Ensure consistent and effective pretreatment performance. |
Regular Maintenance Schedules |
Establish consistent maintenance schedules. |
Regular inspections help identify potential issues before they affect the coating process. |
Key Equipment Checks |
Key checks include examining spray nozzles, pumps, and filters. |
Correct function minimizes contamination risks. Regular calibration ensures precise application. |
Addressing Environmental Factors
Impact of Humidity and Temperature
Environmental conditions, particularly humidity and temperature, significantly influence the e-coating process. These factors alter the coating's properties, leading to defects like cratering.
Seasonal Variations
Seasonal changes bring fluctuations in humidity and temperature, affecting the e-coating process. During humid seasons, moisture condenses on surfaces, leading to poor adhesion and an increased risk of cratering. Conversely, dry conditions may cause rapid evaporation of solvents, resulting in uneven coating application. Industries must recognize these seasonal variations to adjust their processes accordingly.
Climate Control Solutions
Implementing climate control solutions helps maintain consistent environmental conditions. Dehumidifiers and air conditioning systems regulate humidity levels, ensuring optimal conditions for e-coating. Temperature control systems stabilize the environment, preventing rapid changes that could affect the coating's integrity. By investing in these solutions, industries minimize the impact of environmental factors on the e-coating process.
Role of Air Quality
Air quality is vital for a successful e-coating process. Contaminants in the air settle on surfaces, leading to defects such as cratering.
Airborne Contaminants
Airborne contaminants, including dust, dirt, and industrial pollutants, threaten e-coating quality. These particles land on the substrate or mix with the coating solution, creating imperfections. Regular monitoring of air quality helps identify potential sources of contamination, allowing industries to take preventive measures.
Ventilation Systems
Effective ventilation systems are essential for maintaining clean air in e-coating facilities. High-efficiency particulate air (HEPA) filters capture airborne particles, reducing the risk of contamination. Properly designed ventilation systems ensure a continuous flow of clean air, preventing the accumulation of pollutants. By investing in robust ventilation solutions, industries enhance the quality and consistency of their e-coated products.
Managing Post-Tank Contamination
Post-tank contamination poses a significant challenge in maintaining the e-coating's quality. Identifying and managing these contaminants is crucial for ensuring a defect-free finish.
Identifying Sources of Contamination
Understanding where contaminants originate helps in developing effective prevention strategies.
Common Contaminants
Common contaminants include dust, dirt, and residues from previous processes. These particles settle on surfaces after the coating tank, leading to imperfections. Oils from machinery or human handling also contribute to contamination. Recognizing these elements is essential for maintaining a clean environment.
Prevention Techniques
Preventing contamination involves several strategies. Regular cleaning of workspaces and equipment reduces dust and dirt. Implementing strict protocols for handling materials minimizes the introduction of oils. Using protective covers over coated parts shields them from airborne particles. These techniques help maintain the integrity of the e-coating process.
Implementing Post-Tank Cleaning
Effective cleaning methods ensure surfaces remain free from contaminants after the coating process.
Effective Cleaning Methods
Several cleaning methods prove effective in removing post-tank contaminants. High-pressure air blowers dislodge dust and dirt from surfaces. Wiping with lint-free cloth removes residues without leaving fibers behind. Solvent-based cleaners may be necessary for more stubborn contaminants. These methods ensure a pristine surface, ready for further processing or inspection.
Equipment Used for Cleaning
Various tools aid in the post-tank cleaning process. Air blowers and vacuum systems effectively remove loose particles. Lint-free cloths and specialized brushes help in manual cleaning efforts. Solvent dispensers provide controlled application of cleaning agents. Industries use the right equipment to maintain cleanliness and quality standards in their e-coating operations.
The Role of Surface Tension in Cratering
Understanding Surface Tension
Surface tension plays a pivotal role in the e-coating process. It refers to the cohesive force at the surface of a liquid, which affects how the coating spreads over a substrate. When surface tension is not properly managed, it leads to cratering, a common defect in e-coating.
How Surface Tension Affects Coating
Surface tension influences the flow and leveling of the e-coating on the substrate—high surface tension causes the coating to bead up, leading to uneven coverage and potential cratering. Conversely, low surface tension allows the coating to spread more evenly, reducing the likelihood of defects. Proper management of surface tension ensures a smooth and uniform finish, enhancing the durability and appearance of the coated product.
Methods to Control Surface Tension
Controlling surface tension involves several techniques. Manufacturers often adjust the coating formulation by adding surfactants, reducing surface tension, and improving flow. Maintaining optimal environmental conditions, such as temperature and humidity, helps stabilize surface tension during application. These methods ensure that the coating adheres properly to the substrate, minimizing the risk of cratering.
Adjusting Surface Tension for Better Results
Adjusting surface tension is crucial for achieving high-quality e-coating results. Manufacturers fine-tune this property to tailor the coating to meet specific performance requirements.
Additives and Modifiers
Additives and modifiers play a significant role in adjusting surface tension. Surfactants, for example, are commonly used to lower surface tension, allowing the coating to spread more evenly. Other additives, such as wetting agents, enhance the coating's ability to adhere to the substrate, reducing the risk of cratering. Manufacturers optimize the coating process for different substrates and applications by picking the additives.
Testing and Monitoring Techniques
Testing and monitoring techniques are essential for ensuring consistent surface tension throughout the e-coating process. Manufacturers often use instruments like tensiometers to measure surface tension and make necessary adjustments. Regular monitoring helps identify deviations from the desired surface tension, allowing timely corrections. This proactive approach ensures a defect-free finish and enhances the overall quality of the e-coated product.
In Sum
A defect-free e-coating process extends product life and reduces replacement needs. This approach not only saves costs but also supports sustainability by minimizing waste.
Achieving a flawless e-coating finish requires attention to detail and commitment to quality. By addressing the root causes of cratering, industries enhance their products' reliability and appearance.
Addressing cratering in e-coating is crucial for maintaining product quality and reliability. Craters compromise the finish, leading to aesthetic and functional issues. Industries must implement the discussed prevention strategies to minimize these defects. They achieve a defect-free finish by adopting thorough cleaning protocols, optimizing pretreatment processes, and maintaining controlled curing conditions. Maintaining high-quality e-coating standards ensures long-term benefits, including enhanced durability and reduced waste. Continuous improvement in techniques fosters innovation and excellence, encouraging industries to strive for superior results.